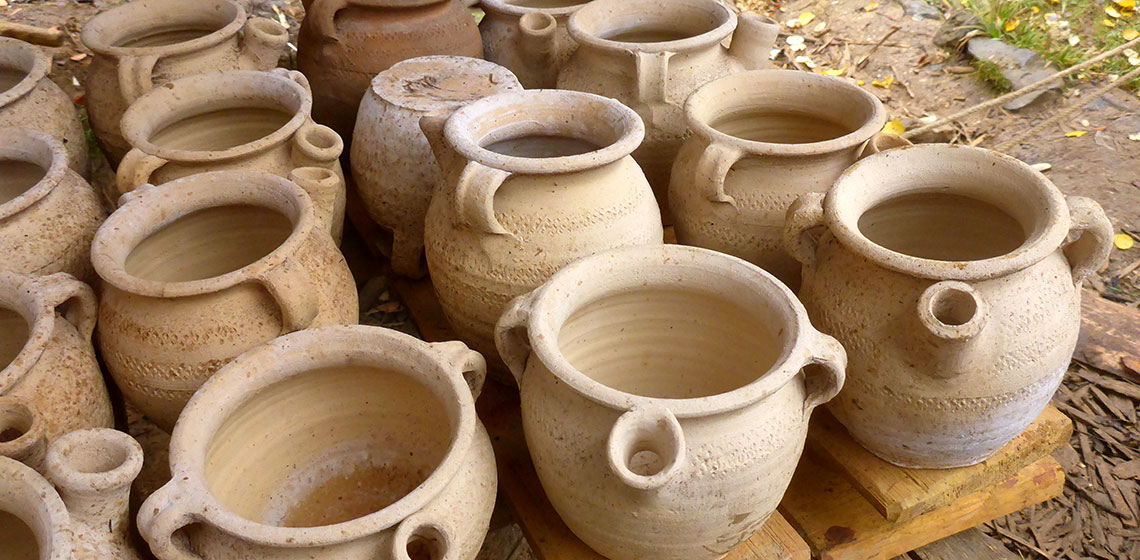
Examples from a 9th century potter’s workshop as presented in "Campus Galli”, a medieval construction site in Southern Germany. The open-air museum Campus Galli is a construction site where we built an early medieval monastery, following the so-called “Plan of St. Gall”, an architectural drawing from the first half of the 9th century (Carolingian period) as our major reference source (cf. Schedl, 2014; Facsimile: Tremp, 2014). Compared to many other archaeological open-air museums, our focus is not only on the appearance of finished buildings, but the crafts and techniques of the building process itself, not unlike the Guedelon castle construction project in France. We started by building a wooden church which we intend to be followed by a large, stone-built abbey church. Along with the construction, we also demonstrate other aspects of early medieval life to the public – monastic life, agriculture and various crafts that are necessary for construction and for supply. The work is performed during our open season and is visible to visitors, so our craftspeople double up as interpreters. Our work is based on archaeological and historical background research. We collaborate with scientists and scientific institutions and we are expanding our scientific network continually.
The potter’s workshop
One of the crafts presented in Campus Galli is the making of pottery. I am a medieval archaeologist, and an autodidact potter in the “Living-History” scene, with experience in producing early medieval and other ceramic replicas. Since I started to work in Campus Galli in 2015, I improved the manufacture of pottery under medieval conditions and thus produce high quality pottery reproductions. We use manual (reconstructed or assumed) medieval resources, techniques and devices. The entire production chain is completed only manually, i.e. clay excavation and processing, forming techniques, firing, as well as tools and infrastructure like the potter’s wheels and the kiln. Replicas of medieval tools and devices are easy to achieve since there are many other craftspeople (blacksmith, rope-maker, basket maker, carpenter, stonemason, producers of textiles). Most of our workshops and work spaces are occupied almost every day, not only at weekends or at special events. I work there seven to eight months per year almost on a daily basis, which provides excellent opportunities to gain routine and experience. In 2016, I completed seven firings and produced between 400 to 450 pots. My engagement is not temporarily limited on one project alone but I hope to work there for future decades. Thus, this will result in the establishment of a daily routine and the development of long time experience. Over such a long time, the usage and the endurance of the pots may be observed; for example, long term use of drinking cups, water jars, cooking pots and storage vessels. These conditions provide convenient opportunities for scientific research, documentation and experiments (cf. Rogier, in press).
Practical experience is not yet scientific profit. To learn from our manual activities, it is important to record and evaluate the work being practiced by the craftspeople. An important part of the preparation of experiments concerning ancient technologies is to search for experts, or engage with training and learning of the relevant crafts techniques. In Campus Galli, this step requires low effort of work. Experienced and practiced craftspeople are already at hand. Not only systematic and elaborate experiments, but already the documentation of some simple observations of the daily work can contribute relevant scientific information on ancient processes and techniques. These observations can be the first steps to develop questions for further research and experimental analysis.
Experiment and Experience
Experimental archaeology usually is distinguished from related phenomena – like Living History, didactic reconstructions and presentations of ancient techniques in open air museums etc. – by experiments, a concept that is originated from the natural and laboratory sciences. Here it is not necessary to give an overview about the state of discussion on definitions, theories and methods of experimental archaeology. In our context it is only interesting to note that experiments are a well-prepared way to collect systematic data towards a specific research question. An experiment in the strictest sense should have a previously defined precise research problem (hypothesis), a previously experiment set-up or design, control(s) or at least the identification of all variables, and a detailed documentation, followed by a subsequent analysis and evaluation.
But I argue that it is possible to gain quite a large scientific profit also from unintentional, random observations. It would be an exaggeration to claim that only scientific experiments can provide scientific profit. Experience and practice may provide important information. During my daily work I have regularly made unintentional, random observations that are worth documenting and recording for archaeological ceramic research. Critics might perhaps claim that these random observations are not scientific, because they are not gathered by a systematic method and therefore are just anecdotal and not reproducible. Experiments are not the only scientific way to collect data. Besides experiments, there are many approaches and methods from different sciences to gain information systematically from reality, including data collected by documenting observations in field studies.
The challenge is to develop concepts and methods to evaluate all these random observations in an adequate, scientific way. What standards have to be met by observations that are not gathered systematically under controlled conditions? What are possible sources of errors? Unique incidents should not be generalised. How and to what extent observations have to be correlated with other information or to be verified by other methods to get significant results? The long-term routine allows the repetition of specific observations and to collect a huge amount of examples. But on the other hand, a well-rehearsed routine in the daily practical work bears the risk that the conditions are not varied enough to discover possible alternative solutions for technical problems. To evaluate observations scientifically and to minimise bias and errors, we have to think about these and similar questions.
But first of all, observations have to be well-documented. In the potter’s workshop in Campus Galli, observations are recorded by written notes, photographs and short memo videos. Besides random observations, other things like quantities and amounts of raw materials, products or frequency and spaces of times of specific processes are being documented as well. All this information is collected during the opening season from April to October and is evaluated during the winter breaks.
But the opportunity to document observations is not the only advantage of practical work in field studies. Practical manual experience is an important precondition for experimental archaeology for different reasons. Experience enables us to develop questions that are suitable for scientific research. And experience enables us to perform experiments in an adequate way. That performers have mastered the basic techniques of the craft and have practice in the applied manual techniques is regarded as an important precondition of the validity of experiments.
Pottery Production in Campus Galli and what to learn from it
Much discussion may be had about scientific theory and methods, but now I am going to focus on the activities in the potter’s workshop. I provide an overview about the production and a few examples of my observations (cf. Rogier, in press).
Clay processing: Various techniques with different results
The decision for a specific way of processing depends on many factors. Not only the scale of production, for example, professional, specialised workshop industries on the one hand, and home industries/ semi-professional production on the other hand, but especially the properties of the raw material source are important. Also important is the choice of forming techniques, the choice of firing techniques and the intended properties of ceramics depending on vessel function.
There are several manual clay processing methods of pre-industrial potters of our recent time that are well-known and documented in ethnographic literature (e.g. Rice, 1987, pp.118-119). These documentations of processes are used by archaeologists as analogies to reconstruct possible clay processing methods of more remote periods.
To process the clay, I tried out various methods according to manual processes known from recent ethnographic or sub-recent historical examples (cf. e.g. Rice, 1987, pp.120-124). We used clays that we dug out on our site (See Figure 1, 2). One way of clay processing is levigation, whereby clay is mixed with water into a thin suspension, and afterwards purified by sedimentation. In our case, three buckets (appr. 30 litre) of clay are mixed with around ten buckets of water in a wooden tank (See Figure 3). The mixture is soaked for two to three days and sometimes stirred, until all lumps of clay are dissolved. This suspension is then left to rest for approximately two weeks, so it can settle. The finer the grains the slower they sink down. After at least two weeks, there are different layers. At the top there is clear water, beneath this there is a huge layer of fine clay slurry, then a lower layer of coarse clay (loam, silt, sand, stones) and finally the layer at the bottom is a deposit of impure, loamy clay mixed with pebbles, silt and sand. The layers are separated by scooping each out using a ladle. The fine clay is soft and still almost fluid. It must be dried to get stiff to knead. We use big, flat, wooden troughs to dry out the fine clay. Processes like this are done preferentially in summer. Traditional pottery techniques depend on the seasons to a large extent (Kerkhoff-Hader, 1996, pp. 232-233; Schütz, 2006, p.131). Levigation changes the grain size composition of the clay as the coarser grain size fractions are removed. The clay is now finer, with a higher content of clay minerals and a lower content of coarser materials. This is a high plastic clay that is suitable to be thrown on the fast potter’s wheel.
Removing impurities, levigation and tempering – all change the petrographic composition, i.e. the content of specific grain size fractions. It is no surprise that processing steps or methods that change the petrographic composition influences clay properties such as plasticity. Removing coarse material is achieved by potters to improve the plasticity of the clay. Adding coarse material decreases plasticity of the clay but improves drying and the firing behaviour and is sometimes also applied to make the clay more workable and less sticky.
There are steps involved with the processing that change clay properties such as plasticity but without changing the petrographic composition. With one of my clays, I tested two different processing methods. In one case, we took the moist clay out of the clay pit, crumbled it a little and soaked it in a bucket of water and kneaded it the next day. In the other case, we dried the same clay in the sun until it became hard, then crushed or ground it with a pole or stone to a powder (See Figure 4), sieved with a basket and then soaked and kneaded it. Similar methods involving drying, crushing or grinding and sieving are documented quite often in ethnographic literature (cf. Hampe and Winter, 1965, pp.4-5; Rye and Evans, 1976; Rice, 1987, p.123; Gruner, 1991, p.94; Vossen, 1991, p.140; Mershen, 1991, p.161; Papousek, 1991, p.203), but also the simple soaking of the moist clay is described (cf. Schneider, 1991, p.71). Surprisingly these two methods provided very different results: The simple soaked clay was coarse, stiff and meagre. In contrast, the dried and crushed clay was highly plastic and even suitable to be thrown on the fast wheel.
Thus, the techniques of clay processing which change the grain size composition of the clay (i.e. adding coarse fractions by adding temper or removing coarse fractions by levigation) have a big influence on clay properties. There are techniques of processing that do not change clay composition. These methods may be crucial to the clay properties. Another example of a process that improves clay workability without changing the composition is the influence of aging the soft, wet clay (Rice, 1987, p.119; Engelbrecht, 1991, p.181).
Interrelations like that are not my invention and are known to potters who prepare their own clay (Cardew, 1969) as well as perhaps to colloid chemists or to ceramic engineers concerned with industrial clay processing for the ceramic industry. To me as an archaeological ceramic researcher it was a surprise what a huge difference in the clay workability these two clay processing methods provided. The importance of these techniques and processes are sometimes underestimated. Archaeologists have concerned themselves a lot with the composition of the clay and the examination of non-plastic material as temper or impurities. However, there is the danger of underestimating the influence of clay processing steps and techniques that are macroscopically invisible because they do not change the clay composition. This influence is significant to specific questions in archaeological ceramic research. When considering soil samples to discover possible raw materials of ancient potters, simple finger testing methods may be used to give a first rough impression, but it would be better to process the samples before ascertaining if these clay samples are suitable for pottery making.
Producing vessel replicas and re-enacting pottery techniques
Vessels are formed using different techniques. Some are made on a reconstructed potter’s wheel that is driven by a pole (See Figure 5, 6). We know about the use of the fast wheel by the manufacture marks on the ceramic findings (Gross, 2009, p.55; Schreg, 2012, Figure 5.) that are typical for wheel-throwing (Rye, 1981, Figure 62a-b; Rice, 1987, Figure 5, 8) (See Figure 7). There is no record of the appearance of the potter’s wheels in either written or iconographic sources from the Carolingian period, thus we used analogies from other periods: Roman (Rieth, 1965, plate 39, 1-2) and later medieval to early modern potter’s wheels (Guadagnin, 2000, Figure 43, Figure 45-49; Leterme, 2008, Figure 4-8). Another technique is to build vessels out of clay coils without using a wheel (See Figure 8). This technique was typically employed in the manufacture of many prehistoric ceramics and had already become rare in the Carolingian period (Schreg, 1998, p.196). The third technique is a combination of coil building and shaping using a slow, hand-driven wheel (“nachgedrehte Keramik”), a typical, wide-spread technique in early medieval and high medieval times (Rogier, 2015a.) (See Figure 9-11).
Manufacture marks on pots
The daily work and routine for long durations enables frequent repeated observations to be made and to gather a large amount of data and examples. One example was the traces of manufacture retained on the vessels. During my work, I observed many of them (See Figures 7, 8, 11-16). In the literature, there are many discussions about the interpretation of manufacture marks (Guthnick, 1985), because they are important artefacts sustained during the manufacture stages and thus provides indirect clues to reconstruct forming techniques. For many periods, they are the only sources of information about pottery manufacture.
Medieval pots with flat, not reworked bottoms usually show two main structures or patterns on their underneath. Some have typical slopes (See Figure 14). The slopes arise when the vessel is cut from the wheel with a strained string, thread or wire. They relate to the use of the fast potter’s wheel and are easy to recognize and often are described in the literature. The second structure consists of marks that indicate that the vessels were lifted directly from the wheel or underlay without been cut by a string. These vessel bottoms sometimes have swollen rims at the edge between the wall and the bottom, like a narrow tiny pedestal ring (See Figure 15, 16), or sometimes they are formed akin to a slight gap or fold parallel to the rim. There is no consensus in the literature as to how or why these vessels were lifted and not cut, and how and why these swollen rims formed (Rogier, 2015b).
Why are the rims interesting? They are usually connected to vessels that are not wheel-thrown on the fast wheel, but coil built on the slow, hand-driven wheel. Do they present sufficient evidence for this technique? The decision of whether a vessel is wheel-thrown on the fast wheel or coil-built on the slow wheel can be significant in identifying and dating ceramic findings, and it can be significant in matters of economic history, therefore it could be interesting as to how and why these items arise. In the literature, there are five to six different ideas of how these rims form (cf. Rogier, 2015b, p.247-248). Mainly they are regarded as the imprint of an intermediate pad that was laid on the top of the potter’s wheel and on which the pot was built.
A few years ago, before I worked in Campus Galli, I started an experiment and tried out the hypotheses about the rims manually, using the descriptions as instructions and formed coil-built pots on a hand-driven wheel (Rogier, 2015b). Incidentally, I found another explanation - these rims or folds can arise automatically, presumably by lateral pressure during forming. I reproduced these swollen rims without using any pad. But though this was a planned and prepared experiment, my database was small. I produced a very small number of vessels, and as such, I was cautious with my conclusion. During my work in Campus Galli I observed these rims on a lot of vessels that I made. It was very interesting to observe how these rims come off almost regularly at the work on the slow wheel. This shows that routine work can have advantages towards planned experiments, which are restricted with time and cost. When I used to perform a well-planned experiment, I produced a few examples, and it was not until I did my daily work in Campus Galli without the aim to investigate anything, did I produce large numbers of examples which confirmed my former experiment.
Non-kiln firings
Our vessels are fired in different ways. Some are fired without a kiln in a bonfire (See Figure 17 and 18) or they are pit-fired (See Figure 19). Those non-kiln firing techniques are sometimes assumed for some medieval ceramic wares, especially coil built and slow wheel pottery examples. Apart from these assumptions that were derived from the appearance of these ceramic wares, archaeology cannot contribute much to medieval non-kiln firing technology because there are nearly no excavated medieval firing sites. Firing technology must be reconstructed with the help of analogies from ethnographical examples (Rice, 1987, pp.153-158; Mershen, 1988, pp. 92-93; Wotzka, 1991, pp.290-296; Schneider, 1991, pp.80-82; Gruner, 1991, pp.99-100; Herbich and Dietler, 1991, pp.125-127; Mershen, 1991, pp.168-169; Lucke, 1991, pp.335-336). The firing techniques described are roughly similar but vary in their details. So, in reconstruction of early medieval firings, there is large range of latitude of possibilities.
Our firings were oriented towards ethnographic descriptions of non-kiln firings, in conjunction with our own experiences. It seems that it was not useful to adhere too closely to the ethnographic descriptions. We must consider that many of these descriptions come from tropical and sub-tropical regions where potters have different conditions of geology (Cardew, 1969, pp.79-80), climate and fuels. Our pots are preheated before firing, because they cannot dry completely in the open air. They are placed in a fire for several hours and sometimes turned. For the actual firing, they are usually stacked on a thick layer of fuel and surrounded and covered with more fuel. The fuel is ignited. This is a critical stage for the pots, because the fire starts to burn very quickly. Throwing earth onto the fire or using moist fuel can slow down rising temperatures. Another possibility is a more continuous transition from the preheating to the actual firing, e.g. by moving the pots step by step closer to the fire, or to place the pots in the centre and surround them by a ring of fire that is gradually made narrower and thus moving the vessels to the centre. But in this case, it is difficult to get fuel under the pots, so there is no distance to the soil. This bears the danger of too low-fired zones, because the vessels cannot get enough heat from below. In any case, when the fire is burning, more fuel is added to increase the heat. Sometimes the pots can be seen glowing red. We tried out a technique that is documented ethnographically from many parts of the world - we pulled out the hot vessels and applied a solution of organic material (in our case, flour), that was immediately combusted and left a kind of carbon coating, to get denser ceramics (Rice, 1987, p.163; Herbich and Dietler, 1991, p.127 and Figure 12). After 1.5 to 3 hours, there was no further increases in temperature, we then covered the pile with earth to cool the firing slowly and to get a reducing (i. e. poor in oxygen) firing atmosphere.
As we utilised the ethnographic record on firing techniques, our results are in line with those documented within these firings. A short firing time, a rapid temperature increase, varying temperatures inside a single firing as well as varying temperatures between different firings, varying amount of waste from approximately 10 to 50%. We reach maximum temperatures of approximately 600 to 900 °C, which we learnt from an experiment (discussed below).
The unique situation in Campus Galli allowed us to investigate further the use of possible fuels used by early medieval potters. There are good reasons to assume that medieval firewood was different from modern firewood. Instead of felling and chopping big trees, there is evidence that often coppice wood was harvested and dropped wood or brushwood was collected. In Campus Galli, we also have the possibility to use these different kinds of fuels. We used wood and brushwood from land cleaning. A large amount of firewood is scrap from other crafts, like the large splint from the cutting of timbers and the waste from the chopping of clapboards.
The medieval potter conducted work alongside other fuel-consuming activities, like cooking, heating and baking. There are fuels that are not suitable for these purposes, because of their shape or structure, like tree roots, trunks and scrub from land cleaning or waste from agriculture. But roots and trunks can still be used to produce charcoal and many herbs and twigs from land cleaning are still useful to feed animals. However, there are still materials like brambles, thistles, straw and herbs that are not suitable for any other purpose, but they can still be used to do non-kiln firings of pottery. Especially soft fuels like brushwood, herbs, and other fine, thin materials seem to be suitable for non-kiln firing techniques.
Although our situation at Campus Galli is by no means a perfect simulation of the early medieval economic cycle, the rough approximation of some agricultural and economic aspects can help us to reconstruct the situation of early medieval potters which aids us in the development of ideas and theories about fuel economy.
The Potter’s Kiln
During the early medieval period, there seems to be a connection between wheel throwing and the use of pottery kilns (Rogier, 2015a, pp.97). Both are regarded as features of a specialized craft, in contrast to hand modelling techniques and non-kiln firings, which both possibly represent home industries and seasonal, semi-professional production. Thus since the potter’s wheel was already at Campus Galli, it seemed a logical step was next to build a kiln to demonstrate a broad view of early medieval potter’s craft to the visitors and to equip the museum with historically adequate vessel reproductions.
To date, there have been numerous reconstructions of archaeological excavated kilns and many firing experiments. So, why is it still reasonable to do experimental research about potter’s kilns? The scientific principles as well as the practical processes of kiln-firings are well-known. No experimental archaeology is required to examine the basic aspects and techniques, because traditional kiln types like wood-fuelled updraught kilns are used in modern times, and they are well-described in the ethnographic record (Hampe and Winter, 1965; Lüdtke and Vossen, 1991).
But many questions remain pertaining to specific interest areas. The previous experiments on kiln reconstructions and kiln firings were done with specific, different research problems in mind. They were achieved with different kilns from various periods. Though there are few basic kiln types, the excavated kilns differ considerably in detail - size, building material, shape etc. Therefore, differences in kiln firing behaviour are to be expected. There have been many reconstructions of updraught kilns from many periods which researched different problems: How many experiments were performed to examine the ceramic production of the Carolingian period and the associated specific ceramic wares? Can we confirm former experiments and are their results (as, for example, the maximum temperature, the endurance of the whole firing process etc.) repeatable? Are the observations and results really tied to the kiln type, or do they represent the influence of other conditions, as the practice of the kiln firing team and the stoking techniques? It was criticised that the description and documentation of kiln firing experiences is sometimes not detailed and precise enough (Herdick, 2015, p.228, note 25 and 26). How can we compare different kiln types of various times and regions regarding their efficiency? What conclusions can we draw from archaeological excavated kiln structures on the economic importance of a potter’s workshop, the grade of specialization or the scale of production by its kilns? Perhaps, kiln experiments can provide information for the reconstruction of kilns from the archaeological record. Thus, as far as research on kilns is concerned, there are still many aspects to be examined by experiments. If former experiments are considered and if we are in contact with similar projects, new experiments on potter’s kilns can still provide quite interesting results.
In addition to the didactic purpose and the practical purpose of producing our own vessel replicas, we planned the kiln as an experimental archaeological project – including both kiln building and kiln firing (and perhaps we will even excavate the kiln remains in the future). The kiln was built in a course with students of archaeology from the University of Tübingen, Germany, in summer 2016. The course included the first firing as well. It was held to teach the students about experimental archaeology, pottery technology, and kiln reconstruction. From the point of archaeological ceramic research, there is a lack of knowledge on how to preserve, excavate and document potter’s kilns caused by a lack of knowledge concerning kiln technology (Tzschoppe, 2000, p.111).
The course had a theoretical part that was held in the University of Tübingen. This included background research on excavated early medieval kilns in order to find examples, the aims and methods of other kiln experiments to develop ideas on the reconstruction of our kiln, and to form questions for our experiments.
The questions we had in mind concerned the kiln design and the firing techniques. To what extent does the kiln architecture determine the progress and the results of the firing? How can we control temperature, time and atmosphere? Can we discover methods of checking or estimating the parameters of the firing process (temperature, strength of ceramics, atmosphere etc.) without modern help (observation of smoke, flames, radiant heat colour, pulling out of sample vessels etc.)? How accurate are these techniques? Are they easy or can they only be achieved by lots of experience?
Another important aim was also to discover or develop new research questions. A further question was what is the life-span of a kiln that is used frequently? One prevalent problem within kiln experiments is that reconstructed kilns are not used as often as they might have been in the past, so observations concerning the kiln’s life-span are not reliable. It could be difficult to decide if a kiln is disintegrated because of age or because of use. We hope to use our kiln frequently to get a more realistic impression of a kiln’s possible working age. An additional topic were the interrelations between kiln design and flame movement, for example the influence of dimensions and proportions of flues and vents to the firing endurance and the firing atmosphere (Winter, 1978, pp.40-42).
A further aim of the kiln building project was of more practical concern – to try and experience how the conditions in Campus Galli are suitable to do scientific experiments. How does it work to do a detailed scientific documentation including the recording of the steps of work and observations by notes, photographs, and sometimes videos? What about the work with people who are not scientifically educated, like volunteers or pupils? How does documentation and recording work if we have conversations with visitors at the same time? To what extent do conversations with visitors limit the validity of observations concerning the effort of work? How many people do we need to do scientific documentation?
These questions and subsequent answers helped us to plan and prepare subsequent experiments. The experience from every experiment helps to improve the preparation of the next experiment. The precise recording of the time effort of specific steps in the kiln building did not work because it is influenced by too many factors. A huge effort of work by a big number of persons would be necessary do get valid results, so we restrained from the precise documentation of times already during the kiln building. A great relief is a precise assignment of tasks. The participants are grouped into small teams. One team for example is disposed only to talk to the visitors, so the teams involved in the documentation or the practical activities are not distracted. Especially archaeologist and lab scientists have a good sense for what has to be documented and how. For our different firing experiments a maximum of approximately 15 to 16 participants seems reasonable.
Not only are the kiln and its firing linked to experimental archaeology, but the kiln can additionally be regarded as a kind of expanded laboratory infrastructure to produce vessel reproductions for experiments focused on ceramics. Some sherds already have been used in experiments concerning the chemical examination of residues by Max Zerrer, University of Tübingen.
Original examples, reconstruction and design of the kiln
Our kiln reconstruction is not based on a specific excavated kiln structure from a single site, but it rather represents a typical potter’s kiln from early medieval period and has been reconstructed based on several archaeological excavated kilns (Heege, 2007, Cat. 116, 117, 170, 171, 173, 174, 177, 311). For some rarely preserved details, such as the dome and the perforated floor, we widened the chronological and geographic frame and considered additional kilns (Heege, 2007, Cat. 303; Keller, 2007, Figure 9-10). The idea to use only local materials was before the accurate realization of some well-preserved kiln structures. In one excavated potter’s kiln from Switzerland, the raised kiln floor was built with fire-proof sandstone (Heege, 2007, Cat. 171, Figure 60). For lack of equivalent materials we refused to do it this way and built the kiln from local clay.
It is a two-chambered updraught kiln (See Figure 20-26). It has a domed firing chamber (See Figure 25, 26) with a central exit flue, under which lies the underground combustion chamber with the stoking tunnel (See Figure 20). Between the chambers lies the raised, perforated oven floor (See Figure 23, 24, 29), supported by a radial wall (See Figure 20, 21).
All has been built from cob (i.e. a construction clay mixture including sand, straw, dung). The clay was from our site while the sand was obtained from a distance of approximately 15 km. Moreover, the building of the kiln was part of our experiment. Our questions concerned the effort of work, cob-building techniques and finding reference for the interpretation of traces in the archaeological record of kilns. We tested building techniques that we deduced from the manufacture marks of excavated kilns (See Figure 21, 22). We also recorded the mixing ratio of cob mixtures to develop suitable cob recipes and took samples from the cob mixtures for possible later examinations. In a few decades, the kiln perhaps can be excavated and compared to archaeological records to contribute information to the interpretation of future kiln excavations.
The domed firing chamber (See Figure 25, 26) has a diameter of approximately 1m at its base, a height of approximately 0.8 m and a capacity between 310 and 340 litres (or approximately eleven to twelve cubic feet). In the dome there is a kiln door to the firing chamber to load the kiln (See Figure 25). The exit flue has a 0.35 m in diameter. The raised floor is 13 cm thick and perforated by 34 vents (pipes, holes) with a diameter of approximately 4cm (See Figure 23). The combustion chamber is 0.5m high and 1m in diameter (See Figure 20). The fire tunnel (heat channel) is approximately 0.5m long. Its opening, the firemouth or stoke hole (See Figure 26, 27) that is also the inlet flue, has a cross-sectional area of approximately 0.1 m² like the exit flue.
Kiln firing
In 2016 and 2017, we did five kiln firings. The first firing was part of the already mentioned kiln construction course with the students from the university of Tübingen. In this first firing, the potter Johannes Klett-Drechsel from Fredelsloh, Germany, joined us (See Figure 27). He has more than 40 years of experience in wood fired potter’s kilns and with experimental reconstructions of pottery kilns (Klett-Drechsel, 2015). His experience was a great help to us. The firing started with the loading the kiln. The total number of vessels, or to be more precise, the number of objects, varied between approximately 90 and 400, depending on the size. The amount of clay is much more significant than the number of vessels and will be documented more precisely in the future. Now, we can give just a very rough estimation - of ca. 100 kg of clay. This can be regarded as rather compact (Cardew, 1969, p.221). The vessels were stacked on the floor between the vents (See Figure 29). At the bottom, stacks were quite regular, base on base and rim on rim, with space between the stacks, and with increasing density to the top of the chamber. Stacking devices were usually not necessary.
For fuel we used waste from carpenters, shingle production and land cleaning, but less soft fuels than in non-kiln firings and more compact wood. The fuel was put into the firing tunnel. Between the stoking of fuel, the firemouth can be closed with a kiln door or a kind of huge tile made of dried cob (See Figure 27). During the first firing, we attained fractures in the dome. They did not influence the stability of the dome, but to avoid the flow of cold air into the firing chamber, the fractures had to be closed by applying a soft clay coating during the firing. While the firing atmosphere was rather accidental in the first firings, we were increasingly able to control the intended atmosphere. It was surprising that by already using one kiln and two clays we had reached nearly the whole spectrum of colours of fired clays (black, grey, brown, beige, white, ivory, yellowish, orange, brick-red, rosy). A strong reduction was done at the maximum temperature of the firing by adding a large amount of fuel and then closing all opening of the kiln and sealing with a clay coating.
We determined the temperature by pyrometric cones (See Figure 28) or, in some firings, only by estimating it by the radiant heat colour. We reached maximum temperatures between 800 to 900 °C. We are planning to do precise temperature measurement and recording at different spots in the kiln (see below). Another checking method was to use previously positioned, little sample vessels that were pulled out of the hot kiln with an iron hook to test the hardness and strength of the ceramics. The firing time up to the maximum temperature and the beginning of cooling usually takes approximately 16 hours. Cooling until the kiln can be opened takes another day. To avoid damage of the ceramics by cooling fractures, it is better to wait at least two days for cooling. The waste rate was less than 10 percent in kiln firings. We identified zones where there was a high risk of fractures - at the bottom of the firing chamber, and in the area close to the fire tunnel.
Our kiln firing experiences produced less concrete, practical results. They did raise new questions however. Some of our recorded observations referred to the design of the kiln. The sizes of the flues and vents have a big influence on the firing behaviour of the kiln in terms of both the absolute sizes and the proportions. For reconstructions of updraught kilns, Winter (1978, p.40-41) suggested ideal proportions of the inlet flue, the size of the raised floor, the sum of the intersectional area of all vents of the raised floor, and the exit flue. However, Winter states many excavated Roman kilns show less appropriate proportions. The measures and proportions of our kiln were chosen according to archeologically recorded kiln structures. But, according to the potter J. Klett-Drechsel who was present at the first firing, from a technical point of view, our firing tunnel is too narrow. The tunnel and the combustion chamber are small, so the fire does not have much space to develop (cf. Winter, 1978, pp.37, 40-41). The small size of the firing tunnel is probably one of the reasons for our quite long firing time of 16 hours until the maximum temperature was reached. In the archaeological kilns that we used as analogies and reference, there is no room for differing interpretation. At least some kiln structures were quite well-preserved and recorded (e.g. Heege, 2007, Cat. 116), so the recorded kiln dimensions and proportions are basically reliable. What could be the reason for the narrow firing tunnel? Does it represent a decline of knowledge and skills in kiln building and firing? Can it be explained by quite different techniques in stoking and firing, including the use of soft fuel like brushwood? Or is it even an aid to ensure a steady temperature increase?
Another result from our kiln firing experiences is scepticism towards the significance of kiln experiments. Firing a potter’s kiln is a complex process. There are many parameters that influence both the progress and the result of the firing of which the kiln is but only one. It is not only the plan and the measures of the kiln that determines the firing, it is also the building material of which the kiln is constructed of, the surrounding soil, the weather (humidity, wind, atmospheric pressure, temperature) and the inserted vessels. The stack method in which they are inserted into the kiln has a great influence (Heege, 2007, p.15), as well as their amount, clay composition and humidity. The fuel (type of wood, shape and structure etc.) and the stoking or firing technique is of great interest. If we want to compare different kiln experiments to compare different kiln types of different periods or regions, not all of these and possibly other variables can be controlled, but at least they have to be identified and recorded. Otherwise we probably do not compare different kiln types, but rather compare actually different kiln teams, different kiln building materials etc.
Archaeometric research: Cooperation with the CCA-BW
We have been collaborating with the Competence Centre Archaeometry Baden-Wuerttemberg (CCA-BW) since 2017. Founded in 2016, the CCA-BW was developed from the archaeometry section of the applied mineralogy work group and is headed by mineralogists from the University of Tübingen, Germany (Ch. Berthold, K. G. Nickel and K. Bente). The scientists from CCA-BW are thankful they have the opportunity to conduct field studies and experiments on our site and to examine technical processes not only within the lab but in vivo. On the other hand, Campus Galli, are thankful to have help with documenting and examining our activities and to intensify our scientific work and network. An official memorandum of cooperation contract between Campus Galli and the University of Tübingen is being finalized at the moment and will be signed in April 2018. Our first collaborative projects have already commenced in 2017, when two courses were held by Ch. Berthold, T. Kiemle and S. Amicone in collaboration with Campus Galli.
Our first joint project was a pit firing experiment in July 2017. It was a part of the course Material Science and Archaeological Ceramics: Ancient Pottery and their Pigments that was held by S. Amicone, Ch. Berthold and T. Kiemle. Together with their students they came to the Campus Galli potter’s workshop. We started with preheating the pots next to the fire for several hours. Then the pots were stacked for the actual firing and surrounded with fuel. After igniting, more fuel was stoked. After 95 min we covered the fire with earth to cool it and to get a reducing atmosphere until we excavated the pots the next day.
We used thermocouples to measure the temperature, starting with the preheating, and then we inserted thermocouples at four different positions in the stack of vessels to get the firing curve of the actual firing as well as the cooling. The temperature was tracked on a display during the firing.
We observed a fast increase of temperature at the beginning of the firing. There were large temperature differences of several hundred °C between the different positions inside the rather small stack of vessels. Maximum temperatures varied between ca. 600°C and ca. 900°C, depending on the measuring position. We received smudged (carbon black) vessels, indicating a reducing atmosphere. The waste rate was around 1/3. The whole firing process was documented by the students who noted the details in a preliminary report.
It was exciting to track temperatures on the display during the whole firing process. This also gave us new ideas for the improvement of firing and stoking techniques. But our observations and results are quite typical for what is known about non-kiln firing techniques in the ethnographic literature (Rice, 1987, pp.153-158; Mershen, 1988, p. 92-93; Wotzka, 1991, p.297 (list); Schneider, 1991, pp.80-82; Gruner, 1991, pp.99-100; Herbich and Dietler, 1991, pp.125-127; Mershen, 1991, pp.168-169; Lucke, 1991, p.335-336). It was not our aim to create innovative contributions to the research of firing technology, but rather to test out our cooperation, to get to know each other’s mode of operation and find out which practical problems occur in measuring an open firing. The firing can be regarded as a preliminary or pilot experiment as an aid to design further experiments that are planned in the future.
Another aim of the firing experiment was to teach students about carbon black. We fired small sample vessels in the pit, which had stone-polished and unpolished zones. Graphite was applied to a few sample vessels. The samples were intended to train students to identify and distinguish between glossy carbon black and graphite in the lab.
The second course of the CCA-BW in collaboration with Campus Galli included a visit to Campus Galli to learn about clay processing methods. This was held in October 2017. The students executed important steps of clay processing on their own in Campus Galli. We performed two processing methods: the levigation and the drying-crushing-sieving-soaking process, as described above. Although levigating one clay batch takes weeks, it was possible to do this because various clay batches in different stages of processing were available simultaneously. From the different stages of processing, as well as from different grain size fractions (i.e. both sieving grades and layers of levigated clay), the students took samples to form and fire bricks in the lab as thin sections for ceramic petrography.
We have many research ideas and questions and are preparing further collaborative experiments and courses. There are many aspects to ceramic production and use that could be examined in a combination of archaeometry and experimental archaeology studies. Though the cooperation between Campus Galli and CCA-BW started with ceramic research, other early medieval crafts and technologies can be studied in the future.
Acknowledgements
Johannes Klett-Drechsel, Fredelsloh (D), Katja Thode, formerly University of Tübingen (D), Johannes Reller, Yvonne Arpino, Michael Albers, Sarafina Machholz, from the university of Tübingen (D), contributors from the “Werkstättle e. V.”-project for unemployed people and our Campus Galli volunteers who are too many to list all their names, and my colleagues from Campus Galli, Dr. Christoph Berthold, Dr. Silvia Amicone and Tobias Kiemle from CCA-BW Tübingen with their students.
Bibliography
Cardew, M., 1969. Pioneer Pottery. London: Longman Group Ltd.
Engelbrecht, B., 1991. Töpferei von Patamban (Michoacán, Mexiko). In: Lüdtke, H. and Vossen, R. W., eds. Töpfereiforschung – archäologisch, ethnologisch, volkskundlich. Beiträge des internationalen Kolloquiums 1987 in Schleswig, Töpferei- und Keramikforschung 2. Bonn: Habelt. pp.179-200.
Gross, U., 2009. Keramikverbreitung und herrschaftliche Strukturen. Beispiele aus dem Mittelalter und der Frühen Neuzeit in Südwestdeutschland. In: Krausse, D. and Nakoinz, O., eds. Kulturraum und Territorialität. Archäologische Theorien, Methoden und Fallbeispiele, Kolloquium des DFG-SPP 1171, Esslingen 17. - 18. Januar 2007, Internationale Archäologie 13. Rahden: Verlag Marie Leidorf GmbH. pp.159-175.
Gruner, D., 1991. Töpferei der Malinke. In: Lüdtke, H. and Vossen, R. W., eds. Töpfereiforschung – archäologisch, ethnologisch, volkskundlich. Beiträge des internationalen Kolloquiums 1987 in Schleswig, Töpferei- und Keramikforschung 2. Bonn: Habelt. pp.93-104.
Guadagnin, R., 2000. Fosses – Vallée de l'Ysieux. Mille ans de la production céramique en Île-de-France, Vol. 1: Les données archéologiques et historiques. Caen: Publications du Centre des Recherches Archéologiques Médiévales.
Guthnick, E., 1985. Erkennungsmerkmale einer Gefäßherstellung auf langsamen und schnellen Drehscheiben an einzelnen Scherben. Ausgrabungen und Funde 30(1), pp.1-5.
Hampe, R. and Winter, A., 1965. Bei Töpfern und Zieglern in Süditalien, Sizilien und Griechenland. Mainz: Verlag des Römisch-Germanischen Zentralmuseums.
Heege, A., 2007. Töpferöfen – Pottery kilns – Fours de potiers. Die Erforschung frühmittelalterlicher bis neuzeitlicher Töpferöfen (6.-20. Jh.) in Belgien, den Niederlanden, Deutschland, Österreich und der Schweiz. Basel: Archäologie Verlag.
Herbich, I., and Dietler, M., 1991. Aspects of the Ceramic System of the Luo of Kenya. In: Lüdtke, H. and Vossen, R. W., eds. Töpfereiforschung – archäologisch, ethnologisch, volkskundlich. Beiträge des internationalen Kolloquiums 1987 in Schleswig, Töpferei- und Keramikforschung 2. Bonn: Habelt. pp.105-136.
Herdick, M., 2015. 1000 Öfen und was nun? – Keramikstudien, Technikgeschichte und experimentelle Archäologie. In: L. Grunwald, ed. Den Töpfern auf der Spur. Orte der Keramikherstellung im Licht der neuesten Forschung (46. Internationales Symposium Keramikforschung des Arbeitskreises für Keramikforschung und des Römisch-Germanischen Zentralmuseums Mainz vom 16. bis zum 20. September 2013 in Mayen). Mainz: Verlag des Römisch-Germanischen Zentralmuseums. pp.225-235.
Keller, C., 2007. Karolingerzeitliche Töpferöfen am Vorgebirge – Zwei Beispiele aus Eckdorf und Walberberg, Nordrhein-Westfalen D. In: Heege, A., ed. Töpferöfen – Pottery kilns – Fours de potiers. Die Erforschung frühmittelalterlicher bis neuzeitlicher Töpferöfen (6.-20. Jh.) in Belgien, den Niederlanden, Deutschland, Österreich und der Schweiz. Basel: Archäologie Verlag. pp.205-217.
Kerkhoff-Hader, B., 1996. Rheinische Töpferscheiben und Töpferräder im interregionalen Vergleich. In: Lüdtke, R., and Vossen, R., eds. Töpfereiforschung zwischen Mittelmeer und Skandinavien, Beiträge des internationalen Kolloquiums 1990 in Hamburg, Töpferei- und Keramikforschung 3. Bonn: Habelt. pp.225-257.
Klett-Drechsel, J., 2015. Erfahrungen beim Nachbau eines mittelalterlichen Brennofens zum Brennen von Steinzeug. In: L. Grunwald, ed. Den Töpfern auf der Spur. Orte der Keramikherstellung im Licht der neuesten Forschung (46. Internationales Symposium Keramikforschung des Arbeitskreises für Keramikforschung und des Römisch-Germanischen Zentralmuseums Mainz vom 16. bis zum 20. September 2013 in Mayen). Mainz: Verlag des Römisch-Germanischen Zentralmuseums. pp.237-246.
Leterme, C., 2008. Töpferräder und Töpferscheiben: Archäologische Befunde und zeitgenössische Abbildungen. In: Melzer, W., ed. Archäologie und mittelalterliches Handwerk. Eine Standortbestimmung, Beiträge des 10. Kolloquiums des Arbeitskreises zur archäologischen Erforschung des mittelalterlichen Handwerks, Soester Beiträge zur Archäologie 9. Soest: Westfälische Verlagsbuchhandlung Mocker und Jahn. pp.157-168.
Lucke, A., 1991. Vergleichende ethno-archäologische Untersuchungen zu Brenntechniken in vier nordmarokkanischen Töpferorten. In: Lüdtke, H. and Vossen, R. W., eds. Töpfereiforschung – archäologisch, ethnologisch, volkskundlich. Beiträge des internationalen Kolloquiums 1987 in Schleswig, Töpferei- und Keramikforschung 2. Bonn: Habelt. pp.319-338.
Lüdtke, H. and Vossen, R. W., eds. 1991. Töpfereiforschung – archäologisch, ethnologisch, volkskundlich. Beiträge des internationalen Kolloquiums 1987 in Schleswig, Töpferei- und Keramikforschung 2. Bonn: Habelt.
Mershen, B., 1988. Bemerkungen zur handgetöpferten Gebrauchskeramik in der Dorfkultur des ʿAğlūn (Jordanien). In: Vossen, R., ed. Töpfereiforschung zwischen Archäologie und Entwicklungspolitik, Töpferei- und Keramikforschung 1. Bonn: Habelt. pp.81-95.
Mershen, B., 1991. Frauentöpferei in Jordanien – Ausprägung und Kontext eines Hauswerks. In: Lüdtke, H. and Vossen, R. W., eds. Töpfereiforschung – archäologisch, ethnologisch, volkskundlich. Beiträge des internationalen Kolloquiums 1987 in Schleswig, Töpferei- und Keramikforschung 2. Bonn: Habelt. pp.157-178.
Papousek, D. A., 1991. Paradoxie in los Pueblos: Töpferei in Zentral-Mexiko. In: Lüdtke, H. and Vossen, R. W., eds. Töpfereiforschung – archäologisch, ethnologisch, volkskundlich. Beiträge des internationalen Kolloquiums 1987 in Schleswig, Töpferei- und Keramikforschung 2. Bonn: Habelt. pp.201-218.
Rice, P. M., 1987. Pottery Analysis. A Sourcebook. Chicago/London: The University of Chicago Press.
Rieth, A., 1965. Zur Frage der römischen Töpferscheibe. Fundberichte aus Schwaben, N.F. 17 (Festschrift G. Riek), pp.153-155.
Rogier, M., 2015a. Mittelalterliche nachgedrehte Keramik. Überlegungen zur Definition, Bestimmung und Interpretation am Beispiel Baden-Württemberg, Lehr- und Arbeitsmaterialien zur Archäologie des Mittelalters und der Neuzeit. Tübingen: Verlag des Vereins für Archäologie des Mittelalters, Schloss Hohentübingen.
Rogier, M., 2015b. Nachgedrehte Keramik – Deutung von Herstellungsspuren mithilfe Experimenteller Archäologie. In: L. Grunwald, ed. Den Töpfern auf der Spur. Orte der Keramikherstellung im Licht der neuesten Forschung (46. Internationales Symposium Keramikforschung des Arbeitskreises für Keramikforschung und des Römisch-Germanischen Zentralmuseums Mainz vom 16. bis zum 20. September 2013 in Mayen). Mainz: Verlag des Römisch-Germanischen Zentralmuseums. pp.247-256.
Rogier, M., (in press) Töpfern wie im 9. Jahrhundert. Eine rekonstruierte Werkstatt im Campus Galli. In: H. Stadler and L. Obojes, eds. Keramik zwischen Produktion, praktischem Gebrauch, Werbung, Propaganda und Mission. 50. Internationales Symposium Keramikforschung Innsbruck, Tirol vom 24. - 29. September 2017 = Nearchos 23. Innsbruck: Golf Verlag.
Rye, O. S., and Evans, C., 1976. Traditional Pottery Techniques of Pakistan. Washington, D. C.: Smithsonian Institution Press.
Rye, O. S., 1981. Pottery Technology: Principles and Reconstruction. Washington, D.C.: Taraxacum.
Schedl, B., 2014. Der Plan von St. Gallen. Ein Modell europäischer Klosterkultur. Wien: Böhlau.
Schneider, K., 1991. Töpferei der Lobi. In: H. Lüdtke and R. W. Vossen, eds. Töpfereiforschung – archäologisch, ethnologisch, volkskundlich: Beiträge des internationalen Kolloquiums 1987 in Schleswig, Töpferei- und Keramikforschung 2. Bonn: Habelt. pp.65-92.
Schreg, R., 1998. Keramik aus Südwestdeutschland. Eine Hilfe zur Beschreibung, Bestimmung und Datierung archäologischer Funde vom Neolithikum bis zur Neuzeit, Lehr- und Arbeitsmaterialien zur Archäologie des Mittelalters und der Neuzeit. Tübingen: Verlag des Vereins für Archäologie des Mittelalters, Schloss Hohentübingen.
Schreg, R., 2012. Keramik des 9.-12. Jh. am Rhein. Forschungsperspektiven für Produktion und Alltag. In: Grunwald, L., Pantermehl, H. and Schreg, R., eds. Hochmittelalterliche Keramik am Rhein. Eine Quelle für Produktion und Alltag des 9. – 12. Jh., Tagung im Römisch-Germanischen Zentralmuseum, 6.-7. Mai 2011, RGZM Tagungen 13. Mainz: Verlag des Römisch-Germanischen Zentralmuseums. pp.1-19.
Schütz, I, 2006. Agost/Alicante, ein Töpferzentrum in Europa: Bamberger Beiträge zur Europäischen Ethnologie 8. Bamberg: K. Urlaub GmbH.
Tremp, E., 2014. Der St. Galler Klosterplan (Begleittext). In: Stiftsbibliothek St. Gallen, ed. Der St. Galler Klosterplan. Faksimile, Begleittext, Beischriften und Übersetzung. St. Gallen: Verlag am Klosterhof.
Tzschoppe, J., 2000. Ausgrabungen von Keramikbrennöfen – worauf man/frau achten sollte. In: Mämpel, U. and Endres, W., eds. Der keramische Brand, Beiträge zum 32. Internationalen Hafnerei-Symposion des Arbeitskreises für Keramikforschung in Bremen vom 27. September bis zum 3. Oktober 1999, Veröffentlichungen des Arbeitskreises für Keramikforschung 1. Höhr-Grenzhausen: Verlag der Fachbuchhandlung Hanusch & Ecker. pp.111-118.
Vossen, R. W., 1991. Töpferei in Marokko – Vier Fallbeispiele. In: H. Lüdtke and R. W. Vossen, eds. Töpfereiforschung – archäologisch, ethnologisch, volkskundlich: Beiträge des internationalen Kolloquiums 1987 in Schleswig, Töpferei- und Keramikforschung 2. Bonn: Habelt. pp.137-156.
Winter, A., 1978. Die antike Glanztonkeramik. Praktische Versuche (Keramikforschungen III. Heidelberger Akademie der Wissenschaften. Kommission für antike Keramik). Mainz: Philipp von Zabern.
Wotzka, H.-P., 1991. Keramikbrand im offenen Feuer: Vergleichende Analyse pyrometrischer Daten aus dem Töpferdorf Ikenge (Äquatorregion, Zaire). In: H. Lüdtke and R. W. Vossen, eds. Töpfereiforschung – archäologisch, ethnologisch, volkskundlich. Beiträge des internationalen Kolloquiums 1987 in Schleswig, Töpferei- und Keramikforschung 2. Bonn: Habelt, pp.289-318.