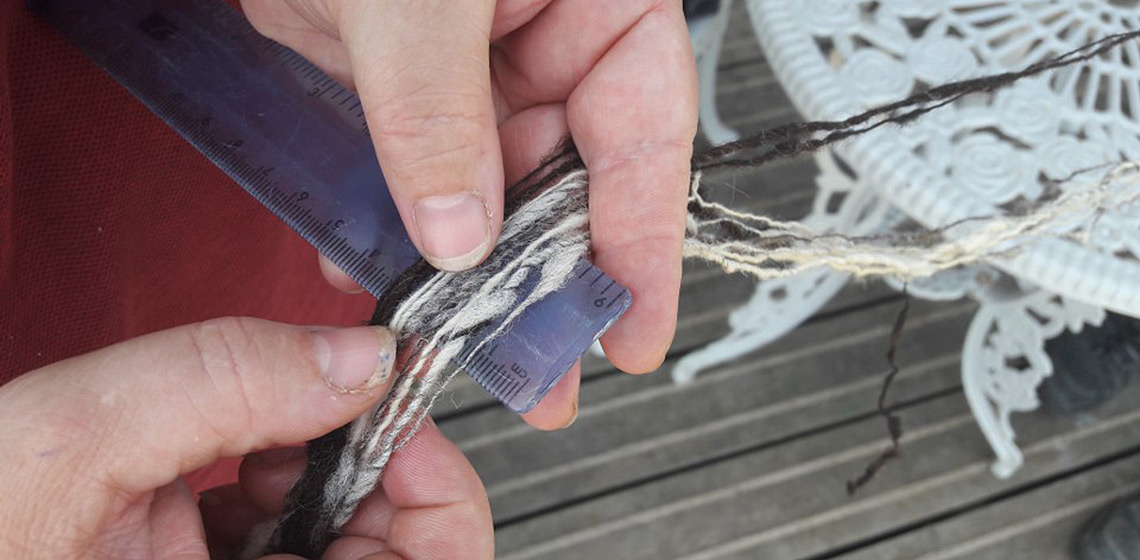
From 2015 to 2017 a series of weaving experiments using warp-weighted looms were conducted in the roundhouses at Butser Ancient Farm. The aim was to focus on the working environment within the roundhouse and to assess any potential issues that may occur whilst weaving, including benefits. The results of the research would also assist in evaluating any seasonal patterns which cause productivity to increase, decrease or even stop. The amount of labour time required to produce a piece of cloth from the fibre would also be examined, alongside tests to investigate theories for the best position for weaving to take advantage of the longer days (Ellison & Drewent, 1971)
The authenticity and efficacy of the warp-weighted loom has been accepted by archaeologists since the 1960s. The reason behind this project using the warp-weighted loom was that the Scandinavian countries used it to weave, and they are supposed to be the nearest neighbours of Britain (Cunliffe, 2007; Koch & Cunliffe, 2013) with a similar climate (See Figure 1). There have been numerous experiments on textiles using warp-weighted loom within the home (Andersson Strand, 2015; Barber, 2003; Cybulska & Maik, 2007; Dimova, 2016; Gleba, 2012; Hansen, 2014; Yilmaz, 2016). Five different looms have been used through later prehistoric Europe; the back-strap, the ridged horizontal and vertical looms, the table loom (horizontal loom with roll bar) and the warp-weighted loom. Further discussion on this point is in the article, 'A discussion on the position of weaving in the society of prehistoric Britain'.
There are limitations to this experiment, firstly the weaver and spinner are 21st century people used to all the comforts of modern-day life. Secondly, Butser Ancient Farm is located in the south of Britain on a chalk and flint bed surrounded by modern farming in a landscape very different from that of the later prehistoric period. Thirdly, the reconstructed houses are either plank construction with thatch or wattle and daub with a thatched roof, all single storey. The wattle and daub houses had a limewash with ochre pigment within the lime wash to provide colour. The walls and doorways' height vary and are different styles, while some have porches constructed within the houses (See Table 1). Still, all are linked in with archaeological sites around Britain.
outer wall diameter (m) | Inter wall diameter | Door orintation | Height of the door | width of opening | Direction of door swing | Height of walls | construction of floor | Wall constuction | Wall covering | Fire | Roof | |
LW | 14,5 | 10,5 | SE | 1,5 | 2,8 | inwards | 1.2-1.8 | Chalk compacted | wattle & Daub | lime wash | centre | Thatched |
MYG | 9,25 | 7,25 | SSE | 1,4 | 1,7 | outwards | 1.2-1.6 | Compact clay/mud | wattle & Daub | clay white and red | centre | Thatched |
M59 (1)* | 4,2 | N/A | S | 1,6 | 1,1 | inwards | 2 | Compact clay/mud | wattle & Daub | clay- white and yellow | none | Thatched |
M74 | 6,3 | N/A | NNW | 1,3 | 1,4 | inwards | 1,5 | Compact clay/mud | wattle & Daub | clay- white and yellow | centre | Thatched |
CS1 | 7,5 | N/A | SSE | 1,7 | 1,3 | outwards | 1.2-1.6 | Chalk compacted | Oak planks | oak planks - silver | centre | Thatched |
M59 (2)** | 4,3 | N/A | SSE | 1,6 | 1,1 | n/a | 1,5 | Mud | wattle & Daub | no covering | centre | Thatched |
CS14** | 9,1 | N/A | SSE | 1,9 | 2 | n/a | 2,2 | not finish | wattle | no covering | not finish | Thatched |
house where the loom were located for the experiment | ||||||||||||
* | 2 looms within house | |||||||||||
** | additional house built which allowed light reading to be taken. |
Table 1. Showing the measurements and construction of the house used
All of the houses had a central lit hearth, accept one, the control house. None of the buildings had chimneys or purpose-made smoke holes, windows or openings other than the door. Light reading, humidity and temperatures were recorded throughout the experiment and smoke movement and patterns observed. The day-to-day activity on the farm continued and was incorporated into the experiment during the period. The primary variable was the weather throughout the calendar year.
Spinning on a drop spindle could have been done all year round as little light is needed, and with experience, it can be done by feel only. However, learning to spin would need to be done in the spring and summer when the light is good, after which it is a matter of practice to hone the technique. Plant fibres which are generally straight require a slightly different method to ensure the twist holds, including passing the fibres through the water. The plant fibre yarn created tends to have little or no elasticity, hence the different technique. The whorl's diameter and weight may indicate the thickness of the thread and possibly the fibres used. The weight and diameter verse the length of shaft, which produces a finer woollen thread or plant fibre thread. It does not matter if the whorl is made of stone, wood, glass bead, bone, leather, clay or metal; it is the ratio of the diameter to the whorl and the shaft. The shaft with an even weight distribution provides the best momentum and downward drafting, providing increased production (See Figure 2). The additional weight spun yarn on the spindle requires a change in technical application. Therefore, it is crucial to place the spun yarn around the shaft in a cone shape, regardless whether the whorl is at the top or the bottom. Five volunteers were recruited to spin yarn, on average, with an aim of five metres per hour spun. The limitation is due to muscle strain on arms stretching to spin yarn. The rate at which the thread is spun at the start of the day is higher than the daily average. The rate drops by end of the day due to tiredness and because the spindle becomes heavier (See Table 2).
Hours spun | Length spun in metres (m) | Length per hour | |
Black Jacob | 3 | 14,5 | 4,8 |
Brown Manx | 2 | 8 | 4 |
White Shetland | 4 | 19 | 4,75 |
Brown and white mixes Manx | 8 | 46 | 5,77 |
Black and white mixed Jacob | 15 | 60 | 4 |
Heberidean | 3 | 15 | 5 |
Black Jacob | 4 | 20 | 5 |
Average | 5,57 | 26,06 | 4,76 |
Table 2. The result of spinning to discover the average length per hours on different wool fibres
There are two different techniques in drawing the fibres; there is the English long-draw (other countries have different names for it) and worsted. These depend on personal preference and size of the fibres. Longer fibres work well with the English long-draw, especially plant fibres and can provide a thin yarn. Hand spinning results in a thread which varies in width and strength. The weavers' skill mixes the different thickness of yarn into the weave and still makes the cloth durable (See Figures 3 and 4).
The weaver's first task is to create the selvedge, a densely woven fabric that provides the strength and locking mechanism for the warp threads. It gives a strong material to be attached to the loom's suspension arm, attached to the roll bar. The selvedge can be created using two methods, the tablet weave, which provides a whole array of patterns (Knudsen & Grömer, 2013) or the Ingle loom, which provides a limited variety of designs. However, the tablet weave does take longer to create than the Ingle weave method. Therefore, if time is a constraint, the Ingle weave method would be the one to use. In many ways, the Ingle weave method requires less skill, patience and concentration than the tablet weave. Both methods were used during this experiment, as checks and balances on each result. It must also be noted that there is a possibility that the Ingle weave can have the warp threads come out both sides and then folded (See Figure 5). Then folded fabric can be attached to the suspension and roll bar and make a clean ending, or decorative band.
The thickness or number of yarns required to make the cloth will determine the length of time needed. Eight, eleven and fourteen threads per centimetre are the most common in Britain's archaeological data during the Bronze and Iron Ages (Greenwell, 1865; Parker Pearson, et al., 2016). Eighteen yarns per cm are more common during the Roman Period, but this may result from textile survival in the archaeological record. Elsewhere in Europe and Eurasia, more delicate yarn cloth is produced.
The warp yarn needs to be straight, and we need to decide which pattern of weave is to be used. The complicated weaves require more heddles (as the heddles is the machinery that provides the weaver easy placement of the weft (horizontal) yarn to pass through the gap the pulled heddle provides and can provide a number of pattern combinations depending which levers (heddles) to pull using a binary system. Therefore, the yarn is placed on heddles once the decision is taken. All the back yarns are placed on one heddle, weighted, and chained in place. The front threads are then attached to another heddle (this is optional as it depends on the angle of the loom and space) weighted and chained, ready for a tabby (plain) weave. If a twill is required, then the back, middle A, middle B and front array of warp yarns will be placed on heddles using the same process as described. Beads or small weights can be used as indicators to which direction and heddle the weaver is on to provide the pattern required and it is essential when leaving the work for the following day.
Setting up a loom takes approximately eight to ten days (seven hours per day) with good and reliable light, depending on the complexity of the weave and thickness of the yarn. Here the weaver's skill comes into its own. If the loom is not set up correctly, the weaver will have difficulty weaving, creating an inferior cloth and an extreme degree of frustration and irritation. It adds more time for little quality, and quality does matter! If time is taken to set up correctly, weaving becomes easier, otherwise up to two hundred hours of work, is lost along with the yarn used.
The roundhouse is a superior shape for allowing maximum light into the house, as the vortex of the smoke disperses from the interior, keeping the temperature relatively consistent. Previous research has observed light within the roundhouse by shadowing observation but had not examined working light for tasks (Pope, 2007). The planked walls and the lime wash interior walls (or light ochre lime wash walls) provide additional light into the room by reflecting the light into the room and onto the loom. It was proven that where the wattle and daub was not lime washed, the light was reduced by fifty per cent.
Can a warp-weighted loom be used in a roundhouse regularly? Technically, yes, but there are some serious issues to consider. Firstly, the smoke over a period of time will discolour the fabric being woven. Secondly, the smoke dispersion rate varies depending on the atmospheric pressure difference between the house's interior and exterior, plus, the state of the fuel used, whether it is dry and well-seasoned, or not. The smoke ceiling will come down if the smoke cannot disperse out of the thatch. But if the fire is built up, it can cause too much smoke, thus bringing it down to the operational level of the loom.
Additionally, unburnt particles drift, providing extra heat to congregate around the cone point, which can ignite the thatch. The smoke ceiling can diffuse light and reflect it on to the loom (See Figure 6). The door can direct sunlight (Pope, 2007) on to the loom, but this depends on other factors such as the doorway's landscape and location. If the building has a lime washed exterior, this can help reflect light into the house. The door opens either in or outwards, left or right; there can be a single or double door. The best result for directing light was an outward opening door, but a double door opening outwards proved to be the preferred choice when we factored in wind and rain. The reason being that the half door closed helped reduce the rain spray into the house and onto the loom and weaver. Therefore, the weaver would not feel as damp and cold. Secondly, it reduced the wind preventing the loom weights hitting the ankles with any force.
However, the real problem is the loom in the roundhouses. The loom used was approximately two metres high and mounted at an angle of roughly 20 degrees. Over the period of 18 months the loom managed to damage the walls both in the plank and wattle and daub constructed houses. The planks pushed out; and the wattle and daub walls began to crumble, resulting in a weakness in the thatch, in turn. The roof needed re-thatching and the walls repairing. These repairs would have taken time and resources to fix, and the frequency of the repairs would probably make the activity unsustainable within the home.
The loom itself did not fare well either. During the experiment, one loom broke, and the second loom became unusable due to the number of repairs it has already received. The reason for the breakage is twofold. Firstly, the physics of the loom against the wall and its construction (See Figure 7). The strongest shape in geometry is the triangle; in a longhouse, the loom against the wall is a triangle; therefore, it is sturdy and moves very little compared to a roundhouse. Due to its concave nature, the roundhouse creates a 'D' shape contact of the wall, which has two points of the loom touching the wall, because of weights swinging at the bottom of the loom. As the heddles move horizontally outward, combined with the pull, it caused the loom to move and rock. It is less of a problem within a longhouse because the force of the weight is distributed around the wall, along the roll bar or pivot bar, as this is a large contact point. The loom is not fully supported on the roundhouse's concave walls, which causes the roll bar to bend and flex. Over time, the roll bar's joint becomes weak, causing it to break, bringing all the cloth down with it. The loom legs also bow inwards due to the wall's curvature, putting extra pressure on the loom's joints near the roll bar, weakening the joints. Finally, this compounded by woodworm attacking the loom weakens the machinery as a whole, regardless of whether a longhouse or roundhouse is used.
Interestingly, the season for weaving in the roundhouse is not what one would think. Weaving (this includes setting up the loom) can be done from the first week of March to the third week of June. Weaving can still continue into July and August, but the sun's elevation and the early and late light intensity can restrict production time. In the roundhouse, weaving stopped at 10 am. It was restarted at 6 pm until between 8 to 9 pm by September, time increasing through October and November (See Figure 8). By October and November, it was no longer possible to set the loom as it was too dark to do the intricate work. Setting up the loom is recommenced in March. Weaving was seriously reduced in December to 10 am to 1.30 pm (See Figure 9). In January, weaving stopped at the end of the second week. February was too dark to weave regardless of the weather. In March, the weather improved, and weaving could start from March 1. However, one year, weaving started a week later due to stormy, icy, wet weather which prevented the sun penetrating through to the interior.
This experiment concluded that warp-weighted looms can be used in roundhouses, but the house needed to be repaired annually, and the loom monitored for weakness and breakages. The best location for weaving is the right-hand side as you walk in through the door, and opposite to where the weights have been found in the archaeological record in Danebury , Glastonbury and Little Woodbury with the whorl weights (Bersu, 1940: Brailsford, 1948: 1949: Coles & Minnitt, 2000: Cuncliffe, 2003; 2011: Fisher, 1985: Ryder, 1993). Finally, assuming weaving was conducted in these roundhouses, the season of weaving is March to June reduced between June and August, then picking up for September, decreasing again at the end of November into December and stopping entirely from January until March (See Figure 8). Therefore, the season is different to previous archaeological thinking which had weaving conducted in the spring and summer months (See Figure 9). The labour-hours needed to create enough cloth is high to the point (See Table 3) that it cannot be sustained as part of a daily routine to clothe the entire home unit, never mind the community. This implies that weaving was a focussed and vocational trade, like metalworking.
6 Spinners + Weaver | 6 Spinners + Weaver | 6 Spinners + Weaver | 6 Spinners + Weaver | Single Person | |
Plain weave | Plain Weave | Twill 2.1 | Twill 2.2 | ||
Spinning | 80 | 80 | 80 | 80 | 480 |
Set up | 236 | 236 | 236 | 236 | 236 |
Weaving | 300 | 180 | 196 | 210 | 300 |
Hours | 616 | 496 | 512 | 526 | 1012 |
Days | 102,6 | 72,6 | 85,3 | 87,6 | 167,6 |
14.6 wks | 10.3 wks | 12 wks | 12.5wks | 24 wks |
Table 3. Average time taken to create the different weaves to assess if weaving could be achieved with in a community or home setting.
Bibliography
Andersson Strand, E., 2015. First Textiles. The Beginnings of Textile Manufacture in Europe and the Mediterranean 7th-8th May 2015. Copenhagen, The Danish National Research Foundation's Centre for Textile Research and the National Museum of Denmark.
Barber, E., 2003. Reconstructing the ancient Argean and Egyptian textile trade. In: D. Jenkins, ed. The Cambridge history of western textiles. Cambridge: The University of Cambridge, pp. 104-111.
Bersu, G., 1940. Excavations at Little Woodbury, Wiltshire. Proceedings of the Prehistoric Society, Issue 6, pp. 30-111.
Brailsford, J., 1948. Excavations at Little Woodbury, parts II. Proceeding of the Prehistoric Society, Volume 14, pp. 1-23.
Brailsford, J., 1949. Excavations at Little Woodbury, parts IV and V. Proceeding of the Prehistoric Society, Volume 15, pp. 156--68.
Coles, J. & Minnitt, S., 2000. Industrious and fairly civilised: The Glastonbury lake village. Taunton: Somerset County Council Museums.
Cunliffe, B., 2003. Iron Age Communities in Britain. London: Routledge.
Cunliffe, B., 2007. Continent cut off by fog: just how insular is Britain?. Scottish Archaeological Journal, Volume 29, pp. 99-112.
Cunliffe, B., 2011. Danebury Hillfort. Stroud: The History Press.
Cybulska, M. & Maik, J., 2007. Archaeological Textiles- A need for new methods of analysis and reconstruction. Fibres and Textiles in Eastern Europe, 15(5-6), pp. 64-65.
Dimova, B., 2016. Textile Production in Iron Age Thrace. European Journal of Archaeology, pp. 1-26.
Ellison, A. & Drewent, P., 1971. Pits and Postholes in British Early Iron Age. Proceedings of Prehistoric Society, 38(01), p. 183.
Fisher, A., 1985. Winklebury Hillfort: A study of an artefact distraction from subsoil features. Proceedings of the Prehistoric Society, pp. 51-167.
Gleba, M. C. J., 2012. Textile Production in Bronze Age Miletos: First Observations. [Online] Available at: < https://www.academia.edu/2509295/... > [Accessed 16 03 2017].
Greenwell, W., 1865. Notice of the examination of ancient grave-hills in the North Riding of Yorkshire. Archaeological Journal, Volume 22, pp. 241-64.
Knudsen, L. & Grömer, K., 2013. Discovery of a new tablet weaving techniques from the Iron Age. Archaeological Textile Review.
Koch, J. & Cunliffe, B., 2013. Celtic from the West 2: Rethinking the Bronze Age and the arrival of Indo-European in Atlantic Europe. Oxford: Oxbow.
Parker Pearson, M., Needham, S. & Sheridan, J., 2016. Bronze Age tree-trunk coffin burials in Britain. In: N. Melton, J. J. Montgomery & C. Knusel, eds. Gristhorpe Man: A life and death in the Bronze Age. Oxford: Oxbow.
Pope, R., 2007. Ritual and the roundhouse: a critique of recent ideas on the use of domestic space in the later British prehistory. In: C. Haselgrove & R. Pope, eds. The earlier Iron Age in Britain and the near continent. Oxford: Oxbow, pp. 204-229.
Ryder, M., 1993. Wool at Danebury: A speculation using evidence from elsewhere. Oxford Journal of Archaeology, 12(3), pp. 305-320.
Yilmaz, D., 2016. Late Bronze Age textile tools from Maydos Kilisetepe in Gallipoli (Turkey) and their Aegean Connections. [Online] Available at: < https://www.academia.edu/Documents/in/Ancient_Textiles?page=3 > [Accessed 15 05 2017].