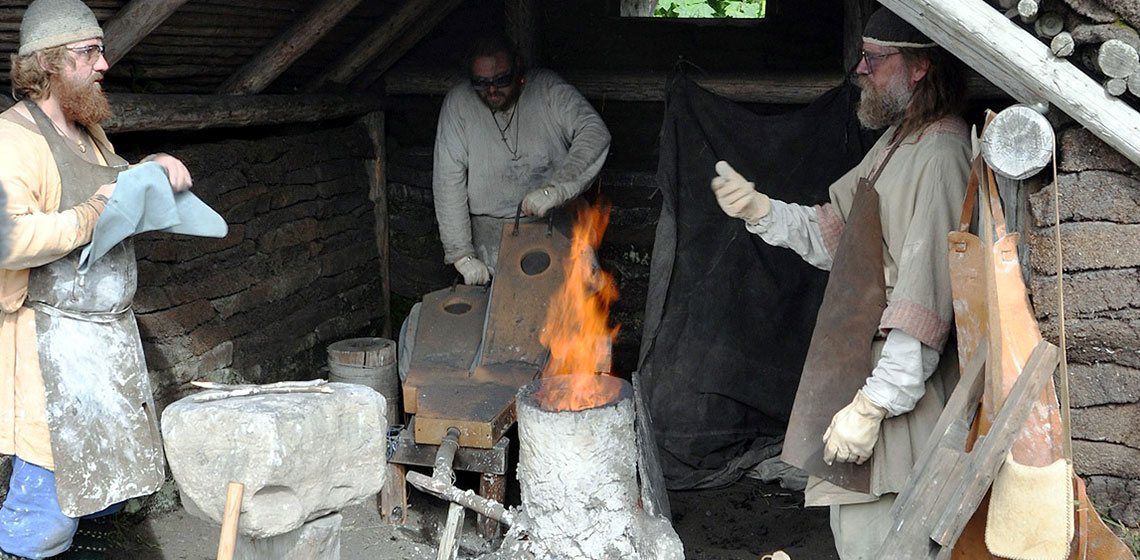
Few ancient processes are as mysterious as smelting ore into metallic iron. Just how, exactly, is this done? The exact processes used by the ancients are unknown, but modern experiments can suggest some possibilities. This essay will concentrate on describing a proven working system, based on Migration Era models, which has repeatedly produced historic type iron blooms. Although labour intensive, the small scale makes this method ideal as a prototype for public demonstrations.
Building and operating a small bloomery iron furnace is certainly a wonderful public demonstration for any museum or living history site. It is however a complex technical process, with many individual factors combining for success. Over the last decade in North America, small teams of blacksmiths have developed predictable working methods through trial and much error. This direct practical experience can provide some insights into questions that even the best researched theories may not be able to solve.
Looking at prototypes from roughly 600-1000 AD in Northern Europe (Viking Age), archaeological samples show a variation in construction, the effect of local materials. Most are more durable 'industrial' furnaces, often dug into the edge of an earth bank, or supported by a ring of large stones (Pleiner 2000).
Still, these furnaces share the following elements:
- Internal diameters, in the range of 30 - 50 cm
- A bellows providing forced air
- Short shaft heights (although archaeology is often not clear)
- Use of primary bog iron oreThe term ‘primary bog ore’ is used to describe an FeOOH material which:
• is newly formed
• is a product of the specific chain of iron rich bedrock, leached by tannic acid bog water, then deposited via the action of bacteria along the margins of small streams immediately below the source bog. - Some provision for taping off slag
The objective is to produce a dense mass of low carbon iron, in the range of 3 - 8 kg in size. The furnace described below has repeatedly created larger blooms (into the 10 - 20 kg range). Although the overall efficiency of the operation increases with larger volumes of ore, it becomes increasingly difficult for workers to manipulate these larger masses.
The furnace is a cylinder of clay filled with charcoal, with high combustion temperatures supported by the injection of air into the base of the furnace1
. Once fully ignited, ore is added in small batches, while keeping the shaft filled with charcoal. In simple terms, burning charcoal creates superheated carbon monoxide (CO) gas, which reacts with the iron oxide (Fe2O3) contained in the ore. In effect, the more reactive CO rips off the oxygen, leaving metallic iron behind. This iron is heavier, so it falls to the base of the furnace. A liquid glassy slag also forms, composed of melted furnace wall, silica from the ore, and charcoal ash. Falling to the colder base of the furnace, it congeals, forming a bowl shape. The descending iron particles collect inside the liquid pool of slag within this bowl into the bloom mass. Excess slag may have to be tapped off to prevent blocking the air flow at the tuyere. The bloom is finally extracted while hot, either through the top or bottom side of the furnace, then hammered to consolidate it.
There is a relationship between furnace size, position of the air system, air volume required, the nature and size of the ore particles, the size of the charcoal fuel, and the best sequence of adding both charcoal and ore. Changing any one of these variables will alter the nature of the bloom produced. Using the wrong combination may result in there being no effective production of iron at all.
The working system described here is based largely on the pioneering work of Lee Sauder and Skip Williams, with further refinements at a series of annual workshops with these two, Mike McCarthy and myself. It has been proven through successful application in over two hundred individual smelts.
The furnace described has walls in the range of 5-10 cm thick which can withstand some internal erosion, but cracking of the walls on initial heating may become a problem. Sauder and Williams mix course beach sand with smaller proportions of clay, often more than half and half (Sauder and Williams)2
. The sand in the mix does not significantly expand on heating, limiting cracking.
My own team mixes straw chopped at 5 to 10 cm lengths with powdered clay (roughly 50/50 by volume)3
. The straw provides channels to vent trapped steam, burns out on the inner surfaces to create a better insulator, plus on the outer layers remains in place to re-enforce the structure.
A number of European teams, most notably Michael Nissen of Denmark, have demonstrated good results by mixing 50% dry, shredded, horse manure with the clay (Nissen)4
.
All three construction materials produce furnaces which can survive through several firings, even when free standing.
A good practical internal diameter (ID) for a working smelter is in the range of 25-30 cm. Below 20 cm ID, there can be problems with the balance between heat loss through the walls (area as a square) against available heat production (volume as a cube). Larger than 30 cm ID and the consumption of charcoal becomes massive.
The furnace should have 20 cm below the air entry point for the development of the slag bowl and bloom. At least 40 cm should be provided above the tuyere to allow for a working column of reactive gases. The ideal height of this combustion zone is determined by the amount of air (oxygen) applied. If there is extra height, excess heat above the combustion zone will drive off any water contained in the charcoal or ore, improving the overall efficiency of the burning. A good overall height for the smelter is thus 65 - 75 cm.
Using a pair of sheet metal forms, covered with a layer of newspaper, will speed construction, controls wall thickness and allows for standardized sizes in an experimental series. In a historic setting use a bundle of straw, twigs or thin wood splints, which can later be burned out. When building, care must be taken as additional clay mix is added not to press downwards, force which will result in collapsing the wall, increasing its thickness, rather than building it up higher.
Once the walls are ‘leather hard’, cut openings for the air system and the tap / extraction arch. Consider the working spaces (and viewing angles) around the furnace, starting with the hole for the air system. The lowest edge of the air pipe (tuyere) needs to be at least 15 cm above the hard bottom of the working furnace. This allows for sufficient space for the slag bowl and the developing iron bloom.
Some provision for slag tapping is suggested. A cut an inverted U shape from ground level, with the blade angled so that the sides of the cut are beveled outwards. This tap arch should not extend higher than the level of the air system hole (so 15 cm). If planing to extract the bloom through this arch, it needs to be roughly the same width as the interior of the furnace. If to be used only for tapping, the arch can be smaller (in the range of 20 cm wide x 15 cm high). Wrap the edges of the cut with paper and push the clay block back into place.
There are a different air systems possible, what is described here is an insert tuyere. Tuyeres made of copper or bronze sheet, ceramic tube, industrial ‘schedule 40’ mild steel pipe have all proven effective. Each specific material choice has its individual characteristics in use.
The ideal angle for the tuyere is between 20 - 25 degrees down from horizontal (Markewitz 2006)5
. Less angle, and the developing slag bowl sits too high and shallow, and will quickly engulf and ‘drown’ the tuyere. Too steep, and there is not enough room for the growing bloom, and the air blast will actually cut into and erode its surface. Set the tip of the tuyere roughly 5 cm beyond the interior wall. Further in than that, and the heat of the furnace simply erodes the tip off. Less, and the air blast tends to roll back over and errode the inner wall. (Any working furnace tends to modify itself internally to its ‘ideal’ configuration as a smelt progresses.) Finish by sealing around the tuyere with clay.
Once completed, the finished furnace needs to completely dry before smelt day. Gentle air drying is certainly effective, if time and environment permit. A gentle, long duration fire, using small wood splits or twigs can be applied to both inner and outer surfaces. Water remaining in the wall material expands into steam, which may crack (even spall off pieces), especially a problem with thicker walls.
Link the air supply to the tuyere using a Y shaped coupling, one branch being a straight line down into the furnace and having a removable end cap. This permits both direct observation, but more importantly gives an ability to probe and clear blockages. With modern equipment, standard threaded pipe sections make for easy assembly. If a hand bellows is used, a thick leather construction is ideal, as the flexibility of the leather reduces any vibration from the pumping from effecting the fragile clay walls around the tuyere.
Critical for an effective smelt is providing for sufficient air volumes. Sauder and Williams have determined the ideal volumes to be from 1.2 - 1.5 litres per minute, for every square centimeter of internal cross section area at tuyere level (Sauder & Williams, 2002). With lower air volumes, iron may be produced, but the results are most likely going to be lacy or fragmented pieces, and not the dense ‘puck’ blooms known from archaeological remains.
Volume in Litres per Minute.
Air blast must be constant, even a stoppage of as short as 3 to 5 minutes is likely to catastrophically drop temperatures, freezing the slag and resulting in an unrecoverable failure. An experienced bellows operator will be able not only to maintain consistent volumes over time, but also control working pressure of the blast. Too little pressure behind the blast and the air will not penetrate into the centre of the furnace. The result is a small and/or lacy bloom. Viking Age blacksmith’s bellows are often not able to produce the air volumes required. A simple measuring method is to time how long it takes the bellows to fill a large plastic garbage bag of known volume.
Also critical is ensuring a high enough iron content in the ore, a content of at least 50 % iron is required, higher if at all possible6
. The furnace system described has proved effective using a wide range of both natural ores and modern preparations. Each ore type has its own peculiarities, and fine adjustments in equipment and sequence may be required for the absolutely best results. Remember that bog iron ores are the result of a complex formation process highly dependent on local environmental conditions, sure to be much different now than in ancient times!
There is a relationship between a given furnace layout and the best possible size for both charcoal and the ore:
For charcoal, pieces too large allow the ore to fall through the reaction column too quickly for reduction. Too many small particles prevent effective air penetration, effecting combustion. For this furnace, the ideal is pieces broken then screened for 'walnut to pea' size - 25 to 5 mm.
For ore, the ideal size ranges between ‘pea to rice’ size - 5 to 2 mm, but retaining the 'dust'. Ore too fine may simply blow back out of the furnace, and tends to absorb excess carbon. Too large and the particles will not completely reduce to metallic iron. Some ore types should be roasted before breaking and adding to the furnace.
Slowly pre-heat the furnace, moving from small wood splits under natural draft, applying gentle air, and finally to pieces of rough charcoal under increasing air blast, typically for 60 - 90 minutes. Add graded fuel with full air, watching for the combustion zone to reach a full 40 cm above the tuyere, typically about 60 minutes. The combustion rate at working temperature should average 2 kg charcoal (standard ‘bucket’) every 8 - 10 minutes, a rate which should be maintained. At 6 minutes per bucket the furnace is running too hot, and production of a high carbon cast iron is likely. Over 14 minutes, and the furnace is too cold and may have problems maintaining an effective slag bath. Modifying air volume can most easily control burn rate.
Once the reaction column has been established, ore is added, starting with roughly 500 gm measures per charcoal bucket. Ore charges should be spread out evenly through the charcoal additions, not laid in thick slabs as is often shown in theoretical descriptions. The first 4-6 kg of ore establishes the working slag bowl. The temperature of the furnace will increase as the bowl is formed, marked by an increase in burn rate. Now larger charges of ore are added, slowly increasing to match (or even exceed) the weight of charcoal. An overly hot furnace (faster consumption) can be dampened by the addition of more ore. A colder furnace (longer consumption) may require higher air volumes.
The production of slag depends on a combination of character of the clay, silica content of the ore and the exact layout of the furnace. Sometimes the furnace will self tap through small cracks in the walls (incontinent7
). The sound of the air through the tuyere is of critical importance here. A reduction of sound means partial blockage of the tuyere, by congealed slag. This must be quickly knocked off by inserting a small diameter metal rod down the Y tube. A thumping / bubbling sound indicates that the slag bath has risen so high as to soon ‘drown’ the tuyere, and a tap must be made to drain the excess. Drain no more than is required, as the slag bath is the working heart of the smelter. Often simply prying open the tap arch is enough to crack the bowl and let the liquid pour out. If not, the metal rod is lightly hammered through the upper side wall of the bowl to form a small hole. Volume of the discharge can be controlled by raking dirt into the path of the flow.
Once the last charge of ore is added, it should be followed by a covering of two last charges of charcoal which are allowed to burn down inside the furnace. Preparation for extraction begins. In public demonstrations, this is a good time to gather together an audience, with a designated commentator.
With a top extraction any remaining charcoal is lifted out of the furnace, using a long handled scoop to expose the top of the liquid slag pool. Then a short section of log (10 cm diameter) is used to pound on the top of the bloom inside the hot furnace (Boonstra, van de Manakker and van Dijk 1997)8
. This will partially compact the metal while it still is at welding temperatures, plus partially loosen the bloom from the lower slag bowl. A metal rod with a small hook end is used to fully free the bloom. Special 'bloom tongs' are used to grab out the bloom and transfer it to the waiting anvil.
The advantage is that there is usually minimal damage to the furnace, which remains fully ignited if secondary working heats of the bloom are required. The negative aspect is that this work is done reaching down inside, while standing directly over, the blazing hot furnace. (Although this process is quite spectacular to the viewing audience!)
With a bottom extraction, first the enlarged tap arch block is pried open. As the slag bowl is normally adhered to the inner surface, this step often requires hammering at the harder parts of the slag with a long chisel tipped bar. Once this slag is pulled clear, expect a spilling of ignited charcoal as the inner workings of the furnace are exposed. It should now be possible to reach in with the tongs and grab the hot bloom mass. The advantage is that the workers are partially shielded from the extreme heat. The work is usually faster and less precise that top extraction. The disadvantage is that the bottom of the furnace is emptied, often making it difficult to re-heat the bloom for further working. There is often extensive damage to the lower part of the furnace.
Once the bloom is free, typically there will be a large amount of slag and lacy iron (called 'mother') clinging to the outside of the metallic bloom. A fast sequence of gentle hammering serves to knock free the slag and compress in the iron. Working on a wooden stump allows the mass to burn in slightly, better holding it in place. The bloom is easy to distinguish, as it retains its initial heat, while the slag cools quickly. The strikers will soon both feel the increased resistance of the exposed iron, along with a change in sound as the metal's surface is compressed. Ideally the consolidation work should be carried out as close to a 'bright yellow' welding heat as possible.
The perfect result is a dense and roughly 'puck' shaped bloom (oval to circular, flattened on top and bottom). An additional heating cycle may allow you to cut the bloom from the edge with an axe, using it like a chisel. With a high iron content ore, and providing there were high volumes of air provided, the expected yield should be in the range of 20 – 35 %.
With the method described, it has repeatedly proved possible to produce blooms virtually identical to those created by iron masters 1000 years ago. It must be remembered however, as with any experimental archaeology process, this system represents 'a' method, but not necessarily 'The' method, as used historically. Further experimental work remains, especially in the area of producing the required high air volumes using historic styled equipment.
Good Luck!
The author would like to thank the members of the Dark Ages Re-creation
Company (Ontario Canada) for their hard work and support over many smelt events.
About the Author:
Darrell Markewitz has worked as a consultant on the Viking Age, specifically related to museum programming and living history, since the early 1990's. He designed, built and installed the 'Norse Encampment' program for Parks Canada at L'Anse aux Meadows NHSC, and 'The World of the Norse' exhibit for the Cranbrooke Institute of Science. Other major exhibit work includes assisting on 'Vikings - North Atlantic Saga' for the Smithsonian Institution and 'Full Circle - First Contact' for the Newfoundland Museum. As a professional blacksmith, with over 30 years experience, he first became interested in the problem of Viking Age iron smelting methods as part of a Parks Canada research team in 2001. Since then he has conducted over 45 experimental smelts, and has observed as many more, in Canada, the USA and Denmark.
- 1Temperatures as high as 1500 C (2750 F) have been repeatedly measured. These have been recorded using multiple equipments, both digital and optical pyrometers, inside different smelting furnaces.
- 2Early work by Sauder & Williams at: http://iron.wlu.edu/
- 3A complete documentation for this experimental series is available at: http://www.warehamforge.ca/ironsmelting
- 4Michael Nissen documents his work at the Ribe Viking Centre (in Danish) at: http://www.jernmager.dk.
- 5Experiments with Sauder, Williams and McCarthy in February of 2005, Lexington Virginia USA.
- 6In the absence of laboratory analysis, Sauder suggests the following simple method of estimating iron content of a sample : A measured weight of ore is crushed and placed in a small jar, the fill with muriatic (hydrochloric) acid (commonly available at hardware stores). The solution is shaken every hour or two, and the top level of fluid drawn off and replaced every day. This process is repeated until the fluid remains clear. At this point the sample is dried, and start and finished weight compared. The difference will be essentially a measure of the amount of iron contained in the sample.
- 7Espelund, E. "The Iron Story", internal Parks Canada document, 2001
- 8A technique initially demonstrated in: 'Experiments with a Slag-Tapping and a Slag-Pit Furnace' Anneke Boonstra, Thijs van de Manakker & Wim van Dijk in 'Early Iron Production - Archaeology, Technology and Experiments' Lars Chr. Norbach editor
Bibliography
JOOSTEN, I., M van. NIE, and P. de RIJK, "Experiments with a slag-tapping furnace at the Historical-Archaeological Centre, Lejre", Early Iron Production - Archaeology, Technology and Experiments, vol. 3, Lejre, Historical-Archaeological Experimental Centre Lejre, pp. 81-92, 1997.
PLEINER, R., Iron in archaeology: the European bloomery smelters, Praha, Archeologicky ustav AV CR, pp. 400, 2000.
SAUDER, L., and S. WILLIAMS, "A Practical Treatise on the Smelting and Smithing of Bloomery Iron", Historical Metallurgy, vol. 36, issue 2, Leeds, Maney Publishing, pp. xx-xx, 2002.