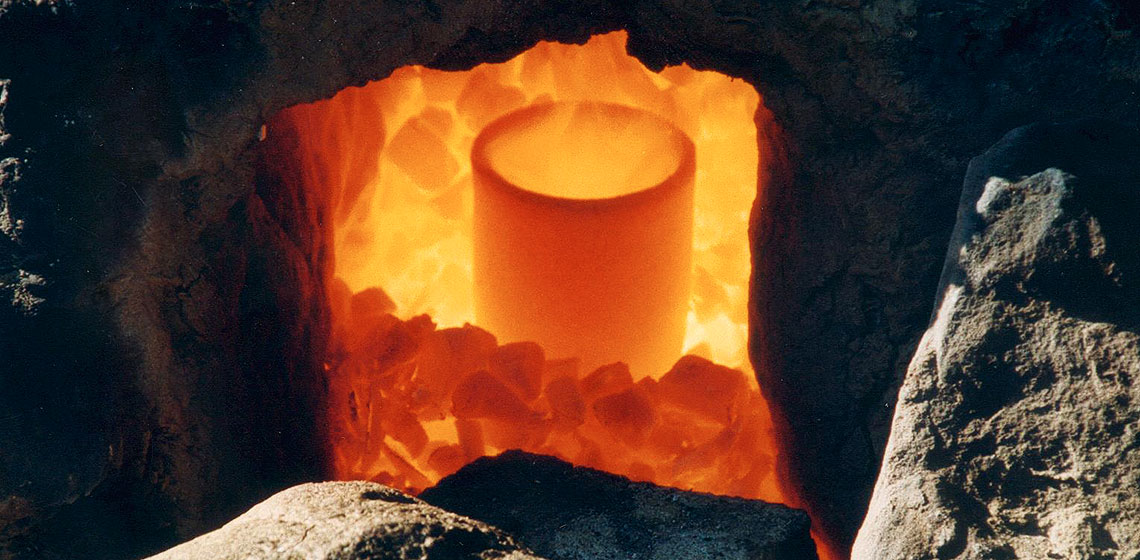
Considerations about a lost ancient fabrication technique of bronze attachements from a merowingian treasure box pointed out that practical experiments had to be done to reconstruct the cast and coldwork. A self made oven and mould sould help to create a realistic situation of a merowingian workshop.
Introduction
A wooden treasure box covered with a layer of bronze was excavated in 1998 (See Figure 1). It was found in a grave of a female at a merovingian graveyard in Bonn-Oberkassel near the river Rhine, Germany. The wooden treasure box was covered with a very thin layer of bronze with a decorative gold work. Different ornaments were punched into the bronze which was only 0.1-0.2 mm thick. Normally archaeological bronze objects this thin would not have survived. It would be expected to find nothing more than corrosion products of the metal. This bronze, however, is in an unusually good condition. In some areas the metal character has completely survived. The composition of the alloy is - copper 88%, tin 6% and zinc 6% and could have been developed in merovingian times, when they start to begin working with thin bronzes. This alloy allowed the ancient caster to get a bronze without gas bubbels, because of the zinc content. During casting, the zinc oxidizes and helps to reduce the copper. Maybe this bronze is more resistent against corrosion than other bronzes. On the other hand we know that it could be possible that the bronze was treated (patinated) to produce a different coloured appearance or to make the surface more resistent to corrosion. This may be especially likely when we keep in mind that in this case it was used to cover a treasure box.
Questions of the ancient production technique
Besides the restoration, which I will not treat here because of lack of time, questions were raised concerning the treasure box and its fittings.
Palaeobotanic analysis identified that the wood used for the box was so-called Great Maple (Acer-pseudoplantanus). Great Maple is only available nowadays in Spessart and the Alps region. It is a very light wood which is very workable.
The copper alloy sheets on the box were partly paper thin. The normal thicknes of the metal was between 0.1 and 0.2 mm. The sheets were broken into more than 200 fragments in the rough gravel ground. The fragments belonged to four plates which were ornamental for the front and the frontal areas of the sides.
Analysis of the alloy made it clear that we have a mixed alloy between bronze and brass without any lead component. Nowadays one would call such an alloy a 'redcast'. In fact this alloy is still used today in the USA. It has the advantage over traditional antique copper alloys that one can cast almost without gas bubbles. Nowadays one uses this alloy, which is unknown in Europe, when one does not want to add modern reduction aids like, for example phosphoric copper. The zinc component of the alloy has an effect on the reduction of the melt. It cannot be certain if in the 6th century AD zinc was used in bar-form or if it was added to the melt like in the Roman Era as zinc oxide (calamine).
The question I wanted to answer was: What kind of technical connection exist between the difficult production of the alloy (Cu, Sn, Zn) without adding lead and the production of thin sheets of metall?
In the specialist literature no clear references were found, which meant I had to test and find out by myself the production and the processing of such an alloy in practical experiments (Rehren 1999, 26ff).
The preparation of these experiments, which themselves would take place at the Workshop 1999 in Wilhelminaoord, were very extended. Colleagues of the Technischen Universität für Gießereikunde in Aachen, who are involved over a longer period with the reproduction of antique bronze objects, could not get me more exact data for this special alloy, like melting temperature, character of casting or processing of it. But, yet, it is clear that alloys which contain zinc make special technical demands.
Important points
- During the melting procedure, temperature should not exceed 1100°C, because at higher temperatures the incorporated zinc will evaporate to zinc oxides. The zinc percentage would go down below desired levels.
- The melting of the alloy should take place in a more reducing atmosphere, to avoid the oxidation of the zinc. Practically, this would mean that oxygen should be limited.
- Copper alloys with zinc are likely to stick to the surface of the mould. This can easily lead to cracks during the cooling down.
- Lead-free 'redcast' alloys have only a limited good cold deformation behaviour, as they belong to the harder copper alloys.
Preparation of the experiment The alloy
While bearing in mind all previous theoretical knowledge, I decided to use pure zinc metal for the preparation of the alloy, as the purchase of natural zinc oxides (Galmei) would have cost a lot of time.
The melting oven
On the basis of my own experiments on the production of antique smelting and solder ovens which I conducted during the Mahida-Project 1990-1994, the use of so-called 'dome-ovens' can be assumed in Greece already in the 1st century BC (Ute Sobottka-Braun & Frank Willer 1994, 1017 ff). During these experiments the production of separately cast loose parts of three-footed oillamp holders could be attained by using dome-ovens. So called dome-ovens are closely related to the technique of ovens which are used for pottery. Because of their closed construction, higher temperatures could be achieved than the Bronze Age pit melting ovens. The bronze age pit ovens looses a lot of energy through the opening. Besides, the use of a dome oven, the addition of oxygen is relatively controllable, because one can seal off the oven. This fact played an important role in my experiment, because it made it possible for me to be sure only a little zinc would oxidize without using a lid on top of the crucible (See Figure 2).
The oven itself was built on a skeletal construction. It was made out of hazel tree twigs that were put into the soil. These twigs were braided into a dome and strengthened with a mixture of loam and clay. This mixture can be found locally in Wilhelminaoord. Grass and straw was added to give higher stability to the loam/clay mixture (See Figure 3).
In spite of the small preparation time of only one day, about 140 kg of loam/clay mixture was worked into an oven and was dried during a prefire of 12 hours.
The crucible
For a crucible I used traditional cup-shaped crucible forms, with a capacity of about 4 kg. Because of the special firing technique in the dome-shaped oven Bthe air is not blown on the crucible from above, but from the side Bit is possible to use a taller type of crucible. The advantage of this type of crucible is that the surface of the smelt is smaller, compared to the pan- shaped crucible which was used in the Bronze Age. Besides the easier handling of the crucible the eagerness of oxidation of the smelt is reduced as well. With the use of the dome shaped oven Bwhere the crucible is blown from the side- the metal can be melted without the addition of charcoal on top of the crucible (See Figure 3 and 4).
The mould
To produce the metal plates that were used as half-fabricates for the original plates, I have chosen the use of an iron ingot mould that I made myself (See Figure 5 and 6). It had to be blacken with the soot of a candel ore oil to isolate the iron mould against the bronze.
The firing
To build the fire, normal charcoal was used. The air supply was not produced by a pair of bellows, because of lack of time and the fact that I had to do the experiments alone, but by a vacuum cleaner. This to general amusement of the other participants of the bronze workshop. Since the use of bellows in the early Middle Ages is not a question anymore, I have taken this liberty.
The tuyère through which the air stream was blown consisted of an iron pipe. Firstly, the crucible with a weight amount of copper was placed on a flat stone within the oven. After slowly blowing the air, the charcoal started to glow throughout. After reaching a certain basic temperature of about 800C°, the 30 x 20 cm large aperture of the furnace wall, was closed up with a stone (See Figure 2). In the top of the oven through an aperture of about 7cm, a draft originated (chimney effect). Through this aperture it was possible to observe and control the melting of the copper, that started after 15 minutes (See Figure 7). Closing this aperture would raise the temperature shortly within the oven. Specially the zinc would oxidise easily, both ingredients tin and zinc were alloyed with the copper after it became fluid. For that purpose, the stone in front of the aperture was removed and both ingredients were added by means of an iron spoon. After adding new charcoal and firing the oven again for 7-10 minutes, the alloy was fluid and could be poured into the prepared mould.
It was immediately clear that it was necessary to blacken the mould with the soot of a candle (See Figure 8). That would make the mould smoother and would prevent the poured bronze from sticking to the mould. After letting the mould cool down the mould could be opened. It showed that by blackening the moulds with soot good pouring results could be obtained (See Figure 9).
The coldwork
The original bronze sheets were forged after casting, so it was not immediately known what the real thickness of the cast was before forging. The first self made experimental cast plates Bof approximately 10 x 14 cm and 6 mm thick Bwere not very easily forged because of the alloy being relatively too hard and brittle. Attempts made to cast thinner sheets of approximately 3 mm that were more workable, but it was still impossible to reach the wonted thickness down to 0.2mm like in the original archaeological evidence, even though the metal was annealed and afterward quenched in water. During the last attempt two pieces of paper were folded four times (distance holder) and put between the iron forming plates to allow a 0.5 mm thick metal sheet to be cast without the paper getting burnt. The cooling process of the metal is faster then the paper could get burned. With this simple technique and alloy I was able to cast thin plates down to 0.5mm.
Contrary to all professional opinions (Yes!) it is possible to produce a very thin copper-tin-zinc alloy which subsequently can be mechanically deformed (by forging) without too large a mechanical demand on the metal structure. An optimal change of the structure of a cast copper alloy piece, with dendritic structure, towards a fine recrystalised structure takes place between 40 to 50 percent deformation of the metal, during which it should be annealed then quenched in cold water every now and then (See Figure 10 and 11).
The experiments confirm the assumption that the medieval craftsmen were able to produce sheets of copper alloy down to 0.1-0.2 mm, even when they were forced to use an alloy which had bad forging qualities. I was able to reduce the 0.5 mm cast metal to 0.1-0.2 mm by hammering, annealing and quenching in water by four times.
Conclusion
Now a days we are able to identify the technical characteristics of antique copper alloys by using modern technical tabels. The relatively simpel castings technique in old days could meke it necessary to use alloys not always exactely for these specific goals. This is the reason why we have to look carefully if we interpret analysis of ancient alloys. This makes clear that analyses have always to be compared with detailed examinations of the production technique of an object.
So the alloy from the bronze coverings from Bonn- Oberkassel seemed to be developed to attain primaly good casts without inner gas-bubbles (defects).
By choosing the right casting thickness of the bronze, one was able to work - in modern view Bforging an unfavourable alloy with unexpected success.
By example of the chest from Bonn-Oberkassel it is made clear how important the experimental testing of results of analyses and theories is. Finally, I would like to thank my Dutch colleagues again, that they offered us the possibility to perform these very exciting experiments.
Bibliography
GECHTER, M., U. MÜSSEMEIER, and F. WILLER, Der bronzezeitliche Friedhof von Bonn-Oberkassel In: Millionen Jahre Geschichte, Fundort Nordrhein Westfahlen. Ausstellungskatalog Köln, , Mainz, 2000.
REHTEN, T., "Small Size, Large Scale Roman Brass Production in Germania Inferior", Journal of Archaeological Science, vol. 26: Elsevier, pp. 1083-1087, 1999.
SOBOTTKA-BRAUN, U., and F. WILLER, "Experimente zur antiken Guß und Löttechnik", Das Wrack. Der antike Schiffsfund von Mahdia, vol. Band 1, 1 and 2, no. Kataloge des Rheinischen Landesmuseums Bonn, Köln, Rheinland-Verlag GmbH, pp. 1017-1021, 1994.