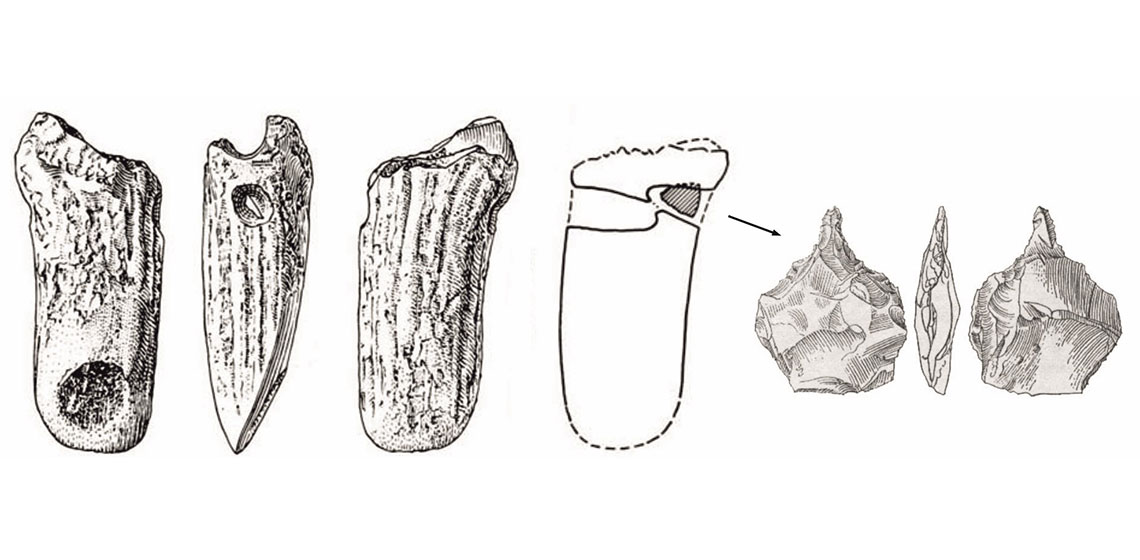
From the Neolithic period comes a whole range of various kinds of artefacts made of antler (for example axes, hammer-adzes), distinguished by the presence of a large hole (diameter over 2 cm) in their structure. With time, archaeologists started to wonder about possible ways of producing holes of this type, as besides their size, they are also quite regular (in the majority of cases their inner walls are smooth), with their inlet parts are the same diameter on both sides. This encouraged researchers to suggest that the holes had to be produced with the help of special drill bits (most probably made of bone or wood), designed for some kind of drilling devices (Bagniewski 1992, 28; Kempisty 1961, 138; Korobkowa 1999:, 99; Pratsch 2006; Riedel et al. 2004, 202-203). The above issue became a starting point for conducting an experiment, designed to test the suitability and effectiveness of wooden, osseous and flint drill bits in obtaining this type of large perforations.
The Neolithic is a time to which a vast range of many different artefacts made of deer antler, characterized by the presence of a large hole (over 2 cm), is dated (for example axes, adzes). Over time, archaeologists started contemplating the possible methods for making such a perforation, since apart from the size, their attention was caught also by its evenness (in most cases inner walls of holes have no irregularities) and the fact, that the opening of the hole is the same diameter on both sides. This led the researchers to propose that the holes must have been made with specialist core drill bits (Drilling devices that operate by abrading the work-piece only around the perimeter of the formed hole. Most probably made of cross-cut long bones or a suitable wood type) and related drilling machines (See Figure 1.; Bagniewski 1992, 28; Kempisty 1961, 138; Korobkowa 1999, 99; Pratsch 2006; Riedel et al. 2004, 202-203), much as in the case of perforating Neolithic stone axes (Clark 1957, 205; Feustel 1973, 251; Filip 1951, 142; Osipowicz 2005, 2012; Walter 2010; Weiner 1996,134-135). At present, apart from the perforations, we have very little evidence for the actual drilling of the antler. Examples include the broken T-shaped axe from Hüde I site in Germany, with a flint borer stuck inside the unfinished hole (See Figure 2; Deichmüller 1965, 9; 1974, 198), or a fragment of a bone drill bit retrieved from a T-shaped axe from a site in Brześć Kujawski, Poland (See Figure 3; Grygiel 1976, 279). When considering the possible application of core drill bits, the most significant find is the unfinished deer antler axe from a Neolithic site in Robenhausen, Switzerland (Rieth 1958, 106, see also 25:5-7; Altorfer & Huber 2010, see also 27:443), with a well-preserved partially drilled hole, whose shape indicates the use of drill bits of this kind (See Figure 4). When seeking information on the potential raw materials that might have been used for perforating, one should also consider the fragment of wood stuck inside a partially drilled stone axe from Bielersee, Switzerland (Weiner 1996, 134), which is thought to be the remains of a wooden core drill bit.
The above evidence became the starting point for conducting an experiment, in which an attempt at perforating un-softened deer antler was made with core drill bits manufactured from wood and bone. Additional works were conducted with flint borers. All works were aimed at verifying their usefulness and effectiveness in creating a similar type of perforation to those found in the archaeological record.
Methods
In the experiment a drilling device modelled on an implement constructed by the members of the Society for Experimental Primeval Archaeology of the Institute of Archaeology, Nicolaus Copernicus University in Torun, was employed (See Osipowicz 2005, 2012 for a discussion on the manufacture and use of this type of drill). As the emphasis for this project was on the raw material used for drilling and the very process of creating a hole, less focus has been put on the assembly and use of the drill itself. Experimental borers and drill bits were made of flint and materials whose morphology allowed a problem-free production of core drill bits, allowing formation of a characteristic by-product called a ‘core’, in the form of a cylinder or a cone, extracted from the raw material in the drilled hole.
a) Bone drill bits
Bone drill bits were made from fresh metatarsal bones of the domestic pig (Sus scrofa f. domesticus). The bones were cleaned, epiphyses were cut off and the marrow was removed from the bone. Prepared drill bits were 5 cm in length and up to 2.5 cm in diameter. They were mounted on suitably prepared straight wooden sticks. A linear scale was put on each drill bit at 1 cm intervals in order to monitor the drill bit wear during the drilling process.
b) Wooden drill bits
The drill bit was made of a fresh shoot of black elder (Sambucus nigra L.) 2.1 cm in diameter and 45 cm in length. Black elder shoots are characterized by a relatively high hardness and, most importantly, straight shape. Their additional advantage is the fact that they are filled with a thick spongy white core. Prior to fitting the drill bit in a drill, the bark was peeled off and then a piece of chamois leather was tightly wrapped around the shoot (this treatment aimed at ensuring proper friction, as initial attempts demonstrated that the leather straps used to turn the drill slid off the surface of the peeled shoot). The drilling edge was slightly thinned around the perimeter and the spongy core was removed to a depth of about 1 cm. Additionally, as in the former case, a linear scale was put on the drill bit at every 1 cm.
In the case of both above described drill bit types, a proper fill proved to be the vital element in the entire process, acting as an abrasive and the proper drilling material (grains of sand set in rotary motion cause abrasion of the work-piece). Dry microcrystalline sand with a grain size up to 0.5 mm used as the abrasive fill. This was formed into a small pile, covering the antler being drilled and part of the drill bit. This allowed the sand to refill itself during the drilling process.
c) Flint borers
For the purpose of this part of the experiment, typologically accurate borers were manufactured, up to 3 cm long and up to 2.5 cm wide. The devices were made of Baltic erratic flint. The manufactured forms were mounted on suitably prepared straight wooden sticks.
In all the cases, after a drill bit was mounted in a drill-stock, a bag filled with stones up to 0.5 kg was fitted to an upper hold-down pole. The drill bit was set in motion by two people sitting opposite one another, pulling the leather strap in turn, continuously and at a steady, moderate pace. Using the described method, holes were drilled in the beam of red deer (Cervus elaphus) antler. The antler was not softened by any means and scraping of the compact bone was not performed (both the antler and the drill bit were mounted in a way that prevented any offset). The hole was drilled on both (opposite) sides.
Course of the experiment
a) Bone drill bit (See Figure 5)
Pre-drilling
After 10 minutes of drilling, a very shallow 0.1 cm deep oval shape was observed to be forming on the surface of the antler. After 25 minutes the hole was already about 3 mm deep and an inner core started forming. After 45 minutes the depth of the hole was 0.5 cm and the total drill bit wear length was estimated at about 1 cm. Changes in the bone shape were observed over time. Walls at the very working edge started taking on a conical shape. After about 50 minutes the rate at which the drill bit sank in the antler increased considerably. This sudden shift was caused by cross-drilling the compact bone (substantia compacta) and drilling into the spongy bone (substantia spongiosa) of the antler. This resulted in the necessity to break off the inner core, which was causing the drill bit to get gradually stuck. After 65 minutes the hole was 0.8 cm deep, whereas the total drill bit wear length was about 1.8 cm. After roughly 80 minutes of drilling the hole was approximately 1.2 cm deep. After reaching a depth of about 2 cm, the drill bit started to get stuck in the hole, with its operation increasingly hindered. For that reason the decision was made to start drilling on the reverse side with a new drill bit.
Cross-drilling
The first traces of a hole forming were observed after only 10 minutes of drilling, as described above. After 35 minutes a 0.4 cm deep hole was formed and the spongy bone became visible. As in the previous case, the drilling rate rose considerably with cross-drilling of the compact bone. After 55 minutes the hole was already approximately 1 cm deep, whereas the total drill bit wear length was estimated at 1.4 cm. After 75 minutes of drilling, a hole roughly 2 cm deep was formed. After this, the drill bit started to get stuck in the hole. As such, the core that started to form was broken off. Following this, a small clearance was observed. After about 80 minutes of drilling the action was ceased, as a through hole was successfully formed.
b) Wooden drill bit (See Figure 6)
Pre-drilling
After 5 minutes of drilling, a very shallow 0.05 cm deep oval shape was observed forming on the surface of the antler. After 15 minutes, the hole was approximately 3 mm deep and an inner core had started to form. After that, the drilling became increasingly harder; the contact area between the drill bit and the antler remained flat, though a moderate abrasion on its outer walls was observed. After 25 minutes the hole was 0.8 cm deep, whereas the total drill bit wear length was estimated at about 0.5 cm. As time passed and the drill bit sank deeper in the antler, changes in its shape were observed. The drill bit faces became thinner, most likely due to friction both on the inside (sliding against the core being formed) and on the outside. A hole of increasing depth was forming inside the drill. The spongy inside was compressed by the core forming in the antler. After roughly 30 minutes of drilling, the rate at which the drilling bit sank in the antler increased significantly. After 35 minutes the hole was already circa 1 cm deep. After 40 minutes, a hole about 1.6 cm deep was formed, whereas after another five minutes of drilling it was already around 2.2 cm deep. This sudden shift was caused by cross-drilling the compact bone and drilling into the spongy bone of the antler, which was considerably easier to process due to its porous structure. The compact bone was approximately 0.35-0.4 cm thick on this side of the antler. At the same time, after about 40 minutes of drilling, the inner core formed by the drill bit was broken off, since it was observed that after reaching a depth of around 2 cm, the drill bit started to get stuck in the hole. This seems to be affected, to some extent, by the depth of the drilled hole, which prevented the abrasive fill under the edge of the drill bit from working properly. Despite removing the core, further drilling on this side of the antler proved ineffective. Filling the hole with sand made no difference and only caused clogging of the drill bit’s cutting hole. For that reason a decision was made to start drilling on the reverse side with the same drill bit.
Cross-drilling
The first traces of a hole forming were observed, as before, after only 5 minutes of drilling. After 10 minutes the drilling rate rose considerably higher due to the drill edge sinking deeper in the spongy bone of the antler, as in the case of the blind hole formed as a result of the pre-drilling. The compact bone on this side of the antler was circa 0.25-0.3 cm thick. After 25 minutes, a 1 cm deep hole was formed. The drill bit wear length at that time was estimated at 1 cm. After 35 minutes, the hole was already 1.5 cm deep. After another 10 minutes of drilling, the hole depth was 2.5 cm. Similarly, as in the former case, the formed core was broken and a small clearance was observed. Since drilling at such depth became increasingly difficult (due to the refilling of sand being hindered), a decision to knock out the remaining spongy bone (around 2-3 cm thick) was made. After this, a through hole was formed.
In the case of forming the through hole during cross-drilling, the drilling rate was higher. This was possibly due to the drill bit faces being somewhat hardened (as a result of continuous friction the temperature rose, allowing the water to evaporate from the wood), though thinner (in comparison to their initial thickness). On the other hand, the drill bit itself became more conical in shape, which facilitated deeper penetration of the antler. The drill bit did not start wearing at a higher rate until the ending of the cross-drilling process. This seems to result from late removal of the core, which caused high-rate thinning of drill bit faces, which in turn caused high-rate abrasion of the raw material in the contact area with the antler.
c) Flint borer (See Figure 7)
Pre-drilling
After 5 minutes of drilling a conical hole roughly 0.5 cm deep started forming in the antler. After another 5 minutes the hole was already about1 cm deep in the centre. Due to the shape of the borer, the diameter of the hole at the exit was approximately 1.5 cm at that time. After 15 minutes the unquestionably more fragile spongy bone was drilled through, with the hole in the centre around 2 cm deep. Unfortunately, the borer then broke and could not be reused. After another 5 minutes of drilling with a new borer, the hole was circa 3 cm deep. At that moment a decision was made to start drilling on the reverse side.
Cross-drilling
After approximately 5 minutes of drilling, a conical hole about 0.4 cm deep started forming in the antler. After a few more minutes, a small clearance was observed in the centre. The only thing left after this was to widen the hole by drilling, in order to make it equal in diameter to that on the other side. Drilling on this side of the beam was finished after about 15 minutes of drilling.
Summary
The experiment allowed observation of the following variables during drilling of individual holes.
Bone drill bits
Total drilling time | Total wear length of the drill bit | Total depth of the drilled hole |
15 min. | 0.6 cm | 0.2 cm |
30 min. | 0.8 cm | 0.4 cm |
45 min. | 1.1 cm | 0.55 cm |
60 min. | 1.7 cm | 0.75 cm |
75 min. | 2.2 cm | 1 cm |
90 min. | 3.5 cm | 2 cm |
Drilling started on the reverse side of the beam with a new drill bit (cross-drilling) | ||
15 min. | 0.5 cm | 0.1 cm |
30 min. | 0.7 cm | 0.3 cm |
45 min. | 1 cm | 0.5 cm |
60 min. | 1.6 cm | 0.8 cm |
75 min. | 2.1 cm | 1.1 cm |
80 min. | 2.2 cm | 1.9 cm |
Thickness of the drilled beam = ab. 4 cm
Diameter of perforation = 27 mm (entry part), 25 mm (inner part)
Table 1. Bone drill bits. Note: The thick line indicates the shift between cross-drilling the compact bone and the beginning of drilling the spongy bone.
Drilling a through hole with a bone drill bit proved far more time-consuming (See Table 1). Drilling a 1 cm deep hole required around 75 minutes of continuous drilling, while drilling through roughly 4 cm thick antler with a 2 cm diameter required approximately three hours of continuous drilling and at least two drill bits. Additional difficulties might have been caused by methods of manufacturing such drill bits. Firstly, they required mostly oval-shaped bones, and secondly, after removing the epiphyses, the obtained tools were relatively short, often up to 4-5 cm in length. This in turn caused the necessity to mount such drill bits on suitably prepared straight sticks. Which, in turn, resulted in reducing the actual length of the drill bit. The holes formed are characterized by a cylindrical shape, though a conical shape can be observed at the entrance to the holes. Inner walls are very regular, and the diameters of the entrances of the holes are similar. The wearing on its inner walls of the drilled holes is relatively easy to see; decomposing stacked linear traces of variable width, consisting of pits and polishing caused by friction of sand grains (See Figure 8A).
Wooden drill bits
Total drilling time | Total wear length of the drill bit | Total depth of the drilled hole |
15 min. | 0.3 cm | 0.3 cm |
30 min. | 1 cm | 1.2 cm |
45 min. | 1.9 cm | 2.2 cm |
Drilling started on the reverse side of the beam with the same drill bit (cross-drilling) | ||
15 min. | 0.5 cm | 0.7 cm |
30 min. | 1.1 cm | 1.4 cm |
45 min. | 2.6 cm | 2.5 cm |
Total drilling time = 90 min.
Total wear length of the drill = 6.1 cm
Thickness of the drilled beam = ab. 5 cm
Diameter of perforation = 20 mm (entry part), 19 mm (inner part)
Table 2. Wooden drill bits. Note: The thick line indicates the shift between cross-drilling the compact bone and the beginning of drilling the spongy bone.
The above averaged data shows (See Table 2), that drilling a 1 cm deep hole with a wooden drill bit, could take no longer than 25-30 minutes and cause bit wear lengths of approximately. 0.8-1 cm. Drilling a hole 2 cm in diameter through an antler roughly 5 cm thick required up to 1.5 hour. Interestingly, the drill bit used in the experiment lost about 6 cm of its initial length in total. Although part of the bone was knocked out of the drilled hole, the ratio of the worn wooden material and the worn antler was still approx. 1:1. This seems to be an interesting observation, which shows a relatively high performance for this kind of drill bits.
Similar to a large number of prehistoric tools, the hole drilled in the course of the experiment is characterised by a cylindrical shape. Its inner walls are highly regular (apart from a small thickening formed as a result of the extraction of the spongy bone), whereas the entrances have the same diameter on both sides. The drilled hole has on its inner walls, a different size of pitting and polishing, which creates distinct bundles of striae (of different bandwidth) caused by the abrasive impact of grains of sand set in motion and the drill itself (See Figure 8B).
Flintborers
Total drilling time | Depth of the drilled hole |
5 min. | 0.5 cm |
10 min. | 0.9 cm |
15 min. | 2.2 cm |
20 min. | 3 cm |
Drilling started on the reverse side of the beam with the same drill bit (cross-drilling) | |
5 min. | 0.6 cm |
10 min. | 1 cm |
Total drilling time = 30 min.
Thickness of the drilled beam = ab. 4 cm
Diameter of perforation = 22,5 mm (entry part), 20,5 mm (inner part)
Table 3. Flint borers. Note: The thick line indicates the shift between cross-drilling the compact bone and the beginning of drilling the spongy bone.
Borers proved far more effective and a faster means of drilling antler (See Table 3). The total time for making a through hole with a diameter of 2 cm was circa 30 minutes. Owing to the use of borers of adequate size and shape, such as the diameter of a planned hole, the formed perforation was cylindrical. A moderate widening was observed only at the entrances to the holes, giving a slightly more conical shape. Due to the lack of an abrasive sand fill, traces inside the hole are different to those obtained by drilling with the use of a sand fill. They are highly regular and evenly distributed, forming relatively wide linear traces situated one over another, resulting from the friction caused by the edges of the tool while retouching (Figure 8C). The only problem observed in this entire process proved to be the occasional stuck or broken drill bit, particularly when the working was done with unretouched edges.
Though in all cases an effort was made to locate the drilled holes in a straight line by creating a regular hole, this attempt failed and the obtained holes were slightly offset from each other (by roughly 1-2mm). It should be noted, however, that this is also often observed in the case of artefactual material, among others, Hüde I (Deichmüller 1974).
Conclusions
The conducted experiments allowed several conclusions to be drawn, pertaining to the use of various raw materials as drill bits for making large perforations in deer antler. The findings prove, that each of the materials employed enabled the formation of large holes of almost ideally cylindrical shape. Observable differences are related mostly to bit wear rates between the drill bit types and the time required to make a perforation. The presented results constitute a single attempt that should be complemented in the future with many optional variables, for example, drilling in softened raw material, use of other types of bone, such as bird bones, or drilling with organic drill bits with the compact bone partially removed in advance. Notwithstanding the limitations of this experiment, it seems plausible to state that due to the high availability of the raw material and undoubtedly shortest drilling time, the best drilling method was the one that employed stone drill bits. The use of organic core drill bits seems more time-consuming, at least in the light of conducted experiments. Moreover, it has been proven, that the cylindrical shape of the hole, with identical diameters at the entrances of the holes, can be obtained without any problem with the use of proper flint tools, and not only, as it was suggested, with use of core drill bits.
Unfortunately, the holes obtained in the course of the experiment, despite comparisons with numerous artefacts, do not always allow a clear identification to be made of techniques used in prehistoric times. This is due to the fact that after drilling, the hole might have been additionally widened with the use of a flint tool (for example by whittling the surface). As a result, possible traces useful in reconstructing the drilling process might have been destroyed. The traces on the inner part of the hole, below the entrance, are also illegible, due to the properties of the spongy bone, whose structure is far more prone to disintegrating. Additional variables are caused by post-depositional factors, as well as the use of the tool itself. In the latter case we ought to take into consideration the fact that a wooden shaft was fitted in the hole, causing additional friction and, hence, destroying possible traces related to technological procedures.
The methods for drilling holes applied in the experiments, as well as the raw material itself, have proven to be relatively efficient. Moreover, against all appearances, they do not require a considerable amount of time, energy or raw material. Possibly, this sort of operation called for even less effort when performed by a Stone-Age expert - obviously, this is providing the described methods for drilling holes in antler, coincide at least to a small extent, with the techniques used by men in prehistoric times.
Acknowledgements:
I would like to thank Dr Grzegorz Osipowicz who inspired me to take up this topic, who has always supported me and offered me advice. Sincere thanks go to two anonymous reviewers and language editor for reading and providing useful comments and corrections on the paper.
Bibliography
ALTORFER K., HUBER R. 2010. Die prähistorischen Feuchtbodensiedlungen am Südrand des Pfäffikersees : eine archäologische Bestandsaufnahme der Stationen Wetzikon-Robenhausen und Wetzikon-Himmerich. Monographien der Kantonsarchäologie Zürich, 41.Baudirektion Kanton Zürich, Zürich.
CLARK, J.G.D. 1957. Europa przedhistoryczna. Podstawowy gospodarcze. Państwowe Wydawn. Naukowe, Warszawa.
BAGNIEWSKI, Z. 1992. W sprawie obróbki surowca rogowego w mezolicie. Studia Archeologiczne 22: 13-33.
DEICHMULLER, J. 1965. Die neolithische Moorsiedlung Hude I am Dummer, Kreis Grafschaft Diepholz. Neue Ausgrabungen und Forschungen in Niedersachsen 2: 1–18
DEICHMULLER, J. 1974. Eine Geweihaxt mit Flintbohrer aus der Siedlung HüdeI am Dümmer, Kr. Grafschaft Diepholz. Archäologisches Korrespondanzblatt 4: 197–199
FEUSTEL, R. 1973. Technik der Steinzeit: Archäolithikum-Mesolithikum. H. Böhlan,Weimar.
FILIP, J. 1951. Pradzieje Czechosłowacji. Instytut Zachodni, Poznań.
GRYGIEL, R. 1976. Osady kultury ceramiki wstęgowej rytej w Brześciu Kujawskim koło Włocławka. Prace i Materiały Muzeum Archeologicznego i Etnograficznego w Łodzi, seria archeologiczna 23: 5-111.
KEMPISTY, A. 1961. Ze studiów nad sposobami obróbki surowca kostnego i rogowego w kulturze pucharów lejkowatych. Wiadomości Archeologiczne28: 133-141.
OSIPOWICZ, G. 2005. Drilling through stone axes. Experimentelle Archäologie in Europa 4: 115-122.
OSIPOWICZ, G. 2012. Wiercenie otworów w toporach kamiennych. In: Gancarski J. (ed.): Skanseny archeologiczne i archeologia eksperymentalna. Muzeum Podkarpackie, Krosno.
PRATSCH, S. 2006. Mesolithische Geweihgeräte im Jungmoränengebiet zwischen Elbe und Neman. Ein Beitrag zur Ökologie und Ökonomie mesolithischer Wildbeuter : Studien zur Archäologie Europas 2. Habelt, Bonn.
RIEDEL, K., POHLMEYER, K., RAUTENFELD, D. B. von 2004. An examination of Stone Age/Bronze Age adzes and axes of red deer (Cervus elaphus L.) antler from the Leine Valley, near Hannover. European Journal of Wildlife Research 50 (4): 197-206.
RIETH, A. 1958. Zur Technik des Steinbohrens im Neolithikum. Zeitschrift für Schweizerische Archäologie und Kunstgeschichte (Zürich)18: 101-109.
WALTER, P. 2010. Bohren im Museum. Forschungsgeschichte, Didaktik, Mathetik. Experimentelle Archäologie in Europa, Bilanz 2010, Heft 9:71-84
WEINER, J. 1996 Zur Technologie bandkeramischer Dechselklingen aus Felsgestein und Knochen - Ein Beitrag zur Forschungsgeschichte. Archaeologia Austriaca 80 : 115-156.