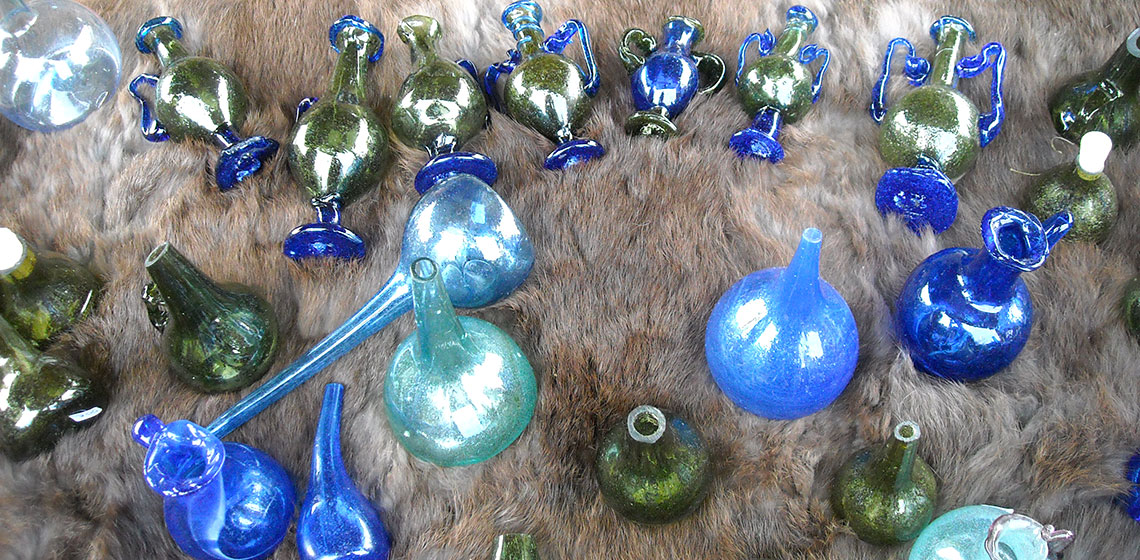
Experimental archaeology is taking on an ever more important role in pre- and early historical research. The archaeological open-air museum at the exhibition at the Museum of Pre- and Early History in Asparn/Zaya was a centre and teaching site for experimental archaeology from its beginnings in 1970.
The experiments carried out in Asparn are mostly in the field of light industry. These include stone-, wood- and metal-processing, skin, textile, leather and pottery production, and bone working. Dye plants, the cultivation of ancient fruits of the field and also the preparation of various dishes are also offered. The open-air museum at Elsarn im Strassertal also increasingly hosts days of action led by Gerhard Putzgruber.
Part of the reorganisation of the archaeological open-air area at Asparn are plans for a remaking of the Iron Age workshop area. The construction of an Iron Age smithy and a glass production furnace are also being planned. As is widely known ‘glass can be made out of quartz sand, potash and lime’. But is it as easy as that? It is therefore legitimate to discuss here the experimental efforts involved in its production. At the Eslarn open-air site Gerhard Putzgruber and his team, “ArchäotechnikElsarn” www.archaeotechnik.at, have succeeded after many attempts in successfully carrying out the experimental construction of a glass furnace. This experiment is the subject of this paper.
First experiments
A preliminary experiment was carried out on 21 December 2007 by a team led by Putzgruber to explore possible ways of manufacturing glass. A mixture of quartz sand, potash and lime was melted directly in the fire of a simple charcoal forge and with the help of an electric fan. The mixture was made by instinct. 5% lime, 20% potash and 75% quartz sand. Our aim was to find out if this primitive mixture would melt directly in the fire without using a crucible.The attempt showed that this mixture melts in the heat and produces a semifluid glassy mass, which, it was noticed, was significantly contaminated by charcoal and ash (See Figure 1). For this reason, a charcoal furnace was erected again at Whitsun 2008 and a second attempt carried out, in which the glass batch was introduced in a fireclay crucible and the potash-quartz-lime mixture melted with the help of a pair of bellows. The result was a green mass, similar to glass, which improved continuously after the experiment had been going on for several hours. Another part of the experiment was to find out how long it would take to melt the glass by using bellows instead of the fan. During the experiment it turned out that working with bellows was not economic- because too many workers would be needed. Possible solutions were sought by using an excavated third-century Roman glass furnace (Wedepohl 2003, 62, Fig. 21) from Aix-en-Provence as a model (See Figure 2). It appears to have been a working furnace (Wedepohl 2003, 61). First, a sketch was made of the possible appearance of the future furnace. The measurements of the firing channel, combustion chamber and chimney were calculated. Construction began in June 2008. The team thought that a drawn-out firing channel would make it possible to achieve and maintain high temperatures over a longer time period. Thus it would be possible not only to process glass in the furnace, but also to produce it (See Figure 3). The furnace was built of mud bricks and clay and stabilised by hay. To protect the inner surface of the furnace from the great heat expected, a layer of naturally-occurring fire resistant clay several centimetres thick was applied.
Based on previous experience with building smelting furnaces it was thought impossible that a furnace fuelled by wood would generate enough heat to melt glass unaided, so a very tall chimney with a solid foundation was necessary in order to create enough suction. First a keyhole-shaped foundation trench with a depth of 80 cm was excavated, filled out with rough stone and finished off with clay and earth. Next, the combustion chamber and the firing channel were built of bricks and clay. On top of this fresh air ducts were built in the walls of the firing channel with the help of reed, in order to be able to ignite gases in the chamber and thus increase the temperature.
A warming cupboard was added above the firing channel, which was intended to be heated by the surplus heat from the furnace. This is necessary in order to relax the glass products. Three fireclay supports were inserted into the combustion chamber, and the crucible was to rest on them and thus be surrounded by flames on all sides. Finally, a chimney was built above the furnace, resulting in a total height for the entire structure of 4 m (See Figure 4).
As no commercial crucibles suitable for the furnace were available, we made our own of fireproof clay, which was first baked, then crushed and mixed with 50% potters’ clay.
After the furnace was left to dry for a about three weeks, the first attempts began in August 2008 with a mixture consisting of lime, potash and quartz sand (See Table 1).
At first, we used beech for firing purposes, but this led to the firing channel becoming rapidly clogged with ash. Instead, softwoods such as spruces or pine were used in metre-long logs. Pine turns out to be best for generating heat. The experiment lasted for a little more than five hours and the temperature was monitored with an electronic measuring device. At the end the crucible contained glass, which had not quite finished melting. It proved possible to generate temperatures of c. 1200°C without too much difficulty. By carefully opening the air ducts it was possible to raise the temperature by a further 50°C for short periods of time.
Another attempt began on 3 October 2008. This time we used a mixture of quartz sand, soda and lime, because mineral soda was common in the Roman glass industry (See Table 1)(Wedepohl 2003, 1-13).
At 11:00 a crucible containing the mixture was placed in the pre-warmed furnace. By 15:30 the mass had reached 900°C and become clayey, after which we maintained the heat at temperatures of 1000-1100°C. At 18:00 at a temperature of 1200°C the mass frothed up, then at 18:30 we stopped firing and let the furnace cool down.
The next day we began firing early and placed the glass mass, which had been ground down in the mortar, in the combustion chamber. The temperature rose slowly to 1000°C at midday.
Ultimately we reached temperatures of around 1200°C. However, the mass had not really become liquid by 15:00, when the experiment was concluded (See Figure 5). Afterwards, having been advised by a friendly chemist, we used the more appropriate washing soda (Na2CO3.10H2O) instead of baking soda (NaHCO3)as it is closer to Trona (Na3(HCO3)(CO3)•2H2O), the mineral used by Romans.
The next attempt took place the following week on 10 - 11 October 2008. The mixture used is described in Table 1.
aug-08 | 3-10-2008 | 10-10-2008 | 26-10-2008 | 21-12-2008 | |
lime | 14% | 7% | 11% | 8,57% | 11% |
(1 part) | (93g) | (powdered lime, 132 g) | (220g) | ||
potash | 29% | ||||
(2 parts) | |||||
quartz sand | 57% (4 parts, total weight of 1 kg) |
75% (1000g) |
55% (669.84g) |
47,64% | 64% (1280g) |
soda | 18% | 23% | 32,40% | 22% | |
(baking soda, 240g) | (crystal soda, 224g)* | (not calcinated) | (calcinated, 440g) | ||
lead | 2,50% | ||||
(34g) | |||||
cobalt oxide | 0,10% (1g) |
0,18% (2.16g) |
0,09% | ||
feldspar | 4,70% | ||||
borax | 6,60% | ||||
roasted iron ore | 1% (20g) |
||||
fluorite | 2% | ||||
(40g) |
During this experiment we encountered the following problems:
- First the crucible would fall off its supports as they slipped rearwards, possibly due to the intense heat. This was solved by rebuilding of the supports. Another problem was that the furnace was melting internally. The combination of great heat and ash led to the glassification of the daub and the firing channel changed its course due to the melted furnace wall. It had to be chiselled free.
- Second, the glass mass had again not melted homogenously due to the proportionof soda used being too small because of an arithmetical error (23% instead of 33%). We now know that even if we had calculated the soda content correctly it would still have been too small, as at this point we were not calcinating the soda.
The new experiment
The new experiment was to be presented to the public on October 26 2008. Three weeks earlier a smaller ‘fritting oven’ was built alongside the big smelting furnace. We found hints of a two- level melting process in Karl Hans Wedepohls book. (Wedepohl 2003, 45). At this stage of our experiments we thougt this would be necessary. Before the glass was further processed or melted, it had first to be fritted for several hours at 900°C. This leads to a reaction between the quartz and the soda, which causes the glass mass to froth up. This temperature is reached in the smaller oven in order to help take pressure off the big glass furnace. This was first used for smelting. The first measurements showed, however, that the small oven could also reach very high temperatures of up to 1200°C. Both ovens could therefore be used for smelting (See Figure 6). This little oven was remarkably similar to the picture of a Roman glass oven on an oil lamp1 .
Both ovens were fired up in the course of an event. Once the necessary high temperatures had been reached it turned out that the ‘fritting oven”’ needed only about half of the wood that the big furnace consumed. The reason was that the furnace developed very strong suction due to the very tall chimney and therefore left a great deal of energy unused. In this attempt we utilised an altered mixture (See Table 1).
In order to prepare the glass production, both ovens were fired up from 9:00 the day before and a glass mixture set in both, with the aim of achieving a good glass quality twenty-four hours later. The first successes were visible at 16:30 when the mixture began to melt. During the night of the 26- 27 October 2008 firing was maintained continuously by working in shifts. Slip-ups took place during the night, however. At 1:00 the crucible in the fritting oven fell off its supports.
The supports had slipped outwards due to the great heat. Luckily, the crucible had not broken due to the embers which had accumulated in the chamber and, after the firing channel had been completely emptied, the glass was salvaged with tongs and put in position again. The ash sticking to the glass was not a problem, as this burns off at such high temperatures. However, the crucible in the big furnace was also a cause for concern. A test look in the chamber, only half-an hour after the first crucible incident, showed that the crucible there suddenly no longer contained glass. The base had sprung a leak, the glass had run out and was now stuck at the bottom of the furnace, as there was no ash which might have formed an undercoat. This meant that the glass could no longer be taken from the furnace. Luckily, the team, having thought ahead, had prepared a new crucible, which was then put in position. The rest of the night was uneventful, apart from the fact that both ovens had to be cleared of surplus embers several times.
In the morning, with everyone looking forward to the day, the big furnace put the dampeners on the team again. As previously mentioned, the high temperatures were threatening the stability of the combustion chamber and at 8:00 part of the inner wall of the chimney fell into the crucible containing the glass, which then broke. The glass mixture was also lost. For this reason, the furnace was shut down for the duration of the event. Everyone was very disappointed as almost twenty-four hours of work had been wasted. Nevertheless, we succeeded in producing simple vessels without a handle or a complicated rim (See Figure 7).
The most important insight from this experiment was that the small oven functioned considerably better than the large furnace. The high temperatures, which the large furnace can reach with the help of the chimney are not useable, as the furnace would then melt and destroy itself. The furnace wall, which consists of clay and mud bricks, melts away at 1250°C or more like ice in the sun. Fritting also turned out to be unnecessary. We were able to produce a homogenous glass mass without going through the fritting stage. The glass batch melted, but did not become sufficiently homogenous. Another problem was the distortion of the crucible due to the high temperatures.
Following this, small-scale experiments with 100 g glass batches were tried out in an electric annealing oven (See Figure 8). After several attempts, during which the crucible repeatedly broke as it heated up, it became apparent that the soda used was responsible for the lack of success2 . The liquid soda was absorbed by the crucibles and when it continued to boil they were destroyed.
Experiments with new mixtures
Exactly one year after the first experiment, on 21 December 2008, a new smelting process was carried out in the small oven. Small experiments in the annealing oven, during which fluorite was also employed as liquefier (up to this point the glass had been too tough to work with), led to a new formula (See Table 1). This time the mixture melted well. Despite the necessity to replace the crucible as the first one broke due to too high temperature we gained glass, which could be worked and matched our hopes. The progress of the smelting is recorded in Table 2.
9:00 AM | Oven fired - measurements begins, unburnt crucible installed |
11:00 | 800°C reached, crucible is undamaged |
11:10 | 900°C |
11:30 | The crucible is glowing, glass mixture is introduced |
11:35 | 1000°C |
12:30 | 1150°C |
12:40 | 1230°C |
13:15 | 1200°C, test sample, the mixture has melted well and is a very thin liquid |
14:15 | 1150°C, test sample, well melted, the rest of the mixture abandoned, now a glass mixture of 2kg |
18:30 | 1291°C, the crucible has broken due to the great heat (we now know that fireclay breaks up when exposed to temperatures of c. 1290°C) and the glass may have fallen into the oven. The ambers clear out, the glass cleaned and returned to the oven in a new crucible. |
19:35 | 800°C |
2:13 | 1110°C |
2:23 | 980°C, firing channel cleared our |
2:27 | 1047°C |
2:44 | 1109°C, smaller wood used |
3:12 | 1061°C, the temperature remains at c. 1060°C for a long time |
3:57 | 1013°C |
4:02 | 1061°C |
4:40 | Firing channel cleared out, firing continues with smaller logs and collected wood |
4:48 | 1035° |
5:00 | 1105° |
5:40 | Embers cleared out |
Our conclusion was that in the next attempt less liquefying agent, soda, iron ore and fluorite should be used, perhaps 1% less soda and no iron ore. In this attempt we had not had a lehr, so that the glass could not be further processed.
At that stage of the experiment, we only used ingredients we found in the analysis from Karl Hans Wedepohl (2003). First we wanted to prove that it was possible to produce glass with our furnace. Also, at that time we did not have the opportunity to make a chemical analysis of our glass. Later on (after writing the report) we got an analysis from the University of Vienna. We were very close- this gave us the possibility to rework our mixture.
Rebuilding the glass oven
In spring 2009 we decided to demolish the large furnace due to space and because of the large amounts of wood it needed, and to rebuild it. It was now rebuilt along the same lines as the small oven, but now included thicker outer walls for stability, and an integrated cooling oven to relax the glass. In this model the warming cupboard had to be separately heated, so that the beads which might later be produced could relax there (See Figure 9). The new furnace was built on the foundations of the older version, that means again we followed the groundplan of the furnace from Aix-en-Provence (Wedepohl 2003, 62, Fig. 21). The above ground part was modelled on a drawing from an oil lamp from Asseria (Archaeological Museum Split). The furnace was carefully fired after two weeks drying time. It was then operated for two days at Whitsun 2009.
A glass batch similar to that used in December was employed (with the addition of copper and lead). The aim was to produce red (ruby-coloured) glass. The glass mass was easily workable, but the colour turned out to be problematic. The glass was partly red, but mostly green or copper-coloured. Nevertheless, we were able to manufacture very usable glass vessels, some of them with handles (See Figure 10). Early glass analyses carried out by Vienna University showed that fluorite remained in our glass. We had hoped that the fluorite would dissolve, as it did not occur in any of Wedepohl’s analyses of ancient glass.
We were thus faced with the problem of developing a new glass batch without fluorite. Several small-scale experiments in the annealing oven enabled us to roughly estimate the soda content in the finished glass. It turned out that there was far too little soda in the glass batch used in our previous experiments up to that point. After we had solved this problem we were able to produce glass that was very close to the Roman product.
The next attempt took place from 3 – 5 July 2008. The wood consumption and the usefulness of the new glass batch was to be tested. The new glass batch was shown to be very suitable. The early warming phase began on Friday at 8:45. The glass batch was placed in the crucible once 800° C had been reached. A glass batch has a larger volume before it is melted and it is not possible to empty the entire mass into the crucible in one go. It was 14:00 before the entire batch had been added to the crucible. The temperature was then gradually brought to 1150°C and held at that level. The glass was completely melted by 21:00 and it was already possible to create vessels (although at this point there were still lots of air bubbles in the glass). Up to now we had used almost exactly 1m³ wood.
The newly built oven functioned successfully. A large part of the inner wall of the furnace melted during the first attempt, but this did not seriously hamper the work. This problem was no longer relevant at the second try. Presumably the material had melted in places where the width of the oven was too constrained (hot spot) or the frequent melting had made the material more resistant to heat. Interestingly, the oven wall below the crucible melted considerably more than above it. This is not necessarily a disadvantage as it also leads to the heat below the crucible being maintained for a longer period. We had now successfully produced a workable glass in our own self-made oven.
Working the glass
During the first experiments, once we were able produce workable glass, there had been attempts to blow the self-made glass with rudimentary blowpipes. Humble small bottles could be blown with relative ease, but attempts at more complicated models failed repeatedly3 . After a while we were able to produce more difficult pieces with an added foot or a complicated rim (See Figure 11).
The glass oven was repeatedly repaired and improved. Finally, the warming cupboard was removed and replaced by a portable model. As the present glass oven is now showing considerable signs of wear and tear, it is to be replaced by a new model. This is to be built in such a way that work with both a reduced and an oxidised atmosphere will be possible, thus producing a wider spectrum of colours. There will also be up-to-date analyses of the newly-produced glass, to assess our successes and improve the mix.
Acknowledgements
We would particularly like to thank Mag. Erich Broidl, director of the open-air museum “ElsarnGermanic Farm”, for allowing us to conduct the experiment at that museum, and Christain Lepolt, who is in charge of the restaurant there and who kept us well fed. We would also like to thank Mag. Wolfgang Lobisser for encouraging us to go ahead with the project. The numerous colleagues from friendly re-enactment groups who repeatedly gave us great support should also not be forgotten (particularly our former colleagues Anita Kail und Rene Arbesser, and our new helpers, who have assisted us since Spring 2010: Eveline Brandtetter, Florian Götzinger, Tina Papst, Markus Papst and Simone Piccolo). Last but not least, we would like to thank the company Stölzle Glas from Alt Nagelberg, who acted as advisors.
About Authors:
Dr. Ernst Lauermann
Landesarchäologe für Ur- Frühgeschichte und Mittelalterarchäologie
Schlossgasse 1
A-2151 Asparn/Zaya
Ernst.lauermann@noel.gv.at
Gerhard Putzgruber
Talstraße 110
A-3491 Straß im Straßertale
Gerhard.putzgruber@evn.at
Dorina Götzinger
Lorenzo-Mattielliweg 21
A-3400 Klosterneuburg
Dorina.T@hotmail.com
Photos by:
Fig 1, 3-11: Martin Heimhilcher
Fig 2: Manuela Kotas
- 1WEDEPOHL 2003, 62, Fig. 21 (glass furnace portrayed on an oil lamp from the first century AD, from Assena, Split Archaeological Museum, Dalmatia)
- 2Soda contains a great deal of water and becomes liquid at 100°C. If the temperature continues to rise it begins to boil and the liquid vaporises, c. 60% of the original amount remaining in the form of a white powder.
- 3The experiment was very kindly supported by the company StölzleGlas, who helped us to learn basic working procedures at their industrial furnace. On the other hand, the firm’s glass blowers found working with our oven a very particular challenge.
Bibliography
WEDEPOHL, Karl Hans. 2003. Glas in Antike und Mittelalter: Geschichte eines Werkstoffs. Stuttgart.