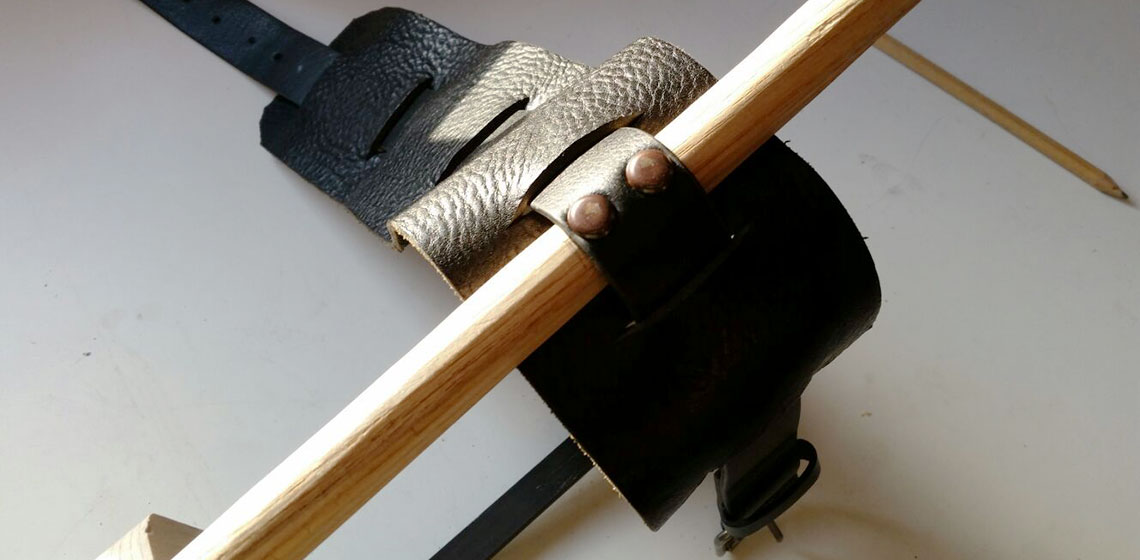
Scientific attempts to understand early prosthesis manufacturing techniques are rare. The academic research of artificial limbs has been limited to the historical analysis of documentary sources. This area still remains a fairly under-researched topic even under the more recent developments of disability studies (Childress, 1985). There may be many reasons for this; the organic materials used in manufacturing limbs such as wood and leather, mean few prostheses survive archaeologically in situ, and disability was until more recent times hidden or not spoken of (Sweet, 2016). Our understanding of the early artificial limb manufacturing industry, has been based primarily on drawings, patent applications and rudimentary manufacturing methodologies. However, that all societies (past and present) follow a single technological trajectory just at different rates of progress would be an inaccurate assumption (Pfaffenberger, 1992). Therefore, the employment of experimental methods can aid the exploration of technological questions surrounding consumer networks, use and discard patterns, craft specialisation and workforce requirements.
A recent new wave of prosthetic interest has seen researchers such as Jaqueline Finch (2011) beginning to dissect the origins of prosthesis, using a new scientific approach. Finch’s methodology utilises a combination of reconstruction and lab based biomedical analysis in order to assess whether an artificial toe discovered in Thebes, dating to around 950BC, was intended for functional use or just aesthetics. Her work provides a framework for future research across academic disciplines, in order to establish the efficiency of different types of prosthesis, levels of anatomical understanding and social attitudes to disability during wide-reaching historical eras and cultures. This research draws on the methodological processes employed by Finch in her 2011 analysis.
Whilst medieval England saw an arrival of internationally designed forms of prosthesis, these were often upper limb variations and usually designed for soldiers to wear with their armour. The fact was that people rarely survived lower limb amputations at this time due to the high levels of infection and shock-based mortality so peg-legs rarely needed innovating. During the post medieval era, wars and battles made the necessity to advance surgery of paramount importance. In combination with the larger battles, which spurred on the need for medical appliance innovation, more people began surviving their horrific injuries due to increased medical knowledge and care. Therefore, by the turn of the 19th century, when we observe industrialisation in cities and towns, we also see larger numbers of people with new injuries from industrial injuries, which required prosthetic appliances. The need for advancement was vital.
This research plans to examine surviving post-medieval prosthetic devices, which can offer greater insight into the origins of the state-of-the-art engineered prosthetics used today – for it is here we see the developments of a specialised industry with the opening of the first stores primarily dedicated to the manufacturing of prosthesis. The lack of written information about production methods and manufacturing techniques of post-medieval devices however, highlights a gap for the utilisation of similar methods to those used by Finch (2011). Combining this new scientific approach with a historical research, will illuminate not only attitudes to disability and prosthesis, aesthetic perceptions and value but also cognitive themes for producer, wearer and wider society.
Research Questions
Forming part of a wider PhD research which considers two military lower limb prosthetics available during nineteenth century Britain – the ‘box leg’ (peg leg) and the ‘Anglesey leg’ (utilised by lower and upper class soldiers respectively). The experimental sequence used here, is designed to test the production methods of a box leg and test their efficiency compared to modern prosthesis utilising a similar form. Understanding their production processes will highlight the skill level of the producers and by assessing their efficiency, it will demonstrate potential detrimental effects that may have been caused to the wearer. The effects should be visible skeletally on contemporary archaeological remains. A positive outcome to this research will allow examination of historical amputees in order to propose not only if the individual survived amputation and wore a prosthetic, but also whether the prosthetic they used left skeletal markers similar to those left by the use of a peg leg. Furthermore, this research would illuminate the manner in which the limb was lost and the potential social class of the amputee; peg legs were usually worn by lower class soldiers who lost their leg in battle.
This short paper will explain the experimental production process and the materials involved. Analysis of efficiency is yet to be assessed and so the questions, which will be answered at this stage, are;
- How skilled were peg leg manufacturers?
- What issues arose during this preliminary experimental phase?
- Can the initial findings tell us anything about amputees in the military during the nineteenth century?
The rest of the questions will be answered at a later stage when the digital analysis involving Vicon Nexus software will be completed, this computer software allows the processing of data from gait analysis, biomechanical research and ergonomics.
List of Materials
The main materials used were wood, metal and leather. Documentary analysis indicates the wood used for construction of peg legs was a fine-grained hard wood. Precise information about specific woods used however has been hard to find, with references to ‘hardwoods’ being the most common (Gray, 1855). Visually analysing such objects in museums made it apparent that the most common wood used was oak, lime or ash. These woods were also widely available and affordable during this time. Selecting woods here, involved the collation of small samples of different wood species to see the ease of which they were carved by hand, their aesthetics and their potential durability. The pieces of lime and ash were carved into smaller fragments using a hand chisel and their grains compared to archaeological artefacts. The wood selected after the test carving was ash because it matched the desired attributes noted for original peg legs, which include durability, strength and accessibility.
The specific material used for the nails is not mentioned in production descriptions, however as artificial limb makers were also often cobblers or clock makers it seems logical to assume that the types of nails used were what they already had for these primary purposes. Original artefacts also display nails, which have the same attributes as copper-alloy or wrought iron cut or wire nails. The type of nail tacks used in this reconstruction to secure the three wooden components together was a copper-alloy nail, this was because copper-alloy is commonly used where corrosion may be an issue, such as furniture where contact with human skin salts will cause corrosion on steel nails, it will not rust in water (Ashby and Johnson, 2002). It is often used where low friction is required such as locks, gears, bearings and where it is important sparks are not struck (Ashby and Johnson, 2002).
Whilst it is important for authenticity of material and processes to remain as true to the originals as possible, it is important to highlight where this was not the case. Mild steel was used for the medial inner thigh support opposite to the lateral stabiliser, instead of wrought iron because it is difficult and expensive to acquire wrought iron today especially in the small quantities necessary for this experiment. Wrought iron is virtually pure iron with low carbon content (0.1-0.25%), it is therefore tough, malleable, ductile and easily forge welded (Kord, 2013: 9-10) – important during the nineteenth-century because the welding torch had not yet been invented. Wrought iron was used for items like artificial limbs because although refining steel was possible from the 1600’s onwards, it was expensive as the iron used for steel was imported from Sweden as it was of a higher quality than British iron. Wrought iron was strong particularly under tensile strength and could be easily worked but primarily, it was cheap (Kord, 2013: 10). Mild steel was used in this reconstruction, it contains slightly more carbon than wrought iron (0.33%) yet this changes its properties significantly, it is harder and hardens quicker when hammering, making it more difficult to forge-weld.
Many sources such as Warne (2008, 2011), describe homemade peg legs using easily sourced items. Lazenby and Pfeiffer (1993, p.23), who researched an ectoprosthesis belonging to a nineteenth century criminal called Maddie Brown showed ‘much evidence to suggest that the prosthesis was ’homemade’, albeit with some expertise’. Warne (2008, p.3) expands upon this by suggesting that the ‘lower classes would produce their own peg legs from table or chair legs and belts due to the expense involved in purchasing one’.
Finally, equipment such as specific wood working tools including chisels and hand planes were also required throughout the production phase. All of which were authentic tools, available at the time, similarly, where a required tool was not available, the woodworker manufactured his own tool from scratch – something that has been mentioned as occurring in production manuals such as Bigg (1885), Marks (1905) and Gray (1855).
Experimental Steps and Variables affecting Experimental Outcome
Working Wood
The first step required was to establish exactly how much wood was required for the construction. This was done by taking measurements of the intended wearer’s remaining limb assuming the amputee was trans-tibial. Whilst no documentation was found to describe this process, it was done to ensure what was produced would be the right fit and safe for the wearer. In this case, the wearer’s left limb length is 0.96m, the right thigh circumference (where the leather strap attachment will sit) is 0.52m and the waist circumference (for the leather attachment) is 0.82m. Using these measurements, it was established that the amount of wood required for reconstruction for a male trans-tibial amputee of 165cm in height and 67kg in weight, is about 0.007125m3. Lower and working-class demographic data for Victorian Britain suggest 165cm was an average height (Galofré-Vilà, Hinde and Guntupalli, 2017) and around 60kg in weight for a man during the 19th century (Floud and Harris, 1997). The wearer for this experiment matched these averages.
The wood was sourced partially prepared from a local boat yard as seen in Figure 1. The main structure of the ‘box’ peg leg comprises three individual wooden components (See Figure 2), these are the lateral stabiliser, a base to hold the stump and the peg. Based on Lazenby’s (Lazenby and Pfeiffer, 1993, p.22) description of the proportions of each three sections, the wood was measured and divided into three parts. A ruler and pencil were used to mark out the areas, which would be cut to size, with the offcuts highlighted by the hashed pencil marks (See Figures 3 and 4). Initial observations of these measurements indicate a large amount of waste. The stump is 45.2cm tall 15cm wide at the bottom, its thickness is also 5cm. The stabiliser is 87cm tall and 2cm wide by 2cm thickness. Finally, the stump support block is 2cm tall, 15cm by 8cm wide. In total this makes 0.003978m3 which means the off cuts and potential waste is approximately 0.003147m3, almost half the original amount of wood sourced. As few records explain production processes of a peg leg, especially ones which suggest a use for the off cuts of wood, it may be practical to propose this wood was used for other purposes, perhaps in the prosthesis manufacturers other businesses as cobblers, clockmakers or carpenters. Alternatively, the offcuts could have been used in ways described below.
In the nineteenth century, hardwood timber was still sourced locally in England, unlike softwood, which was imported from Canada. Greater mechanisation of sawmills during the industrial revolution saw logs turned into lumber and so the manufacturers requiring wood would have received their material in much the same way as acquired for this experiment (See Figure 1) stripped of bark and cut into manageable pieces. The wood working expert explained that to source a block of wood in the thickness required would prove very expensive today as it is an unusual thickness. To combat expenses and keep overall costs down, the offcuts produced during the carving process were used to build up the thickness in areas, which required more strength to withstand weight. He then sanded the harsh edges down to create a smooth other surface and ensure the joins were almost invisible. After analysing photographs, drawings and descriptions it became apparent that most peg legs had a varying appearance, and so the shape of the peg was left to the wood workers discretion (within the parameters of the photographs). As one of the aims of this reconstructive element was to establish an experiential methodology, observing material skill and perceptual aspect of a process meant allowing the expert to make decisions based on his expertise. The final shape is seen in Figure 14 and shows a similarity between typical 19th century designs.
The next section of wood that was measured and marked out for cutting was the lateral stabiliser. This is attached to the outside of the thigh stump to provide support. It is a thin piece of wood, which can move and bend slightly with the wearers movements. The final wooden element to be produced was the stump support (See Figure 8). This is a solid block, which was used by the amputee to place their leg for stability. It is the point of contact between the prosthetic and stump and therefore requires the most attention to ensure pressure and forces on the stump are minimised to reduce pain. The support was chiselled and carved to the template drawn onto the block originally, the edges were then smoothed to remove any splinters or sharp edges which may eventually cause discomfort to the wearer or damage to the leather which will be attached. Open socket peg legs had cloth rags to provide cushioning for the distal end of the stump, allowing a free range of motion, however, these were not added by the manufacturer, they required extra materials and therefore expenditure so the amputees were told to “rest the knee on a very full pad, otherwise it will soon become tender and incapable of transmitting the weight of the body to the artificial appliance.” (Bigg, 1885, p.67). Gray (1855, p.78) claims that the endeavour of artificial limb makers was ‘to make the stump fit the socket, not the socket fit the stump’. As the padding was not originally supplied by the manufacturer, it has not been included in this production. However, for the wearer’s comfort during gait analysis it will be supplied.
The final process involved attaching the three wooden elements together (See Figure 2, 8 and 9). This required the use of metal nail fasteners, which discussed below.
Working with Metal
A total of four copper-alloy nails were used to secure the lateral stabiliser to the peg (See Figure 9), and two were used to secure the stump support to the peg (which will eventually be covered with leather). The holes for the nails to fit through were roughly made using a hole saw and then hammering the nails into the wood so they created a tight, secure fit.
As explained above, mild steel was used for the medial inner thigh support opposite to the lateral stabiliser, instead of wrought iron. The metal was sourced from a blacksmith who advised it to be roughly hammered on a knife makers’ anvil to the shape of the peg, before securing it onto the wooden peg. Once the thigh support was roughly shaped using a hammer and anvil, holes were punched using a cross cut chisel in order to make small slots for the nails to fit into in order to secure the thigh support to the peg (See Figure 10).
Leather
Many sources describe homemade peg legs using easily sourced items, for instance Lazenby, (Lazenby and Pfeiffer, 1993, p.23) who researched an ectoprosthesis belonging to a nineteenth century criminal called Maddie Brown showed ‘much evidence to suggest that the prosthesis was ’homemade’, albeit with some expertise’. Shortland (2004) notes that some manufacturing processes create by-products, only one needs to be recognised as useful and the possibility of reuse occurs.
Consequently, the leather that was sourced and secured to the artificial limb in this reconstruction was a reused belt leather. This decision also offered the opportunity to make the straps adjustable to fit the stump and waist of the wearer, not only a positive for this experiment which means a range of people can wear it but it also would have proven beneficial for original wearers due to the changing stump sizes after amputation. Gray (1855) explains that for about two years after amputation, the stump goes through a series of shape changes as a result of swelling, possible infection, irritation from ill-fitting sockets and prosthesis. Therefore, whilst the literature does not confirm this, it may be suggested that a useful attribute of utilising adjustable belts as straps meant that the wearer could self-manage the fit of their artificial limb. There are two leather straps attached to the lateral stabiliser, 0.30m apart. The lower thigh strap is 0.09m wide, it sits 0.10m above the stump support and was attached to the lateral stabiliser utilising a slit in the leather that already existed. It slipped over the top of the stabiliser where after securing it to the wood with two copper alloy tacks, it was finally attached with another two copper-alloy nails to the thigh support (See Figure 12 and 13).
The next phase involved attaching the leather waist support to the lateral stabiliser, again that was secured in position using two copper-alloy tacks (See Figure 14). The last leather that needed to be attached was the leather covering the stump support, this involved cutting to size the circular piece of leather required and then stretching over the wooden support block. It was secured in place using some hide glue and ten copper-alloy tacks, then the excess leather was trimmed away. The completed the leg was then polished and varnished to bring out the woods natural grain, making it more aesthetically pleasing. Figure 15 shows the completed leg, Figure 16 shows how the limb looks whilst being worn. Figures 17 and 18 shows how the straps fit the torso and upper thigh.
Analysis, Conclusions and Next Phases
During the production of the peg leg, the manufacturing process was recorded using photographs and notetaking. What became clear during the process is that the wood working expert’s familiarity with the material and tools created a fluidity to the process with decisions appearing to be made instinctively rather than calculatedly as Sennett (2008) has discussed. The engagement with the material and the use of the same materials available during the nineteenth century have created a more reliable, comparative reproduction. Likewise, the effort, timescale, and skill level involved in production is more comparable to the original. Due to employing the assistance of a woodworking specialist historical and scientific authenticity has been applied to the reconstructions.
The woodworking expert’s familiarity with the investigative and recording process, meant that they were aware that spatial movements, material, tool and technological decisions made during the manufacturing process were to be kept as truthful original production method as possible. For instance, he explained that it was unlikely that he would have all of the necessary wood working hand tools required for the job and would therefore make tools for the specific job he needed it for. As documentation such as Kirkham (Kirkham, Mace and Porter, 1987) has stated, it was not ‘uncommon’ during the nineteenth century for manufacturers to ‘create their own tools’ specific for a particular job as required. The anticipation of mechanical need, demonstrates a material understanding and a familiarity with potential manufacturing issues but also the knowledge of how to overcome these issues.
The processes necessary to reconstruct a peg leg style artificial limb (identified from Bigg 1887 documentation of a ‘box leg’) were demonstrated and documented. This included identifying the potential order of manufacture process, the materials and methods utilised. By applying information collected from contemporary documentation and the various elements necessary for the production of a peg leg, an identifiable artefact was produced. From here, the reconstruction will be subject to further analysis to determine the accuracy of is shape, size and material. Its efficiency in comparison to modern prosthetics and the Anglesey Leg will be assessed through the use of Vicon Nexus software, a wearer will walk and their gait will be recorded and compared to their gait in an Anglesey Leg. This data will then be used as a comparative element to modern gait analysis in order to highlight potential detrimental effects. This will allow a greater comparison and reflection on original peg legs.
About the Author:
Charlotte Waller-Cotterhill
PhD Candidate
University of Sheffield
Bibliography
Ashby, M. and Johnson, K., 2002. Materials and Design: The Art and Science of Material Selection in Product Design. Butterworth-Heinemann. p.223.
Bigg, H.H., 1885. Artificial Limbs and Amputations: Artificial Limbs and the Amputations which Afford the most Appropriate Stumps in Civil and Military Surgery. London: Institute of Orthopaedics.
Childress, D., 1985. Historical Aspect of Power Limb Prostheses. Clinical Prosthetics and Orthotics, Vol 9, 1. pp.2-13.
Finch, J., 2011. The Art of Medicine: The Ancient Origins of Prosthetic Medicine. The Lancet, Vol 377.
Floud, R., and Harris, B., 1997. Health, height and welfare: Britain 1700-1980. In R. Steckel and R. Floud, eds., Health and welfare during industrialisation. Chicago: University of Chicago Press, pp.91-126.
Galofré-Vilà, G., Hinde A. and Guntupalli A., 2017. Heights across the last 2000 years in England. Discussion Papers in Economic and Social History, Number 151, Oxford University. Available at: https://www.economics.ox.ac.uk/... [accessed 10/08/18]
Gray, F., 1855. Automatic Mechanism, As Applied in the Construction of Artificial Limbs in Cases of Amputation. London: H. Renshaw.Kirkham, P., Mace, R. and Porter, P., 1987. Furnishing the World. The East London Furniture Trade 1830-1980. Journeyman.
Kord, M., 2013. A Study of Test Data for an Informed Assessment of Old Metallic Structures and Early Reinforced Concrete Structures, Masters Thesis available [online] at https://core.ac.uk/download/... [accessed 31/07/18]
Lazenby, R. and Pfeiffer, S., 1993. Effects of a Nineteenth Century Below Knee Amputation and Prosthesis on Femoral Morphology. International Journal of Osteoarchaeology, 3. John Wiley and Sons Ltd, pp.19-28.
Marks, A., 1905. Artificial Limbs, Copiously Illustrated: An Exhaustive Exposition of Prosthesis. New York, USA.
Pfaffenberger, B., 1992. Social Anthropology of Technology. Annual Review: Anthropology, 21, pp.491-516.
Sennett, R., 2008. The Craftsman. London, Penguin Books.
Shortland, A., 2004. Hopeful Monsters? Invention and Innovation in the Archaeological Record. In: J. Bourriau and J. Phillips, eds. The Social Context of Technological change 2: Egypt, the Aegean and the Near East 1650-1150 BC. Oxbow Books: Oxford.
Sweet, R., 2016. Prosthetic Body Parts in Literature and Culture 1832 to 1908. PhD Thesis, University of Exeter.
Warne, V., 2008. Artificial Leg. Victorian Review, 34(1), p.1.