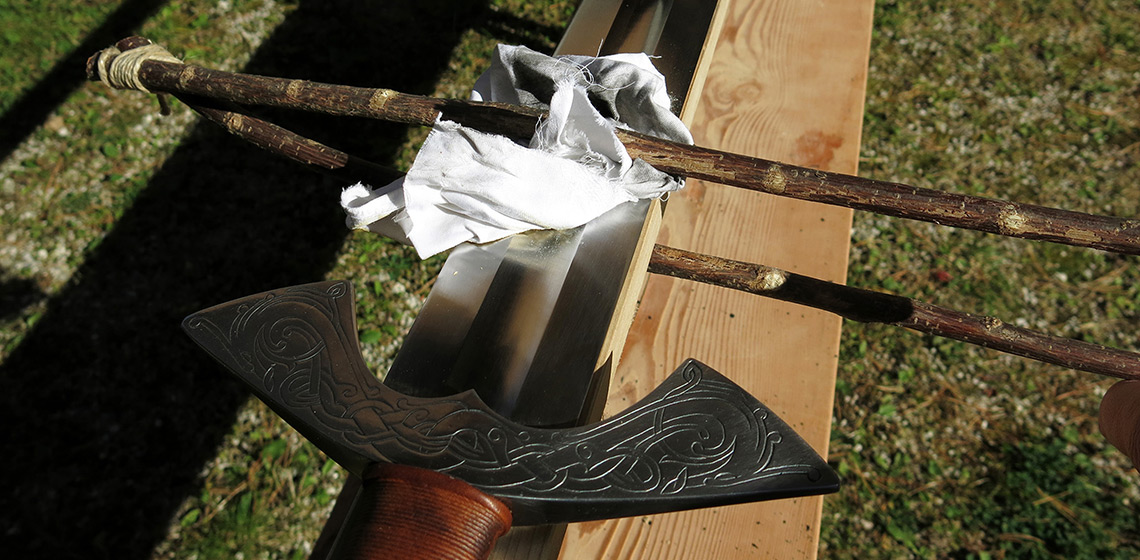
In the late 5th century AD, the famous Ostrogoth Theoderic the Great received a truly regal gift from the king of the Warini: he was given highly elaborated swords, richly decorated and able to cut through armour. Their fullers (long grooves along the flat side of the blade to reduce weight and to gain stability, often falsely called “blood groove”) were so well made it was as if worms (or dragons) were crawling upon the surface. But the most outstanding feature was indeed the surface of the blades, which were so expertly polished as if to create “a mirror for men”. To prove that this description of the quality of medieval swords wasn’t an exaggeration I was granted funding by the Tyrolean Scientific Fund (TWF) to reconstruct a medieval polishing bench and to examine possible historical abrasive agents.
Starting Point
At the core of this endeavour stood the well-known letter from Theoderic the Great, king of the Ostrogoths. Herein he thanks the king of the Warini, who had sent black timber (bog oak) and blonde boys, also “swords, which are able to cut even through armour and which I adore even more for their iron than the gold on them. Their clarity is so polished, that they reflect with exact clearness the faces of those who look at them. Their cutting edges run so evenly to the tip that one might assume that they are not made with files but formed in the furnace. Their centres, hollowed out with beautiful impressions, appear as if crimped with little worms, and here there play so manifold shadows that one might think that the shining metal is interwoven with many colours. This metal is ground on your grindstone and polished with your shiniest (possibly "most famous") powder so persistently until its steely gloss becomes a mirror for men [speculum virorum]; this powder is granted to you among the natural treasures of your land, so that its possession may give you unique glory. Such swords, in their beauty, could be seen as the work of Vulcan, who is said to have refined his craft with such dexterity that all that was formed by his hands was not made with human, but with divine power […]”. (Mommsen, 1894, 4 C 1. Translated by the author on base of Mäder, 2003, p.38f.)
We can see that the Ostrogoth king was very impressed by the gifts, and eloquently praised the quality of the weapons. He was not only fascinated by the shape of the swords, but even more by their surface. The mention of the mysterious polishing powder is the starting point for my scientific investigation. Obviously, it was a special polishing substance for steel or iron, which was widely famous.
Unfortunately, the letter does not mention exactly which substance it was. For this reason, I have started a series of experiments to test the effect of different agents on a reconstructed polishing bench.
The reconstruction of the polishing bench involved several considerations:
- Are the visual sources precise enough to reconstruct the polishing bench and its tools? If not, what needs to be changed?
- Do the illustrated working procedures work at all or are they just conceptual?
- Which medieval methods and abrasives are best suited for the task?
Picture sources of polishing benches
An abrasive cannot be easily applied to a sword. When polishing, the weapon must be fixed in some way on a working platform to allow an even surface treatment. This also makes the work considerably easier.
For this purpose, a special form of polishing bench was developed in Europe. The oldest pictorial evidence of such a bench comes from the Utrecht Psalter, which was made around AD 820-835 in the monastery of Hauteville. This psalter contains the Book of Psalms, which was illustrated with detailed Indian ink drawings (digital scan: http://psalter.library.uu.nl).
Along with weapons, clothes and other things of daily life, craftspersons are also depicted. On folio 45v there are three sword cutlers (Ger. “Schwertfeger”) which accompany the text. “Hear, O God, my prayer, when I make supplication to thee: deliver my soul from the fear of the enemy. Thou hast protected me from the assembly of the malignant; from the multitude of the workers of iniquity. For they have whetted their tongues like a sword; they have bent their bow a bitter thing, to shoot in secret the undefiled.” (Psalm, 63, 2-5).
In the corresponding illumination (Utrecht Psalter, 820, fol. 45v) one can see at the edge two stages of sword polishing: On the right, an artisan with a sword in his hands bends over a rotating grindstone driven by a helper. Here the coarse grinding of a weapon is shown very realistically. In the lower part of the picture (See Figure 1) it is possible to see a low bench with a sword on it (probably fixed). The sword cutler bends over it and works the weapon with a simple stick-shaped tool in both hands. His hand position is remarkable. With the left hand he grasps the tool from below, with the right hand from above.
The composition of this psalm is reinterpreted in the Eadwine Psalter around AD 1150, and there is added a transverse, bright appendix to the stick-shaped tool (See Figure 2, Eadwine Psalter, 1150, fol. 108v). This appendix could be a polishing or honing stone as Mäder had already suspected (Mäder, 2003, p.55ff.).
From the High Middle Ages onwards, the design of the polishing bench changed. In the Codex MS Bodley 264 of the Oxford Library there are two illustrations (See Figures 3 and 4, MS Bodley, 264, 1300, fol. 49r and 113v) of polishing benches, which are used by two craftsmen each. Here an additional raised working platform is mounted on the low polishing bench. This changes the tool from a simple stick to a clamp like tool consisting of a stick and possibly a belt. The new design allows the tool to be guided better and to be more stable. But the strange hand position is still the same. While at the polishing bench on fol. 49r the left figure has a whetstone/steel fastened in the tool, the two craftspersons on fol. 113v, have dark objects between the tool and the surface of the sword, possibly leather or textile rags.
In addition, the illustrations in the MS Bodley Codex show small horns tied to the sides of the polishing bench, which probably contained the abrasives. This positioning allowed the craftsperson to quickly add new polish.
Very detailed depictions of early modern age polishing benches can still be found on a ceiling fresco in the Uffizi in Florence (See Figure 5) and on a songbook page from Brod in Bohemia around 1600 (See Figure 6, Husa, et. al., 1971, p.163). These two illustrations also provided the decisive indications for the reproduction of the polishing bench and the clamp like tool.
Reconstruction of the polishing bench and the tool
Due to the detailed image sources, the reconstruction of the polishing bench was not a major problem: Two massive uprights (28 x 20 x 5 cm) were mortised into a board with four legs, 180 cm long and 24 cm wide, and fitted with dowels. A 128 cm long and 5 cm wide board was then applied on these. The dimensions of the latter board depend on the length of the swords to be polished: one-handed swords of the High Middle Ages usually have a length of about 100-110 cm, but late medieval one-and-a-half-handed swords can be up to 125 cm long, or even longer.
The main type of wood used was larch, due to local availability. This wood is much heavier than the more common spruce or hardwood, which in this case brings a major benefit: Because of the higher weight the polishing bench is much more stable when working - especially when polishing alone. To make the bench easier to transport, all connections are made of wood and can be dismantled in a few simple steps (See Figure 7).
The tests have shown that either one or two people can work well on it. The working height of the sword is approx. 80 cm, which is enough to allow the workers to bend over the weapon to take a closer look at the polishing sections.
The clamp like tool was interpreted as two flexible wooden rods. A functional example of this clamp could be made from two hazel branches (See Figure 8). When dried, these branches are both elastic and sturdy, thus making them perfect for this type of handling. The advantage of polishing with such a clamp is that the pressure on the surface remains constant and that the craftsperson could not injure their hands at the sharp cutting edges. In picture sources from the Middle Ages one can often see that the polisher grasps the clamp with one hand from above and with the other from below. This may make it easier to control the tool with certain sword shapes. In order to bring the polishing substance evenly onto the surface of the sword, a piece of moist linen was clamped in, which worked excellently during the reconstruction. The image sources do not show whether the swords were fixed during polishing. In the picture (See Figure 4, MS Bodley, 264 1300, fol. 113v.) the handle could be tied onto the board, but you can't see it properly. On the medieval illustrations you can usually see two craftspeople who probably stabilized the weapon reciprocally.
During my experiments, in order to prevent the sword from slipping without a helper, it had to be attached on the handle with a cord to the polishing bench. A wooden clasp at the tip provided additional stability.
Research on historical polishing agents
To polish a sword blade to mirror finish, it requires a series of preceding steps. After forging, the weapon has to be coarsely ground on a whetstone and then smoothed with increasingly fine abrasives. Only when a grain size of P600-800 (according to the standard of the FEPA - Federation of European Producers of Abrasives) has been reached and the surface is already glossing dull and has no scratches, can various polishing agents be used. Here again the principle applies that one goes from coarse to increasingly finer polishing agents.
In the letter of Theoderic to the king of the Warini a shiniest powder is mentioned, which, however, is not specified more exactly. This is presumably kieselguhr, a siliceous sedimentary rock also called "Tripel" in German (cf. Mäder, 2003, p. 57). The collection of technical formulations "Mappae Clavicula" (Mappae Clavicula 12th century) also dates from the Middle Ages. This work consists of numerous descriptions of substances and recipes, the core of which dates back to late antiquity and which were repeatedly expanded into the High Middle Ages. A part of the "Mappae Clavicula" is dedicated to the production and refinement of metals. For polishing, emery, old sherds of pottery (probably Terra Sigillata) and pumice are mentioned (cited after Mäder, 2003, p. 58f.).
In addition to these source texts, close cooperation with the project partner Dr. Stefan Mäder served as the basis for research on medieval polishing agents. In his dissertation (Mäder, 2003), Mäder dealt extensively and in many ways with the surface treatment of early medieval seaxes using polishing methods from Japan. Furthermore, the historical works "Die Kunst des Messerschmiedes" (Landrin, 1836), "Die Geschichte der Schleifmittel" (Feldhaus, 1919) and "Handbuch der metallografischen Schleif-, Polier- und Ätzverfahren" (Berglund, 1940) provided important clues.
The book "Die Kunst des Messerschmiedes" (Landrin, 1836) is one of the most important sources for pre-industrial metalworking, as it was written before the mechanisation and industrial production of metals and other substances. The engineer Landrin meticulously describes all the steps and materials used by the cutler. On the topic of polishing the steel surface he mentions three substances: emery (Ger. "Schmirgel") in three different grain sizes, ash of tin ("Zinnasche") and "Colcothar", or "Engelroth". The latter is a red iron oxide (Iron(III)oxide) whose name derives from its origin from England (Landrin, 1836, pp.122-128). Red iron oxide is also mentioned very often in other historical literature as a polishing agent (i. a. Feldhaus 1919, p. 43; Berglund, 1940, pp.30-31).
The ash of Common Horsetail (Ger. "Zinnkraut") is known as a plant-based polishing agent. Also, in traditional craft, ash was often used to polish metals (thanks to Reinhard Messner for the information). Ash from Common Horsetail contains about 70% of SiO2 (Dreuw, 2013) and is therefore suitable for producing a fine white shine on iron surfaces.
The use of emery as a grinding and polishing agent is still widespread today. Originally, emery was a natural stone from Naxos, today it is produced industrially. Since there was no possibility for me to get the stone from Naxos, emery was not used in the test series. Ash derived from tin was also not considered, as the production under historical conditions involves health risks. For this reason, other historical polishing agents could also not be taken into account. For example, there is evidence of polishing agents containing arsenic that are said to have provided a special shine (thanks to Peter Johnsson, MA, for the information). Landrin also describes a range of polishes based on lead and other metallic oxides (Landrin, 1836, pp.117-128), which are considered toxic.
Practical tests of the polishing agents
For the practical tests of the polishing agents I chose eight different substances (See Figure 9).
Kieselguhr (also called "Tripel") | Is a natural sediment consisting of the shells of fossil diatoms. It consists mainly of amorphous SiO2 and is highly porous. Acquisition: Purchase from chemical company Zeus (Bozen/Bolzano, Italy). |
Ash of Common Horsetail ("Zinnkraut") | Acquisition: gathering of the horsetail, incineration and preparation by the author. |
Iron silt | Consists mainly of iron (III) oxide: In order to obtain a product as pure and natural as possible, sedimented iron silt was obtained from an abandoned iron mine in Antholz-Obertal (Italy). The silt was then levigated (“Schlämmen” in German: separation of the inhomogeneous components according to their density by mixing it with water and sedimentation) finely by the author, dried and processed into fine powder. |
Clay | Consists of fine-grained silicate clay minerals. Purchase: Gift from Dr. Ulrike Töchterle, University of Innsbruck, fine levigation by the author. |
Finely ground stone powder | As reference materials were used: (1) Dolomite (samples from the Tofana, Italy, obtained by the author), (2) Calcareous tuff from Greece (bought from Ikea) and (3) Volcanic sand from Iceland (samples from the beach near Vik, obtained by the author). |
Terra Sigillata | This type of ceramic consists of particularly high-quality and fine clay. Purchase: Gift from Dr. Julia Rabitsch, who snapped off small fragments of insignificant body sherds of Terra Sigillata for her ceramic analyses. This ceramic type was chosen due to the mention in the Mappae Clavicula from the 12th century (see above). Further processing by the author. |
All samples were ground to a very fine powder in several passes first with a hand mill and then with a stainless-steel mortar. A more common stone mortar was not used in order to avoid contaminating the samples with stone abrasion. The graining was evaluated using haptic methods, as no suitable measuring instrument was available.
All polishing agents were applied to a piece of linen cloth moistened with water. A modern sword (model Ulvbane by Albion Armorers) served as a reference object for polishing (See Figure 11). The steel of the blade corresponds to a 1060 High Carbon Steel which is basically iron with a carbon content of 0.6%. Like other swords from Albion Armorers, first sword smith Peter Johnsson developed the design and made a prototype. For the mass production Albion Armorers uses a billet of industrial forged steel, which is then carved out with computer guided tools on a work bench to ensure that every sword is identical. The further processing includes heat treatment and quenching, grinding of the exact form and the final assembling with pommel, guard and grip (thanks to Peter Johnsson, MA, for the information).
The sword was not forged with traditional methods but with modern ones. Therefore, the surface corresponds just rudimentary to that of historical swords and the polishing of modern homogeneous steel is probably easier than hand forged metal. This sword was chosen for the polishing since firstly a hand forged weapon was not available and the “Ulvbane” has a very broad and long blade which made it ideal for the testing of different agents on the same blade. The aim of this first test was to evaluate the polishing abilities of the agents. Here the homogeneous modern steel surface enabled a very good possibility to compare the results.
During the polishing process the cloth had to be moistened again, and again since it dried really fast (the testing was done during warm summer days) and polishing agents had to be added repeatedly (future experiments will also include linseed oil for making the paste). As a reference, each polishing process lasted the same amount of time (one hour) and concentrated on one part of the blade, sometimes with several cycles.
Polishing agent | Grain size | Grain size (µm) Dx (90) | Suitable for |
Volcanic sand | coarse | 283 | finishing |
Dolomite | Medium coarse | 253 | finishing |
Calcareous tuff | fine | 145 | finishing to first polish |
Iron silt | fine | 86.9 | first polish |
Levigated clay | very fine | 22.6 | first to fine polish |
Terra Sigillata | utterly fine | 416 | fine polish |
Kieselguhr | utterly fine | 74.8 | fine polish |
Ash of Common Horsetail | utterly fine | 152 | fine polish |
Table 1. Results of the tests.
A brief note here on grain size: All polishing agents passed through the same grinding procedure, but some of the samples could be ground much better and finer. The designations from coarse to fine refer to the relationships between the substances themselves. Even the relatively coarse volcanic sand has the consistency of fine flour.
Thanks to Jasper Moernaut of the Institute of Geology at the University of Innsbruck it was possible to analyse the grain size of the agents. For the research a Malven Mastersizer 3000, a laser diffraction particle size analyser (dispersion with ultrasound for 30 seconds with a frequency of 30%) was used. The “Dx (90)” parameter means that 90% of the total volume of material in the sample is contained and is a standard value.
In summary, it can be said that the historically known substances kieselguhr and ash of Common Horsetail are best suited to achieve a shine on the homogeneous iron surface of the benchmark blade (See Figures 12 and 13). Based on these first results, the author started a second series of experiments with these two substances, which after about five hours each actually resulted in a mirroring shine on the sword.
The grain size of the best polishing agents differs from 74.8 µm (Kieselguhr) to 152 µm (ash of Common Horsetail). The levigated clay was very fine (22.6 µm) and that explains the non-optimal results. Probably it was too fine. The result of the Terra Sigillata was a surprise as it was coarse (416 µm). That could be explained with the fact that the most refined powder was already used for the tests. As acquisition of new Terra Sigillata was not possible, the remnants had to be measured. Also, the pottery contained a wide range of grain sizes due to its manufacturing process (~20-400 µm). So, we can assume that the optimal grain size for polishing lies around 100 µm. But it seems that the actual grain size is not as important as the component and the form of the grains (for a detailed chart of the measurements see fig. 18)
Polishing of a reconstructed early medieval blade
The author is well aware that modern steel is by not equivalent to the material used in the Middle Ages. After evaluating the polishing materials, the reviewer's suggestions led to the polishing of a reconstructed seax, whose blade is closer to the originals of the early Middle Ages.
It is a "Langer Schmalsax" (length of the blade 35 cm, width 3.5 cm), with elaborate decoration in animal style from Scandinavia, made by Jeff Helmes from Canada (See Figure 14). The swordsmith refined the metal for the blade himself, so that it comes close to an original. Characteristic are the clearly visible foldings of the iron in the area near the cutting edge. With this process of the repeated folding the iron was cleaned from slag and other impurities. The heart of the blade is the characteristic pattern welding in the area of the fuller, which consists of two twisted steel rods with different carbon contents.
The seax reached the author with a carefully ground surface that already had a matt gloss (See Figure 15). Since ash from common horsetail had proved to be the best polish agent, the seax was now polished with this substance using the method described above. After four hours of repeating polishing and the consumption of approx. 0.6 litres of ash, one complete side of the blade was polished. It showed a fine mirror-like shine, which, due to the inhomogeneous steel structure, was not comparable to a modern mirror, but still appeared satisfactory. Even on the relatively narrow blade a reflection was clearly visible (See Figure 16). Since the surface of the seax is relatively close to that of early medieval spathas, it can be assumed that the mentioned swords of Theodoric mentioned also could have had a similar shine.
Conclusive remarks of the polishing process
Regarding the polishing bench, it was found that the existing pictorial documents were more than sufficient for the reconstruction. This part of the project therefore posed few difficulties. The choice of heavy larch wood proved to be right, as the greater weight provided additional stability.
A little headache was the correct fixing of the sword on the working surface when working alone. This was solved by fixing the hilt with a string to one of the uprights and attaching a wooden clamp to the tip of the sword. Since during polishing there was only movement along the sword and not to the side, the weapon remained stable. When polishing in two it became obvious that the sword could be fixed to each other: While one person polished the back part of the blade, the second person fixed the weapon with the polishing tool at the tip and vice versa.
The tool made of hazelnut branches proved to be surprisingly effective and proved itself from the beginning. The elasticity of the wood allowed the pressure to be precisely transferred to the surface of the blade. The polishing tool did not need to be replaced during the tests but showed some wear towards the end where it touched the underside of the working surface.
In addition to these technical aspects, it also became apparent that polishing for hours on the workbench was not particularly beneficial to health. The monotonous back and forth movement of the arms and the entire upper body resulted in tensions in the upper and lower back area. Therefore, the author had to do stretching exercises for 2-3 minutes every quarter of an hour in order to be able to continue the work effectively. In earlier times the craftspersons were certainly better used to this activity, but it certainly influenced their posture (hump, bad posture etc.). It could be considered whether these characteristic movements could possibly also be determined anthropologically.
Another conclusion from the experiments shows that polishing a sword is incredibly time-consuming. In five hours only a small part of the blade, about 10-15 cm long, could be polished to a mirror finish. Even though skilled craftspersons certainly worked more effectively, polishing an entire sword would be a job of several days. Probably also for this reason the specialization of the "Schwertfeger" developed in the Middle Ages, which brought swords and other weapons to high gloss. Very important for this result, however, is that the previous fine grinding and pre-polishing of the sword was carried out very carefully, as the deeper scratches cannot be removed by polishing alone.
At the same time, it has been shown that polishing makes the surface of the steel extremely even. This results not only in a shine, but also in effective rust protection, since aggressive substances find less surface to attack. The process can be compared to the so called "pließten (also pließen or blaupließten)" of modern knife blades. This technique, developed in Solingen, uses very fine emery from Naxos to “close” the surface of a blade which makes it nearly rust-free.
Dissemination for museum didactic purposes
In order to effectively present the knowledge gained from the project to a wider public, the idea of presenting the entire work process in the style of the late 13th century was born in cooperation with Dr. Stefan Mäder. The first detailed depictions of the advanced form of the polishing bench (See figures 3 and 4) and polishing agents date from this period.
Starting point was a sword from the High Middle Ages, provided from the collection of Dr. Mäder. This made it possible to simulate the complete manufacturing process of a sword from forging to polishing. As a highlight of this part of the project, the internationally renowned swordsmith Dr. Fabrice Cognot was convinced to forge an exact reconstruction of the sword using traditional methods (See Figure 17).
First the sword itself: It is a weapon from the 13th century (Oakeshott type XII), which was originally discovered during construction works in southern Bavaria and from there got into the antique market in Switzerland, where Mr. Mäder acquired it. Unfortunately, he was not able to find out more about the origin of the weapon.
This specific sword was chosen for two reasons: Firstly, it was the only original sword that was accessible for this invasive kind of experiments. Originally it was intended to conduct more analyses like a polished and etched microsection for the composition of the blade. Due to the poor conservation this had to be cancelled.
Secondly, the chosen sword matches perfectly the second stage of the polishing benches with the elevated working platform which was reconstructed. Thus, it’s an ideal matching situation of a sword, a bench and the agents all inspired by the knowledge of the High Middle Ages.
The sword itself is heavily corroded, which is hardly visible from the outside, because the first owner had the weapon restored and strengthened. To learn more about the construction of the weapon, the sword was x-rayed (thanks to Radiologie Dr. Lungenschmid, Medicent Innsbruck). Due to the strong corrosion, the X-ray machine was able to achieve excellent results: It turned out that the fuller was much longer than had been expected and that the blade was once broken. During the first restoration, the parts of the weapon were joined together again. It was also noticeable that the tip was incomplete. The accurate folding of the metal could be seen on the guard: The simple bar consists of numerous horizontal layers of iron, which were created by cleaning the pig iron.
Since apparently only little of the original iron core was preserved, the blade of the sword could not be polished at any point as was the original plan. However, two small sections were chosen for polishing: One end of the guard and the front of the octagonal pommel. Careful grinding and polishing on the guard revealed that corrosion had separated the previously welded iron layers. It looked better on the thick pommel, the iron core of which should have been almost completely intact due to the thicker material thickness. When polishing the front, limited pitting occurred, but it was possible to achieve a reflective shine on the surface.
Based on Peter Johnsson's theories regarding the geometric design of swords (Johnsson, 2015), the original length and shape of the weapon could be reconstructed (1160 mm).
Due to other orders, the completion of the sword by Fabrice Cognot PhD is planned for summer 2020. Cognot uses historical iron, the surface of which differs significantly from modern iron. In this way it will be possible to reconstruct the picture of a medieval sword as authentically as possible.
As a special feature, Mr. Cognot will polish only one side of the blade with conventional machine methods, while I will treat the other side with traditional polishing methods on the reconstructed bench.
This will give the entire project a special highlight. After completion of the research, the ensemble will be exhibited in the Klingenmuseum in Solingen and then in the Archaeological Museum of the University of Innsbruck. Visitors will then be able to see for themselves that a sword can also nowadays serve as a mirror for men and women alike.
Acknowledgments
The present research forms part of the author's PhD thesis, which he is currently writing at the University of Innsbruck (Institute for Archaeology).
Thanks to Stefan Mäder, Reinhard Messner, Ulrich Lehmann, Fabrice Cognot, Peter Johnsson, D. Ryan Gray, Jaspert Moernaut, Dieter Lungenschmid and Ulrike Töchterle.
Bibliography
Berglund, T., (1940) Handbuch der metallographischen Schleif-, Polier- und Ätzverfahren. Berlin, Julius Springer Verlag.
Dreuw, P., (2013) Warum Zinnkraut?. Available at < https://ackerschachtelhalm.net/wieso-zinnkraut.html > [Accessed 4 February 2020]
Eadwine Psalter, (1150) Trinity College, Cambridge (MS R.17.1). Available at < https://commons.wikimedia.org/wiki/File:Illustration_from_Eadwine_Psalt… > [Accessed 4 February 2020]
Feldhaus, F. M., (1919) Die Geschichte der Schleifmittel. Hannover, Hainholz.
Husa, V., e. a., (1971) Homo faber. Der Mensch und seine Arbeit. Die Arbeitswelt in der bildenden Kunst des 11. bis 17. Jahrhunderts. Wiesbaden, Löwit GmbH.
Johnsson, P., (2015) ‘Die Geometrie und das mittelalterliche Schwert’ In B. Grotkamp-Schepers, (ed.): Das Schwert – Gestalt und Gedanke, Ausstellung 26. SEP 2015 – 28. FEB 2016 im Klingenmuseum Solingen, Solingen, Deutsches Klingenmuseum, pp.16-27.
Landrin, M. H., (1836) ‘Die Kunst des Messerschmiedes.‘ Neuer Schauplatz der Künste und Handwerke, Band 85. Weimar, B. F. Voigt Verlag (Reprint 2016: Sternverlage Berlin).
Mäder, S., (2003) ‘Stähle, Steine und Schlangen. Zur Kultur- und Technikgeschichte von Schwertklingen des frühen Mittelalters.’ Schriftenreihe des Kantonalen Museums Altes Zeughaus Solothurn, Ausgabe 24. Berlin, Solothurn.
Mappae Clavicula, 13th century. Here mentioned: Mappae Clavicula 4, MS 17 of the city library of Schlettstadt, Dép. Haute-Rhine, kap. 99, 133, 145, 146-B-E, 191-A, 216). Available at < https://www.cmog.org/library/manuscript-mappae-clavicula > [Accessed 4 February 2020]
Mommsen, T., eds. (1894) MGH Auct. Ant. V, 1. = Cassiodorus, Flavius Magnus Aurelius, Cassiodori Senatoris variae. München, Berolini.
MS Bodley 264, 1300. Bodleyan Library, Oxford. Available at < https://digital.bodleian.ox.ac.uk > [Accessed 4 February 2020]