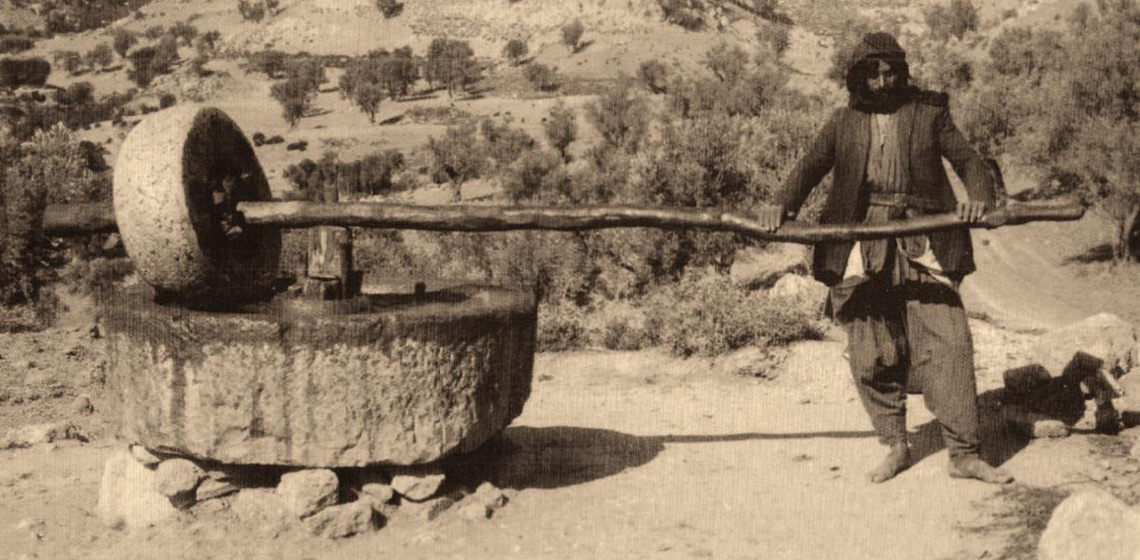
The vertical crushing mill turns the olives into pulp by combining the rotational and rolling motion of a heavy upright stone wheel that moves with continuous contact along a circular horizontal trajectory on a stationary base which forms the system's frame of reference. It was devised during the Hellenistic period and served as one of the most important and impressive means of production in the pre-industrial olive mills of Crete and the Mediterranean in general, until more advanced mill types gradually started replacing it from the mid-19th century onwards. Although there is a rich bibliography historically and from a technical point of view, there seems to be a relative knowledge gap from the aspect of the physical quantities that regulate its movement and affect its productive capacity. The paper examines this type of mill from the aspect of a complete machine, according to the ideas of F. Rouleaux (1875), whose approach is still regarded to be fundamental in the field of kinematic analysis and machine theory in general. The use of animal power is considered indifferent to this theory. A generic kinematic diagram for this specific mill type was composed, according to the rules of modern mechanical analysis. The diagram describes the kinematic pairs and defines its degrees of kinematic freedom. On the other hand, by examining the mill's actual function, the specific forms of energy involved in its operation were determined. The energy balance and mechanical efficiency of the mill were expressed as a factor of these energy forms. Also, by making use of a few but essential data, there was an attempt to estimate roughly the productive capacity of this type of mill. Although it can only be tested by experiment, it is suggested that this subtype of mola olearia was a machine with relatively high mechanical efficiency but very low productive capacity per time unit, mainly because of its underdeveloped feed mechanism.
τυφλώνουν σε, κακότυχον, δέρνουν σε μὲ τὴν βέργα,
γυρίζεις καὶ σκοτίζεσαι ἡμέραν τε καὶ νύκταν,
ἐκδέρνουνται οἱ κουτάλες σου, ὅλος ὁ σπόνδυλός σου,
καὶ ἀπὸ τὸν κόπον τον πολὺν καὶ ἀπὸ τὴν σκοτίαν
οὒτε νὰ φάης ἠμπορεῖς οὒτε νερὸν νὰ πίνεις, ...
When you get old, you get harnessed to the mill,
you poor horse; blind-folded, beaten by the stick,
revolving in dizziness - all day and night long,
your shoulders and spine a wound,
unable to eat, unable to drink
out of hard work, out of giddiness ...
Introduction
The vertical monolithic olive mill of the type of mola olearia which, like the Roman trapetum, first appeared during the Hellenistic era and spread all over the Graeco-Roman Mediterranean, surviving until the 20th century 1 . As elsewhere around the Mediterranean Basin, the numerous early modern era olive mills on the island of Crete, Greece,2 extracted olive oil according to a typical, labour-intensive, three-stage production cycle: (i) grinding of the olive fruit to produce pulp, (ii) pressing of the pulp to produce oil, and (iii) separation of the olive oil from water.3 The heavy, single upright millstones were engaged in the first production stage by turning the olive fruit into pulp. They used to be a conspicuous and very valuable4 element of every olive mill. Along with the oil presses, these impressive monoliths were the true machines of these primitive factories (See Figure 1). From the mid-19th century onwards,5 they were gradually replaced by more productive, multiple stone mill types, but some of them survived locally in Greece until the beginning of the 20th century and then, permanently abandoned with the prevalence of fully mechanized production methods. This paper aims to underline the mechanical dimension of these pre-industrial machines, describe their motion according to accepted kinematic models, and also express their energy balance in terms of physics.
Key features
The vertical crushing mill turns the olives into pulp by combining the rotational and rolling motion of a single, heavy,6 upright cylindrical7 stone wheel which moves with continuous contact on a horizontal stationary base along a circular trajectory. The massive stone wheel and the machine mechanisms are combined in such a way, whereby immense compression and friction forces are simultaneously exerted upon the olive fruit and its kernel, turning both into pulp. There are two important features to consider: a) the rolling motion happens around a more or less horizontal axis (the lever)8 and the rotational motion around a vertical one (the post),9 and b) a specific difference of the upright single stone mill when compared to the roman trapetum, is the continuous touch of the stone wheel with the firm base as it revolves around the pole.10 Due to the substantial thickness of the stone wheel11 this contact unavoidably generates slippage,12 which was not taken into consideration in the abstract kinematic model proposed here. Under these two important considerations, any variations in the arrangement of the machine parts such as the diameter of the base or the diameter and thickness of the wheel, the height of the post et cetera, do not affect the substantial kinematic features of the single stone upright mill. Yet, a typology of olive mills drawn upon their kinematics combined with regional variations would offer a fresh insight into the family of mola olearia.13
The kinematic mechanism
The fact that the power to move this type of mill is not automated but instead is generated by animals or humans is totally indifferent to the basic, modern era definition of what constitutes a machine: a machine is a device or mechanism which transforms energy, transfers and re-directs forces in order to achieve a specific purpose.14 In our mill, the chemical energy nested in the animal's muscles is turned through the machine's mechanisms into a compression force capable of crushing the olive fruit into pulp, thus processing it structurally and morphologically, ready for the olive press. Behind the sense of archaicity created by the sheer volume or robustness of these mills and by their slow-motion tempo,15 lies a rather complicated sequence of physical quantities that regulate their function. According to the modern era machine theory (after circa 1800), as developed and codified by Franz Rouleaux in his fundamental work Kinematics of Machinery - Outlines of a Theory of Machines,16 a machine is not a self-referential, isolated and admirable piece of innovation. Instead, a machine can theoretically and mathematically be analyzed into its components, which are nothing less than its kinematic mechanisms.17 Although other factors such as the chemical composition or strength of its material, size, power, et cetera of a machine are not ignored, it is precisely the kinematic chain and its forced movement18 which constitutes the very essence and originality of a machine. Regarding the machines of the pre-industrial era, Rouleaux recognises the absolute synergy of man and machine19 in the kinematic chain.20 This synergy considers man not only as a mere provider of brute motion power (as in the olive mill), but mainly as an intelligent part of its kinetic chain, capable of minute motions (as in the case of a loom). The synergy is also complemented by the manufactured item, as part of the kinematic chain itself. Rouleaux observes that the wear inducted to the manufactured item (in our case the olive oil fruit) during the course of this manufacturing process is typologically equal (although of a far greater magnitude) to the wear inducted upon the various kinematic chains of the machine.21 According to Rouleaux, human- or animal-powered machines form perfectly closed kinematic chains22 that are typologically equal to machines driven by a mechanical source of power.23 They are only differentiated by the fact that the more "archaic" a machine appears to be, the lesser its kinematic pairs in number are. In the case of these machines, the kinematic pairs resemble force-restraining pairs, more than movement-restraining pairs,24 and human involvement in the kinematic chain is much more substantial. Certainly, mola olearia does neither possess the delicacy nor the six degrees of movement a modern robotic arm does. On the other hand, its mechanisms are not as primitive as those of the wedge.25 According to the theoretical scheme of Rouleaux, mola olearia should be considered as a true and complete machine.
During the early stages of describing a machine, the joints (kinematic pairs) must be defined26 and take the form of a kinematic diagram, which is followed by a due mathematical analysis. The terminology and rules for drawing such a scheme are very precise, employing links,27 joints28 and degrees of freedom.29 The model of the vertical monolithic mill produced here (See Figure 3) represents―from all the possible variations I tried―the most concise one, also closest to the type of mills that were used in Greece. The model represents only those elements necessary for the kinematic analysis, omitting others such as the horizontal stability beam of the post, frequently seen in covered olive mills.30 There are three links in our model (No 1, No 2, No 3), forming three kinematic pairs: (1-2), (2-3), (3-1). Link No 1 is the reference frame ; the firm, motionless part of the machine required by the kinematic models.31 Link No 2 is the unified post-lever, bound together in a single linkage.32 The monolithic wheel (No 3) is the third link of the mill's closed kinematic chain. There are also three joints, namely A, B, C. In theory, the maximum possible number of motion freedom degrees for our system are:
[1 stationary frame of reference × 0 degrees] + [1 moving link (the lever-post combined) × 6 degrees] + [1 moving element (the wheel) × 6 degrees]=0+6+6 = 12 degrees of freedom. |
Joints A, B, C, each of which possesses a maximum of 6 degrees of freedom, impose motion restraints upon the links they connect by admitting some degrees of freedom and prohibiting others.33
- Joint Α, between the base (Link No 1) and lever-post (Link No 2) restrains every movement, except the revolving motion around the vertical axis ΖΖ. It has 1 degree of kinematic freedom and 5 kinematic constraints.
- Joint Β, between unified lever-post (Link No 2) and wheel (Link No 3) restrains every movement, except two, the rolling motion around ΧΧ and the movement along ΧΧ.34 It has 2 degrees of freedom and poses 4 degrees of kinematic constraint.
- Joint C between the wheel (Link No 3) and the base (Link No 1) restrains only the motion along the vertical ΖΖ, allowing all the rest, thus counting 5 degrees of freedom and posing 1 kinematic constraint. This joint forms the mechanism's point of interest, because it is exactly where force Fkinetic is redirected, resurfacing as a compressive force Fcompressive.
The sum of degrees of freedom from all the joints is 1+2+5=8 and the sum of the restraints is 5+4+1=10. The maximum number of potential degrees of freedom is 12 (as computed above), so the model's degree of freedom equals 12-10=2. This means that the monolith can revolve around a vertical axis ΖΖ (obviously) and according the construction technique of joint B can perform an extra movement (not so obvious, the so-called wheel's camber), although this special degree of freedom is usually inactive.35 According to the motion we want our machine to perform and the sophistication of the construction of the joints, we could possibly assign different degrees of freedom to each of the afore-mentioned joints. Yet, no matter what the possible variations of the kinematic model are, the total sum Σ of freedom degrees must conform to the Kutzbach criterion, applicable to every single mechanism that performs a motion in three-dimensional space.36
Σ = [6×(Number of links ‒ 1 ‒ Number of joints)] + (Degrees of freedom of all the joints) |
If Σ ≥ 1 then the system can perform a motion relative to its frame of reference.37
The Kutzbach criterion is fulfilled in our case, since Σ=[6×(3-1-3)]+8=2 >1. The three-dimensional kinematic diagram presented in Figure 3 is supplemented with the vectors of the two main forces that act through the system. A force Fkinetic, applied laterally on the horizontal axis38
ΧΧ (except of course the point where it meets ZZ) generates a torque which activates the system. As the system is performing a motion, a force Fcompress appears at the contact point of the wheel and the base. The magnitude of thıs critical force39
is Fcompress = (m×g) + (½×m×r×Ω2), which is greater than the sheer weight m×g of the millstone. Threfore, the mill's inert compressive ability is much augmented, depending not only on the wheel's mass m but also on the rotational angular velocity Ω squared. According to physics, the work produced by Fcompress can be equal or less compared to the work produced by Fkinetic. Actually it is always less, because there are unavoidable energy losses. A close look at the mill's energy balance will tell us about these losses and the mechanical efficiency of our device, and this is precisely the next step necessary to describe this type of mill as a machine.
The Mechanical Efficiency
Mechanical efficiency is a kind of energy identity of a system, simply defined as the ratio of the output energy to the input energy. In the case of the monolithic olive mill, although there is a rich bibliography about its evolution as well its historical and financial context,40 there is a knowledge gap regarding the strictly technical data that could help us define accurately its mechanical efficiency right from the start.41 My approach inevitably focuses on the mill's energy balance, through which one can readily grasp the machine dimension of this device. Let us assume that Εanimal is the input energy fed to the system by an animal or a human. The animal must constantly provide energy in order to balance the energy losses due to friction, according to the universal law of energy preservation:42
Εanimal = Εkinetic + Εloss (i) |
Where Εkinetic is the total kinetic energy43
of the stone wheel and Εloss the energy dissipated to every sort of friction that is generated during the rotation and rolling of the massive wheel. What is of interest though, is that a great part of what is conventionally classified as energy loss (Εloss) is in fact energy used for squashing the olive fruit, something achieved through both compression and friction.44
The portion of energy that is actually useless in the squashing procedure (let us name it Εparasitic) is what gets lost in the rolling friction of the wheel and lesser friction phenomena developed in the machine's joints.45
Thus, the fundamental mathematical equality (i) can be expressed as:46
Εanimal = Εkinetic + (Εgrind + Εparasitic)(ii) |
We can compare the monolithic wheel of the olive mill which is rolling atop a dense and unstable layer of mash spread on the base, to a tractor wheel47
as the latter is rolling on soft ground. In order to move, the tractor wheel has to compress and deform the ground, winning over surface slippage.48
In the same way and in order to keep moving, the mill's stone wheel has to deform the olive fruits under its path and push aside some quantity, while rubbing and squashing a fraction of it. The olive fruits' deformation is also achieved when the wheel slips from time to time.49
Yet, what would be an energy loss and obstacle in the case of a tractor, should count as useful output energy in the case of a mill, where instead of soil there is a layer of fruits. Thus, considering this subtle point and by replacing Energy with Work quantities,50
the factor n of mechanical efficiency is defined as:
|
a formula which can be equally described as:
|
or more elaborately:
|
where input Winput equals Wanimal provided by the animal as it moves around the circular base, turning the upright wheel.51
Wgrind is the useful work done by the forces that develop in the narrow contact area between the wheel and the base, grinding the fruit's flesh and the kernels as mentioned previously.52
Winitiation is the input work, generated by the force which starts and accelerates the wheel until it reaches a certain velocity.53
When the movement reaches a desired, steady and continuous level, there is theoretically no need for providing further moving force and thus there is no work attained. The initiation energy has been stored as kinetic energy (Ekinetic) in the wheel, and is given back as parasitical work Wparasitic when the wheel decelerates and stops.54
Considering that the formula (v), Wgrind and Winitiation can be both theoretically calculated and verified by experiment, the denominator as a block, which equals Wanimal in formula (iv), can only be estimated or verified by experiment. What remains unknown is Wparasitic, the real losses due to rolling friction and friction at the joints. Rolling friction itself is not significant and can be theoretically estimated;55
the friction at the joints would not be so high because these are lubricated by oil slippage.56
We thus expect Wparasitic to be a small fraction of Wanimal and certainly Winitiation is also small when compared to Wanimal so the ratio expressed in formula (v) tends to 1. This means that the monolithic upright olive mill was probably a high efficiency machine, something of course that should be verified by experiment. The best we can do at this stage is to estimate Wanimal and Wgrind.
"Motor" Power and Production Capacity
The mill's motor is usually animated by a donkey or mule, but less often a horse or a bovine is utilised. The choice was regulated along practical and cultural lines. In Greece, the burden was borne by the donkey, not an especially powerful equine, but nevertheless offered an excellent value for money ratio.57 A medium-sized Mediterranean donkey weighing about 200-300 Kg,58 producing a traction force up to about 30-40 Kg,59 and moving at a linear speed of 1,1 m/sec (3,96 Km/h)60 is estimated to have a power P around 350 Watt (=Joule/sec) according to this formula: 61
|
An animal of power Ρ, if it works for a time period t produces work Wanimal = P×t. Thus, the old horse scorned by the camel in the quote in the beginning of this paper (or instead the donkey) when it makes the wheel mill rotate for an hour62
produces work63
:
Wanimal = P×t = 350 (Joule/sec) × 3600 (sec) = 1260 KJoule (vii) |
Let us now estimate Wgrind. Our donkey cannot significantly exceed the power of 350 Watt, even if it is adequately fed or forced to its physical limits as the medieval poem implies, or if the owner assists, or if a more powerful animal such an ox is employed instead. To proceed further, we should know the required energy for grinding the most resistant part of the fruit - its kernel. A paper by Kılıçkan–Güner64
provides here the most useful data. According to them, in order to pulverize a single 20 mm diameter kernel of the Gemlik65
olive variety, the maximum force (rupture force) which has to be applied parallelly to the long axis X of the kernel is circa 585 Νewton and the total rupture energy66
is circa 28,41 Νm. Along the lesser Y kernel axis, the quantities are respectively circa 378 Νewton and circa 5,15 Nm, and for the vertical Z axis circa 401 Newton and circa 6,35 Nm.67
The mean force quantity drawn from the above data68
mentioned in the Kılıçkan–Güner paper, is circa 455 Newton/kernel item and accordingly, the energy required to totally grind the kernel is circa 13,30 Joule/kernel item.69
Energy needed for squashing the flesh is negligible, around 0,1 Joule/olive item.70
As 1 Kg of the specific olive variety contains around 263 items,71
we need Wgrind = (13,30)×263 =~3,50 KJoule/Kg.72
In fact, not every single kernel is pulverized during grinding. An interesting experiment carried in a mechanized olive mill73
showed that only ¾ of the kernels were ground.74
It means that theoretically speaking, Wgrind should be estimated at three quarters of the 3,50 Kjoule/Kg because, as the experiment suggested,75
grinding of the total number of kernels was not technically possible. On the other hand, we should also consider the fact that multiple wheel passes were required for grinding an adequate number of fruits and their kernels. The latter's actual number depending not only on the wheel's mass76
or the compression force it developed, but on the performance of some very practical tasks.77
The actual time employed in useful grinding was shortened by the need to manually spread the fruits on the base and keep arranging them under the wheel's path, and by the need to remove the pulp and replenish the fruits.There were the additional physical limitations of the animal and a series of hard to estimate practical factors.78
Attempting an educated guess, the olive fruit quantity that could be ground in such a mill during a time period t, using an animal of power P can be expressed as:
|
where α a reduction factor, only determined by experiment, inevitably fluctuating along historical, regional and temporal lines. This factor represents the energy and time losses ascribed to the actual conditions in those pre-industrial olive mills. In order to estimate the productivity of the mill, which means the quantity of the fruit ground per working hour, we express formula (viii) as:79
|
Where P is counted in KJoules/sec, t=3,600 sec, the denominator (¾×3.50) in KJoules/Kg as described previously. The hour of 3600 sec is understood here as "working hour", hence the involvement of factor α. This formula should be considered as a working hypothesis, the accuracy of which can only be tested by experiment. In fact, one expects factor α to have a rather low value. For example, if P=350Watt=0,35KJoul/sec as mentioned, α=0.20 and n=0.80, then the result is (0.20×0.80×3,600×0.350):(¾×3.50) = circa 80 Kg/hour, a quantity that seems to be in accordance with the paucity of documented evidence.80
This means that even the mechanical efficiency of the mill was adequately high, its productivity remained low81
because it lacked work and feed flow control mechanisms. This was a weak point indeed. A more modern and manageable type of olive mill with three or four, less voluminous millstones had an obvious advantage and gradually replaced the older, monolithic version discussed here.82
The old monolithic wheel could be compared to a heavy elephant that tries to crack nuts spread on the floor by jumping using one of his feet. The resulting blow would unquestionably be fatal for the nut, provided the elephant could find the target. So, the scorn of the camel in the old medieval poem seems to be justified, as during peak milling days the poor, old horse had to reach the limits of its power potential to do the job.
Acknowledgment
I am indebted to Mr. Christoforos Vallianos, Ethnologist, Mr Symeon Parcharidis, Architect, Mrs Loeta Tyree, Archaeologist, Mr Ioannis Antoniadis, Engineer at Athens Technical University, and Mr George Fanourgakis, Physisist at the University of Crete for their valuable insights and help.
Quote
from The camel is scoffing at the horse, Eideneier, ed., 2016, verses 784-789, from a 14th century satirical poem in Greek Demotic (Codex Constantinopolitanus Seragliensis 35). The translation is by the author.
- 1For a typology, see Hadsjisavvas, 1993; Hadsjisavvas, 2005, pp.64-65. For an overview of the older research on millstones, see: Runnels, 1981, pp.11-16.
- 2 Or post-byzantine, according to the historiographic point of view. There are a lot of historical reasons for the olive-boom in Crete during the 17th and 18th centuries, not to be considered here. See for instance Stallsmith, 2007, just to mention a paper accessible to the English reader.
- 3 For an overview see: Hadsjisavvas, 2005, pp.33-34, Pikoulas, 2006, pp.287-288.
- 4 See for example Doğan, 2007, p.161, where according to an ottoman olive mill inventory from 1854, the olive grinding mill is valued for 1,000 gurush and the olive press for 1,800 gurush, sums that account for 97% of the total mill value. A good idea of the work demanded for shaping a big round monolith is given by a comparison to the difficulty and time required for a mere quern (Runnels, 1981, pp.249-252). For details of a typical pre-industrial olive mill equipment see: Sordinas, 1971; Frankel, Avitsur and Avalon, 1994; Katsarakis, 1996; Parharidis, 2006.
- 5 For specific cases in Greece see Sordinas 1971, p.12; Runnels 1981, Table 44. For a broader view see: Μazzotti, 2004. The first machine-powered olive factory in the ottoman lands was established in Smyrna in 1851 (Doğan, 2007, p.186).
- 6 For a detailed description, see: Sordinas 1971, pp.8-9 and Frankel, Avitsur and Avalon 1994, p.109. Zivas records a monstrous millstone of 2.10 meters in diameter, with a width of 0.45m which weighs about 3,500 Kg (2000, pp.39-38).
- 7 Or about cylindrical, since its curvilinear surface (the strip between the faces) has in fact a double curvature. Excessively thick millstones, often take the form of a truncated cone.
- 8 The lever offers a mechanical advantage to the system, but from an energy point of view, there is no difference if it protrudes to the inner or outer face of the millstone. For reasons of ergonomy it often takes a curved shape. From a technical aspect, horizontality is not a prerequisite and could theoretically be adjusted by an exra joint at the meeting point of lever and post. See also footnote 37.
- 9 In covered olive-mills, like the one photographed by F. Boissonas (Figure 1), for reasons of balance, the upper hinge socket nests in a strong horizontal beam. Yet, in open-field mills, this beam is absent, the post becoming much shorter or entirely merged with the base.
- 10 In trapetum both millstones have a concave, lens-shaped section, but they do not touch the deep stone cup.
- 1140-50cm is a mean thickness; more substantial widths are often combined with millstones of lesser diameter.
- 12 Slippage occurs because the inner face of the stone wheel revolves around a lesser radius and so by definition moves at a lower linear speed when compared to the outer face. This phenomenon is understandably much more pronounced in thicker millstones. For details, see Μontes-Tubio, Burgos-Ladrón de Guevara and Carranza Canadas, 1998, also: Parharidis, 2006, p.301. In some millstones, the cross section takes the form of a slight curve, so as the contact with the base is restricted to a minimum. Only truly conical millstones (such as those used in Spain) can avoid slippage.
- 13 The proposed typology schemes so far are based on constructional, not kinematic features, see for instance Hadjisavvas, 1993; Runnels, 1981.
- 14 For a definition, see: Shigley and Uicker, 1981, pp.4-5 and Myszka, 2012, p.1. According to Rouleaux (1876, p.35): "A machine is a combination of resistant bodies so arranged that by their means the mechanical forces of nature can be compelled to do work accompanied by certain determinate motions". On the other hand, mechanism is a part of a machine, transforming motion in a pre-determined fashion, and transferring less force compared to a machine, which is something more substantial (Norton, 2004, p.4). All machines are mechanisms, but not all mechanisms are machines, the dividing line between the two not being very clear-cut (Norton, 2004, p.4).
- 15 I precisely kept time of the revolving motion of still working mills, displayed at amateur but very informative videos accessible through the internet on the YouTube platform. I observed that the revolving angular speed Ω falls in the span between 0.40-0.70 rad/sec. Angular revolution speed Ω depends of course on the species and strength of the animal (bovines and camels move at a slower pace), and the quantity of the olives processed. See the discussion here, at part E.
- 16 For the evolution of modern machine theory in general see: Koetsier, 2012; on Rouleaux: pp.496-497.
- 17 Kinematics is the study of motion without considering the forces applied to the system (Norton, 2004, p.3).
- 18 The condition of forced movement is pivotal. Kinematic pairs are engaged in pre-determined movements.
- 19 Rouleaux, 1876, pp.500-501.
- 20 Linkage or kinematic chain. According to Νorton, 2004, p.29: "An assemblage of links and joints, interconnected in a way to provide a controlled output motion in response to a supplied input motion".
- 21 Rouleaux, 1876, p.503.
- 22 In this type of linkage, each link is joined to two or more other links. In open chains, there is at least one link which is connected to only one other link (Myszka, 2012, p.4)
- 23"...they may be regarded as complete machines, and do not in themselves differ from machines driven by any other than muscular force" (Rouleaux, 1876, p.508).
- 24 Or as Rouleaux puts it, force-closure and pair-closure machines respectively (1876, pp.230-231).
- 25 Wedge is a mechanism that belongs to the so called "simple" or "basic" machines, although there is no concensus as to what is included in this group or what can be related to them (Rouleaux, 1876, pp.275-283).
- 26"A joint is a connection between two or more links (at their nodes), which allows some motion, or potential motion, between the connected links" (Norton, 2004, p.27). According to Rouleaux (1876, p.86): "We have already found, in the general solution of the machine problem, that the elementary (or what may be called the elementary parts of a machine) are not single, but occur always in pairs, so that the machine, from a kinematic point of view, must be divided rather into pairs of elements than into single elements".
- 27"Links are the individual parts of the mechanism. They are considered rigid bodies and are connected with other links to transmit motion and forces" (Μyszka, 2012, p.2).
- 28"A joint is a movable connection between links and allows relative motion between the links" (Μyszka, 2012, p.3). The motion between the links is predetermined. Joints are characterized mostly by their degrees of freedom (zero to six). See also the definition in Norton (2004, p.27), quoted here in reference 28.
- 29 If Χ, Υ, Ζ are the three axes of a Cartesian coordinate system, the highest possible degree of freedom for a single point in three-dimensional space is 6: 1degree for movement along Χ (forth-back) plus 1 degree for movement along Υ (left-right), plus 1 degree for movement along Ζ (up-down) plus 1 degree for revolution around Χ (clockwise-counter clockwise), plus 1 degree for revolution around Υ, plus 1 last degree for revolution around Ζ. Of course, zero degrees of freedom means movement incapacitation.
- 30 That such elements are excessive from a kinetic point of view, is proved by the open-air olive mills. Masonry arches, walls and other interconnected static structures seen at olive mills must be considered as part of the kinematic reference frame (Link No 1). The forces involved, the strength of materials, the construction details of the joints are indifferent to kinematic models. Links are considered to be rigid.
- 31 Shigley and Uicker 1981, p.6. The plane of the base is considered to extend infinitely. In the kinematic diagram (Fig. 3), the firmness of the reference frame is indicated by small triangles. The actual geometry and construction method of the base is indifferent to our motion model.
- 32 From the point of view of construction, the lever and the post are independent but in the proposed diagram are connected (think of them as a curved metal bar). The post can actually be omitted if considered merged with the base, as it happens in the open-air mill from Jordan, reproduced here in Fig. 2.
- 33 For every joint, the sum of degrees of freedom plus the kinematic restrains is always 6.
- 34 In most cases, the second degree of freedom is an inactive (or passive) degree of freedom (see: Phillips, 2006, pp.29-30), because the actual joint construction prevents its actuation. This specific degree of freedom is internal to the system and has no relation to phenomena of construction "play", which are secondary, neither to construction defects and material elasticity (in kinematic models joints are considered to be stiff).
- 35 The inclination of the wheel in the man-operated mill from Jordan (Frankel, Avitsur and Avalon, 1994) reproduced here (Fig. 2), makes a use of this second degree of freedom. Camber also means that the vertical angle between the lever axis and wheel plane is not a prerequisite for a smooth rolling motion. See also the inclined wheel of a Berber olive mill from Algeria (Camps-Fabrer, 2000, p.13), which has three joints.
- 36 Phillips 2006, p.14. For planar mechanisms respectively Σ=3×(links‒1‒ joints)+(number of degrees of freedom).
- 37 If Σ=0 the system is absolutely static. This is the case of buildings, bridges and other engineering structures that safely transmit forces down to earth (the reference frame) without of course being capable of moving (elasticity apart).
- 38 More precisely, the component of Fkinetic which is exactly vertical to the lever.
- 39 For the formula, see problem 7.4 in Kleppner and Kolenkow, 2010 and its solution in Baltz and Strovink (1998, p.4, Solution to problem 7.4 by K.&K.) The initial formula is Ν=mg+(½mr2ωΩ/R), substituting ω=RΩ/r, where ω is the angular velocity of rolling, Ω the angular velocity of revolving, r the radius of a mass m millstone, R the radius of revolution and g=~9.80 m/sec2 the earth's gravitational acceleration.
- 40 For an overview of the main bibliography, see: Hadjisavvas, 2005, pp.8-20.
- 41 The roman olive press productivity has drawn a special attention, see: Μattingly, 1993.
- 42 For a similar treatment of energy balance, see: Υong et al., 1984, p.221: Ιnput energy = Pull energy (the useful work for a tractor) + Dissipated Energy (energy losses).
- 43 One-third of the total kinetic energy comes from the rolling motion and two-thirds from the revolving motion of the wheel (Halliday, Resnick and Walker, 1993, p.323, Table 12.1).
- 44 The turning of the olives into pulp is a product of two types of forces: direct squashing under the wheel's weight and mashing because of friction forces between the wheel's edge and the base.
- 45 Mostly at the post's hinges.
- 46 For a similar treatment of the energy equilibrium in a water mill, see Holdsworth et al. (2015), where the kinetic energy is added to the energy required for grinding the wheat; also Υong et al. (1984, p.138): Input Energy = Output Energy (useful traction work)+Work Energy (energy for compacting the soil)+Interfacial Energy (energy for overcoming the slippage).
- 47 Υong et.al., 1984, p.55, Fig. 3.10; pp.135-136.
- 48 Slippage is considered to detrimental to the traction ability of a tractor, energy losses growing exponentially, see: Υong et.al., 1984, p.137, Chart 5.2; p.153, Chart 5.13.
- 49 The olive mills take advantage of this, see Parharidis, 2006, p.301.
- 50 The unit of Work in SI is Joule.
- 51 Equals Fkinetic×length of path covered by the animal.
- 52 Due to a combined action of Fcompress and of forces in the contact area of wheel-base.
- 53 Let us clarify this point. The still standing millstone is accelerated due to the force input by the animal, until its linear rotational and rolling velocity reach a more or less steady quantity. Because the motion trajectory is circular, so the acceleration vector is centripetal and not linear. The centripetal acceleration is due to the centripetal force Fc the vector of which is coaxial to the lever and points inwards to the pole. This type of acceleration constantly changes the direction of the vector of the linear rotational velocity and conserves the rotational movement. The presence of Fc is constant, even when the linear acceleration becomes zero, (Halliday, Resnick and Walker, 1993, p.294b) and does not produce any work. In a theoretical world with no friction, no further force would be needed after the initiation, for keeping the wheel running. In the real world, after the wheel's velocity has reached a desired level, the animal keeps providing a little force and small quantities of Fkinetic (albeit of lesser magnitude than Finitiation) to cope with friction losses.
- 54 The initiation of the wheel means its "endowment" with kinetic energy Εkinetic, which does not produce work because it represents movement and not force (only a force can produce work). The centripetal force cannot either produce work.
- 55 A practical calculation of rolling friction μκ can be achieved through formula μκ = (F×r)/(mg), where F is the easily measured force required to roll a load of a radius r wheel (Lippert and Spektor, 2013). This factor is a length quantity. In advanced mathematical models the rolling friction factor is a pure number and is calculated differently.
- 56 See: Parharidis, 2006, p.301.
- 57 The ratio of milling fees paid to the mill owner to the money spent for purchasing and feeding the animal. See: Falvey, 1988, p.137.
- 58 Goe and McDdowell, 1980, p.17.
- 59 Goe and McDdowell, 1980, p.17. Boie (1980, Table 1), gives for a 200-300 Kg donkey moving at 0.7 miles/hour (=0.313m/sec), provides a power of 245 Watt and traction force of 30-40 Kg. A 350-500 Kg mule moving at 0.9-1 miles/hour (=0.40-0.447m/sec) provides a power of 510 Watt and traction force of 50-60Kg. So 350 Watt is an adequate estimate for a reasonable revolution speed of 1,1 m/sec. Forbes (1965, p.85) quoting an older source, gives only 108 foot-pounds/sec (circa 146.5 Watt) for the power of a donkey moving at a speed of 3.6 feet/sec (=1.09 m/sec)
- 60 This speed was confirmed by watching and counting the time spent for one revolution of the animal.
- 61 Goe and McDdowell, 1980, p.3.
- 62 The hour of 3600 sec, as a scientific unit of time is longer than an ordinary and empirically defined "working hour". Actually, 12-15 working hours of an animal in the olive mill corresponded to a much lesser number of scientifically defined hours under the yoke.
- 63 We see that the work Wanimal produced by the animal is independent of the wheel's mass. Yet, a heavier stone would tire the animal in a much shorter time, or make it to move at a slower pace.
- 64 Kılıçkan and Güner, 2008.
- 65 Grey-greenish, fleshy, thin-skinned variety with a small kernel. The mean largest dimension of the fruit was measured about 25.25mm and the lesser 18.06 mm. The kernel is accordingly 16.73mm and 7.75mm (Kılıçkan and Güner, 2008, p.225, Table 1).
- 66 Rupture force is applied for a little longer after it has reached its "ceiling" value, until the kernel is tottaly shattered (Kılıçkan and Güner, 2008, p.224, Chart 2).
- 67 Kılıçkan and Güner, 2008, p.226, Table 3.
- 68 Assuming that rapture force is equally distributed along the three axes.
- 69 Work=Force×Distance, so 1 Joule=1Nm.
- 70 Kılıçkan and Güner, 2008, p.226, Table 3. The values for grinding the flesh of a single olive fruit item are 57 Newton / 0,10 Joule for axis Χ and 32 Newton / 0.060 Joule for axis Υ (no values provided for axis Ζ).
- 71 The bulk density of this variety is 556 Kg/m3, and the mean weight of a single fruit is 0.0038 Kg (Kılıçkan and Güner, 2008, pp.225, Table 1).
- 72 Compare the grinding of wheat, which requires much more energy, about 22 to 37 Κjoule/Kg and the energy consumed by a horizontal water mill per workday was estimated at 75.10 MJoule (Holdsworth et al. 2015). Of course a Kg of wheat (a hard seed) contains many more grains than a Kg of olives. A wheat grinding mill, typically powered by wind or water energy source, also rotates at a far greater speed than the olive mill (80-170 revolutions per minute, or max.17,80 rad/sec, Holdsworth et al., 2015).
- 73 Tyree and Stefanoudaki, 1996, pp.171-178; Tyree and Stefanoudaki, 1997.
- 74 Tyree and Stefanoudaki, 1997, p.262: "The constituency of the mix indicated that 1) at least half, but probably about three-fourths of the ftuits were pulled under the path of the crushing stones causing the entire fruit to be crushed and 2) that the remaining fruits, surprisingly, were forced aside, stripping the flesh but leaving the pits intact."
- 75 This specific mill employed a pair of 1.70m diameter and 0,40m thickness wheels, revolving on a granite basis. (Tyree and Stefanoudaki, 1997, p.61).
- 76 As a ratio of Fcompressive to the contact surface between wheel and base.
- 77 The stone wheel tends to push the olive fruits aside, so constant attention is needed to push them back under its path. See: Parharidis, 2006, p.295; Sordinas, 1971, pp.9-10. Υong et al., 1984 give an idea of such parameters that blend into the model (1984, p.243, Chart 8.23; Chart 7.43).
- 78 Parharidis, 2006, p.295.
- 79 Observe that if n is the mechanical efficiency factor, then (Wanimal − Winitiation − Wparasitic) = Wuseful = (Wanimal × n) = P×t×n
- 80 See for example the limit of 500-600 ottoman kiyye (around 640-768 Kg) of olive fruit per 24 hours, ground in 10 shifts at a four-wheeled, 19th century olive mill (Stavroulakis, 1984, pp.233-239). Parharidis, 2006, p.300 estimates a quantity of 1,700-2,000 kiyye (2,175-2,560 Kg) for a four-wheeled mill with an advanced feed mechanism during a 15-hour period, that is a maximum of 170 Kg of olive fruit per hour. Sordinas, 1971, p.31 cautiously mentions that in a shift, 450-465 lbs (205-209 Kg) of olive fruits were ground in two stages, lasting 5 to 6 hours in total. Frankel, Avitsur and Avalon, 1994, p.110 mentions 50-70 Kg per shift per hour (including breaks), or 400-600 Kg in 8 hours. The table provided by Doğan (2007, p.170) points to the difficulty of estimating such fluctuating quantities.
- 81 As a ratio of the value of the olive pulp to the value of human and animal labour.
- 82 In multiple-wheeled olive mills, every stone wheel runs on a different revolution radius. Each cylindrical wheel also has a different diameter. The olive fruit displaced by the inner wheel is pushed to the middle one and then to the outer, covering a spiral path from the centre to the rim of the base (Parharidis, 2006, describing a four-wheeled machine that had a special feed mechanism above). 20th century mechanized pairs of stone wheels used to rotate in a deep conical metal cup which prevented unwanted displacement of the olive fruits.
Bibliography
Physics and Kinematics
Baltz, E. A. and Strovink, M. 1998. Solution to Problem Set 7 (by K.&Κ.) Physics H7A Mechanics and Vibrations [online] University of California, Berkeley. Available at: < www.6911norfolk.com /d0lbln /h7af98 /h7af98-psoln7.pdf >, accessed January 2017].
Halliday, D., Resnick, R. and Walker, J., 1993. Fundamentals of Physics. 4th ed. New York: John Wiley & Sons [1st ed. 1974].
Holdsworth, L. J., Spender, E. I., Bentley, A. L. and Fogg, A. R., 2015. The [Mill] Power of Norman England. Journal of Physics Special Topic 14/1 (2015), pp. P1-4.
Kılıçkan, A. and Güner, M. 2008. Physical properties and mechanical behavior of olive fruits (Olea europaea L.) under compression loading. Journal of Food Engineering 87 (2), pp. 222–228.
Kleppner, D. and Kolenkow, R. 2010. An Ιntroduction to Μechanics. Cambridge: Cambridge University Press, p. 335, problem 7.4 [in the 2014 edition it is numbered problem 8.4 (Grain Mill), p.337 ].
Koetsier, T. 2012. The Case of Kinematics, the Genesis of a Discipline. In: T. Koetsier and M. Ceccarelli, eds. Explorations in the History of Machines and Mechanisms: Proceedings of HMM2012, History of Mechanism and Machine Science 15. Dordrecht: Springer, pp. 491-505.
Lippert, D. and Spektor, J. 2013. Rolling Resistance & Industrial Wheels. Hamilton White Paper Νο 11. [online] Hamilton, OH: Hamilton Caster & Mgf. Co. Available at < www.hamiltoncaster.com/Portals/0/blog/White Paper Rolling Resistance.pdf > [accessed December 2016].
Montes Tubío, Francisco de P., Burgos Ladrón de Guevara, E. and Carranza Cañadas, M. del P. 1998. Consideraciones Geométricas sobre los molederos de aceitunas clásicos. Actas del X Congreso Internacional de Ingeniería Gráfica: La expresión Gráfica, nuevas Dimensiones (INGEGRAF X, Málaga 3-5 June 1998). Málaga: Universidad de Málaga, Departamento de Expresión Gráfica, Diseño y Proyectos, pp. 157-165.
Myszka, David H., 2012. Machines and Mechanisms: Applied Kinematic Analysis, 4th ed. Boston: Prentice Hall [1st ed.1999].
Norton, R. L., 2004. Design of Machinery: An Introduction to the Synthesis and Analysis of Mechanisms and Machines, 3th ed. New York: McGraw-Hill.
Phillips, J., 2006. Freedom in Machinery, Vol. I. 2nd ed. Cambridge: Cambridge University Press [1st ed. 1984].
Rouleaux, F. 1876. Kinematics of Machinery: Outlines of a Theory of Machines. Translated from German by Α. Kennedy. London: Macmillan and Co.
Shigley, J. E. and Uicker, J. J. 1981. Theory of Machines and Mechanisms. Auckland et al.: McGraw-Hill.
Animal Power
Boie, Wulf, 1996. Introduction of Animal Powered Cereal Mills. Deutsche Gesellschaft für Technische Zusammenarbeit. Available at www.nzdl.org [Accessed Jan. 2017].
Eideneier, H., ed., 2016. Tale of four-footed Beasts & Tale of Birds. Ηerakleion: Crete University Press [Διήγησις των Τετραπόδων Ζώων & Πουλολόγος].
Falvey, J. L., 1988. An Introduction to Working Animals. Melbourne: MPW Australia.
Goe, M. R., McDowell, Robert E., 1980. Animal Traction: Guidelines for Utilization. Ithaca: Cornell University, Department of Animal Science.
Archaeology and History of Technology
These works focus mainly on the Eastern Mediterranean, but contain useful bibliography on a series of special issues.
Camps-Fabrer, H., 2000. Huile. Encyclopédie Berbère, Volume 23. Leuven: Peeters Publishers, pp.3521-3553.
Frankel, R., 1993. Τhe Trapetum and the mola olearia. In: Μ.C. Amouretti and J.P. Brun, eds. La production du vin et de l'huil en Meditérraneé. Βulletin de Correspondance Hellénique: Supplément 26. Athens: École Française d' Athènes, pp. 477-480.
Frankel, R., Avitsur, S., Ayalon, E., 1993. History and Technology of Olive Oil in the Holy Land. Arlington, VA: Oléarius. Tel Aviv: Eretz Israel Museum.
Forbes, R.J., 1965. Studies in Ancient Technology. Volume 2. Leiden: E. J. Brill.
Hadjisavvas, S., 1992. Olive Oil Processing in Cyprus: From the Bronze Age to the Byzantine Period. Nicosia: Paul Aströms Förlag.
Hadjisavvas, S., 2005. Olive Tree and Olive Oil in the ancient Greek World. Athens: Pireus Bank Group Cultural Foundation [Xατζησάββας, Σ. 2005. Η ελιά και το λάδι στον αρχαίο ελληνικό κόσμο. Αθήνα: Πολιτιστικό Ίδρυμα Ομίλου Πειραιώς.]
Mattingly, D. 1993. Maximum figures and maximizing strategies of oil production? Further Thoughts on the Processing Capacity of Roman Olive Presses. In: Μ.C. Amouretti and J.P. Brunö eds. La production du vin et de l'huil en Meditérraneé. Βulletin de Correspondance Hellénique: Supplément 26. Athens: École Française d' Athènes, pp. 483-498.
Mazzotti, Μ., 2004. Εnlightened Mills: Mechanizing Olive Oil Production in Mediterranean Europe. Technology and Culture 45 (2004), pp. 277-304.
Pikoulas, Y., 2006. Olive Oil Production Technology in Ancient Greece: An Interim Report. In: A.Polymerou-Kamilakis, ed. Ode to the Olive Tree. Athens: Academy of Athens-Hellenic Folklore Research Centre-Hellenic Ministry of Culture-Archaeological Receipts Fund, pp. 284-293.
Runnels, C. N., 1981. A Diachronic Study and Economic Analysis of Millstones from the Argolid, Greece. Ph.D Bloomington, Indiana University.
Tyree, L. and Stefanoudaki, E., 1996. The Olive Pit and Roman Oil Making. The Biblical Archaeologist 59/3 (1996), pp. 171-178.
Tyree, L. and Stefanoudaki, E., 1997. Τhere is more than one way to crush an olive: Does the pit affect flavor?. In: C.Gillis, Ch.Risberg, B.Sjöberg, eds. Trade and Production in Premonetary Greece: Production and the Craftsman. Jonsered: P.Åström, pp. 257-274.
Olive Production in early modern Greece
The content of some of the works cited here is unfortunately uncomprehensible to most of the readers, yet they contain plenty of specific information and bibliography, mostly focusing on Crete. They usually provide an abstract in English.
[Anonymous], 1968. «Gourna. A new village in Egypt», Architecture & Review of Greek
Αk, S.A., 2004. Fotoğraf ve Kartpostallarıyla Girit'ten İstanbul'a Bahaettin Rahmi Bediz. Beyaz atlı fotoğrafçı, 1875-1951. İstanbul: İletişim Yayınları.
Doğan, F., 2007. Osmanlı Devleti΄nde Zeytinyağı (1800-1920). Ph.D İstanbul Marmara Üniversitesi [Olive Oil in the Ottoman State (1800-1920)].
Κatsarakis, Α., 1996. A fortified Olive Mill in Maroulas, Crete. In: Proceedings of the Three-Day Working Meeting on “Olives and Olive Oil”, Kalamata, 7-9 May 1993. Athens: Pireus Bank Group Cultural Foundation [Kατσαράκης, A. Oχυρωμένο ελαιοτριβείο της Ενετοκρατίας στο Μαρουλά Ρεθύμνου. Ελιά και Λάδι - Τριήμερο Εργασίας. Αθήνα: Πολιτιστικό Ίδρυμα ΕΤΒΑ, pp. 303-323].
Parharidis, S. 2006. The Construction and Working of Olive Presses. In: A. Polymerou-Kamilakis, ed., Ode to the Olive Tree. Athens: Academy of Athens-Hellenic Folklore Research Centre, pp. 294-301.
Sordinas, Α., 1971. Old Olive Mills and Presses on the Island of Corfu, Greece: An Essay on Industrial Archaeology and the Ethnography of Agricultural Implements. Mephis State University Anthropological Research Center Occasional Papers 5. Memphis: Mephis State University.
Stallsmith, A. B., 2007. One Colony, Two Mother Cities: Cretan Agriculture under Venetian and Ottoman Rule. In: Between Venice and Istanbul: Colonial Landscapes in Early Modern Greece, Hesperia Supplements Vol. 40, pp. 151-171.
Stavroulakis, Α. S., 1984. Stavroulakis, Andreas S., 1984. The olive mill before the olive factory, Promithefs Pyrforos 39, Rethymnon 1984 [Σταυρουλάκης, Α. Σ., 1984. Το αλετριγουδιό πριν από το ελαιουργείο. Προμηθεύς ο Πυρφόρος 39, pp. 233-239.]
Zivas, D. A., 2000. Pre-industrial agricultural facilities on Zakynthos. Athens: Pireus Bank Group Cultural Foundation [Ζήβας, Δ. Α., 2000. Προβιομηχανικές αγροτικές εγκαταστάσεις στη Ζάκυνθο. Aθήνα: Πολιτιστικό Τεχνολογικό Ίδρυμα ΕΤΒΑ].