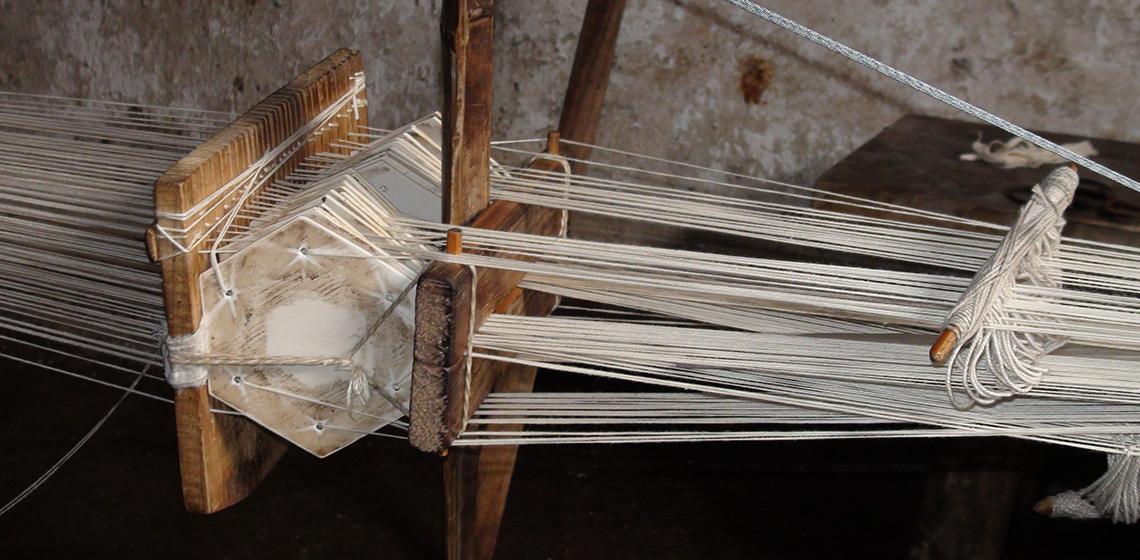
The remote mountain area of Guizhou in southwest China is ethnically diverse, and interesting textile traditions survive among the groups. Perhaps the best known are the multicoloured costumes of the Miao people that are skilfully decorated with embroidery and braids (Smith, 2007). Another ethnic group are the "Lao Han" (the ancient Han Chinese) who consider themselves unique from the rest of the majority Han population of China as a whole. They have lived in the Guizhou region since at least the 14th century CE when they were sent there as soldiers on military campaigns. Many stayed and took minority women as wives and formed separate communities. They are also known as the Chuanlan (Blue Dressed people) and are among the many ethnic groups in Guizhou province not officially recognised (Wikipedia, 2020; Joshua Project, 2020). Traditional costume has survived in the isolated Lao Han villages, especially amongst the women. Part of their costume includes a very long handwoven belt that incorporates two different weaving techniques on the same warp and is finished with a complex knotted tassel at each end. The belt begins and ends with a tube that is woven in a tabby weave, whereas the middle section has one or two textured areas that are achieved by using hexagonal weaving tablets in an unusual way.
The renowned weaver Peter Collingwood briefly mentioned such belts in his book The Techniques of Tablet Weaving (Collingwood, 1982, pp.219-220). Not long before he died in 2008, he contributed a couple of pages on these belts to the book Minority Textile Techniques: Costumes from South-West China (Collingwood, 2007, pp.28-29).
Collingwood found Lao Han belts to be technically of great interest. “For most of its length it is a flattened tube of simple plain weave, but this is twice interrupted by patterned, one-layered areas requiring the use of six-sided tablets; these two techniques seem almost impossible to combine” (Collingwood, 2007). Tabby (plain) weave is achievable using four-sided tablets but not hexagonal ones.
To an experimental practitioner such as myself, this was extremely intriguing and demanded further investigation. However, the purpose of this research was not only to understand for myself how the belts may have been created, but also to document some of the processes involved for the benefit of others.
Description of the belts
Detailed information about the structure of the belts was gathered from three main sources. The National Museums Liverpool have an example in their stored collection (accession number LIV.2010.118.92) that I was fortunate to study. I subsequently sourced one to purchase from Martin Conlan of ‘Slow Loris’ (UK), see Figure 1. Finally, I learned that Dominique Brocade from France had been on a textile tour to the Guizhou region and had some photographs and videos of such a band being woven. Dominique has generously given me full access to them.
The band I own has the following characteristics:
Colour: | The band is black throughout, although now faded in places. |
Length: | The band is 402 cm long. In addition, each end has a long, knotted tassel that is separate from, but attached to, the band; each is 50 cm long and made with a silk-like yarn. |
Width: | The band is 6.5 cm wide in the tabby areas and 6.6 -7 cm wide in the twined patterned areas. It is just 6 cm wide where it disappears under the tassel. |
Weave/construction: | The band starts with a plain weave tube 77 cm long, with a small simple pattern area beginning at the tassel end; following next is a tablet woven area, 61 cm long, with several geometric patterns (with a reversal point in the middle); followed by another plain weave tube 123 cm long; then another tablet woven area, 64 cm long, with several geometric patterns (with a reversal point in the middle)1 . Finally, there is another plain weave tube 77 cm long, with a small simple pattern area at the tassel end. Figures 2, 3a and 3b illustrate these different areas in the purchased belt. |
Warp: | The warp thread is plied with an overall S-twist, used doubled, and is assumed to be cotton. In the tabby area there are 10.5 doubled ends per cm, and in the patterned area there are 3.5 to 4 elements of ‘twined cords’ per cm2 . The warp yarn is visually estimated to be approx. 2/16 to 2/20 cotton count. |
Weft: | The weft is much thicker than the warp, being made up of several strands, each of which has a Z-twist, with a Z-twist to the overall group of strands. Like the warp, it appears to be cotton. Individual weft threads appear finer than individual warp threads. The weft ends are generally joined by knotting. In the tabby area there are 6.25 picks per cm, in the patterned area there are just over 3 picks per cm. The weft appears to be the same throughout the band. |
The difference in thickness between the warp and the weft gives the tabby areas a ribbed effect. Both warp and weft are black, although some areas have faded to a dark grey.
The band from the Liverpool collection is similar although it has one entire block of tablet-woven geometric patterning rather than the two separated by an area of plain weave. It is woven with white cotton warp and weft, except for the tablet-woven area where the weft is a terracotta-coloured glossy yarn that appears to be silk. Collingwood (2007) states that the belts are woven in white thread and then dyed in indigo, which is consistent with the Liverpool belt being undyed.
Therefore, it is clear that both the tabby-weave tube and the hexagonal tablet-woven patterns are woven on the same warp, but how is this possible?
Weaving the tube
The Swiss ethnologist Volkart reported in 1907 that string heddles were used for the purpose of weaving the tube (Volkart, 1907). The relevant text says (my own translation from German):
“In Fraülein Lehmann-Filhés’s collection are also many very interesting Chinese belts that are only partly woven with six-sided tablets. The first part, for example (normally figures or letters) is woven with tablets, then all these are pushed to the end of the warp. Then the warp threads are spread out and every one fixed to a small stick that corresponds to the shafts on our looms. Through variable lifts of 1, 2 or 3 loop rods a tube is woven, in which there is often in the middle a piece left open at one edge; this open part forms a pocket in the finished belt. When the planned piece woven with the loops is complete, the loops are pulled out and the tablets are again moved nearer (the weaver) and he weaves with the tablets without interruption, as at the beginning. “
Collingwood (2007) states that modern eye-witness accounts mention only two sets of heddles, which he rightly found puzzling because two sheds are needed to weave the top layer of the tube and two the bottom layer3 .
Images taken by Dominique Brocade explain how the weaving is set up. The entire warp, threaded through hexagonal tablets and then a spreader, is stretched out under tension across a room. The weaver sits to one side of the warp and moves along it as the band is woven. The warp threads nearest the weaver are passed either over, through or below a piece of slotted wood, with one quarter of the warp above, one half in the centre and one quarter below (See Figure 4). This provides 2 natural sheds. The centre threads are then connected to string heddles, one half of them to allow a second upper shed, and the remaining half to form the second lower shed (See Figure 5). The two vertical sticks in Figure 4 relate to the making of the tassel, so are not part of process for weaving the tabby tube. Figure 6 is a representation of how the warp threads may be allocated to the relevant positions.
The simple but effective patterning at the tassel ends of the tube (See Figure 7) is most likely woven with pick-up sticks, which is a technique practised by the Miao people (Torimaru, 2006, pp.78-93).
Tablet weaving the patterned areas
Tablet woven bands are generally warp-faced with the weft visible only at the edges. In contrast, the thick weft in Lao Han belts forms a key part of the patterning4 . Therefore, rather than being crammed as close as possible, the warp threads need to be spaced out, as shown in Figure 4.
The process of tablet weaving produces a warp-twined structure if the tablets are turned continuously in one direction or the other. This shows up on the surface as a corded structure that is parallel to the edges of the band. Such cords can be seen in Figure 3b; the thick weft makes them particularly visible. The angle of the threads within a cord depends upon the way that the tablets are threaded (so-called S or Z) and the direction of turning. In the case of these belts, the tablets are threaded S and Z alternately, so that the threads within adjacent cords run at opposite angles.
Collingwood stated that the tablets are used so that they form 2 natural sheds; a weft can be passed through the top shed and back through the bottom shed so that a substantial fabric is formed. All of the tablets can then be given a sixth turn in one direction, so gradually forming a 6-ply cord, each ply being held in place with a weft thread. “In the tablet-woven sections of the belt, 26 such cords are visible, running down the length of the band. So, 26 tablets were employed, which implies that the total thread count was 26 x 6 = 156” (Collingwood, 2007). This was confirmed when he counted the threads in the tubular section.
Figure 8 illustrates this process diagrammatically. The blue lines represent the warp threads; the orange circles represent the weft, which passes through the top shed, turns at the selvedge and returns through the bottom shed. The combination of a thick weft, and two passes of the weft in one move, creates a very sturdy band.
The thick weft is also a crucial factor in the production of motifs within the tablet-woven areas5 . Collingwood (2007) describes the motifs as being formed by 2 turns backwards, then two turns forwards which had ‘the unexpected effect of making the warp threads group into tight bunches of four, between which the thick weft bulged out visibly.’ Figure 9 shows part of the belt where plain tube (right) meets a patterned area; the overall pattern consists of simple continuous cords with occasional spot designs. As mentioned above, each turn is one sixth of a complete turn i.e. 60 degrees.
As an experienced tablet-weaver, I have conducted experiments that have revealed that the tablets are in fact turned three times forwards or backwards in blocks using the sequence summarised in Figure 10.
The triple turns are what draws the threads together to form the bars in the motifs that lie at right angles to the corded effect produced by continuous turning. The sequence of triple turns one way, then the other, stops the build-up of twist in the unwoven warp.
Figure 11 shows examples of 2 different motifs that show up against the background continuous turning. The edge tablets are turned continuously in one direction to form cords.
When tablets are turned continuously to form a corded weave, an equal amount of twist builds up on the far side of the tablets, in the unwoven warp. To eliminate this build-up, the direction of the turning needs to be reversed periodically. Such reversal points are characteristic of this type of tablet-weaving, and one can be seen in Figure 11 (right) where it has been incorporated into a geometric pattern. At the reversal point, the tablets are turned in the opposite way to their previous direction, which causes two surface threads to float parallel to the selvedge rather than being angled.
I wove my experimental samples using cotton warp and weft of different colours (pink and blue respectively) so that the motifs were readily visible against the background corded effect (See Figures 12 and 13). Therefore, a reversal point can perhaps be more clearly seen in Figure 12a, as can the change in the positions of the cords. On one side of the reversal (left), ten evenly spaced pairs form across the band. After the reversal (right) the cords form nine pairs, but with one additional single cord at each selvedge (there are 20 tablets in this experimental band). Exactly the opposite happens on the reverse face (See Figure 12b).
Selective triple turns forwards or backwards, as depicted in Figure 10, can create interesting designs. Particularly effective is a motif that I call “noughts and crosses”. Figures 13a and 13b show both faces of one such motif. The “noughts” appear on one face, the “crosses” on the other.
In the bands, various motifs are mirror-images of each other on either side of the reversal point so that at the completion of a tablet-woven section, all twist build up has been eliminated. Thus, new string heddles can be tied on and the plain weave tube recommenced. The join between the two areas is neat and does not disrupt the continuity of the band.
The knotted tassel
Each tassel consists of hundreds of twisted loops that are incorporated in rows near the beginning and end of the band as it is being woven.
The stages of the process of creating these twisted loops can be pieced together from video filming taken by Dominique Brocade.
In Dominique’s video, the weaver apparently starts by weaving a short length of tabby while the warp is attached to a stick or other such implement (the loops are visible), then stitches the end of the warp to a pre-woven length of tube, probably part of an old belt, then removes the stick. A thin metal rod has then been pushed through the old belt about 45 cm from the attachment point. The rod is at right angles to the length with each end protruding out about 4 cm. Then a length of tube continues to be woven on the new warp for a few more centimetres.
The first row of yarn for the tassel is then inserted. The yarn for the tassels is quite highly over-spun and so needs to be kept under tension during manipulation. The loops are made by passing the yarn through the warp shed instead of a weft, then pulling the yarn from between the warp threads and securing the loop on the metal rod, which holds the loops under tension. This is repeated so there are two to four rows of loops in the same shed. Because of the highly twisted nature of the yarn, when the tension is released, it naturally countertwists to form closed loops that cannot fray.
This process is summarised in an experimental setting in Figures 14 and 15.
Dominique's photos are helpful here: Figure 5 shows some of the loops (greyish yarn) being held under tension on the right of the picture. Figure 4 shows how these loops are held under tension after being manipulated. Groups of loops are then temporarily secured together, so they do not interfere with the weaving process.
There are typically several lines of loops created, as shown in Figure 16.
Once the weaving has been completed and taken off the loom, the loops are knotted together to form a decorative covering for the end of the band (See Figure 17).
The loops in rows D to H of Figure 16 are simply knotted once to their adjacent neighbours, and the loops allowed to hang freely. Those loops in rows B are knotted until reaching point C (forming an inner layer), then the loops in row A are knotted to cover the inner layer, but remain separate from it (forming the outer layer) (See Figure 18).
The knot used for the inner and outer layers is a variation of half-hitching (also called needle hitching) and depicted in Figure 19 (Emery, 1994, pp.34-37; Ashley, 1988, p.561). Each knot is a half hitch with a single working element knotted around 2 parallel passive elements, thus there are three elements per unit; A, B and C (from left to right). For the first row in the diagram, C is the working element. Once a row of such knots has been worked, the units move one element to the left, so the new unit is formed of C from the left adjacent unit and A and B of the original unit. For this row, B becomes the active element. Therefore, the knotting proceeds in a diagonal manner. Figure 20 shows the knotting on an experimental piece. It produced a structure that is not only visually like the original but has a similar rigidity and robustness.
Discussion
Volkart (1907) reported that the tablet-woven sections of the belts he had seen were patterned with “normally figures or letters” whereas the belts that I have studied have geometric patterns. The description of figures or letters is more in keeping with those found on the sazigyos (manuscript binding tapes) of Myanmar, which have been described in detail by Issacs (2014). These, however, are woven as a warp-faced weave with square (4-thread) tablets. The Liverpool belt is in pristine condition, undyed, and apparently unused and modern, while mine was estimated by the seller to be 70 to 80 years old. It would be very interesting to source belts known to be older, in other museum collections, in order to compare their motifs.
Likewise, Volkart (1907) mentions that a piece of the belt was left open at one edge to form a pocket. Neither of the examples that I have studied have this feature. This perhaps reflects a move away from a partly functional, to the purely decorative, use of the belts, although it equally could be that it represents the tradition of a particular village, or even weaver.
Therefore, this has been a preliminary study of these unique belts and I hope to investigate them further.
Acknowledgements
I would like to thank Dominique Brocade for making her photographs and videos so freely available to me and allowing me to share them in this publication. She describes herself as “just a traveller who loves braids”. Thanks also go to National Museums Liverpool for allowing me access to study the Lao Han belt in their collection.
- 1See the tablet weaving section for an explanation of reversal points.
- 2See the tablet weaving section for an explanation of the corded effect.
- 3A shed is the gap between 2 sets of warp threads through which a weft is passed.
- 4Patterns or patterning is the overall effect produced by the combination of motifs and background cords.
- 5Selective turning of the tablets produces individual motifs that show up against the background cords. The individual motifs are described here by appearance e.g. spot designs, noughts, crosses.
Bibliography
Ashley, C.W., 1988. The Ashley Book of Knots. London: Faber and Faber.
Collingwood, P. 2007. Tablet Weaving. In: Smith, R. ed., 2007. Minority Textile Techniques: Costumes from South-West China. Sussex, UK: Occidor Ltd. pp 28-29.
Collingwood, P. 1982. The Techniques of Tablet Weaving. London: Faber and Faber.
Emery, I., 1994. The Primary structure of fabrics: an illustrated classification. London: Thames and Hudson.
Issacs, R., 2014. Sazigyo. Woven miniatures of Buddhist Art. Thailand: Silkworm books.
Joshua Project, 2020. [online]. Available at: < https://joshuaproject.net/people_groups/18430/CH > [Accessed: 19June.2020].
Smith, R. ed., 2007. Minority Textile Techniques: Costumes from South-West China. Sussex, UK: Occidor Ltd.
Torimaru, S. 2006. Spiritual Fabric, 20 years of textile research among the Miao people of Guizhou, China. Japan: The Nishnippon Newspaper Co.
Volkart, H. 1907. Die Brettchen- und Kammweberei. Mitteilungen der Geographischen Commerciellen Gesellschaft der Ostschweiz in Sankt Gallen, Vol 1, pp 1-18.
Wikipedia, 2020. [online]. Available at: < https://en.wikipedia.org/wiki/List_of_unrecognized_ethnic_groups_of_Guizhou > [Accessed: 19 June 2020].