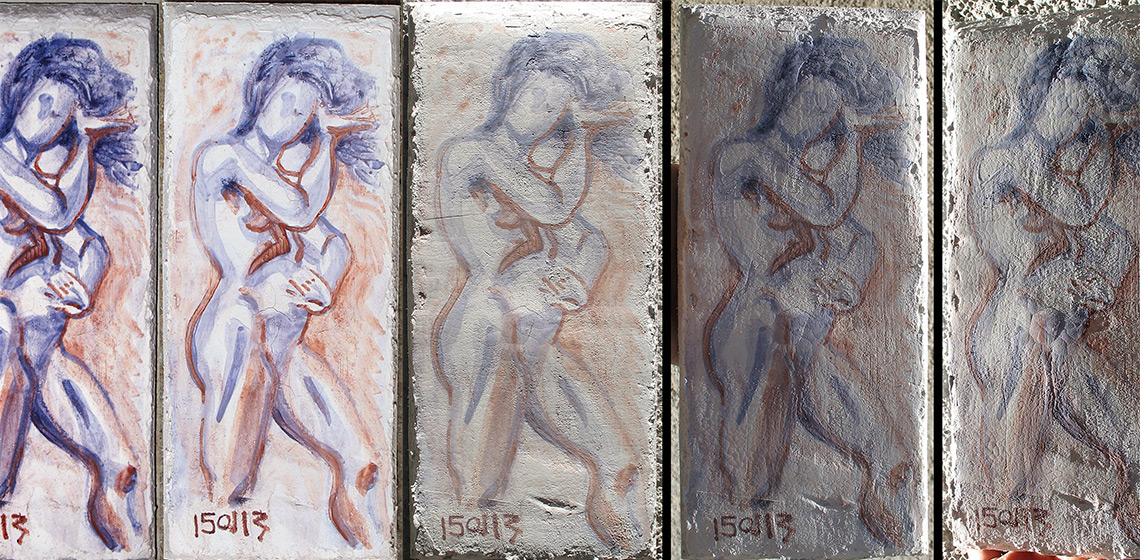
During the Bronze Age, craftspeople of the eastern Mediterranean reused fragments of mortars as aggregates in lime mixtures. In the 1970s, Mark Cameron experimented with the techniques of Minoan fresco preparing and painting. His experiments showed that it is possible to create mortar by mixing lime plaster with dried powdered lime plaster, and by mixing dried powdered lime plaster with water. These mixtures became the basis for the experiments presented in this paper. Fragments of mortar can be used as aggregates in a lime mortar, but only as a small part of the aggregates of a mixture. Mixing dried powdered lime or crushed thin shards of mortars with water produces granular pastes, which can be spread and painted. This technique can be used to recycle mixtures in order to practice spreading mortar, but not to create works that will stand the test of time. Dried lime plaster can be used as an aggregate in mixtures, including those used in fresco. The material behaves better when it is used in a powdered form. Analyses of the mortars of ancient frescoes must be exhaustive and take into account the fact that ancient craftspeople might have used unusual techniques.
1. Examine Cameron’s experiments.
2. Study the technology and the behaviour of these unusual mixtures.
3. Study the use of these mixtures in fresco techniques.
4. Study a form of ancient technology.
Introduction
During the Bronze Age, the craftspeople of the eastern Mediterranean practiced a form of reuse or recycling: fragments of mortar were used as aggregates in lime mixtures intended for walls or floors (Shaw, 1973, p.222; Brysbaert, 2003, pp.168-173, pp.175-176; Jones, 2005, p.220; Brysbaert, 2008, p.118). Such a mixture was found in a house in the Akrotiri settlement of Santorini, in a part of the wall that was intended to be painted (Jones, 2005, p.220). Piles of fragments of mortars - including fragments of wall paintings - have been found in different Bronze Age locations in Greece (Brysbaert, 2003, p.170; Jones, 2005, p.220). This form of recycling or reuse shows that the craftspeople were aware that these fragments were compatible with lime plaster (Brysbaert, 2003, pp.169, 172). During later periods, as was reported by authors discussing fresco techniques, fragments of old mortar were used to produce a type of lime white pigment. This practice has been identified in the frescoes of the 16th century church of Voronet in Romania (Dionysius of Fourna, 173?, p.14; Kondoglou, 1993, p.62; Istudor, 2008, p.31, note 9).
In the beginning of the 20th Century, Heaton studied the composition of the wall and floor mortars of the Palace of Tyrins. His analyses on the frescoes’ mortars showed that the first layer consisted of a mixture of 1 part lime with roughly 1 part pulverized limestone. The second 2 mm-thick layer consisted of plain lime (Heaton, 1912, pp.211-212, pp.214-216; Cameron, Jones and Philippakis, 1977, p.149; Jones, 2005, pp.208, 220). This mortar was the one that Mark Cameron wanted to study in his experiments. Cameron’s experiments took place in 1976 at the University of Western Ontario in Canada (Cameron, Jones and Philippakis, 1977, p.166; Chryssikopoulou, et al., 2000, p.119; Jones, 2005, pp.208, 220; Brysbaert, 2008, p.69). His research is very important in the study of Bronze Age wall painting techniques, but it was never fully published. The most analytical publication of his research to date is Jones (2005, pp.220, 221, Figure 13.4; see also Brysbaert, 2008, p.69). His experiments and notes are kept at the Cameron Archive of the British school of Archaeology in Athens. In his experiments, Cameron showed that it is possible to create a mortar by mixing 1 part lime plaster to 1 part dried powdered lime plaster or dried powdered lime plaster that had been baked. His experiments also proved that it is possible to create a mortar by mixing dried powdered lime plaster with water (Jones, 2005, pp.220, 221, Figure13.4).
We tried the mixtures mentioned above in a small number of experiments and this paper presents the results1 . These experiments were conducted to:
- Examine Cameron’s experiments.
- Study the technology and the behaviour of these unusual mixtures.
- Study the use of these mixtures in fresco techniques.
- Study a form of ancient technology.
Materials and Methods
The equipment (for example trowels and paintbrushes) and materials (lime and aggregates) used in the experimental samples existed during the time period explored. The only material that did not exist is the extruded polystyrene (XPS), a modern insulation material that was the base for the samples. It was chosen because it does not react with lime, and it is not affected by the alkalinity of the mixtures. Its surface was scored to improve its mechanical cohesion with the lime mixtures. In most cases a mixture was placed over the polystyrene which acted as a base for the layers placed over it.
In all of the samples we used lime plaster that did not contain magnesium or gypsum. The plaster was created from the calcining of a dark marble by a local producer in Crete, Greece. Before using it for the samples it was sieved without dilution with a thin net to remove any impurities.
To prepare the dried lime for the samples we took a quantity of that lime and left it in an open container to dry for a month. It was then left in an open container to dry for a month (See Figure 1). When it was half dry it was crumbled to smaller pieces to accelerate its drying. The dry pieces were ground into powder and mixed with water to form a paste. When the paste settled the water was removed and the plaster was left to dry again. The final stage of preparation was to grind the dried lime into pieces of different sizes, from powder to medium sand. The preparation of the dried lime was based on the methods for lime white production described in artist manuals (Cennini, n.d., p.34; Taylor, 1843, p.43; Thomas, 1869, pp.38, 40; Laurie, 1910, p.123; Thompson, 1956, p.97; Seymour, 2003, pp.449, 451).
The fragments of mortars we used came from breaking older samples with mixtures that contained sand and/or marble chips of various sizes. Some of the fragments that were used were the dried leftovers of various mixtures that were kept for this series of experiments (See Figure 2).
All of the materials were measured by volume, using the same shovel. In each mixture the aggregates were measured first, and then the lime was measured and added. The sizes of the mentioned aggregates are based on the following categorisation:
Thick | Ø 5 mm - 1,1 cm |
Medium to thick | Ø 4-5 mm |
Medium | Ø 4 mm |
Thin to medium | Ø 1-3 mm |
Thin | Ø up to 0.5 to 0.75 of a mm |
Experiments
The samples mentioned in this paper are presented in detail in Table 1. The number of each sample refers to the date of its creation. The name of the majority of the samples refers to the subject painted on it. In the description of the samples we differentiate between layers and doses. When we mention a layer we mean that it was produced by a single spreading of one mixture. When we mention doses we mean that a single mixture was spread at intervals. The application in doses allows the spreading of a thin mixture in a thicker layer than what it would normally withstand.
Since the focus was on the application of fresco techniques, all of the samples were painted in order to behave like a normal fresco. When we refer to painting in fresco we mean that they were painted within 30 minutes from spreading or levelling the mortar, with the pigments mixed with water, lime water or milk of lime. The binder for all the pigments used in this series of experiments was water. In contrast to Cameron’s experiments in Canada, this series of experiments took place in Chania, Crete where the climate is closer to that of the period during which the ancient frescoes were created.
All of the observations on the samples were made using the senses and not with specialised laboratory equipment. A more detailed analysis of such samples would be useful in the future to study the characteristics of these mixtures.
Mixtures of lime and recycling practices
We undertook a small number of experiments with mixtures that contained a small quantity of fragments of mortar (1/3rd-1/6th of the mixture). These quantities proved enough to influence its behaviour: the lime mortar produced dried faster than a mixture of lime and sand because the fragments absorbed part of the humidity of the fresh lime. When we wetted the dry samples we observed that absorbed a bit more water than normal mixtures of lime and sand did. All of the mixtures with fragments of mortar were used as base coats for other lime mixtures that were painted (See samples 15713 Abduction; 15713 Roman Venus; 2813 Palmette Persephone; 5514 Aineia Lily; 5714 Lily; 25714 Pluto; 26814 Palmette). The surfaces of the base coats were sanded to improve their mechanical adhesion to the top coats. The mixtures placed above them did not develop cracks or other forms of damage that can be attributed to the basecoats (See Figure 3). Fragments of mortar can be used as aggregates in a lime mortar, but it is better if they are a small part of a mixture and not the sole aggregate.
Mixtures of lime and dried lime
Sample 150113 Female Figure was our first attempt to make a mixture of lime plaster and dried powdered lime. The ratio of materials was 1 lime : 1 dried lime plaster crushed in thin and medium sand-sized pieces. The mixture was placed in one 6 mm thick layer, over a wetted base coat of lime and sand (See Figure 4). When it dried the layer was full of thin cracks, the majority of which were very shallow. The pigments were used in various states of dilution (including excessive dilution) and adhered well to the mixture (See Figure 5).
The experiments that followed were made with powdered lime plaster used in different ratios (See Figure 6). A ratio of 1 lime plaster : 2 dried powdered lime plaster produces a mixture that is very tight. The ratio of 1 lime plaster : 1-1,5 dried powdered lime plaster is more appropriate, especially in cases where the mixture is spread in a single layer (See samples 5613 Lily; 18813 Griffin; 12913 Persephone; 15714 Pluto; 20714 Lachesis). Mixtures with a ratio of 1:1 are generally more stable and can also be compressed after spreading. Powdered dried lime plaster cannot be used with a ratio smaller than 1:1, as was observed in sample 6613 Egg & Dart (ratio 1:0,5, see Figure 7. See samples 2513 Alavastron; 5613 Lily; 6613 Egg & Dart; 18813 Griffin; 15714 Pluto).
We also tried a mixture ratio of 1 lime plaster : 1 dried powdered lime plaster : 1 chalk powder (See Figure 8). The creamy mixture behaved well and dried with a glossy surface texture (See samples 151113 Persephone; 22714 Hermes). Historically, powdered chalk has been used as a white pigment, as a filler in pigments, as a base for organic pigments, and in the preparation of painting grounds (Laurie, 1910, pp.24-25, 123, 254; Forbes, 1965, p.233; Gettens and Stout, 1966, p.103; Martin, 1986, pp.39, 92-93; Seymour, 2003, pp.94-95; Vlavogilakis, 2020, pp.790-793, 851-857, 895-898). As an aggregate in lime mortar, powdered chalk as a material, behaves in a way that is between marble powder and dried lime plaster powder. Powdered chalk produces a white mortar with yellowish hue (Vlavogilakis, 2020, pp.235-236; see Figure 9). We would not recommend it as an aggregate because materials such as marble dust and powdered limestone are widely available and more appropriate for fresco making.
These experiments prove that dried lime plaster can be used as an aggregate in mixtures, including those used in fresco. The material behaves better when it is used in very thin shards or –ideally- in a powdered form. When used in medium sand-sized pieces it behaves better than when it is part of the mixture and not the sole aggregate. Pigments adhere well to mixtures with powdered lime plaster. That is a characteristic that was somewhat expected: in fresco painting, lime whites also act as a binder to the pigments that they are mixed with (Laurie, 1926, p.199; Winfield, 1968, pp.109-110; Kay, 1983, p.186; Howard, 1995, p.96; Vlavogilakis, 2020, p.779). Mixtures of lime and dried lime plaster powder can be spread in doses that are placed at a maximum of 30-40 minutes apart. The time constraint is due to the fact that these mixtures tend to dry fast. The maximum number of doses that can be spread are four. As with most aspects of fresco techniques, the number of doses depends on the application (for example, over a wet or dry mixture or the type of mixture). It was also observed that such a mixture may be allowed to rest after mixing before spreading it on a surface, as is done with other lime mixtures (Cennini, n.d., p.42. See samples 080912 Lily; 5613 Persephone Face; 281013 Atropos; 10714 Abduction; 11613 Pluto Arm). The powdered lime absorbs part of the humidity from the fresh lime, which makes the mixture more pliable, gives it a better workability, and allows it to remain wet for longer. In contrast to fragments of mortar, the absorption of the humidity of the plaster does not diminish the properties of the resulting mixture (See samples 150113 Female Figure; 2513 Alavastron; 5613 Lily; 6613 Egg & Dart; 18813 Griffin; 151113 Persephone; 15714 Griffin; 15714 Pluto; 15714 Palmette; 20714 Lachesis; 20714 Okeanis; 22714 Hermes; 25714 Demeter; 26714 Pluto; 4814 Romaios lily; 211114 Demeter; Ω10a; Ω10b).
Mixtures of dried lime and water
In a small number of experiments we tried to create a mortar by mixing dried powdered lime with water (See Figure 10). A mixture of a ratio of 1 dried powdered lime:0,5 water was spread over a dry layer of lime and thin sand and was painted successfully five minutes later. When dried powdered lime plaster is mixed with water or lime water it produces a granular paste. That paste is sticky, tightens quickly and absorbs water. It also has a limited ability to absorb pigment. In such a mixture the quantity of water needs to be smaller than that of the dried lime. The technique produces a mortar that cannot withstand the test of time. We believe that this method can only be applied in a sample (See samples Ω10a and Ω10b, and Figures 11 and 12).
In two small experiments we tried using crushed shards from mortars that were composed of lime and thin sand. Instead of adding lime, we added water and kneaded the mix until it became a soft paste (See Figure 13). This mixture was spread over a dry base layer of lime and sand that had been wetted. The layer was left to settle for an hour before levelling the surface, and another 20 minutes before painting it. In sample Ω12 (See Figure 14) the mixture was composed of thinner shards and included powdered dried lime. The second sample, Ω12b (See Figure15), was made from larger shards and had a coarser surface texture. In both samples the thin layer produced was painted and dried without a problem. The pigments appeared to adhere well to the surface of both samples.
Both of the above techniques can be used to recycle mixtures in order to practice the fresco technique or to practice spreading mortar -as was frequently the case in our research. However, we would not recommend these methods for painting a fresco. The technique cannot be applied to a surface that is larger than a sample without the appearance of cracks and flaking when it dries.
Conclusions
In the analysis of ancient frescoes, it is necessary to bear in mind that the ancient craftspeople who created these works might have occasionally used unusual techniques. The analysis must, moreover, be exhaustive. This is important because as an aggregate dried lime plaster cannot be identified in the analyses by laboratory techniques because it has the same composition as the fresh lime plaster of the mixture. Lime on its own can only be spread in thin layers with a thickness up to 1 mm (Gettens and Stout, 1966, pp.238, 250; Kay, 1983, p.174; Jones, 2005, p.208; Goffer, 2007, p.149; Vlavogilakis, 2020, pp.396-399). By that we mean that a single spreading of undiluted lime, and not successive layers of diluted lime or milk of lime. Such a technique produces a layer that has a total layer thickness ranging from 0.2 mm to 1.2 mm when it dries (Vlavogilakis, 2020, pp.399-405). One is able to identify a mixture of lime and dried lime in analyses in observing a layer that is composed solely of lime, but has a thickness that is larger than 1,5 mm.
One must also consider that in experiments in fresco painting some techniques work on small samples but cannot be applied to large surfaces. Mixtures of lime and dried lime powder can be applied to large surfaces. We believe that these mixtures are possible, but we also believe that one needs to be careful when attributing techniques to findings. This paper hopes to shed more light into Bronze Age mortar technology and to give ideas for future avenues of experimental research.
Sample | Ratio of materials | Number of layers or doses | Thickness of layer or total thickness of doses | Placed over a base coat or is a base coat | Outcome |
150113 Female Figure | 1 lime : 1 dried lime (medium to thin sand-sized pieces) | 1 layer | 6 mm | Yes | Cracks |
2513 Alavastron | 1 lime : 0,5 dried lime (medium sand-sized pieces) | 1 layer | 1,5 mm | Yes | Cracks |
5613 Lily | 1 lime : 1,5 dried lime (medium sand-sized pieces) | 1 layer | 1,5 mm | Yes | Cracks |
6613 Egg & Dart | 1,5 lime : 2 thin sand : 1 dried lime (medium sand-sized pieces) | 1 layer | 4 mm | Base coat | Successful |
1 lime : 0,5 dried lime (powder) | 1 layer | 0,5 mm | Yes | Cracks | |
15713 Abduction | 1,5 lime : 1 thin sand : 1 Egyptian quartz (medium sand size) : 1/3 chopped goat hair : 1 fragments of mortars with thick medium and thin aggregates : 1/5 clay : 1/5 brick powder : 1/3 water | 1 layer | 5 mm | Base coat | Successful |
15713 Roman Venus | 1 lime : 1 thin sand : 1 Egyptian quartz (medium sand size) : 1/3 chopped goat hair : 1 fragments of mortars with thick medium and thin aggregates : 1/5 clay : 1/5 brick powder : 1/3 water | 1 layer | 5 mm | Base coat | Cracks |
2813 Palmette Persephone | 2 lime : 2 thin sand : 0,5 fragments of mortars with thick and medium aggregates : 1 Egyptian quartz (medium sand size) : 1 pumice (thick sand-size) : 1/4 brick powder : 0,5 clay : 1/4 water | 1 layer | 1,3 cm | Base coat | Cracks |
18813 Griffin | 1 lime : 1,3 dried lime (powder) : 1/5 water | 1 layer in 3 doses | 1,2 mm | Yes | Successful |
12913 Persephone | 1 lime : 1 dried lime (powder) : 1/3 water | 1 layer | 1,5 mm | Yes | Successful |
151113 Persephone | 1 lime : 1 dried lime (powder) : 1 chalk (powder) | 1 layer | 0,5 mm | Yes | Successful |
4314 Brysbaert 2 | 1 lime : 0,5 thin sand : 0,5 dried lime (powder) : 1 straw : 0,5 marble (powder) : 1 crushed seashell | 1 layer | 2 mm | Yes | Successful |
5514 Aineia Lily | 1 lime : 1 thin sand : 1 fragments of mortars with thin aggregates (thin and medium sand-sized pieces) | 1 layer | 1 cm | Base coat | Cracks |
5714 Lily | 1 lime : 1 thin sand : 1 fragments of mortars with thin aggregates | 1 layer | 9 mm | Base coat | Cracks |
15714 Pluto | 1 lime : 2 dried lime (powder) | 1 layer in 2 doses | 1 mm | Yes | Cracks |
20714 Atropos | 1 lime : 2 dried lime (powder) | 1 layer in 4 doses | 1,5 mm | Yes | Cracks |
20714 Lachesis | 1 lime : 2 dried lime (powder) | 1 layer in 2 doses | 0,8 mm | Yes | Cracks |
20714 Okeanis | 1 lime : 0,5 dried lime (powder) | 1 layer in 3 doses | 1,5 mm | Yes | Cracks |
22714 Hermes | 1 lime : 1 dried lime (powder) : 1 chalk (powder) | 1 layer | 1 mm | Yes | Successful |
25714 Demeter | 1 lime : 3 dried lime (powder) | 1 layer | 6 mm | Yes | Successful |
25714 Pluto | 1 lime : 1 thin sand : 0,5 Egyptian quartz (medium sand size) : 1 chopped goat hair : 1 fragments of mortars with thin aggregates : 1/4 pumice powder | 1 layer | 4 mm | Base coat | Cracks |
26814 Palmette | 1 lime : 1 thin sand : 0,5 Egyptian quartz (medium sand size) : 1 chopped goat hair : 1 fragments of mortars with thin aggregates : 1/4 pumice powder | 1 layer | 4 mm | Base coat | Successful |
Ω10a | 1 dried lime (powder) : 1 water | 1 layer | 1,5 mm | Yes | Cracks |
Ω10b | 1 dried lime (powder) : 0,5 water | 1 layer | 1,5 mm | Yes | Successful |
Ω12 | Wet fragments of mortars with thin sand (thin sand-sized pieces) | 1 layer | 1,5 mm | Yes | Successful |
Ω12b | Wet fragments of mortars with thin sand (thin sand-sized pieces) | 1 layer | 1,5 mm | Yes | Successful |
Table 1. The samples mentioned presented in detail.
- 1The experiments, samples and research findings presented here are described and illustrated in more detail in Vlavogilakis 2020. They are part of a PhD research that was conducted at the Department of Mediterranean Studies, University of the Aegean, Rhodes, under the supervision of Professor M. I. Stefanakis.
Bibliography
Brysbaert, A., 2003. Rotating angles in measuring the Aegean Bronze Age. The technology of Bronze Age painted plaster from the Aegean and the eastern Mediterranean. In: K.P. Foster and R. Laffineur, eds. METRON. Measuring the Aegean Bronze Age: Proceedings of the 9th International Aegean Conference, New Haven, Yale University, 18-21 April 2002. Aegaeum, 24. Liège: Universite de Liège, Histoire de l’art et archeologie de la Grece antique. pp.167-177.
Brysbaert, A., 2008. The power of technology in the Bronze Age eastern Mediterranean: The case of the painted plaster. Monographs in Mediterranean Archaeology, 12. London: Equinox.
Cameron, M.A.S., Jones, R.E. and Philippakis, S.E., 1977. Scientific analyses of Minoan fresco samples from Knossos. Annual of the British School at Athens, 72, pp.121-184.
Cennini, C., n.d. The craftsman's handbook. The Italian "Il Libro dell' Arte". Translated by D.V. Thompson, Jr., 1933. New York: Dover Publications, Inc. and Yale University Press.
Chryssikopoulou, E., Kilikoglou, V., Perdikatsis, V., Sotiropoulou, S., Birtacha, K. and Zacharioudakis, M., 2000. Making wall paintings: An attempt to reproduce the painting techniques of Bronze Age Thera. In: S. Sherrat, ed. The wall paintings of Thera: Proceedings of the First International Symposium, Petros M. Nomikos Conference Centre, Thera, Hellas, 30 August-4 September 1997. Volume 1. Athens: Petros M. Nomikos and The Thera Foundation. pp.119-129.
Dionysius of Fourna, 1729-1734. The painter's manual of Dionysius of Fourna. Translation and comments by P. Hetherington, 1989. London: Sagittarius Press.
Forbes, R.J., 1965. Studies in ancient technology, Volume III. 2nd ed. Leiden: E. J. Brill.
Gettens, R.J. and Stout, G.L., 1966. Painting materials: A short encyclopedia. New York: Dover Publications.
Goffer, Z., 2007. Archaeological chemistry. 2nd ed. Hoboken, NJ: John Wiley and Sons.
Heaton, N., 1912. On the nature and method of execution of specimens of painted plaster from the palace of Tiryns. In: G. Rodenwaldt, ed. Tiryns II: Die Ergebnisse der Ausgrabungen des Instituts: Die Fresken des Palastes, Deutsches Archäologisches Institut. Athens: Eleutheroudakis and Barth. pp.211-216.
Howard, H.C., 1995. Techniques of the Romanesque and Gothic wall paintings in the Holy Sepulchre Chapel, Winchester Cathedral. In: A. Wallert, E. Hermens and M. Peek eds. Historical painting techniques, materials, and studio practice: preprints of a symposium held at the University of Leiden, the Netherlands, 26-29 June 1995., Marina Del Rey, CA: Getty Conservation Institute. pp.91-104.
Istudor, I., 2008. The Church of Voronet Monastery: Technical considerations of the mural paintings. e-conservation, 7, pp.26-40.
Jones, R.E., 2005. Technical studies of Aegean Bronze Age wall painting: methods, results and future prospects. In: M. Lyvia, ed. Aegean wall painting: A tribute to Mark Cameron. British School at Athens Studies, 13. London: British School at Athens. pp.199-224.
Kay, R., 1983. The painters guide to studio methods and materials. Englewood Cliffs, NJ: Prentice-Hall Inc.
Kondoglou, F., 1993. Expression (Ekfrasis) of Orthodox iconography, volume one: technological and iconographic. 3rd ed. Athens: Astir-Papadimitriou. [Έκφρασις της ορθοδόξου εικονογραφίας, τόμος πρώτος: τεχνολογικόν και εικονογραφικόν. Γ’ έκδοση. Αθήνα: Αστήρ-Παπαδημητρίου.]
Laurie, A.P., 1910. The materials of the painter's craft in Europe and Egypt: From earliest times to the end of the XVIIth century, with some account of their preparation and use. The arts and crafts of the nations. London: T.N. Foulis.
Laurie, A.P., 1926. The painter's methods & materials: the handling of pigments in oil, tempera, water-colour & in mural painting, the preparation of grounds & canvas, & the prevention of discolouration, together with the theories of light & colour applied to the making of pictures. New art library. London: Seeley, Service & Co. Ltd.
Martin, J.F., 1986. Longman dictionary of art: A handbook of terms, techniques, materials, equipment and processes. Harlow: Longman.
Seymour, P., 2003. The artist's handbook: A complete professional guide to materials and techniques. London: Arcturus Publishing.
Shaw, J.W., 1973. Minoan architecture: Materials and techniques. Annuario della Scuola Archeologica di Atene et delle Missioni Italiane in Oriente, 49 (Nuova Serie 33). Rome: Istituto Poligrafico dello Stato.
Taylor, W.B.S., 1843. A manual of fresco and encaustic painting; Containing ample instructions for executing works of these descriptions; with an historical memoir of these arts from the earliest period. London: Chapman & Hall.
Thomas, W.C., 1869. Mural or monumental decoration: its aims and methods. Comprising fresco, encaustic, water-glass, mosaic, oil painting: With an appendix. London: Winsor and Newton.
Thompson, D.V., 1936. The materials and techniques of Medieval painting: with a foreword by Bernard Berenson. Reprint 1956. New York: Dover Publications.
Vlavogilakis, A., 2020. Experimental archaeology and ancient Greek monumental painting. Fresco techniques and the case of the tomb of Persephone in the Great Tumulus of Vergina. PhD. University of the Aegean, Department of Mediterranean Studies, School of Humanities, Rhodes. [Πειραματική αρχαιολογία και αρχαία Ελληνική μνημειακή ζωγραφική. Τεχνικές νωπογραφίας και η περίπτωση του τάφου της Περσεφόνης στη Μεγάλη Τούμπα της Βεργίνας.]Winfield, D.C., 1968. Middle and later Byzantine wall painting methods. A Comparative Study. Dumbarton Oaks Papers, 22, pp.61-139.