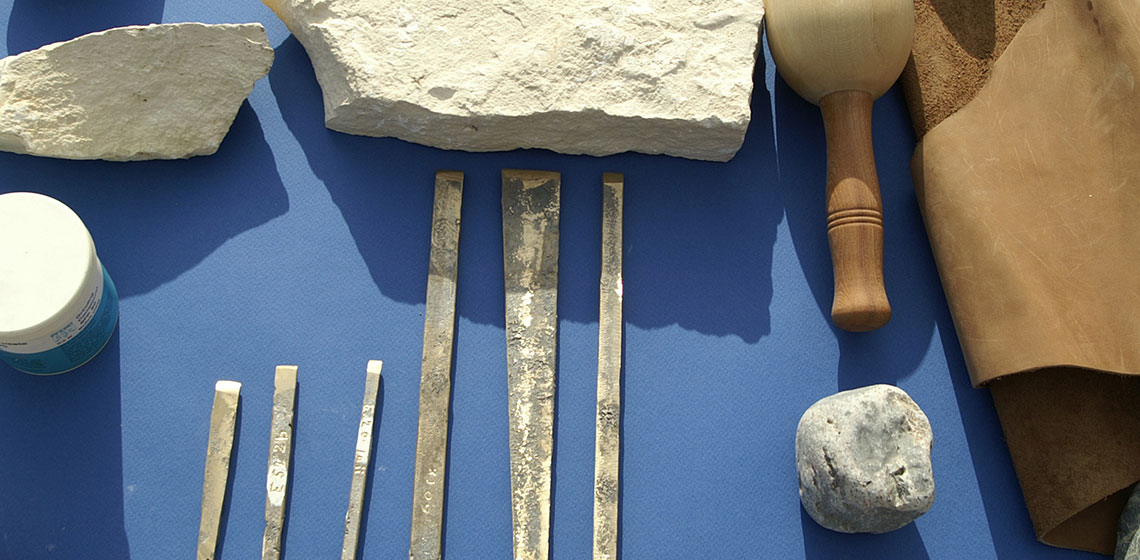
The Minoan chisel is thought to have been used by the metal worker, the stone mason, the sculptor, the carpenter, and the ivory and bone worker. However, barely any work has been conducted to substantiate the different workers and their chisels. For example, the different materials used by the proposed workers indicate that use-wear on the cutting edges probably are of diverse characters depending on the different grade of hardness of the material worked on. To add to this, there have been extremely few experiments conducted with bronze chisels, which could give some indications of use and users. This article aims to disentangle questions regarding the chisels and the working of stone by addressing two issues: The use of chisels on stone during the Minoan period and experimental work with replicas in order to investigate if the bronze chisels were suitable as stone working tools.
Firstly, I will briefly present the Minoan chisel and the archaeological evidence for their use on stone during the Minoan period, while also examining what kinds of stones were used during this period. This presentation is not exhaustive or comprehensive, but points to the different working actions conducted on stone during the Minoan period. The second part of the article will detail the experimental work using chisel replicas on stone.
The Minoan chisel
There are several chisel typologies presented by different scholars. However, the typology presented by D. Evely in his book from 1993, Minoan crafts: Tools and techniques. An introduction, is the only one to concentrate on Minoan chisels. He presents five types of chisels, which are divided into subgroups depending on the different lengths and shapes of the chisels (Evely 1993, 2-11) (See Figures 1.1 and 1.2 below).
Simplifying this complex typology, my conclusion is that there are two kinds of Minoan chisels. One has a somewhat square body of different lengths and a cutting edge width of circa 1-2 cm, with or without a flare, while the other has a rectangular body, also found in different lengths, but with a wider cutting edge circa 2.5-6 cm. These can also be found with or without a flared cutting edge.
Several of these “types” have been found on Crete; over 60 specimens of the square chisel and approximately 70 of the rectangular chisels. The contexts are diverse; they are found in graves, palaces, settlements and shrines (Evely 1993, 2-11).
The archaeological evidence for stone working with chisels: Quarrying and dressing stone
Basically, chisel-work on stone concerns three different working actions: quarrying, dressing and sculpting. Evidence of all these working actions can be detected in the Minoan material. In this section I will consider Minoan quarries and in addition bring forward material from Egypt to further substantiate the use of the bronze chisel in quarries.
It seems as if the Minoans were the first in the Aegean to open quarries, which is probably related to the massive building programs which began in the Old Palace Period, circa 1900 BC (Waelkens 1992, 11). One of the stones quarried was ammoúdha, which is soft sandstone that could be quarried with bronze tools (Shaw 1973, 35-39; Soles 1983, 44-45; Waelkens 1990, 54, Figs. 1 & 3; Waelkens 1992, 8-9; Shaw 2009, 28-36). In the eastern part of Crete, several ammoúdha quarries have been identified which were in use during the New Palace Period (1700-1450 BC), such as one east of the Mallia palace. The stone was used for interior walls and facades in the palace and the surrounding buildings. Of the other quarries, Mochlos served Gournia with ammoúdha, Skaria served Palaikastro and Pelekita and Malamoures provided the palace of Zakros with building material (Shaw 1973, 31-39; Soles 1983, 33-46; Driessen 1984, 143-149; Waelkens 1990, 54, Figs.1-3; Waelkens 1992, 9-10; Papageordakis 1992, 22-23; Shaw 2009, 23, 28-36).
Apart from ammoúdha, limestone was quarried and used as building material during the Minoan period, though mainly in the areas of Knossos and Phaistos (for further reading see: Shaw 2009, 18; 1987-1988 Vandeput, 89). It was the softer limestone of the poros or porólithos variety that was in use. The harder one, sidherópetra, does not seem to have been quarried (Vandeput 1987-1988, 90).
Even though we can pinpoint several locations for quarrying, evidence for the use of chisels is meager. However, in order to free blocks at Mochlos, scoring seems to have been executed with a chisel. A five centimeter wide score, which corresponds to a chisel of the wider rectangular type (Evely’s type 3b), has been identified (Soles 1983, 40; Waelkens, De Paepe and Moens 1990, 52; Evely 1993, 8-10).
The evidence for chisel use for quarrying, based on the Minoan material, is not convincing. Turning to Egypt during the Bronze Age, the picture is slightly different. In Egypt finds of copper or bronze chisels increase during the third Dynasty when building programs in stone were introduced (Petrie 1901, 24, 28, Pls. 6, 9a, 38, 41; Arnold 1991, 257). During the Late Bronze Age (from 18th Dynasty) chisel marks can, for example, be detected in Gebel Silsila (Klemm 1990, 27, Figs. 4 & 5). Arnold notes that there are two chisel types used by stone masons; the round bar chisel and the flat mortise chisel (Arnold 1991, 257-258, Figs. 6.10 & 6.11). These two types are plentyful and date from the Old Kingdom to the New Kingdom (circa 2700-1100 BC). The round bar chisel was used for dressing and leveling a stone surface and the flat mortise chisel was used to cut out, for example, mortises (Petrie 1917, 20, Pls. 11-12; Arnold 1991, 258).
The archaeological evidence for stone working with chisels: ‘Sculpting’
In this section I will point to smaller items produced or ‘sculpted’ in stone during the Minoan era, starting off with stone vases, production of which started in the EM II period, circa 2500 BC. A stone-vase-maker’s tool kit is considered to include: knife-blades, points, chisels, drills, abrasives and polishing equipment, a wheel and lathe, as well as a cutting compass. The chisel was used to define the outer lines of the vase and to scoop out the interior of the vase-to-be (Warren 1969, 157-165; Evely 1992, 19; Evely 1993, 190; Evely 2010, 395). Later on, when making stone vases, drilling out of cores became the most used technique. The evidence for this manufacturing process mainly comes from Egyptian tomb paintings (for examples and further references see: Davies 1943, Pl. LIV; Warren 1969, Fig. 7; Evely 1993, 190). Experimental work has been undertaken to make replicas of Minoan vases by drilling out cores and compare these to Minoan vases and cores (Morero, Procopiou, Vargiolu and Zahouani 2008, 479-482). In these experiments the chisel was not used. Hopefully, further experiments will be undertaken and more stone vases studied, in order to better understand the drilling and chiseling of stone vases.
Stone figurines or sculptures are not abundant from the Minoan period, but if one examines the Cycladic islands and the Cycladic Idols, one can get an understanding of early stone sculpting. Research focusing on the manufacture of Cycladic Idols seems to be divided into two groups; manufactured with or without bronze chisels. Oustinoff indicates that only stone “tools” (emery, obsidian and pumice) were used to shape and polish the Idols. To substantiate this she has undertaken convincing experiments showing that the Idols are “easily” formed using stone (Oustinoff 1984, 39-42). However, other researchers point out that metal chisels could have been used to manufacture the Cycladic figurines. They could have been used in the process of preparing a rough marble surface, prior to more precise working (Getz-Preziosi 1977, 71; Getz-Preziosi 1987, 20, 35).
The archaeological record from Crete, however, does reveal plenty of small stone ornaments of different kinds; personal ornaments such as beads and jewelry and ‘non-personal’ inlays for furniture and additionally, another category of small items – sealstones. As in the case of the Cycladic figurines, the toolkit consisted of stone abrasives, such as emery and obsidian, but also saws, chisels, knives, drills and hammers (Evely 1993, 150-152, 195-205). It is questionable if the chisel was used for the precision work during the manufacture of sealstones and other small ornament. The chisel was probably used to prepare the stone and not for the detailed work. Experiments replicating cylinder seals from Mesopotamia, dating to 3000-2000 BC, revealed that depending on whether they were made of soft or hard stone, chipped flint and copper drills were used for the precision work (Gorelick and Gwinnett 1987, 15-24).
Another category of items that needed to be ‘sculpted’ were stone moulds. These have been found with cavities for various objects and made of different stones. Several moulds made of schist have been found for casting double axes, such as one from Quarter Mu, Mallia (Poursat 1996, 69). From Phaistos, several schist and limestone moulds have also been unearthed; the cavities show that they were casting chisels, bars and knives (Pernier and Banti 1951, 369-371, Fig. 235 a-d). In order to carve a mould, I believe that the same tool-kit as for the smaller items would suffice. Perhaps it was the same workmen who conducted both actions.
Although not exhaustive, this account of the possible working of stone with chisels, gives an idea of what kind of experiments need to be accomplished in order to come closer to verifying the different uses of the chisel. The following part of the article will address the experimental work conducted with Minoan chisel replicas.
Experimentswith chisel replicas
In order to, as far as possible, understand the manufacturing process of Minoan chisels, experiments were undertaken to make modern replicas. Five different chisel types were chosen, based on the types presented by Evely in his book Minoan crafts: Tools and techniques. An introduction, from 1993 (nos. 20-21, 52 and 101). Evely’s no. 101 was, in addition, cast in an altered version (here called no. 101 square) in order to investigate if the cast bars reported from Kommos were used to produce chisels or other small tools (Evely 1993, 2-14; Blitzer 1995, 511-517) (See Figure 2).
Altogether twenty-three replicas were cast, at Forsviks Bruk, an industrial heritage community in Sweden. I am in the process of writing a full account of the manufacturing process which included casting and finishing treatments. These experiments are forthcoming in the article “The chaîne opératoire of the Minoan chisel”.
Carving a stone mould
The first experiment was conducted by Mr. Nigel Ratcliffe Springall, a sculptor who has a workshop in the village of Kritsà, Crete. The experiment consisted of cutting out a stone mould for a chisel and a trunnion axe using the chisels cast at Forsviks Bruk (the chisel model is Evely 1993, 8 no. 74 and the trunnion axe model is Evely 1993, 58 no. 2).
The archaeological material includes, as accounted for above, stone moulds made of limestone; therefore a piece was attained from a local stone yard. The limestone, used for the experiment, is of the poros sort described above and the hardness is approximately 2.5 on the Mohs’ scale. The other materials for the experiments were “river stones”. We discussed the use of stone as a hammer. Not questioning its usefulness as a hammer, but how it was to work with as a tool; the impact of a stroke with a stone could be very painful going back up the wrist and arm. Furthermore, in the case of stone against metal it could be very hard and in a worse case cause severe injuries. However, the conclusion was that depending on the type and shape of the stone the force on the wrist, hand and arm was different. Even though Ratcliffe Springall found a stone that was somewhat comfortable to work with, a wooden mallet was also used. Grinding powder was also obtained in case an abrasive was needed; unfortunately not emery, but a mechanically made substitute for it (See Figure 3).
A wooden mallet was an important tool for the sculptor (and stone mason), however, to my knowledge there are no such tools found on Crete. Nevertheless, examples have been found and also represented in tomb paintings, in Egypt, dating to the Bronze Age. The examples found in Egypt are made of two pieces of wood: an elongated to bell shaped head and a round handle (Freed 1981, Fig. 26; Arnold 1991, 264-265, Figs. 6.18-6.19). A groove on the mallet has been interpreted as a location point for a metal band in order to prevent the mallet from breaking or splitting. Though, Arnold also mentions that the groove could come from the chisel when hammering on it (Arnold 1991, 264).
To start off, the piece of limestone was secured in a wooden box with sand around it, to stop the stone from moving when cut. The stone needed to be dressed in order to cut out the cavities. The no. 101 chisel was chosen because of its’ broad cutting edge, which meant that larger parts of the uneven stone surface were removed in one stroke. To begin with, the stone-hammer was used. After seven minutes the face of the stone-hammer was worn. The chisel’s cutting edge showed use-wear which consisted of several small dents in a row and were somewhat concentrated at the centreof the cutting edge. The butt end of the chisel started to show mushroom edges due to the impact of the stone-hammer.
Although the cutting edge measured below 1 mm it had to be resharpened in order to cut the limestone. The leveling of the stone continued, but with the wooden mallet as a hammer and from this point on, this was the only hammer used. The wooden mallet’s hitting area is larger than the stone’s and also has a handle which meant that more kinetic energy was delivered with one stroke with the mallet (and one does not have to look out for ones fingers!). In practice this meant that the amount of stone cut out using the wooden mallet was far more than with the stone-hammer. The mallet after only five minutes began to show a ‘waist line’ comparable to the wooden mallets found in Egypt (de Morgan 1903, 105, Fig. 153). The chisel became blunt faster this time, due to the effectiveness of the wooden mallet. Another interesting result was when comparing the marks created by the stone-hammer and the mallet. The stone hammer created ridge-like marks in the stone, which were built up almost as small individual sections in the stone. The marks created by the wooden mallet were like small smooth wavy lines in the stone (See Figure 4). This directly reflects the different strikes on the chisel, which affects the kinetic energy and the movement of the chisel in the stone.
The cutting edge, after five minutes using the wooden mallet, showed small dents in a row as previously but the dents were softer than before. In addition, a small mushroom edge had built up in the center of the cutting edge (below 1 mm in width). Although the center of the cutting edge was most worn, the overall appearance was that the cutting edge was more evenly worn now. The butt end of the chisel was not affected by the wooden mallet.
When the stone’s surface was leveled, models of a chisel and trunnion axe were drawn on the stone with a pencil. In Minoan times, they probably would have used charcoal for this (at least for the poros limestone which is creamy-white in colour). Continuing the mould cavities, Ratcliffe Springall changed chisels and from now on used no. 52, since no. 101’s cutting edge was too wide.
Ratcliffe Springall started off with the cavity for the trunnion axe. After twelve minutes the cutting edge had become blunt, but only a few tiny dents were visible. However, one side of the cutting edge seemed more effected than the other, which was probably due to the working angle. The butt was hardly affected; the only way of telling that it was hit was as the rough surface left from casting slowly wore off. The chisel was resharpened in order to continue.
After another fifteen minutes the chisel needed to be resharpened again. The cutting edge was now more affected and tiny dents were visible on the whole cutting edge, even a slight mushroom edge had started to build up (width below 1mm).
Two-three deeper individual dents and a small mushroom edge had appeared (below 1 mm) after six more minutes of work. The cutting edge wore down fast when work was conducted on the ‘ears’ of the trunnion axe. This required working with the cutting edge at a different angle and shorter and more precise strikes on the chisel. The trickiest part of cutting out the trunnion axe was, according to Ratcliffe Springall, the “ears”, which are important for the hafting procedure and therefore of great significance to the axe.
The chisel was resharpened and used for 14 more minutes (a total of 47 minutes). The cutting edge now showed small individual dents along the whole cutting edge. Three larger dents were also identified which had built up a mushroom edge, bending towards the face of the chisel. The butt had now begun to show a mushroom edge. The chisel was again resharpened.
The chisel was checked again after a total of 73 and 93 minutes and the overall appearance were the same. The cutting edge by now was rounded and blunt and the individual dents had been worn down both by use and resharpening. When studied in profile the chisel’s cutting edge had started to flare out.
The chisel was once more resharpened and used for sixteen more minutes (a total of 109 minutes) to complete the mould (See Figure 5). The cutting edge’s outer most parts were flared and had a somewhat convex appearance, but the cutting edge was almost straight. Two-three smaller dents could be identified on the cutting edge but the overall appearance was rounded and worn. The butt end had built up a slightly larger mushroom edge.
After one hour and 49 minutes the limestone mould was finished and had cavities for a trunnion axe and a chisel (See Figure 6). The chisels had performed better than was thought from the beginning and I believe that Ratcliffe Springall was positively surprised by what the bronze chisels could achieve, although constant resharpening was required, unlike the steel chisels he normally uses.
Carving a relief plaque in limestone
I was fortunate to be guided around Athens Acropolis by Petros Georgopoulos, a marble sculptor, and member of The Acropolis Restoration Service and more specifically, a member of the Propylaia Restoration Group. The purpose of my visit was to follow a stone mason in his daily work and also to study the working actions needed to cut stone and what specific marks were created by the different chisels. Furthermore, I took six different bronze chisels to the Acropolis to have Georgopoulos’ opinion of them. An experiment with the bronze chisel replicas was conducted with four of the six chisels (Evely’s nos. 101, 52, 20 and 101 square) (See Figure 7).
The relief was carved on a piece of limestone from Malta, which according to Georgopoulos, corresponds to ones found on Crete. Petros started out with leveling the stone with the flat rectangular chisel (no. 101). After leveling the uneven surface Petros sketched a female face and started to carve it out in relief with the bronze chisels (See Figure 8). For the larger areas which needed some depth, he used nos. 101 and 101 square. For the details and lines around the nose, eyes and mouth he used the smaller chisels, nos. 52 and 20. Georgopoulos commented that the smaller chisels were too short, though if a handle was secured on these they could be effectively used as they were. The relief quickly took form in the stone. He worked very fast; swapping the chisels so fast that I could not keep track of the times they were separately used. He also resharpened them from time to time. The one most affected by the work was no. 101 which became circa 2 mm shorter during the work (See Figure 9). No. 52 was also severely worn during the process and became circa 1.5 mm shorter.
After two hours the relief plaque was finished (See Figure 10) and Georgopoulos concluded the difference between his normal iron chisels and the bronze chisels were that the iron ones are more effective on limestone. So the real advantage of the iron tools would be in saving time (he stated that the iron chisel took out one third more per blow than the bronze ones did). However, the bronze chisels were very stable and easily controllable. He even thought that no. 52 was better for carving details than his chisel with a synthetic diamond cutting edge mounted on a steel handle. The reason for this was that the synthetic diamond chisel cuts too deep with one blow of the hammer and therefore is less controllable. The bronze chisel, on the other hand, did not cut so deep into the stone, which meant that the same line/s had to be cut two or three times instead. This meant that any mistakes could without difficulty be corrected; therefore the bronze chisel was easier to control and the work conducted with more precision (See Figure 11). He also thought that carving the details was much easier than he had ever thought with a bronze chisel. He had, so far, underestimated bronze as a material for tools! There was no difference in the feeling when carving with bronze versus iron chisels on a soft material as limestone. It felt like using his ordinary iron tools.
Conclusionsand future research
These experiments show that the bronze chisels, without any problem, can be used to work soft stone. During the experiments the chisels were used to level limestone in order to cut out a mould with cavities for a chisel and a trunnion axe and carve a relief. However, this does not mean that the Minoans chose to actually use the tools in this manner. To really come to terms with who used the chisels and for what purpose, more experiments must be conducted on bone, metal, wood and also on a harder stone such as marble. One interesting result was that the straight cutting edge of no. 52 started to flare after some use; is this result worth considering when studying the typologies and their subgroups?
To further substantiate the results from the experiments it is most important that the cutting edges of the replicas are compared to the Minoan ones. This further research is under progress and I have studied chisels at the Archaeological Museum at Chania, however these few examples are not enough to draw any further conclusions of work on stone. My hope is that further investigations can be conducted in the near future so as to be able to substantiate the use and users of the Minoan chisel.
Acknowledgements
This article is developed from the poster and demonstration I and Mr. G Lowe participated with during the 7th Experimental Archaeology Conference organized by Cardiff University and St Fagans National History Museum, Wales, 11-12 January 2013. We deeply thank the organizers for the opportunity to participate and for fruitful conversations with other participants during the conference.
My results are due to expert help from all kinds of areas. I was guided by Mr. Petros Georgopoulos for two days at the Acropolis and he generously gave me an insight into what a stonemason’s main tasks are. I want to deeply thank Petros for these two most invaluable days. I sincerely thank Υπηραήα Ευντήρησης Μυνμαίων Ακρόπολης (Acropolis Restoration Services, Ministry of Culture) and Professor Vassiliki Eleutheriou for this opportunity and permission to study the work done by the stonemasons at the Acropolis. I also want to thank Mrs. Bodil Nordström-Karydaki, at the Swedish Institute at Athens, for helping me with the permit and arrangements.
The mould could not have been cut without the expertise and hard work of Mr. Nigel Ratcliffe Springall, whom I sincerely thank for an instructive and productive day at Kritsá. I am most grateful to the manager of Petrákis O.E. at Hersonissos who gave me the stone required for the experiment.
This research could not have been conducted without the scholarships from The Swedish Institute at Athens and Stiftelsen Enboms donationsfond (Kungl. Vitterhetsakademien). I am extremely grateful to them for the opportunity to follow my own research visions and interests.
Bibliography
ARNOLD, D., 1991. Building in Egypt. Pharaonic stone masonry. London & New York: Oxford University Press.
BLITZER, H., 1995. Minoan implements and industries. In J.W. Shaw and M.C. Shaw, eds. 1995. Kommos 1. The Kommos region and houses of the Minoan town, Part 1. The Kommos region, ecology, and Minoan industries. Princeton, N.J.: Princeton University Press. pp.403-535.
DAVIES, De Garis, N., 1943. The Tomb of Rekh-mi-re at Thebes, vol. 1. New York: Plantin Press.
DRIESSEN, J., 1984. Notes on building materials and quarries. In J.A. MacGillivray, L.H. Sackett, D. Smyth, J. Driessen, D.G. Lyness, B.A. Hobbs and A.A.D. Peatfield, eds. An archaeological survey of the Roussolakkos area at Palaikastro, The annual of the British School at Athens 79, pp.143-149.
EVELY, R.D.G., 1992. Stone vases and other objects. In Evely, D., and C. Runnels, eds. Well built Mycenae. Ground stone, Fascicule 27. Oxford: Oxbow Books.
EVELY, R.D.G., 1993. Minoan crafts: tools and techniques. An introduction, Studies in Mediterranean Archaeology 92:1. Göteborg: Åström.
GETZ-PREZIOSI, P., 1977. Cycladic sculptors and their methods. In J. Thimme and P. Getz-Preziosi, eds. Art and culture of the Cyclades. Karlsruhe: C. F. Muller, pp.71-91.
GETZ-PREZIOSI, P., 1987. Sculptors of the Cyclades: Individual and tradition in the third millennium BC. Ann Arbor: University of Michigan Press.
GORELICK, L. and GWINNETT, A.J., 1987. The change from stone drills to copper drills in Mesopotamia. An experimental perspective. Expedition 29:3, pp.15-24.
KLEMM, R. and D., 1990. Roches et exploitation de la pierre dans l’Egypte ancienne. In M. Waelkens, ed. Pierre éterneller du Nil au Rhin carrières et prefabrication. Bruxelles: Credit Communal, pp.23-36.
MORERO, E., PROCOPIOU, H., VARGIOLU, R. and ZAHOUANI, H., 2008. Stone drilling in Bronze Age Crete. In L. Longo and N. Skakun, eds. 2008. ‘Prehistoric technology’ 40 years later. Functional studies and the Russian legacy, British Archaeological Reports - International Series 1783, pp.479-482
DE MORGAN, J., 1903. Fouilles a Dahchour en 1894-1895, Vienne.
OUSTINOFF, E., 1984. The manufacture of Cycladic figurines: a practical approach. In J.L. Fitton, ed.Cycladica. Studies in memory of N.P. Goulandris. Oxford: British Museum, pp.38-47.
PERNIER, L. and BANTI, L., 1951. Il palazzo Minoico di Festòs. Scavi e studi della missione archeologica Italiana a Creta dal 1900 al 1950, vol. II.Rome: Libreria dello Stato.
PETRIE, F., 1901. The Royal Tombs of the Earliest Dynasties, Vol. II. London and Boston: Egypt Exploration Fund.
PETRIE, F., 1917. Tools and weapons. London: British School of Archaeology in Egypt.
POURSAT, J.-C., 1996.Fouilles exécutées à Malia. Le Quartier Mu, vol. 3. Études Crétoises, 32. Athènes: École française d'Athènes.
SHAW, J.W., 1973. Minoan architecture: materials and techniques. Annuario della Scuola Archeologica di Atene e delle Missioni Italiane i Oriente 49, 1971, pp.1-236.
SHAW, J.W., 2009. Minoan architecture: materials and techniques. Studi di archeologia cretese 7, pp.1-337.
SOLES, J.S., 1983. A Bronze Age quarry in eastern Crete. Journal of Field Archaeology, pp.33-46.
VANDEPUT, L., 1987-1988. Spitting techniques in quarries in the eastern Mediterranean. Acta Archaeological Lovaniensia 26-27, pp.81-107.
WAELKENS, M., 1990. Techniques de carrier, prefaçonnage et ateliers dans les civilizations classiques (Mondes Grec et Romain), in M. Waelkens, ed. Pierre éterneller du Nil au Rhin carrières et prefabrication. Bruxelles: Credit Communal, pp.51-72.
WAELKENS, M., 1992. Bronze Age Quarries and quarrying techniques in the Eastern Mediterranean and the Near East. In M. Waelkens, N. Herz and L. Moens eds. Ancient Stones. Quarrying, trade and provenance. Interdisciplinary studies on stones and stone technology in Europe and Near East from the prehistoric to the Early Christian period, Acta Archaeological Lovaniensia, Monographiae 4, pp.5-20.
WAELKENS, M., DE PAEPE, P. and MOENS, L. 1990. The quarrying techniques of the Greek world. In Marble. Art historical and scientific perspectives on Ancient sculpture. Papers delivered at a Symposium organized by the departments of antiquities and antiquities conservation and held at the J. Paul Getty Museum April 28-30, 1988, The J. Paul Getty Museum, pp.47-72.
WARREN, P., 1969. Minoan stone vases. Cambridge: University Press.