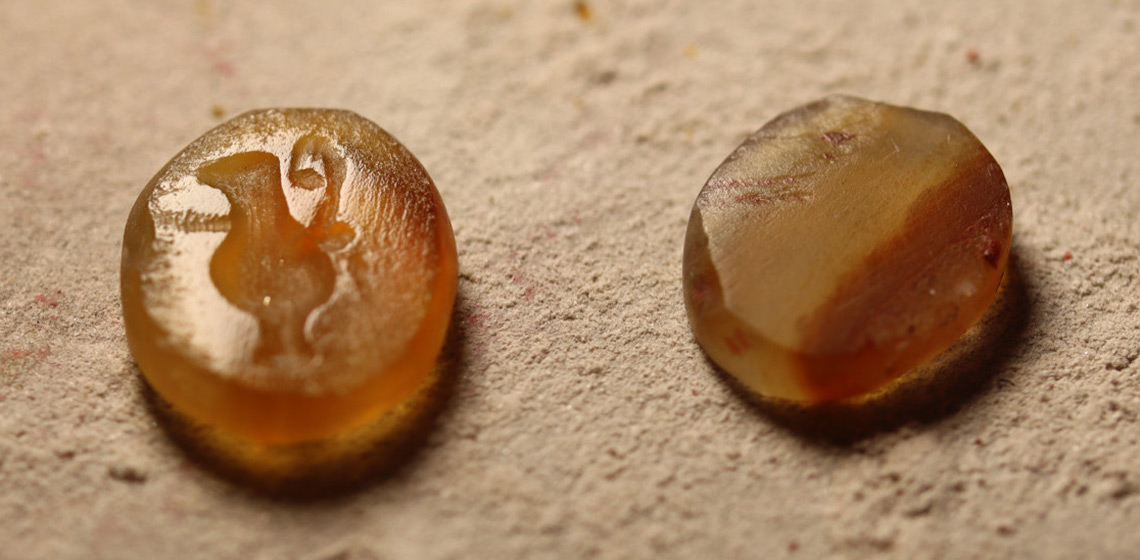
The analysis of archaeological works of art involves their formal, thematic and interpretative description. The importance of these stages rests in their potential to reveal the biography of an artefact. Research methods investigating the production technology behind an object are a valuable factor extending the field of interpretation of a given object. Each finished work is the result of a creative process whose deconstruction might lead not only understanding the artefact itself but also to new perceptions of its creator, artist/craftsperson and the community in which they functioned (Śliwa, 2018, p.68).
Using an experimental method, this article sets out to focus on the sequence and outcome of production stages in the engraving of a Roman gem of carnelian.
Engraved precious stones began to decorate the ancient world as early as 1600 BC, with the art developed in Rome around the 3rd century BC (Michałowski, 1974, p.198). Glyptics with sculpted and carved miniature representations on precious and semi-precious stones, collectively known as engraved gems, fall into two categories: intaglios, where the design is cut into the flat background of a stone, and cameos whose design protrudes from out of the background. (Michałowski, 1974, p.197).
Intaglios are the main point of our interest, as they often served as seals, embedded into pendants and signet rings. Engraved gems are characterised by a wide variety of depictions applied to them, from simplified, schematic reliefs to highly detailed works of art with images of rulers, mythological or other genre scenes. The relics tend to bear tell-tale traces reflecting the craftsman's level of skills. Some are precise and organised (See Figure 1) while others display a chaotic arrangement of unskilfully engraved lines (See Figure 2) (Michałowski, 1974, p.197).
Engraved gems were more than just mundane everyday objects or jewellery. The carved images frequently served as efficient communication tools of propaganda. Roman elites frequently employed experienced artists to engrave gems that would exhibit their status and power (Gołyźniak, 2020, p.31).
Early descriptions of precious stones processing can be found in The Histories by Herodotus of Halicarnassus, completed around 450 BC (Herodotus, VII, p.69). Also, Pliny the Elder wrote extensively about the use of precious stones. Written in the 1st century AD, his Natural History - Book 37 contains a compendium of knowledge about engraved gems with information about the origin and use of precious and semi-precious stones. The descriptions include most of the minerals known today. Moreover, the work provides tips on techniques for processing specific stones, the text is also enriched with comments indicating the popularity of given minerals. That said, ancient sources related to the technology of gem engraving are still insufficient, which prompted the authors of this article to consult Diversarum Artium Schedula, the work of the early medieval monk Theophilus Presbyter (Theophilus Presbyter III, p.95).
Pliny the Elder referred to carnelian as a sard stone due to its commonness (Pliny the Elder: XXXVII, p.105). This opinion is confirmed by the large number of engraved gems made of carnelian, which are common in archaeological sources (Wąsik, 2018, p.49). The modern name carnelian is probably derived from the Latin word carnis, meaning body. This notion is echoed in Pliny's comparison of the sard colour to that of meat (Pliny the Elder, XXXVII, p.86).
The material used in this experiment by the authors for it processing technology is the orange-red variety of chalcedony, whose colour is determined by iron oxides in its structure. Carnelian is graded at standard seven on the Mohs scale of mineral hardness, which characterises scratch resistance of minerals. This means that only a gemstone with a higher hardness such as corundum or diamond, can scratch it to produce a white-coloured mark (Bonewitz, 2012, p.169).
Research on the technology of carnelian engraving began with the preparation of a semi-finished product. Using direct percussion, a flake of the approximate thickness for the finished gem was produced (See Figure 3). The next stage of work called for a retoucher to chip off successive pieces of stone. This was made using materials and methods available in antiquity. The tool's bronze working pointed head was cold hammered for extra hardness and then ground with files (See Figure 4), the socket end was given a cross section similar to Roman tools (Jażdżewska and Sicieński, 2017, p.53). Then, using a knife, a wooden handle was carved, into which a round hole was burned to hold the metal element of the retoucher. When the square section of the tool was hammered into the handles round hole a durable and solid connection was produced. The finished retoucher was used to process the stone by splitting off small pieces to obtain a semi-finished product with a shape as close as possible to a flat, oval plate (See Figure 5). This stage of work is visible in unfinished engraved gems from 1st century BC found in the harbour cities of Muziris (India), Barnis (Egypt) or Aksum (Ethiopia) (See Figure 6) (Thoresen, 2015, pp.155-218; Francis, 2004, pp.447-604; Gupta et al., 2004, pp.9-33; Sidebotham, 2011, pp.236-238).
The irregular shapes of the carnelian chips had to be smoothed out (See Figure 7). The material from which the engraved gem was made can be ground on a sandstone block (Theophilus Presbyter, III, p.95), which was probably done in one of two ways. The first consisted of rubbing the semi-finished product on each side while sprinkling it with water (See Figure 8) (Theophilus Presbyter, III, p.95). The second involved the addition of "sharp sand" (Theophilus Presbyter, III, p.95). This smoothing stage, depending on the sandstone grain size, strength and skill of the craftsperson and the size of the gem could last from minutes to several hours. It took about three hours for the Authors of this article to produce two equal plates (See Figure 9). The work involved alternate grinding of both samples by two people. A third method which involves replacing the water with oil found in some reference literature, failed to produce the expected effect (Osborne, 1912, pp.271-276). In our observations, the oil limited the observation of smoothing progress, which negatively influenced the course of the experiment. But oil can also act as a lubricant in polishing techniques for getting a highly polished surface.
Then, came the stage when the shaped carnelian gems were to be engraved. For the experiment, a stone decorated with a concave Christogram (See Figure 2) served as the model (Spier, 2012, 1p.96). Decorating the intaglio required much less work and provided reproducibility of the results of the experiment (Gray, 1983, pp.191-192). Consequently, the pattern was made with the help of two techniques known in antiquity.
The first method involved the engraving of an ornament with a stylus made of mineral with a higher hardness on the Mohs scale (Osborne, 1912, pp.272-273; Krzemnicki et al., 2019, 7p.14). An account of the use of hard material burins can be found in The Histories by Herodotus (Herodotus, VII, p.69), where he describes stone arrowheads of the Ethiopians, the hardness of which made them suitable for gem engraving (Herodotus, VII, p.69). The fragment implies the use of diamond or sapphire-tipped burins (Osborne, 1912, p.271). Both stones occupy the top of the Mohs scale, which allows them to scratch other minerals of lower hardness (Bonewitz, 2012, p.17). Unambiguous information about the use of a diamond as a stylus is provided by Pliny the Elder in his Natural History (Pliny the Elder, XXXVII, p.190). He mentions sharp pieces of this gemstone set in iron handles which were highly desired by engravers (Pliny the Elder, XXXVII, p.60).
Hardness | Mineral | Other materials for hardness testing |
1 | Talc | Very easily scratched by a fingernail |
2 | Gypsum | Can be scratched by a fingernail |
3 | Calcite | Just scratched with a copper stylus |
4 | Flourite | Very easily scratched with a steel knife |
5 | Apatite | Scratched with a knife with difficulty |
6 | Orthoclase | Cannot be scratched with a knife but scratches glass with difficulty |
7 | Carnelian | Scratches glass easily |
8 | Topaz | Scratches glass very easily |
9 | Corundum (Sapphire) | Cuts glass |
10 | Diamond | Cuts glass |
Table 1. The Mohs Scale of Hardness (acc. to Bonewitz, 2012, p. 17)
The next step of experiment involved the use of a sapphire nugget broken into small fragments (See Figure 10) of which two, with sharply pointed tips, were selected. The small size of the sapphire stylus made it impossible to hold it in the hands, thus necessitating the production of a handle with a socket for the stone. For this purpose, a piece of a bronze rod was given a fan-shaped at one. Copper alloy element was heated and cooled rapidly, allowing the metal to soften. After the stone holder had been hammered onto a wooden shaft, it was possible to bend the metal sheet (See Figure 11). Precisely mounted on the tool, the stylus was then fixed with melted wax (See Figure 12). Such a combination made future replacement of a damaged sapphire possible if need be. Interestingly, engraving tests performed afterwards proved this solution highly effective. The groove cut with the tool were high accuracy and allowed for continuity of lines (See Figure 13). The replaceable tip proved to be of vital importance when the sapphire point deteriorated. Repeated engraving activities resulted in slight but consistent wear of the tool finally hindering work, at which point, it required a repair. This stage of the experiment shows that it is possible to perform engraved ornamentation in the final stages of work, or during the processing of details.
An alternative method of engraving required a simple grinder or a bow drill. Early tools of this type used to produce engraved gems date back to ancient Egypt more than two thousand years BC (See Figure 14) (Gray, 1983, p.192). The production of such a device involved the preparation of a metal working element, which was a carrier of "sharp sand" (Osborne, 1912, p.274; Gray, 1983, p.192). According to later sources, this sand may have been emery, i.e. fine-grained corundum, mentioned by Theophilus Presbyter in his work Diversum Artium Achedula (Theophilus Presbyter, III, p.95). This experiment required the reconstruction of an uncomplicated version of a grinding machine (See Figure 15). It comprised several pieces of wood forming a frame in which holes were drilled. Another element was a rotating, cylindrical piece of wood with a rod fixed on one side and a rod with a disc on the other. The device was completed by inserting the rotating element into the previously made holes in the frame. The bow worked as the driving mechanism (Rajan and Athiyaman, 2004, p.405). The craftsperson set the grinder in motion by wrapping a piece of string or thong on the rotating part of the machine. The metal disc with emery served as an efficient engraving element (Osborne, 1912, p.274; Gray, 1983, p.192). During the experiment, it took one hour to complete an ornament on the first stone (See Figure 16). A skilled craftsperson would be able to achieve the same result much faster, and proficiency in the craft would allow for far more precise and involved ornamentation.
In the final stage of the experiment, the gem was polished using the waste material resulting from earlier grinding of the carnelian plate. In this process, material from both the mineral and the sandstone block was gradually scraped off to create a kind of abrasive paste. After drying into dust, a small amount was dissolved in water or saliva and then applied to a piece of leather or wood (See Figure 17) (Theophilus Presbyter, III, p.95; Osborne, 1912, p.276). The gem was rubbed against the prepared polishing material until a smooth surface was obtained. It was also possible to use a ceramic powder paste with the addition of small amounts of water (See Figure 18) (Theophilus Presbyter, III, p.95). The experiments showed the effectiveness of both methods (See Figure 19).
The experiments conducted by the authors led to the following conclusions. The research confirmed the possibility of making uncomplicated ornamental gemstones with simple tools produced with simple craft techniques. The simplicity of the tools facilitated quick replacement of the working material after possible wear.
The experiments based on ancient and early mediaeval sources helped to verify the methods described in them. In the accounts of both Herodotus and Pliny the Elder, there is an annotation of the use of harder stones for engraving on gems, and the experiments confirmed both sources. The monk, Theophilus Presbyter, also mentions the processing of precious stones and minerals. His comprehensive description of the mediaeval craft proves it to have been both superior to, and more developed than the ancient one. That said, his Diversarum Atrium Schedula does contain technological instructions that were undoubtedly available in the ancient world, too. Among them are the use of emery and the methods of polishing stones. The techniques depicted by the early mediaeval author were also positively verified.
The variable which did not appear in any of the above-mentioned historical sources was the time required to produce an engraved gem. Only with experimental archaeology was it possible to shed some light on this matter. Adding up the duration of the individual production stages makes it possible to draw a hypothesis about the probable length of the entire process. The smoothing stage, depending on the sandstone grain size, strength and skill of the craftsperson and the size of the gem, could last from minutes to several hours. It took about three hours for the authors of this project to produce two equal plates. During the experiment, it only took one hour to complete an ornament on the first stone.
The conducted experiments described in this paper may prompt further investigation into the field of ancient engraved gem-making technology.
Bibliography
Bonewitz R. L. 2012. Nature Guide: Rocks and Minerals, New York. Dorling Kindersley
Francis P. 2004. Beads and selected small finds from the 1989-92 excavations In V. Begley (ed.) The Ancient Port of Arikamedu 2. New Excavations and Researches 1989-1992, Paris. Pondicherry: 447-604.
Gołyźniak P. 2020. Engraved Gems and Propaganda in the Roman Republic and under Augustus. Oxford. Archaeopress Roman Archaeology 65,
Gupta S. P., Gupta S., Garge T., Pandey R., Geetali A. and Gupta S. 2004. On the fast track of the Periplus. Excavations at Kamrej 2003. Journal of Indian Ocean Archaeology 1: 9-33.
Herodotus, Dzieje, translation: S. Hammer, Warszawa 1954, 2020.
Jażdżewska M. and Siciński W. 2017. Siemiechów stan. 2, woj. łódzkie. Cmentarzysko i osada kultury przeworskiej, Łódź: Muzeum Archeologiczne i Etnograficzne..
Krzemnicki M. S., Butini F., Butini E. and De Carolis E. 2019. Gemmological Analysis of a Roman Sapphire Intaglio and Its Possible Origin, The Journal of Gemmology 388, Basel: 710-724 {online} Available at < https://www.ssef.ch/wp-content/uploads/2018/03/2019_Krzemnicki_sapphire… > [Accessed 16/05/2021]
Michałowski K. 1974. Encyklopedia sztuki starożytnej. Europa – Azja – Afryka – Ameryka, Warszawa: Wydawnictwa Artystyczne i Filmowe .
Osborne D. 1912. Engraved gems. Signets, talismans and ornamental intaglios, ancient and modern, New York. Henry Holt and Company
Pliniusz Starszy, Historyi naturalnej ksiąg XXXVII, translation: J. Łukaszewicz, vol. X, Poznań 1845.
Rajan K., and Athiyaman N. 2004. Traditional gemstone cutting technology of Kongu region in Tamil Nadu, Indian Journal of History of Science, 39(4): 385-414.
Sidebotham S. E. 2011. Berenike and the Ancient Maritime Spice Route, Berkeley. Los Angeles.
Spier J. 2012 Late Antique and Early Christian Gems: Some Unpublished Examples. In C. Entwistle and N. Adams (eds.), Gems of Heaven: Recent Research on Engraved Gemstones in Late Antiquity, c. AD 200-600, London. British Museum Research Publication177:193-207
Śliwa M. 2018. Estetyka sztuki pradziejowej. Figuralne przedstawienia kobiece w sztuce epoki kamienia w Europie, In R. Filozoficzny and R. Wiśniewski (eds.), Vol LXXIV, Toruń: 67-82.
Teofil Prezbiter, Diversarum Artium Schedula. Średniowieczny zbiór przepisów o sztukach rozmaitych, translation: S. Kobielus, Kraków 1998.
Thoresen L. 2015. Archaeogemmology and Ancient Literary Sources on Gems and their Origins, In A. Hilgner, S. Greiff and D. Quast (eds.), Gemstones in the first millennium ad Mines, trade, workshops and symbolism, Mainz: 155-218.
Wąsik A. 2018. Kamienie szlachetne w łacińskich źródłach literackich: od Pliniusza Starszego do Izydora z Sewilli (PhD thesis), Wydział Polonistyki Instytut Filologii Klasycznej Uniwersytetu Warszawskiego, Warszawa.