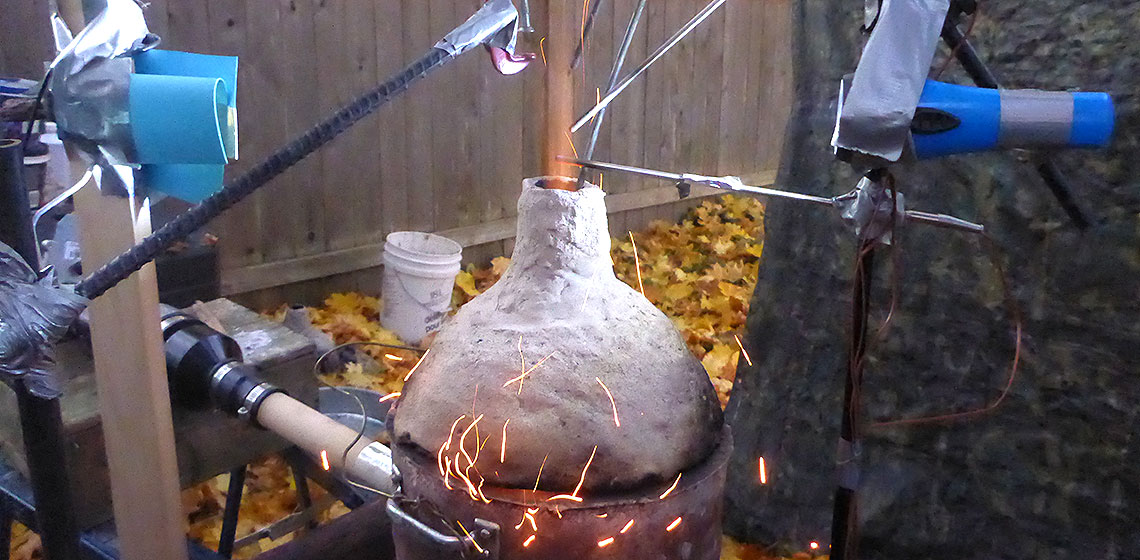
Tens of thousands (Callmer, 1977, pp.12-32) of beads marking the rich graves of the Viking world indicate that the production of these beads is an area worthy of study. Evidence such as mandrels, crucibles, bead fragments, and semi-manufactures exist at Helgo, Birka, Paviken, Hedeby (Lundström, 1976, p.3), Kaupang (Gaut, 2011, p.232), Frojel (Carlsson, 2011), Åhus (Callmer, 2001, p.138), and Ribe (Sode, 2004, p.86). At Ribe, further evidence provides the best published look at possible direct evidence of the bead furnaces themselves. Seven hearths, including most notably hearths ÆZ and ACU (Bencard and Jørgensen, 1990, p.95), are known from the Ribe excavations.
Experiment Background
Unfortunately, no intact furnaces survive. Only the base plates for these potential furnaces and an additional scattering of sherds exist in the archaeological record. Thus, the shape of the body, lid, and chimneys must be inferred and then tested through experimental bead production.
Previous experiments by the Dark Ages Recreation Company’s bead team have explored the functionality of furnace designs based on the Ribe hearths in generating required temperatures (Peterson, et al., 2014). These previous furnaces have been compared to the archaeological evidence and adjustments have been made to try and more closely match the extant remains. Working techniques both in terms of materials (tesserae or rods), and location (chimney or inside the furnace body), have been explored through the production of beads1 . One consistent problem in these experiments has been an excess of ash embedded in the glass beads produced using these furnaces when contrasted with extant examples of Viking Era beads.
The experiments discussed below will further explore one small step in the effort to reconstruct the glass bead making that occurred during the Viking Era in Scandinavia at locations such as Ribe.
Research questions
This next experiment sequence is designed to enable testing of a variety of chimney and furnace top shapes to determine their impact on ash in the working areas. It is hoped that the furnace chimney design can be modified to minimize the ash produced. If so then future experiments involving bead production should show less ash embedded in the beads, hopefully producing beads more similar to the extant examples. At no point in this ash-minimizing sequence will any beads be created. These experiments discussed below explore some questions around the measuring equipment and experimental process that will be used during the ash-minimizing sequence.
The specific questions we are determined to explore:
- Are the experimental steps workable as is or do they require changes?
- Is the equipment set complete and functional for determining levels of ash production?
- Do the sensors and ceramic plates show a similar measurements of ash over the experiment or is either type of sensor a poor method of measuring ash production?
List of Required Materials
The primary need for this pilot experiment is a reusable furnace base that will support several different tops (See Figure 1). This base must be robust enough to survive many experimental runs and the movements required to empty it between such runs.
The next set of equipment is the sensors. Two different light sensors2 and associated software were used to record light levels from an LED flashlight used as the lighting source. The temperature measurements were taken using standard type J/K thermocouples connected through a USB datalogger3 to a computer based recording tool. Bisque plates4 covered in a Cone 06 glaze5 were used to collect ash samples as a check on the effectiveness of the light sensors. A light blue glaze was chosen as it was felt that both the white and black ash particles would stand out against a neutral background colour. Cone 06 glaze was chosen as it sets at 1000ºC which was a temperature close to those expected in the area. Various stands were used to support the furnace, with others supporting the thermocouples, light source, and light sensors in positions around the top of the furnace. The final setup was quite tight in terms of working space (See Figure 2) which should be adjusted for the actual experiment sequence.
Heat generation required additional materials including size-graded oak charcoal, a hair dryer to provide a constant source of air, a ceramic tuyere, couplings, and softwood for the pre-heat phase.
Experimental Steps
Before the pilot run could be accomplished a number of preparatory steps were required. The furnace was constructed by cutting open a propane tank. The top was removed, an opening for a tuyere was cut leaving room so that in future experiments the angle of the tuyere could be easily adjusted, and two handles were bolted onto the frame. A cob mixture of high temperature clay, sand and horse manure was used to line the inside of the furnace with a wall thickness of 2-3 cm. Cob and the high temperature clay were deliberately chosen to increase the durability of the body, and the top was built out of the same material.
As this was a pilot run the top was not built on any particular frame or model. Future tops will need to be built on such frames to ensure that the tops can be matched while the chimney designs are adjusted. Similarly, frames will be needed for the chimneys to ensure they remain true to form while the tops are varied.
The body and top were allowed to air harden before being fired to a ceramic. Firing the cob is required, otherwise the majority of the heat generated would go to driving water out of the cob rather than generating the required heat levels to melt the glass. This heating and the related sintering of the cob into ceramic must be carried out slowly allowing the water within the matrix to evaporate a little at a time, rather than explosively converting to steam causing cracking. To encourage this process, the bottom of the furnace was fired first without a top in place, which worked very well. The tops are a different matter as they concentrate the heat as it is produced. This means the fire must be balanced between going out due to too little fuel, or cracking and breaking the top when too much fuel was added. In this sequence using a pre-fired body made the problem worse. Two tops broke during the firing process and had to be replaced. The third top worked sintering6 without cracking or breaking. It should be noted that due to the thickness of the cob structure the furnace is never fully sintered. It grades from a completely fired interior to a completely dry mud. This will have a clear impact on the taphonomic process as the outer surface will be easily weathered away, while the interior might be expected to survive, but will be thin enough to suffer significant breakage in the freeze/thaw cycle.
The charcoal was graded to a consistent size by breaking it through a frame with 2.5 x 6.25 cm openings and sieving the result through a 6mm mesh. Using charcoal of this size reduces the amount of ash from the fines7 , while ensuring a more even burn without the charcoal moving in large steps as the bigger pieces form bridges and then burn away. The final preparation steps included glazing the bisque plates, and ensuring that the required software was installed and functional.
The actual experimental run was planned to be done twice to allow confirmation of results. By the end of the first run it was clear that the ceramic plates would not be providing the planned cross-check on the light sensors, and that several sensors were going to need to be relocated and their stands adjusted accordingly. Since a new run was going to be required the pilot was stopped after the first run-through was complete.
The experimental run was to consist of the following steps:
- Preheat Furnace. This involved starting a wood fire within the furnace using passive draw rather than forced air. Once this had run for a time forced air was added, further raising the temperature. Finally, unsized charcoal was added bringing the temperature up to the planned temperature range.
- Record Environmental Conditions. As the environment has an impact on the amount of ash generated the temperature, humidity, and wind speed were recorded. This is also when the data loggers were turned on to begin recording temperatures and light levels.
- Empty Furnace. To accurately measure the ash generated in a single run there needs to be no ash left over from previous burns. To empty the furnace, the air flow is shut off and the tuyere is removed from the furnace body. The top of the furnace is removed and placed aside on a concrete tile. The furnace can then be carefully picked up using the handles, carried to the metal dumping station, and inverted allowing the charcoal and ash to pour out. In a previous attempt at this pilot the handles were noted as being problematic. Before this run additional, larger, handles were placed in new locations which allowed the furnace to be easily emptied
- Reload Furnace. A can of the burning coals was placed back into the furnace, and 2.35 kilograms of sized charcoal were added to fill the furnace. The top was placed back on, the tuyere was inserted and air flow was restored. While the charcoal was igniting, the top was sealed onto the base using a previously prepared clay/water mix.
- Record Ash Levels. When the temperature was up to 700ºC, which is a suitable temperature for working glass, the data loggers were marked. One of the glazed bisque plates was rotated into the air column with the glazed side down. Three minutes later the plate was removed. Three minutes later the next plate was placed in the same position. A total of five plates were placed into position during this period. This temperature zone lasted for approximately 35 minutes.
- Close experiment. When the temperature dropped below 700 ºC glass would no longer be workable and the experiment run was complete. Environmental conditions were again measured.
The original plan called for repeating steps 2 through 6 at this point but due to problems with recording the ash levels this repeat was not done. Instead the air was shut off, the tuyere removed and the system allowed to cool.
Variables Impacting Experiment Outcome
There are a number of environmental factors that can influence the sensors, ash levels, and furnace operation. Many of these elements could be minimized by running the experiment indoors, but the use of a charcoal fire, with temperatures occasionally in excess of 1000ºC requires a high ceiling indoor space such as a large garage which was unavailable. The use of light sensors makes the experiment subject to changes in the ambient light level, effected by the weather conditions. Changes at that level may obscure changes in light levels caused by the differing amounts of ash in the air column. Using a strong directed light source, and shielding the sensors to focus the input from a single point source should limit the impact of this variable.
Ambient wind can impact both temperatures above the chimney as cool air enters the column, and also the ash levels as the additional air could move the ash out of the measurement area. This was mitigated by placing tarp walls around the experimental area.
Humidity enters the experiment chain both through the humidity level of the charcoal and in the air being forced into the furnace. On days with higher humidity this impacts the possible temperatures since that extra water needs to be heated in the air column. Additionally, it impacts the water content of the charcoal which can impact ash produced as steam explosions can drive off small flakes of burning charcoal. Higher humidity should thus produce more sparks and ash while reducing the burn time and temperature. Working outdoors this cannot be mitigated and must be recorded and hopefully balanced out by recording the final experiment series on days with similar humidity.
The charcoal is also a source of additional variables. Different kinds of wood will burn at different temperatures and generate different amounts of ash. The choice of an optimal wood will be explored in a separate experiment sequence. For this experiment series this will be addressed through the use of a single product, Royal Oak charcoal, generated from a single type of wood (oak). The size of the charcoal will also impact the conduct of the experiment as discussed above, hence the use of size-graded charcoal. Lump charcoal is required rather than briquets to avoid introducing additional elements such as dust and glue, while providing the closest match to the extant charcoal.
Air flow has a number of impacts on the operation of a furnace; too little air will mean temperatures below the required working level, too much air will push more ash into the air column and will burn the charcoal faster than needed leading to reduced working times. During the Viking Era, the forced air would have been provided using bellows. Previous experiments with bellows have allowed us to confirm that this method works and to measure the air flow provided by a set of bellows. For this experiment series, the bellows were replaced by a hair dryer providing the same air flow to ensure that operator error does not impact these measurements.
The furnace itself can add additional variables into the experiment. If there are openings between the top and body of the furnace these additional vent locations can reduce air flow up through the chimney and hence temperatures and ash level in the air. This can be mitigated using the prepared clay/water mix to temporarily seal the two pieces together in a way that can still be easily broken to open the furnace to refuel it. It is possible, but not known, if the starting temperature of the furnace will impact the ash production. To avoid a possible complication this will be standardized through the use of a pre-heat and two runs to determine if there is any difference in ash production between the runs. The temperature of the furnace will also be measured with one thermocouple.
Analysis and Conclusions
In addition to the breakage and handling problems discussed above other problems did crop up. The thermocouples proved easier to move than desired getting bumped out of the way while one of the bisque plates was being moved (see Figure 3). The interaction between the bisque plates and the thermocouples was also unplanned with the plates providing a protection causing reduced temperature above them, and additional heat below them. This is visible in Figure 3at 17:51:30 when the ‘middle’ and ‘high’ thermocouple readings increase. Additional care was required in choosing the placement of the thermocouples and plate to prevent this interaction. It may be necessary to remove some thermocouples entirely, or to merely accept the interaction. This same interaction will need to be avoided between the plates and the light sensors. This should be easily accomplished by keeping sufficient space between the plate and the light area.
The support arm for the bisque plates was also not firm enough to withstand the heat. This was the reason for the impact between the plate and the thermocouples. The support arm will need to be re-engineered to allow more solidity without restricting the necessary motion to move the plates in and out of the main air column.
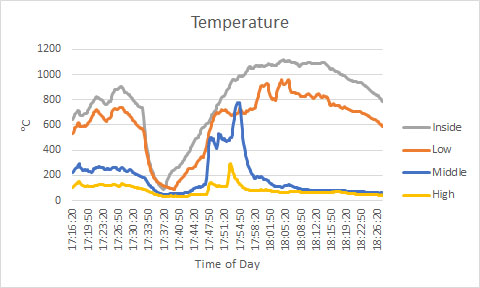
Fig 3. Temperature readings
The use of three different data logging software packages came with an unexpected problem. All three packages default to recording data in elapsed time from the beginning of the experiment – yet all three packages cannot be started at the same time as each start button must be clicked individually. This makes synchronizing the data extremely difficult. Thankfully two of the packages can record based on computer time. The fact that one light sensor cannot, while annoying, can be dealt with by ensuring that a measurable activity (increasing or decreasing the light level) occurs to both light sensors at the same time during the initial moments of data logging, perhaps by placing a piece of paper over both sensors and removing it. For this analysis, the synchronization was accomplished using the arrival of the ceramic plate and the resultant drop in light levels.
Another difficulty with the default software is that the recording intervals do not match. The Neulog sensor defaults to recording one sample per second with two decimals of accuracy while the μLog sensor records every five seconds to no decimals. Settings will need to be explored to see if it is possible to record to an appropriate accuracy at a faster rate, perhaps one decimal at tenth of a second intervals.
Figures 4 and 5 record the light levels from both sensors over the course of the pilot run. In spite of the problems discussed above some interesting points are still visible on the graphs. In figure 4 the red marks are marks set using the data logging software. In the case of marks 1,3,4, and 5 they are set and then the corresponding action was taken. The first one is immediately before the furnace was opened after the pre-heat. The second marks the point where the column of air above the chimney ignited. The third is just before the first ceramic plate was swung into position. The fourth and fifth are just before the second and fifth ceramic plates were moved into position.
As expected around 17:32 the temperature dropped due to the forced air being discontinued and the top removed. The contemporary drops in the light levels and in particular the rapid increases and decreases can be easily seen as a result of the top, furnace body, and hands moving into and out of the light path. What is surprising is the differences in what was recorded by the two sensors. The μLog sensor began the experiment recording approximately 450 lux while the Neulog sensor was recording only around 250. This may have been a fault of the covers that were put in place or a reflection adding more light to the μLog sensor. Since the two settled down to equivalent readings as the reheat began this should merely be monitored during the next pilot run. It is more difficult to understand why the μLog recorded a drop that lasted until 17:40 while the Neulog returned to normal at 17:35. The two sensors were separated by little more than 1cm leaving the question of what could obscure only one of those sensors for five minutes.
The ignition of the air column at 17:47 provides another point of confusion. The μLog records a decrease in light at that point in time. The Neulog records an increase in light and also a much higher variability in light levels as of that time. The values recorded by the Neulog seem to make sense when we consider the type of light that would be added by a flickering combustion in the air column. Understanding what is occurring with the μLog will require more research.
Both sensors record drops in levels at 17:53, 18:04, and 18:17 which match the removal of ceramic plates 1, 2, and 5 implying that as the plates were removed the sensors were momentarily blocked. The Neulog also recorded the removal of plate 4 at 18:11 although that did not impact the μLog. Neither sensor recorded a change when plate 3 was removed leaving an open question of what was different between the movement of plate 3 and the other ceramic plates. Had there been a video record or additional staff, it is possible that an explanation might have been recorded.

Figure 4: Sensor readings from the μLog sensor

Figure 5: Sensor readings from the Neulog sensor
The glazed bisque plates did successfully capture ash. Unfortunately, likely due to a reducing atmosphere, the blue glaze came out grey which makes identifying the black and white ash more difficult (See Figure 6). Due to problems with the support arm the first plate worked the best with the impact of the chimney clearly visible across the entire plate. Counting the ash on this first plate produced a reading of 52.5 flakes per cm2 averaged over the 31.35 cm2 of the plate. Several pieces of ash appeared to be partially overlapping others. This suggests that exposing the plate for a shorter period (perhaps 60 or 90 seconds) would both provide additional readings, and also have lower levels of overlapped ash leading to a more accurate reading.
Increasing the staff level would be useful as attempting to press buttons on the data loggers to generate marks (See Figure 4), take notes, and physically move everything that needed to be moved was very difficult. This could also be addressed by running a continuous video record and taking notes by speaking to the camera or making notes at certain times. The use of the camera would add one more time stamp that would need to be synchronized with each of the other timestamps.
One additional problem, however, overshadows the previous problems. The use of the light sensors assumes that increasing ash levels in the column of heated air over the chimney will decrease the transmission of light through that air. Unfortunately, the gasses in that column of air are also ignited which generates additional light. A number of options to accommodate this have been considered including the use of multiple sensors. With two sensors available, it is possible to configure them such that one sensor registers changes in generated light (See Figure 7 – Sensor 1) while the other records changes in a source light across the column of air (See Figure 7 – Sensor 2). Using baseline measurements for each sensor and eliminating the increased light from the flame it should be possible to record the impact of the ash at time (t) using the formula:
Impact of Ash(t) = Sensor 2(t) - Sensor 2 Baseline - (Sensor 1(t) - Sensor 1 Baseline)
An additional pilot experiment with two runs is now required to test changes to the sensor locations, data logger readings, and ceramic plate placement and timing.
An easier approach to this problem was suggested by Darrell Markewitz and Dr. Marcus Burnham of the Dark Ages Recreation Company. It may be possible to simply filter out the light generated by the flame itself. Normal didymium safety glasses will filter out the majority of the flame wavelengths while allowing enough light from an LED flashlight through to generate good readings. Shifting to a blue filter may also provide good results. Additional pilot runs are currently being planned to test these theories.
The fact that a new pilot experiment is needed provides the answer to the first and second research questions. The steps and equipment planned at the beginning of this pilot were inadequate to run the full experiment series. The results of this new pilot experiment should confirm that the modified equipment and sequences defined above will be adequate to the original purpose of testing the impacts of top and chimney design on ash levels in the air column. Work can then progress on running tests on multiple top and chimney designs. The third research question cannot be answered at this point in time as not enough data was collected on the ceramic plates. Additionally, the light sensors were not configured in a way that would allow the calculation of a single value for the interference of ash. Thus, comparing the two values to determine if there is a correlation must wait until the next pilot experiment is run.
A second pilot experiment was run to test a new theory proposed by Darrell Markewitz in discussions of the problems with the light sensors above. This involved adding a long chimney that could be rotated into place over the furnace (See Figure 8). The length of the chimney and the bend was expected to allow the ash to precipitate out of the air column. A quick pilot run was arranged. When the air column hit 700°C the chimney was rotated into place and when the temperature dropped back below 700°C it was rotated out. The chimney was brushed out and the ash collected (See Figure 9). The pilot run was successful enough to warrant further exploration of this option. The next pilot run should involve sealing the lid onto the body and doing at least five runs so that an idea of the variability of this collection method can be determined.
- 1 See http://www.darkcompany.ca/beads for a record of previous experiments and additional background information.
- 2Neulog NUL-204 and μLog USB Light Sensor
- 3Omega TU120CAXL14U12SMPWM thermocouples. PicoTech TC-08 was used for the datalogger.
- 4Pottery Supply house OT42X
- 5Pottery Supply house GBLU2
- 6 A cob furnace like any clay construction undergoes a transformation at temperature sintering from a clay structure into a ceramic.
- 7‘fines’ are the small pieces of charcoal ‘dust’. Due to their very light weight they are easily thrown upwards in the air column sticking to the beads as ash.
Bibliography
BENCARD, M. and JØRGENSEN, L.B., 1990. Excavation and Stratigraphy. In: M. Bencard, L.B. Jørgensen, and H.B. Madsen, eds. Ribe Excavations 1970-76, Text Volume 4. Esbjerg: Sydjysk Universitetsforlag.pp.15-168
CALLMER, J., 1977. Trade Beads and Bead Trade in Scandinavia ca. 800-1000 A.D. Lund, Sweden: CWK Gleerup.
CALLMER, J., 2001. North-European Trading Centres and the Early Medieval Craftsman. Craftsmen at Åhus, north-eastern Scania, Sweden ca. AD 750-850+. In: B. Hårdh and L. Larsson, eds. 2002. Central Places in the Migration and Merovingian Periods: Papers from the 52nd Sachsensymposium, Lund. Stockholm: Almqvist & Wiksell International. pp.125-157
CARLSSON, D., 2011. Beads at Frojel. [in-person] (Personal communication, 2011)
GAUT, B., 2011. Vessel Glass and Evidence of Glassworking. In: D. Skre, ed. Things From the Town: Artefacts and Inhabitants in Viking-Age Kaupang. Aarhus: Aarhus University Press. Ch.9.
LUNDSTRÖM, A., 1976. Early Medieval studies 9. Bead making in Scandinavia in the early middle ages. Antikvariskt arkiv 61. Stockholm: Kungl. Vitterhets Historie och Antikvitets Akademien.
PETERSON, N., Backa, S., Ross, J. and Schweitzer, R., 2014. Glass on Fire: Temperatures in reconstructed Viking Era bead furnaces.In: M.A. Cramer, ed. If these Bones Could Talk Vol II. Wheaton, IL: Freelance Academy Press. pp. 27-44
SODE, T., 2004. Glass Bead Making Technology. In:M. Bencard, A.K. Rasmussen, and H.B. Madsen, eds.Ribe Excavations 1970-76, Vol. 5. Moesgard: Jutland Archaeological Society. pp.83-102