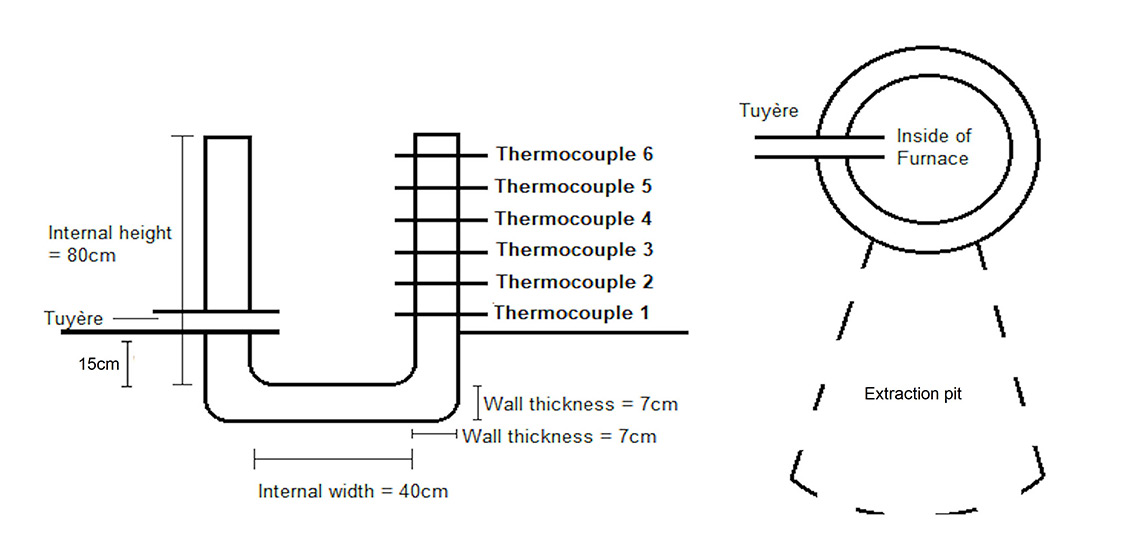
The material record for bloomery furnaces in Iron Age and Roman Britain is fragmentary and, because of this paucity of evidence, the reconstruction of the ceramic structures used in iron production is difficult. Experiments have nevertheless been carried out to explore the working parameters and efficiency of iron smelting in bowl furnaces (small structures with little structure above ground level, interior measuring about 30 cm in height) (Craddock, 1995; Girbal, 2013) and shaft furnaces (height c.1m) (Smith, 2013; Crew, 2013; Doonan and Dungworth, 2013; Tylecote and Merkel, 1985; Tylecote and Wynne, 1958). These experiments aimed to clarify which furnace is more efficient for iron smelting and therefore what method was most likely used in Iron Age and Roman Britain. It is theorised that iron smelting furnaces developed from bowl structures to shaft structures over time, as smelters sought furnaces which could reach higher temperatures and create more reducing atmospheres (Dungworth 2013; Tylecote and Merkel, 1985; Tylecote and Wynne, 1958). These experiments suggest that the shaft furnace was used as it could meet these requirements. This study looks at the working conditions of a shaft furnace at an intermediary height - between that of a bowl furnace and of a shaft furnace - in order to understand its working parameters and to consequently better understand the progression from a bowl to a 1m high shaft structure.
Introduction
Metallurgical remains are one of the most abundant bodies of evidence found during excavations at Iron Age and Roman sites in Britain. These remains include slag, iron blooms, hammer scale, roasted ore and conglomerate. However, relying on such material alone for holistically reconstructing the complex technological processes of metallurgical production at these sites is problematic (Coghlan 1977 p.19) because these materials could have been produced in a number of different pyrotechnical structures. Therefore, in order to fully comprehend the production of iron blooms in this period, an understanding of the type of furnace used in iron smelting is necessary. Unfortunately, remains of Iron Age and Romano-British furnace structures are rare: most sites only present ceramic evidence, scattered at the base of the furnaces (Collard et al., 2006). Whilst this evidence can provide us with information on the diameter of the furnace base for example, it does not inform us about other structural dimensions such as the thickness of the walls, the position of the tuyère, the full height of the walls, and the diameter of the top of the furnace. These features are important if we are to understand the smelting process, because previous experimentation has suggested that furnace dimension can influence the size of the bloom produced (Tylecote 1992, p.47).
The current archaeological consensus is that iron smelting started in a bowl furnace structure and that over time the structure’s walls were raised in order to achieve higher temperatures and more reducing atmospheres (Dungworth 2013; Tylecote and Merkel, 1985; Tylecote and Wynne, 1958). Structures with higher walls are known as shaft furnaces, and it is accepted that, at a fully developed stage, they reached 1 m in height (Crew, 2013; Doonan and Dungworth, 2013; Tylecote and Merkel, 1985; Tylecote and Wynne, 1958). To explore this development in technology, experimental campaigns have been carried out to investigate the working parameters of bowl hearths and shaft furnaces at an established height of 1 m and over (Smith, 2013; Crew, 2013; Dungworth, 2013; Tylecote and Merkel, 1985; Tylecote and Wynne, 1958). However, there is little academic publication looking at the altering level of charcoal within a shaft furnace. Work has been conducted to assess the differing heights of shaft furnaces, however this has been documented primarily as conference papers, individual papers and internet publications. It was our desire to add to these investigations and to consider the development of the shaft furnace. If a shaft furnace of 1 m in height developed over time to improve smelting conditions, it can be considered that the higher the shaft becomes, the better the internal conditions are, in terms of temperature, reducing environment and the amount of ore which can be inputted. Two smelts were run during an experimental campaign (one filling the furnace to a height of 50 cm, and one at a height of 80 cm), in order to, first, compare their internal environments and iron production, and second to investigate the development of the shaft furnace in more detail. The results are presented in this paper.
Iron smelting technology
The most common reconstruction of a bloomery shaft furnace consists of a cylindrical chimney measuring c.50 min diameter (external diameter including walls) and c.1 m in height (Cleere, 1971, p. 205). I would also suggest that the average height is more in the range of 70 cm. The composition of the building material is clay, mixed with sand and straw. A hole is placed in the side of the chimney, into which a tuyère is inserted in order to direct air from the bellows during the heating of the furnace (Crew 2013, Tylecote and Merkel, 1985; Tylecote and Wynne, 1958). A larger hole at the front and base of the chimney facilitates the tapping of slag and the extraction of the bloom. The furnace is filled with charcoal to achieve a combustion zone that allows the iron ore to reduce (Markewitz, 2012). A combustion zone is achieved by heating the charcoal and iron ore together. The combustion of the charcoal produces superheated carbon monoxide. The iron ore reacts and reduces with the carbon monoxide, converting the ore into metallic iron (Friede and Steel, 1977). The ore and fuel travel down the shaft together, allowing different stages of decomposition and reactions to happen at different stages (Mihok, 1993, p. 230). The reduction starts at c.750°C. At 900°C, in the austenite phase of iron, the carbon becomes a solution. The ‘purer’ iron produced then falls to the bottom of the furnace where it forms a spongy bloom. Slag is formed as a by-product as the impurities are separated from the iron and it can be ‘tapped’ from the furnace or removed after the bloom is extracted, since it cools much quicker than the iron (Markewitz 2012). The structure of the furnace and the resources put into it affect the achievement of necessary conditions for the reaction and process to take place.
Experiments testing the working parameters of iron smelting in a bowl hearth have been carried out. The experiments by Cleere (1971, 1972) and Coghlan (1977) deemed that the bowl furnace was too oxidising for a successful separation of the slag from the iron to occur. However, an experimental campaign undertaken in Sheffield in 2012 showed that the bowl furnace could create a suitable reducing atmosphere for smelting iron if it was loaded in a certain way. The experiment by Lucas et al. (2012) achieved a reducing environment but showed that the amount of iron which could be produced was limited due to the size of the furnace. The experiment presented in this paper looks to expand knowledge on the development of the bowl hearth by testing a furnace with a height between that of a bowl furnace and a 1 m shaft furnace. By running such a furnace, the internal environment can be investigated and it can be assessed whether the higher walls do realistically create a better internal environment (in terms of heat and reducing atmosphere), or if the larger furnace instead facilitates the production of a larger bloom.
Methodology
For this study, two comparative smelts were carried out. Due to time restrictions, one furnace was used for both the smelts. The furnace was filled with charcoal to a height of 80 cm for the first smelt (smelt 1) and to a height of 50 cm for the second smelt (smelt 2) in order to simulate both heights. An external and internal marker was drawn onto the furnace to allow this to be conducted as accurately as possible, when reloading the furnace. Using the furnace twice reduced the number of variables in each smelt, because the size and thickness of furnace walls, the percentage and distribution of organic material in the clay, shape of chimney and the overall form of the furnace remained the same. However it is recognised that the furnace will have altered during the first smelt, it will have become vitrified and will have gained fractures and cracks. The furnace was checked between smelts and the furnace walls on the interior were intact, but had become more vitrified. This ensured that differences in the smelt were less likely to be caused by differences in furnace construction, and instead more likely to be caused by the structure’s height, the smelting environment and the amount of charcoal.
The furnace constructed for this experiment had an internal diameter of 40 cm, a height of 80 cm, and a wall thickness of 7 cm (See Figure 1). During the construction the clay slumped due to the wet weather, making the external wall thickness at the base thicker, than at the top. However the internal diameter was consistent, throughout the shaft, from base to top. The furnace was built by moulding bricks of hand processed natural clay (local Sheffield clay) to which sand (silica building sand) and straw (commercially-bought) had been added. The ratios of the material added were clay:sand = 1:1, with 15% of the overall material being straw, which was processed to be an average length of 4 cm. The furnace was built in two stages to allow the clay to dry out and to prevent it from slumping. However, heavy rainfall and storms during the week in between the two building sessions prevented the clay from successfully drying, thus allowing for a maximum of 80 cm rather than the desired 1 m. Once the furnace was moulded to 80 cm, a low temperature wood fire was lit and maintained inside the furnace for 3 hours to allow the clay to dry. The tuyère was added at ground level, which was 15 cm above the base of the furnace (internal base, not including walls). The clay was made with studio clay and sand (1:1) and pre fired in a kiln.
During the experiments (See Figure 2), internal thermocouples (K-type thermocouples with a Vichy DM6804A+ reader) with a range of up to 1200°C was used to measure the temperatures reached during the smelts. The thermocouples were placed 5 cm into the furnace, beyond the walls and temperatures were taken every 10 minutes.
The metallurgical products (iron bloom, slag and roasted ore) were collected for subsequent identification and weighing in a laboratory environment. Iron bloom and production debris (slag and partially reacted ore) were assessed and compared macroscopically in order to assess how the differences in furnace height may have affected the iron product (See Figure 3).
For both experiments, the furnace was pre-heated, for an hour, with a wood fire. This allowed for slow warming and for cracking from thermal shock to be prevented. The furnace was then filled with charcoal (lump wood charcoal) to the designated height for the experiment. Once the charcoal was lit, crushed iron ore (67% iron content hematite) and charcoal were added when required for 2 hours. The charcoal was crushed to an average size of 5 cm and weighed before being administered to the furnace in 3kg batches. Iron ore was crushed using a hammerstone to an average size of 1 cm then weighed before being placed into the furnace in 100g batches. These batches once weighed, were then administered in smaller amounts of a period of time (6 loads). When a load was administered, was determined by the furnace burning down. When the furnace had burnt the fuel down to a level c.8 cm from the rim of the chimney, the load of ore was sprinkled into the furnace, then charcoal placed until it reached the rim. This can allow us to consider which smelt was more efficient in terms of the amount of charcoal used to the amount of iron produced.
Air was added to the furnace with large single action bellows (1 m in length). These bellows produce a steady gust of air which lasts 5 seconds (stroke length of bellows is 80 cm). The metal pipe from the bellows was attached to the tuyère which was built into the side of the furnace. The latter was inserted into the wall of the furnace and positioned at a 90° angle to the extraction pit. The bellows were pumped to continuously admit long slow blasts of air throughout the smelting process. Participants alternated to allow for relaxation between sessions and to keep the bellowing at a consistent pace. This task was paused for safety reasons while ore and charcoal loads were added: the size of the flames coming out of the top of the furnace subsided when the bellowing was halted.
After 2 hours of smelting, the furnace was allowed to burn down before the bloom was extracted from the furnace. This took c.40mins for smelt 2 (smelt 1 did not burn fully down due to a problem with the tuyère). The charcoal was burned down (from full to the rim to c.1/3 full) before the bloom was extracted. This is to allow time for the majority of ore which has been added to the structure to reach below the height of the tuyère. This makes the extraction of the bloom easier: the less unburned fuel there is to empty from the furnace, the easier it becomes to locate and extract the bloom and manage with temperatures of extracted fuel in the extraction pit.
The bloom was extracted by removing the clay plug from the arch at the front of the furnace. The remaining charcoal left in the furnace was scooped out using tongs and a shovel. Then the bloom was located and extracted using tongs.
Results
Smelt 1 (height of 80 cm) used a total of 1.6 kg of ore and 22.8 kg of charcoal. The temperatures for thermocouples 2, 3, and 4 (See Table 1) remained between 800°C and 1000°C during the 2 hours of smelting. This means that the middle zone of the furnace attained the temperature required for the transformation of the ore to begin: reduction starts at c.750°C and the carbon becomes a solution in the austenite phase of iron at 900°C (Tylecote, 1986, 151-2). Thermocouple 1 recorded that the temperature at the bottom of the furnace exceeded the temperature required for the slag to liquefy and separate from the bloom of iron (1200°C). The recorded temperatures therefore exceeded those required for smelting. In the lower part of the furnace, temperatures quickly reached 1200°C or higher. This was above the limit for the thermocouples used and therefore, temperatures could not be accurately measured after this point. This suggested that the furnace was achieving and maintaining the high temperatures required for a successful smelt.
The temperature readings inside the furnace steadily increased until around 100 minutes into the smelt, but then began to plummet (See Graph 1). This was due to the tuyère becoming blocked and the furnace becoming deprived of air. Slag cooling and forming inside the furnace, where the tuyère was positioned, blocked the latter. This lack of air also affected the burn rate of the charcoal. This altered the efficiency of the smelt and meant that temperatures decreased due to lack of oxygen. This also decreased the consumption rate of the charcoal, as the lower temperatures inside the furnace meant that the charcoal in the furnace could not be fully burnt. Because the charcoal consumption rate had slowed considerably, it was decided to extract the bloom. 160 minutes into the smelt, although the charcoal had not fully burnt down to the desired amount of 1/3. This decision was taken to prevent the temperature in the lower part of the furnace from dropping further and the cooled bloom from fusing to the furnace walls or base. The temperature readings had remained consistent until the blockage of the tuyère occurred.
Mins | Time | Thermocouple 01 | Thermocouple 02 | Thermocouple 03 | Thermocouple 04 | Thermocouple 05 |
30 | 10:30:00 AM | 1130 | 912 | 704 | 650 | |
40 | 10:40:00 AM | 1123 | 896 | 857 | 839 | 808 |
50 | 10:50:00 AM | 1185 | 977 | 865 | 825 | 812 |
60 | 11:00:00 AM | 1137 | 914 | 914 | 844 | 819 |
70 | 11:10:00 AM | 1131 | 908 | 886 | 875 | 892 |
80 | 11:20:00 AM | 1158 | 923 | 973 | 923 | 933 |
90 | 11:30:00 AM | 1155 | 921 | 992 | 973 | 944 |
100 | 11:40:00 AM | 1200 | 938 | 1012 | 977 | 958 |
110 | 11:50:00 AM | 933 | 1020 | 953 | 915 | |
120 | 12:00:00 PM | 896 | 1040 | 905 | 902 | |
130 | 12:10:00 PM | 1118 | 901 | 786 | 810 | |
140 | 12:20:00 PM | 980 | 884 | 720 | 763 | |
150 | 12:30:00 PM | 901 | 750 | 683 | 719 | |
160 | 12:40:00 PM | 893 | 733 | 664 | 704 |
Table. 1. Internal temperature readings taking by thermocouples during smelt 1.
Graph 1. Smelt 1 data: Graph showing temperature readings from thermocouples.
Macroscopic analysis of the iron slag collected revealed large proportions of undiagnostic slag alongside a considerable quantity of run slag. Similar to tap slag, run slag indicates that the slag was fluid at some stage during the smelt although the flow surface suggests a vertical flow in contrast to the horizontal flow witnessed in tap slag (Dungworth and Mepham, 2012).
Smelt 2 (height of 50 cm) used a total of 1.6 kg of ore and 23.6 kg of charcoal. Thermocouples 1, 2, and 3 were used. Thermocouples 4, 5 and 6 were not used as in smelt 1because these were placed above the height of the charcoal. This smelt did not encounter any problems with the tuyère (See Figure 4).
During the smelt, the temperature at the base of the furnace reached 1200°C rapidly, but fluctuated comparatively more at position 3 – at 40 cm from base (See Graph 2). This temperature fluctuation at position 3 is most likely due to the thermocouple’s position at the upper limit of the charcoal fill, as at times it was exposed to the air due to the charcoal burning down below that point. The substantial drop in heat near the charcoal line at 11:35am is thought to correlate with the addition of ore and charcoal at 11:36am. It is likely that this reading was taken during the 1 or 2 minute gap in which the bellowing was paused for the safe placement of the raw materials into the furnace. Thermocouple 2 was withdrawn when temperatures reached above 1200°C. Most notably, towards the end of the smelt, as the charcoal burnt down, temperatures remained above 1200°C. This was determined by placing the thermocouple back inside the furnace to see if the temperature had dropped. When the temperature reached above 1100°C, the thermocouple was taken out to prevent it from breaking, and therefore an accurate temperature reading could not be recorded. This contrasts with the readings from smelt 1 which demonstrate that temperatures had decreased by the end of the smelt.
The temperatures recorded during this smelt show a more consistent range across the furnace than during Smelt 1 where the temperatures were more varied. In smelt 1, an area in the top half of the furnace showed lower temperatures (c.700-900°C) than the bottom half of the furnace (1200°C). This is likely due to smelt 1 involving more charcoal and a taller furnace: this structure took more energy to heat.
The temperatures needed for the slag to liquefy and separate were achieved at the bottom of the furnace (location of thermocouple 1 and 2 at 20 and 30 cm from the base). However the temperatures recorded for thermocouple 3 varied because it was positioned near the upper limit of the charcoal. This indicates that the shorter furnace can achieve the temperatures needed for iron smelting and for the slag to separate from the bloom of iron, but that there is only a small zone in which the reaction can take place.
Mins | Time | Thermocouple 01 | Thermocouple 02 | Thermocouple 03 |
0 | 0 | 0 | 0 | |
35 | 10:45:00 | 933 | 340 | 308 |
45 | 10:55:00 | 1014 | 930 | 350 |
55 | 11:05:00 | 1045 | 910 | 290 |
65 | 11:15:00 | 983 | 1085 | 541 |
75 | 11:25:00 | 968 | 1190 | 600 |
85 | 11:35:00 | 934 | 1175 | 194 |
95 | 11:45:00 | 940 | 1200 | 460 |
105 | 11:55:00 | 978 | 1093 | |
115 | 12:05:00 | 1035 | 1210 | |
125 | 12:15:00 | 1035 | ||
135 | 12:25:00 | 1281 |
Table 2. Internal temperature readings taking by thermocouples during smelt 2.
Graph 2. Smelt 2 data: Temperature readings from thermocouples.
The bloom produced during smelt 2 was more consolidated and better-reacted than the one produced during smelt 1.
Discussion
The results from the two smelts can inform us about the efficiency and productivity of what might be considered an intermediary stage of the shaft furnace. As well as measuring temperatures and analysing the products of the smelts, it is possible to understand the development of the bowl furnace into a high sided shaft furnace of 1 m.
Both furnace shaft heights were evidently viable options for producing an iron bloom, although a furnace with a shorter shaft required more monitoring and needed filling more often, to maintain the smelt. Temperature maintenance and fluctuations varied between both smelts. Smelt 1 (height of 80 cm) maintained more consistent temperatures than smelt 2 (height of 50 cm) although both events produced the temperatures required to smelt iron from ore. The amount of charcoal used cannot be compared due to the blockage of the tuyère which caused lower temperatures and a slower burn rate for the charcoal.
The similar quantities of iron bloom produced during both smelts indicate that furnace chimney heights of 50-80 cm are viable for the production an iron bloom with a similar production rate. The blooms were cut open to reveal a complete silver metallic content, with no slag inclusions. The internal atmosphere maintained within the furnaces is however significantly different. The smaller furnace (smelt 2) maintained temperatures over 1200°C, whereas the taller furnace (smelt 1) had two zones: with temperatures between 800°C and 1000°C and a second zone over 1200°C.
Additionally, comparing the metallurgical products recovered from each smelt allows us to explore the direct impact of the furnace shaft height on the amount of iron bloom and slag produced. We can also assess the quantities of recovered unreacted ore and how this can inform us about the operational dynamics of the furnace; 500g of unreacted ore was collected from smelt 2, whereas in smelt 1 no unreacted ore was observed. The presence of these unreacted materials points to the limited success of each smelt. However it can also be considered to the time restraints of the smelt. As this was conducted as part of a module, the smelt time was shorter than usual, meaning not all the fuel could be burnt down in the time, to below the tuyère point. There was also some ore from smelt 2 that had not been fully reacted, but had partially reacted and fused together. This material had not been subjected to temperatures high enough to separate the impurities within it. A conglomerate was formed, this happens when the ore has not been smelted fully, but has partially reacted and fused together. The presence of a conglomerate indicates that either the temperatures were too low or the atmosphere was not reducing enough in the furnace. In the case of smelt 2, where a conglomerate formed, it is more likely that this ore was not in the furnace for long enough before the charcoal was burnt down, and so the temperatures at this point would not have been sufficient to smelt the ore.
The difference in morphology between the unreacted ore of smelt 2 and the fused ore of smelt 1, could be considered to result from the furnace height. As the ore began to fuse in smelt 1, however it did not get chance in smelt 2. The shorter shaft furnace, managed to achieved the temperatures needed to separate slag from iron bloom, however due to the lower quantities of charcoal in the shaft (50 cm compared to 80 cm), the ore took less time to move through the furnace and reducing environment. Because of the use of a shorter structure, smelt 2 had no ‘preparation zone’ in the top half of the furnace. Temperatures of c.700-900°C allowed the reduction of the iron ore to start at c.750°C, followed by a zone at 900°C. The ore then moved down to a zone at above 1200°C where the slag became molten and ran away, leaving a solid bloom of iron with some porosity.
In smelt 2, the charcoal level was lower, and the temperatures across the internal environment of the furnace were at c.1200°C. There was no upper region of a lower temperature and a reducing atmosphere as in the case of smelt 1. Therefore, the slag started to liquefy at the same time as the reduction of the iron took place, in the same zone in the furnace. This means that the reaction took place quicker than the more gradual conversion of smelt 1.
Both furnaces were capable of producing an iron bloom and achieved the temperatures needed to smelt iron (above 1200°C). However, the increased height of the furnace during smelt 1 allowed for a slower smelting process. This experimental campaign showed that a specific furnace height is not required for an iron bloom to be produced but that a taller furnace provides different regions of temperature in a reducing environment thus allowing the smelting process to take place gradually as the iron ore descends through the furnace. This is due to a higher positioned reducing zone at a temperature between 700°C and 900°C and a lower positioned zone with a higher temperature of above 1200°C which allows the iron to start reducing before the slag liquefies.
Other metallurgical debris (ore and charcoal) were recovered from the smelting area and provide an insight into other activities which took place around the furnace. For instance, ore and charcoal, consolidated after both smelts, was recovered from around the area from which the bloom was removed. This type of evidence can indicate how the space was used and what activities occurred after the bloom was extracted. Hammer scale, slag droplets, and roasted ore were also recovered in small quantities. These came from consolidating the bloom while it was still hot from the furnace by hitting it with a wooden hammer. This processes forces liquid slag out from the bloom’s structure thus turning it into a more consolidated mass. This evidence from the consolidation process provides more detailed evidence of specific stages of metalworking. Direct engagement with how such material is made and scattered across the ground during the smelting process helps the archaeologist recognise its constituent components during excavation and allows us to understand the specific processes and factors involved in its creation. This therefore provides ample evidence to recreate the processes which took place, based on experimental results which can be extrapolated to archaeological evidence (See Figure 5).
Conclusion
This study has demonstrated that it is possible to successfully smelt iron in a 50 cm high furnace structure which essentially forms a middle ground between a bowl furnace (30 cm high) and a full height shaft furnace (1 m). The temperatures achieved in both smelts show that both furnace heights are able to produce the temperature required (1200°C) for the iron ore to be smelted into a bloom and for the slag to be separated. The experimental campaign showed that the taller chimney, created a larger area within the furnace which has a reducing environment. As well as having a larger amount of charcoal for the ore to pass through during smelting, it allows the smelting process to take place more gradually and completely by going through two zones: a higher zone of reduction (700-900°C) and a lower zone of reduction (>1200°C) where the slag becomes liquid. This study therefore concludes that the reasons for the development of the taller 1 m furnace lie in the need to make the smelting process easier to carry out, to be more reliable and efficient, and to hence be more successful, as well as providing an environment that facilitates easier and more successful separation of slag from the iron bloom.
Acknowledgements
We would like to thank the following for their contribution and support throughout this project: Gareth Perry, Colin Merrony, Patrick Cropper, Matthew Lester, Richard Bakewell, Augustine Chapman, Emma Charity-Kirk, Sarah Child, Tom Clark, Matthew Crowder, Jonathon Friend, Peter Smith, Ryan Ward, John Welsh, Fraser Worthington and Haolan Yao. As well as a special thank you to Tom Booth from Sheffield City Trust for the use of the land at Beauchief Abbey.
Bibliography
Cleere, H., 1971, Iron smelting experiments in a reconstructed Roman furnace. Britannia 2, pp.203-217 [online] Available at: < https://www.jstor.org/stable/525810 >. [Accessed 14/05/2020]
Cleere, H. F., 1972. The classification of early iron-smelting furnaces. The Antiquaries Journal, 52(1), pp.8-23. [online] Available at: < https://doi.org/10.1017/S0003581500020126 > [Accessed: 11/12/2019]
Coghlan, H. H., 1977. Notes of Prehistoric and Early Iron in the Old World. Occasional papers on technology, 8. The University of Oxford.
Collard, M., Darvill, T., Watts, M., Bayliss, A., Brett, M., Ramsey, C.B., Meadows, J., Morris, E.L., Van Der Plicht, H. and Young, T., 2006. Ironworking in the Bronze Age? Evidence from a 10th century BC settlement at Hartshill Copse, Upper Bucklebury, West Berkshire. Proceedings of the Prehistoric Society. Vol.72, Cambridge University Press, pp.367-421.
Craddock, P.T., 1995. Early Mining and Metal Production. Edinburgh: Edinburgh University Press.
Crew, P., 2013. Twenty-five years of bloomer experiments: perspectives and prospects. In: Dungworth, D. and Doonan, R.C.P., eds., 2013. Accidental and Experimental Archaeometallurgy. London: Historical Metallurgy Society, pp. 25-50.
Doonan, R. C. P. and Dungworth, D., 2013. Experimental archaeometallurgy in perspective. In: Dungworth, D. and Doonan, R.C.P., eds., 2013. Accidental and Experimental Archaeometallurgy. London: Historical Metallurgy Society, pp.1-10.
Dungworth, D. and Mepham, L., 2012. Prehistoric iron smelting in London: evidence from Shooters Hill. Historical Metallurgy. 46(1), pp.1-10.
Dungworth, D., 2013, Experimental archaeometallurgy: hypothesis testing, happy accidents and theatrical performances. In: Dungworth, D. and Doonan, R.C.P., eds., 2013. Accidental and Experimental Archaeometallurgy. London: Historical Metallurgy Society, pp.11-16
Fox, A., 1954. Excavations at Kestor, an early Iron Age settlement near Chagford, Devon. In: Transactions of the Devon Association for the Advancement of Science. 86, pp.21-26.
Friede, H. M., and Steel, R. H., 1977. An experimental study of iron-smelting techniques used in the South African Iron Age. Journal of the South African Institute of Mining and Metallurgy. 77(11), pp.233-242.
Girbal, B., 2013. Experimenting with the bowl furnace. In D. Dungworth and R.C.P.
Doonan, eds., 2013. Accidental and Experimental Archaeometallurgy. London: The Historical Metallurgy Society Ltd. pp.83-92.
Lucas, V., Marks, Y., O’Frighil, D., and Doonan, R., 2012. The Little Bowl That Could! Experimental iron smelting in a bowl furnace, poster presented at the International Symposium of Archaeometry (ISA) 2012, in Leuven.
Markewitz, D., 2012. But if you don't get any IRON..." Towards an Effective Method for Small Iron Smelting Furnaces. EXARC. Issue 2012/1. [online] Available at: < https://exarc.net/ark:/88735/10041 > [Accessed: 11/12/2019]
Mihok, L., 1993, Metallographic examination of pattern-welded swords from the Hark Roman period in Eastern Slovakia. Archaeomaterials, 7, pp.41-51 (Philadelphia, 1993).
Smith, T., 2013. A report on the Wealden Iron Research Group smelt. In Dungworth, D., and Doonan, R.C.P., eds., 2013. Accidental and Experimental Archaeometallurgy. London: The Historical Metallurgy Society Ltd, pp.99-106.
Tylecote, R. F., 1986. The Prehistory of Metallurgy in the British Isles London. Institute of Metals.
Tylecote, R.F., 1992. A history of metallurgy 2nd ed., London: Institute of Metals.
Tylecote, R. and Merkel, J., 1985. Experimental smelting techniques: achievements and future. In: P. Craddock and M. Hughes, eds., 1985. Furnaces and Smelting Technology. London: British Museum Press, pp.3-20.
Tylecote, R. F., and Wynne, E. J., 1958. An experimental investigation into primitive iron-smelting technique. Journal of the Iron and Steel Institute. 190, pp.339-348.