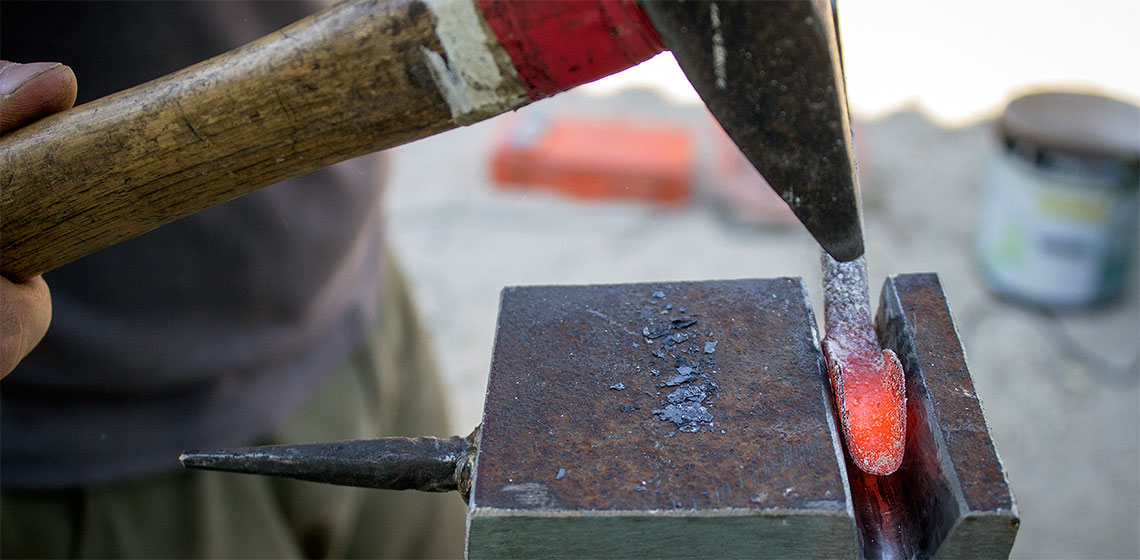
This paper relates to a study of experimental archaeology, executed by Ruben Cataldo, about the forging methods used to produce some replicas of two metal points found during the archaeological excavations carried out between 1992 and 1996 by the University of Salento in the medieval village Quattro Macine (translated Four Millstones), located in the municipality of Giuggianello, a small town in Southern Apulia (South-East Italy). This study has been made by forging several replicas of these two particular finds, describing the step by step forging process of both artefacts. The study also focused on the interpretation problem between arrowheads and crossbow bolt heads, reflecting on the differences between the two types of weapons, and trying to formulate an idea of how to properly interpret the artefacts, to guarantee a certainty on this kind of analysis. The interesting thing about these two points is that not many similar finds have been discovered in the whole area, and none have been found in rural settings like Quattro Macine. For this reason, this study has been made with the aim of trying to understand whether these heads were forged in situ or if they were imported products, and moreover to understand why the village’s inhabitants needed them (Cataldo, 2017).
Introduction
The bow and the arrow are amongst the most ancient weapons created by humankind more than twenty thousand years ago (Rausing, 1967). The most common bow in Europe was the so called Longbow, or self-bow, which is made from a single wooden stave. The wood most used is yew due to its extraordinary mechanical properties, but many other taxa were used in the past, probably according to the availability of materials in each area. Yew was the most used wood, and has been proven by several finds throughout Europe. The most symbolic finds are the 39 bows from Nydam (III – V century AD, Danmark), and the 167 bows from the wreck of the Mary Rose (1545 Great Britain). This study is specifically focused on the only metallic part of this weapon, the arrowhead. Just like the bow, even this element has been subjected to improvements over time, and it assumed the most diverse shapes and sizes depending on the functions for which it was conceived, but the majority of types had a common goal: the best penetration possible. To achieve this, it was necessary to work mainly on the force-to-weight ratio between bow and arrow: the stronger the bow becomes, the more robust and heavier the arrow will be, and the arrowhead plays a decisive role on this factor, being the balancing element of the whole projectile. Therefore, the blacksmith’s work was really important because the arrowheads had to be as high performing as possible in relation to the size of the arrow.
Analytical studies relating to the functioning and functionality of historical bows and arrows are still a topic in the writing phase, since for a long time scholars stopped and limited themselves to typological and iconographic studies, and a practical thought has given to the study of these tools only in the last decades.
The experimental study covered in this article reflects on elements that come before the use of the weapon itself, namely data that deal with the production of their components after the advent of metal. Indeed the element on which attention has been focused is the only metallic part of these weapons, which is the arrowhead. The forging work of an arrowhead was really important, since it had to be as effective as possible in relation to the arrow’s weight and the bow’s strength.
This analysis takes as its object of study some metal points found in the medieval village Quattro Macine in Southern Apulia, Italy (See Figure 1), during the archaeological excavations carried out between 1992 and 1996 under the direction of Professor Paul Arthur (1996).
The survey performed is both typological and functional, and it starts from the production of the points themselves, which have been reproduced as faithfully as possible, observing the production process step by step.
The goal of this experimentation is mainly to understand whether these tips were arrowheads or crossbow bolts, and if it is possible that these objects were made by a blacksmith who lived in the village, or if these items were imported from outside the site.
The archaeological context
Located on top of one of the Salento hills (long karst hills formed by red soil rich in iron and limestone outcrops), at ca. 105 m.a.s.l., the Quattro Macine farmhouse occupied an area of approx. 2 ha and it was located in the middle of an area characterized by the occupation of other medieval villages, now municipal centres, one of which is Otranto.
The village is attested for the first time by 13th century sources, which assert the concession of the Quator Macinarum farmhouse to the Archbishop of Otranto by King Frederick II, Holy Roman Emperor. The farmhouse is also mentioned by King Ladislaus of Naples in 1400 among several villages damaged during his conquest of the Principality of Taranto and the County of Lecce. However, the village remained populated until the end of the 15th century, when it was definitively abandoned probably as a result of raids by the Ottomans (Bruno, 1996).
Archaeological data acquired during the excavations demonstrate a prior period of development, and successive radiocarbon dates allow the origins of the housing nucleus to be placed around the eighth century AD.
The discovery in the northern part of the village of two round holes in the ground is worthy of attention, as they contained fragments of brick roofing. In the same pits there were ash and traces of combustion and this suggests that it was an oven for firing pottery. It is probable that this space was an area of handicraft production, since fragments of metallic slags have been found near these holes (Arthur and Gliozzo, 2005, p.377).
METHODS AND MATERIALS
Analysis and methods
The methodology used to carry out analyses on the production of arrowheads is of a practical-experimental nature, as these metal points have been faithfully reproduced with the forging method, starting from the raw material (mild steel) until obtaining the finished artefact.
An important factor is the working time that is the duration of the entire manufacturing process, which is strictly linked to the type of head, since the forging phases and the methods vary according to the shape and size of the arrowhead. The practical approach in this analysis is considered fundamental because when an object of the past is reproduced, with techniques and technologies of the past, it must be done with the same way of thinking as that of the man of the past. This is because, during the manufacturing process, it is easy to meet the same problems of a practical nature that the past craftsman met, in this case the blacksmith of the period to which these technologies belong. Therefore, the modern thinking of mass-produced, and large-scale mechanical production has been abandoned to adopt that of manual production, in which the main objective is the maximum functionality of the artefact.
Forging process
The forging process is the method by which the replicas of the points from Quattro Macine have been manufactured. It consists of a working process based on the shaping of metals, or metal alloys, as in this case steel, by high temperatures and hammering. The high temperature is the means by which the metal becomes more malleable, and consequently it can be more easily deformed.
The optimal temperatures for steel forging are those in which its crystalline structure changes into austenite crystals and this occurs in a temperature range between 1000°C and 1200°C. These temperatures can be reached with the correct supply of oxygen to the combustion in the forge. As the quantity of oxygen increases, the combustion increases as well and, in turn, the temperature. In ancient times the only way for a blacksmith to understand that the material was in this phase was obviously the appearance because at these temperatures the steel assumes a very bright yellow-orange colour (See Figure 2).
The hammering is the peculiar action through which the metal is deformed and shaped as desired by the blacksmith thanks to the impact of the hammer against the workpiece, held on the anvil, a block of very hard steel. This action does not consist, as many erroneously think, in a rough work represented by hammering randomly on the piece, but, on the contrary, it is an extremely complex process, consisting of hammering with intensity of strength and direction intentionally calibrated. This is the same for the choice of the hammer’s shape and weight, it has to be carefully chosen, according to the type of shape, or deformation, which the blacksmith wants to obtain from the piece worked.
Materials
With regard to the materials used during the analysis, it is appropriate to start from the substance of composition of the points under examination, the steel. In reference to this material, it is necessary to make a terminological-conceptual clarification. The type of steel used is the one that is commonly and erroneously named "iron". Iron, actually, is a metal that is found in nature in the form of minerals, consisting of compounds (mainly oxides), so it is never found in the elemental state. The dark and opaque solid, commonly called iron is the so called “mild steel” that is totally different from mineral iron for the simple fact that it is not a metal, but a metal alloy, more precisely an iron-carbon alloy, made of cementite crystals, a particular iron carbide (formula Fe3C), consisting of an orthorhombic crystal structure. This is the most common steel used since ancient times for its extreme workability due to the carbon content in the alloy, between 0.05% and 0.25%.
Furthermore, an important element is the fuel for the combustion inside the forge. Generally, the most suitable fuels to use in the forging process are two: wood, or charcoal. The difference between the two fuels is considerable and this also influences in a substantial way the production process because of the different calorific power they possess. This substantial difference impacts two aspects in the course of production: time and quantity. That is to say the time it takes to reach optimal temperatures to make the steel malleable and the necessary fuel quantity to allow it to happen.
Obviously, in ancient times, their use always depended on the availability in the local territory. It is known that the extraction of fossil coal is not attested before the Late Middle Ages in Northern European countries, so this makes its use in Quattro Macine somewhat unlikely. For this reason, it was decided that the most appropriate fuel to use was dry wood.
EXPERIMENTATION AND REPRODUCTION
Composition of the arrow
The arrow consists of four main parts: the shaft, the fletching, the nock and the arrowhead.
The shaft is the true body of the weapon, being the main component. It can be built with various profiles, even if the most common form is the cylindrical one (linear profile) and can take different dimensions (diameter and length), based on the archer’s needs, the bow strength, and the type of arrowhead that is mounted on it. Its length varied for each archer, since each archer has a different draw length and this measure usually hovers around 28-32"(71.12-81.28 cm). These dimensions were found in most of the undamaged shafts found in 1971 inside the wreck of the Mary Rose, flagship of the fleet of Henry VIII, sunk near the Isle of Wight in 1545 (Soar, 2006, p.35).
The fletching, located on the back of the shaft, has the function of stabilizing the flight of the arrow and defining its trajectory. This element usually consists of three or four feathers of various shapes, even if the most used is the triangular shape, placed on the shaft using adhesives at an angle of 120° (in case of three feathers). The fins are obtained from the remiges feathers of the wings of big birds, mainly goose and swan, for their characteristic wide dimensions and rigidity.
The nock is a cut in the rear end of the shaft (the cut must always be perpendicular to the wood’s growth rings), or it can be an additional element of wood or other harder material (oriental arrows had nocks made of harder wood, or bone). This element has the function of securing the arrow to the bow string for a greater control during the shooting action.
The arrowhead, which is the element studied in this dissertation, is the key component of the whole weapon, as it is the main part designed to create the damage through the penetration into the target, as well as to perform the balancing action of the whole body of the arrow by means of its weight.
Arrowheads: development and use
While the other parts of the arrow have kept almost the same structure and shape since the moment of its invention, the arrowhead, being a key element, has undergone innumerable changes due to the human experimentation that adapted shapes and dimensions based on the purpose which it was to accomplish. Indeed, since this weapon’s dawn, man has manufactured arrowheads of different materials (flint and obsidian, antler, bone, and metals) and of different appearance.
Arrowheads can be divided into two large groups: war heads and hunting heads. War heads were usually characterized by a tip of reduced size, and prismatic shape. This is because the targets were enemy warriors who wore different protections, such as gambesons, lamellar armours, plate armours and chainmail, through which the arrows had to penetrate as much as possible in order to neutralize the enemy. The prismatic shape was for these projectiles the most suitable for the best penetration through any kind of armour. It is no coincidence that the arrowhead most used in the battlefield, already in the early medieval period, as well as for the easy fabrication, was the bodkin point (Ward Perkins, 1940, pp.66-70), characterized by a prismatic and square section tip.
Instead, the hunting heads were made of larger dimension tips (often called broad head), usually flat, forming a double-edged blade to which could be added barbs in the case of large prey and these elements were well sharpened. These characteristics are due to the fact that the aim of these points was primarily the easy penetration of the animal’s skin and meat, the large dimensions caused a larger wound. This allowed the hunters to catch their prey in an easier way; they just had to follow the animal until its death.
Arrowheads from Quattro Macine
The elements forged for this experimentation are replicas of heads 2 and 4 (See Figure 3) found in the medieval village Quattro Macine. These are both socketed heads and they have prism shaped tips (or bodkins), so they are definitely fighting heads. Head 2 has a triangular section bodkin and it has a total length of 48 mm, and a socket diameter of 8.8 mm, while head 4 has a long square section bodkin and it has a total length of 116 mm, and a socket diameter of 7.4 mm.
Tools employed during the forging process
The equipment used during the forging and finishing phases is of fundamental importance for the production of the heads analysed.
As far as the forge is concerned, unfortunately, there are no typological studies on forges and furnaces so far, because they have a difficult archaeological identification and interpretation (Berna, et al., 2007, pp.358-373.), so it has been built using clay and stones, as a lenticular and double opened structure, following technological and archaeological guidelines (D’Oronzo, et al., 2008, p.371).
The anvil is equally important as well, the support on which the workpiece is placed and on which the hammering action is done. The one used during the forging process is a double horned anvil produced in Germany by the Refflinghaus company in 1959. It is made of eight forge welded components, it has considerable dimensions: a weight of 704 lb (320 kg), a height of 35 cm, a maximum length of 95 cm and a maximum width of 17 cm, for a total processing area of about 1140 cm2, a quite wide surface that favours a very manageable job. Several hardy tools were used together with the anvil during the experimentation.
In addition to these tools, two hammers were used, respectively weighing 800 g and 500 g, as well as various tongs for specific processing steps. Hammers of different size are necessary for roughing and finishing phases.
Productive process of the arrowhead’s replicas
The raw element from which to start to forge an arrowhead is, in this case, a 600 mm long, and 10 mm diameter round bar. The first component that is forged is the socket. The piece is held with the heated end facing the blacksmith. Since the hammer strikes are intense and fast, the metal flattens out and cool very quickly, thus, in this initial phase it is necessary to heat the piece several times. The end of the bar is hammered until it reaches a thickness of approximately 1 mm, at which point this part assumes a flat “spoon” shape (See Figure 4). From this phase on, it is absolutely important to be careful about the piece heating which, due to the very low thickness, heats up very quickly and if it is left in the forge for too long, the temperature becomes excessive, and the metal risks burning, making lose its mechanical properties. Further flattening of the edges of the spoon is necessary because the socket is formed by the overlap of these, which means these together have to be as similar as possible to the rest of the thickness of the socket. To close the spoon a hardy tool is used, which has at one end a concave groove 25 mm deep and 20 mm wide, terminating at the bottom with a 12 mm diameter semicircle. The opposite end, on the other hand, has a 65 mm long taper with a 12 mm diameter at base (which is used to finish the inner surface of the socket). Placing the spoon on the groove, it is gently pushed by the hammer cross peen, making it sink into the groove, giving it a U-shape (See Figure 5). The process proceeds by creating the overlap of the two ends of the U shape, the same flattened parts that have been previously described. It is made by folding the edges inward which overlap one over the other. Thus, an annular shape is obtained (See Figure 6). To close the socket properly, the annular shape is literally rolled by rotating and delicately hammering it. This movement allows the socket to be tighten, producing a progressive narrowing in the diameter along the whole extension, creating the typical conical shape. The arrowhead’s shoulder is formed by creating an opposite taper to that of the socket (See Figure 7). After cutting the socket and the shoulder out from the rest of the bar with a hardy tool, it is possible to forge the tip. In order to forge the long square bodkin, the flat surface of the anvil can be used (See Figure 8). The triangular bodkin is forged by means of a hardy tool which consists of a cubic element (50 mm wide) which has running across the entire working surface a 12 mm wide and deep furrow with a regular triangular shape, in other words it forms an angle of 60° in which the bodkin is hammered (See Figure 9). The last and fundamental manufacturing phase is the heat treatment that is the hardening. It consists simply in heating the piece until it is bright orange, and then quenching it in water. As already illustrated, by heating the piece to a temperature between 1000° C and 1200° C, the crystalline structure of the steel changes to that of austenite, thanks to the acquisition of a greater quantity of carbon. When the material is cooled rapidly, it does not have time to release the absorbed carbon atoms, as would happen in a gradual cooling; these carbon atoms remain trapped in the crystalline structure. This increase in the amount of carbon in the surface layers of the metal gives it a significantly greater hardness and mechanical resistance than the untreated material. To finish the heads, it is sufficient to make finishing touches, grinding possible material excesses, or asymmetries (See Figure 10).
Experimental results: use and functionality
During the work the fact that in the Late Middle Ages, arrowheads could have been made in different ways was taken into account, based on the context and the situation (Wadge, 2007, pp.262-264). During this period, in wartime there was the necessity to produce considerable amounts of arrowheads, noted especially in British contexts where there was a very consistent and specialized corps of archers. A significant example of this is the order made by King Henry VIII in 1510 to the Republic of Venice for the incredible number of 40 thousand staves for the construction of war bows. These staves were specifically of yew wood (Taxus baccata) from the Alps, the best wood with which an English war bow could be made, for the excellence of its qualities in terms of strength and elasticity that gave, as a final result, bows of such massive force, that were able to make the arrows fly over 200 yards (about 183 m). During the military campaign launched in the context of the Hundred Years War by King Henry V, which culminated with the British victory at the battle of Agincourt in 1415, a transport of one and a half million of arrows was recorded. Such an amount presupposes a huge number of hours of work by the smiths at the service of the Crown, consequently there must have been specialized forges. In such a situation, it was necessary to produce as much as possible in the shortest time possible, thus it is plausible to think of an equally considerable work force. For this reason, presumably the fabrication itself had to be optimized by dividing the roles between the smiths. Therefore, it is easy to think that some forges were commanded to stop producing anything else, to be hired to make arrowheads only. In such situations, the smiths had to work on many bars at the same time to reduce the waiting time between a heating and the other. We can imagine that there were workers that powered the bellows continuously, making the forges heat more and more pieces. Such statements are just speculative, because we do not have documents that attest such facts. That could be because, on the contrary of bowyers, and fletchers, there were no “arrowsmith” guilds. Blacksmiths were simply blacksmiths, and they worked any kind of metal items. Nevertheless, the division of tasks between hammering, and heating is very plausible, because it could be the only solution to obtain optimized working times. However, in a rural context, or at least in peacetime, the situation would be quite different. The forging process of arrowheads could have been made in a much less intensive way, and the work could have been carried out by just one blacksmith. Taking this into account, during the experimentation the hammering phase was timed separately from the heating phase because, considering a production with optimized times, as said, the heating time is separate from the hammering time. In this way, no blacksmith had to wait for the piece to heat up, because as soon as he finished forging one, he immediately had another heated and ready to be worked. This allowed an estimation of the whole process, adding heating, hammering, and finishing times, between 10 and 15 minutes, confirming the estimations made by Mark Stretton (archer and master blacksmith specialized in forging arrowheads) during his experiments (Stretton, 2006, p.121). For the hammering times an average duration of around 7 minutes was verified, and since this time is much shorter than the added phases, we can think that an intensive production as the one described before had to be objectively better and preferred during the preparation of a military campaign.
On the typology of the analysed heads, there is no doubt that they are weapons destined for use in war, according to the fact that they have small prismatic tips. Nevertheless, a technical reflection is necessary concerning the distinction between arrowheads and crossbow bolts, focusing on the triangular bodkin. Very often scholars tend to interpret this head as a crossbow bolt rather than an arrowhead for the simple reason that it was the most widespread shape in Europe among crossbow bolts during the 14th century, but actually, the interpretation is not that simple, because pondering only the shape of the tip is not sufficient at all. It is necessary to consider the size of the whole point (De Luca and Farinelli, 2002, p.476). At the same poundage between a bow and a crossbow, the crossbow bolt must be equal in resistance (the stronger a bow is, more high is the potential compression breakage for the projectile), and weight (as said, the force-to-weight ratio between bow and arrow is extremely important, and it is the same for the crossbow bolt) to an arrow that bears such force, or be similar in any case to have a good balancing, and a flight as linear as possible. Since the bolts are undoubtedly inferior in length, they must compensate with the other measurements, the shaft diameter and the head size. Considering that the socket diameter must be equal to the shaft part on which is mounted, the crossbow bolts will have a much more substantial shaft compared to that of an arrow and the head will be unequivocally larger. In reference to previous periods in which the crossbow was not yet so strong, the diameter of the bolts could be equal to that of the arrows, so the classification is not always possible, based on the diameter of the socket. However, it should be noted that the size of the bodkin of head 2 from Quattro Macine is significantly smaller. Considering that the socket diameter of heads 2 and 4 from Quattro Macine were between 8 and 11 mm, and taking into account the really small size of head 2, we can think of identifying both of them as arrowheads. This interpretation finds a match in contexts in which the use of both weapons is attested, not only from archaeological findings, but also from documentary sources, and the triangular bodkin is present in the form of both arrowheads and crossbow bolts. These sources are archives of 13th and 14th century AD from Pisa and Orvieto, together with other records in southern Tuscany (De Luca and Farinelli, 2002, pp.457-459; De Luca, 2003, pp.403-409). The heads analysed find further comparison in the London Museum Medieval Catalogue, both in terms of shape and date. Indeed head 2 from Quattro Macine corresponds to type 11, dating back to the 14th and 15th centuries AD. Head 4 corresponds to type 7, dated between the 13th and 14th centuries AD, not only in the British Isles but also in Scandinavia (Ward Perkins, 1940, pp.68-70.). The same type of head corresponds to the M10 type of the Jessop’s catalogue, in which the M letter represents the Military type, that is to say arrowheads made specifically for military purposes (Jessop, 2002, pp.194-199). It should be emphasized, however, despite keeping the idea that these finds are arrowheads, that an element of doubt must be left on this interpretation, because of the lack of data concerning the dating and the position of these finds (if inside or outside the village walls).
Regarding the conservation state of the arrowheads, unfortunately the effect of oxidation is very evident because some parts are not completely intact, especially on head 4, which is badly damaged. It can be seen by comparing the weight of the two finds with that of their replicas. Head 2 has a weight of 6 g, while the respective replicas have, on average, a weight of around 12 g. Head 4, which is the most damaged find, has a weight of 10 g, instead the corresponding replicas have an average weight around 20 g, so both heads have lost about half of their mass. Having made reproductions of these findings, therefore, has allowed appreciation of the original appearance as well.
Conclusions
The experimental study and reproduction of the two arrowheads found in Quattro Macine has given the opportunity to understand different aspects relating to the heads themselves, to their production method, as well as to consequential reflections on some dynamics of the village.
First of all, it is necessary to take into consideration that between the 14th and 15th centuries, arrowheads were manufactured with shapes destined for well-defined purposes. The fighting heads, indeed, had been clearly distinct from those for hunting use for at least two centuries, unlike during the early Middle Ages in which the leaf shaped heads were predominant and multifunctional. As seen, the arrowhead types found in Quattro Macine were widely known, distributed, and used in the same period throughout Italian and European territory. Considering that even a rural context such as Quattro Macine could have had a village blacksmith, it is plausible that these items were not imported, but made in situ, and part of the many different works of a blacksmith. We can assert this for several reasons. First, the production of arrowheads of these types is far simpler than that of other shapes, besides the fact that it only takes a few minutes to make them, and we have to take into account the simplicity of the forge construction as well. Indeed, among the metal finds discovered, there are fragments of blades, laminae and numerous nails. A confirmation of this is the discovery of metallic slags near to two circular holes with evident traces of combustion, which attest the metal working activity in the village. The production, and the use of these heads could have been caused by the fact that the village was a plentiful centre of agricultural activity. Consequently the inhabitants could have opted for the use of bows and arrows not only for hunting activities, but also to defend the village from possible thefts, or even raids, especially in difficult times such as those of the Angevin conquest and the Ottoman raids between the end of the 14th century and throughout the 15th century AD. Furthermore, these periods represent precisely the last days of the village’s activity, before its definitive abandonment.
With regard to the arrowheads, this analysis has allowed us to elaborate a more concrete idea on the recognition of the two finds, but unfortunately without being able to assert certainty. The most plausible identification is that the two objects are arrowheads, both from a dimensional point of view, and from the absence of finds of other items attributable to the crossbow. Besides, reflecting on the fact that during the Middle Ages the costs of bows and arrows were inferior, they can be considered much more appropriate than the crossbow in a rural setting like that of Quattro Macine. The uncertainty of this interpretation is due to the disconcerting lack of data related to the discovery of these archaeological finds. There is an extremely approximate stratigraphic location, the total absence of topographic relief points and, consequently, the lack of a certain dating, and all of this can only cause a big interpretative confusion on the finds themselves and, consequently, on the archaeological site. Therefore, the experimentation reported proposes the hypothesis of the use and production of bows and arrows within the village, and this can only be a spur to carry out further research, acquiring more concrete data, in order to have a more solid vision of how life was at Quator Macinarum.
Bibliography
Arthur, P., 1996. Masseria Quattro Macine – A deserted medieval village and its territory in southern Apulia: an interim report on field survey, excavation and document analysis. Papers of the British School at Rome, LXIV, pp.180-237.
Arthur, P. and Gliozzo, E., 2005. An archaeometallurgic study of Byzantine and medieval metallic slags from southern Apulia. Archeologia Medievale, XXXII, pp.377-388.
Berna, F., Behar, A., Shahak-Gross, R., Berg, J., Boaretto, E., Gilboa, A., Sharon, I., Shalev, S., Shilstein, S., Yahalom-Mack, N., Zorn, J. R. and Weiner, S., 2007, Sediments exposed to high temperatures: reconstructing pyrotechnological processes in Late Bronze and Iron Age Strata at Tel Dor (Israel). Journal of Archaeological Science, 34, pp.358-373.
Bruno, B., 1996. La chiesa bizantina a Giuggianello, casale Quattro Macine. In: G. Bertelli, ed. 2004. Puglia Preromanica, dal V secolo agli inizi dell’XI. Jaca Book. pp.278-279.
Cataldo, R., 2017. Analisi archeometallurgiche a Quattro Macine. Punte di freccia: diagnostica e metodi sperimentali di produzione. Università del Salento, Dipartimento dei Beni Culturali, C.d.L in Beni Archeologici, Rel. P. Arthur,
De Luca, D. and Farinelli, R., 2002. Archi e balestre. Un approccio storico-archeologico alle armi da tiro nella Toscana Meridionale (secc. XIII-XIV). Archeologia Medievale, XXIX, pp.455-487.
De Luca, D., 2003. Le armi da tiro nella Rocca di Campiglia Marittima. Frecce per arco e dardi per balestra. In: G. Bianchi, ed. Campiglia. Un castello e il suo territorio II. All’Insegna del Giglio S.a.s., pp.397-413.
Jessop, O., 2002. A New Artefact Typology for the study of Medieval Arrowheads. Medieval Archaeology, 40, pp.192–202.
Rausing, G., 1967. The bow: some notes on its origin and development. Rudolf Habelt: CWK Gleerups, 1967.
D’Oronzo, C., Marinò, G. P., Solinas, F. and Fiorentino, G., 2008. Archeobotanica ed archeologia sperimentale: bilancio termico, modalità d’uso, tafonomia e visibilità archeologica di un esperimento in margine al workshop di Cavallino. In: C. Giardino, ed. 2011. Archeometallurgia: dalla conoscenza alla fruizione, pp.371-376.
Soar, H.D., 2006. Secrets of the English War Bow. Westholme Publishing: Pennsylvania.
Stretton, M., 2006. The development and manufacture of military arrowheads. In: H. D. Soar, ed. 2006, Secrets of the English War Bow. Westholme Publishing: Pennsylvania, pp.102-126.
Wadge, R., 2007. Arrowstorm, the world of the archer in the Hundred Years War. Stroud: The History Press.
Ward Perkins, J. B., 1940. London Museum Medieval Catalogue, London. pp. 68-70.