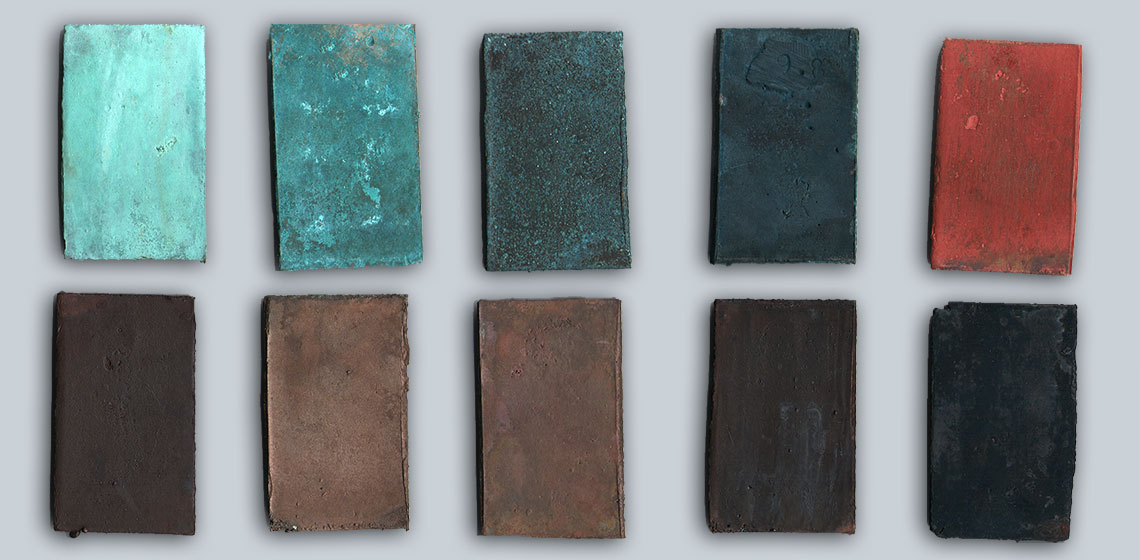
Bronze is an alloy of copper and tin, with lead also added. Hellenistic and Roman bronze objects have a variable percentage of metals, and because of this the colour of the alloy will differ depending on the proportions. The colour of the alloy can be maintained by polishing, but it is also possible to give a patina to the surface of bronze using a reagent. Other metals and alloys (copper, silver, gold, Corinthian bronze) can be inlaid by damascening, or by plating to create polychrome decorations. Unfortunately, copper alloy materials recovered from archaeological sites suffer from the effects of time and deposition, which may lead to corrosion and discolouring of the surface, often appearing green or brown. Archaeological bronzes also may suffer from overly aggressive restorations which scour original surfaces or cover them with a layer of paint imitating green corrosion. The collection of swatches I created gathers the spectrum of colours of antique bronzes, and allows for a restoration the original colours of the objects of my study: Greco-Roman bronze furniture. This study combines the processes of the lost wax method and the addition of polychrome bronze surfaces (patina, inlay and gilding). Some platelet samples from this collection of swatches have also been analysed to determine their elemental composition and their patina, so as to compare them to archaeological materials. Initial results suggest that the colours of bronze luxury furniture vary greatly, and that the spectrum of colours is a product of bronze alloy composition, and of the techniques used in finishing the surface, either polishing or patina application.
As part of my thesis, entitled The colours of bronze ceremonial furniture in the Greco-Roman world, 200 bc – 200 ad: from technical characterization to symbolic values, and in addition to a techno-typological corpus of luxury bronze furniture and a corpus of literary sources referring to the colour of antique bronzes, I have developed an experimental archaeology project to create a collection of swatches of the spectrum of colours of antique bronzes, to understand the chaîne opératoire of foundry element manufacturing, and for the restoration of original colours of Greco-Roman bronze furniture. The chaîne opératoire is a concept defined for the first time by the French Prehistorian André Leroi-Gourhan (1911-1986) to analyse all the stages of the process of making and using an object (de Beaune 2000). The collection of colour swatches can also be helpful in restoration work with the data of physicochemical analyses.
My thesis explores the history of both techniques, arts, and mentality. It employs archaeological, archaeometric and sociological methodologies. Using context, techno-typological study, physicochemical analysis, and digital imaging, it puts colours back into the discussion of luxury bronze furnishings. The aim of this research is to characterize the specificity and originality of the use of bronze as a custom of Greco-Roman elite, the owners of this ostentatious furniture.
The chronological parameters of my research are defined by archaeological discoveries, by the evolution of customs, and by the political and military events that played a major role in the emergence and development of Hellenic-inspired furniture in Rome. Livy’s History of Rome (Ab Urbe condita libri, XXXIX, 6) and Pliny the Elder’s Natural History (Naturalis Historia, XXXIV, 8, 14) tell us that the Roman discovery of these luxurious furnishings takes place during the triumph celebrating General Cn. Manlius Vulso’s victory in the campaign against the Galatians in 187 bc. They further enhance them with polychrome decoration to increase their ostentatious value until the second century ad, when the taste for visual effects and for coloured metal contrasts fade gradually for chromatic drapery.
The geographical area of my study is linked to this timeline and corresponds to the Roman conquest. These victories lead to the creation of several provinces in the Mediterranean basin, and to the foundation of the Roman Empire in 27 bc, further emphasizing the political and cultural unification of the Mediterranean. The gradual acculturation of “the Greek world” as a result of Roman expansion is evident in a study of this furniture, its colours, and other treatments using the same historical perspective defined by Paul Veyne as: “Un Empire où la culture était hellénique et le pouvoir romain” (Veyne 2005, page number?).
The sources we can use to identify and understand polychrome decorations are textual, iconographic, and material. For the latter, it is most useful when employed in archaeometric analyses to determine the elemental composition of alloy and other inlaid metals. Textual sources come mainly from Greek and Latin authors, as well as Egyptian sources such as Zosimos of Panopolis (Mertens 1995; Giumlia-Mair 2002; Hunter 2002; Muller-Dufeu 2006). Some authors describe and occasionally criticize the luxury of their society and thus provide information about the decorative elements present in their time. Others authors explain, in a mythological or technical discourse, the manufacture of bronze and the processes of surface treatments. The iconographic sources are essentially vase or wall paintings and decoration in bas-relief. As for the scenes showing activities related to the metallurgy of bronze, they are very rare. Such as twopaintings: one on the exceptional Attic Red-Figure kylix, the ‘Berlin Foundry Cup’ dated to the early fifth century bc (inv. F2294); and the second, on the Attic Red-Figure Nolan amphora of the Museum of Fine Arts of Boston (inv. 13.188), also dated to the early fifth century bc. Both Attic Red-Figure vases were discovered in Etruria, respectively Vulci and Suessula. They predate my study period however because of their exceptional nature and small changes in the chaîne opératoire of manufacture of antique bronzes, I rely on their painted decoration to explain the different activities related to the production of bronze artefacts. The third type of source, the archaeological material, includes all bronze furniture elements with one or more polychrome decorations produced in the Mediterranean basin (circa 500 listed objects): lecti tricliniares with fulcrum, bedframe and baseboards, tables, tripods, candelabras and lamp holders, lamps, chests, and censers.
Antique bronze is a binary alloy of copper and tin. It can also be ternary, with the addition of lead. Corinthian bronze is an alloy of copper, silver and gold, highly regarded by the ancients (Giumlia-Mair and Craddock 1993; Craddock and Giumlia-Mair 1995; Mattusch 2003). Bronze is unstable and seeks to stabilize with its surrounding environment. It naturally tends to return to its initial state of ore. For this reason, archaeological objects reflect the passage of time and their deposition, and are regularly covered with concretions and dull corrosion (natural patina). Bronze may also suffer from overly aggressive restoration which scours the original surface or covers it with layers of paint that imitates the ‘antique green’ colour. In reality, however, bronze has a variety of colour shades that are dependent on alloy composition, and particularly on the percentage of tin present. The surface colour can be changed or completed with treatments, such as damascening, gilding, or patination (Pernot 1994; Descamps-Lequime 2006; Ferro et al. 2013; Formigli 2013a).
To study such variety, I have developed a collection of colour swatches. The colour palette is an important research tool in this historical study, and is closely related to physicochemical analyses. It permits identification and appreciation of the spectrum of copper alloys, patinas, and other surface treatments through colour representations. It is in line with the research work of Richard Hughes and Michael Rowe for fine metalwork (Hughes and Rowe 1991), the study of François Mathis on patina from Japanese receipts (Mathis 2005, 277-294), the research of Markus Binggeli and Myriam Krieg on bronze beds of Avenches (Duvauchelle et al. 2013, 107-108), and the experimental work directed by Edilberto Formigli on the polychrome reconstruction of the Roman bronze statue of an ephebe at the Archaeological Museum of Florence, known as Idolino of Pesaro (Bertelli et al. 2013). Archaeological experimentation was carried out in collaboration with a fine metalworker, Laurent Inquimbert, and his team. In 2015 he became ‘Meilleur Ouvrier de France’, option Art Foundry – lost wax. He has provided me with access to his workshop, named Delta 960° and located in Carcès (Var, France), and the professional skills necessary to create a collection of swatches. As regards to archaeometric analyses, XRF Spectrometry and XRF Imaging, they were carried out by the chemical researcher Matthias Alfeld associated with the Laboratoire d’Archéologie Moléculaire et Structurale (LAMS, UMR 8220, CNRS, Pierre and Marie Curie University, Sorbonne Universities).
The alloys of this collection of colour swatches are based on the elemental composition of objects of my corpus. The elemental compositions are known through physicochemical analyses conducted as part of different studies and publications (for example Piccot-Boube 1960; Walter 1976, 230-232; Boucher 1982, 192; Baudoin et al. 1994, 125-132; Stock & Giumlia-Mair 2002, 562; Ventura & Giumlia-Mair 2002, 556; Mattusch 2003, 220-221; Kaltsas et al. 2012). Recipe ingredients and application methods used to produce patinas were selected from the results of archaeometric analyses (for example Hellenkemper Salies 1994; Mathis 2005, 269-270), ancient literary sources (for example Halleux 1981; Hunter 2002), and hypothetical study.
The hundred platelets of collection of swatches were numbered for classification. Method used comprises a first number, from one to 11 corresponding to a type of alloy, and a second number, from one to 11 corresponding to a recipe of patina (See Figure 1). The classification by number allows for the expansion of colour palette. The colours obtained through experimentation were measured by colorimetry with the Soil Color Charts of Munsell (Munsell 1975), a system of colour matching in three colour dimensions. Its three components include hue for the shade of colour, value for lightness, and chroma for colour strength.
Experimental archaeology is a scientific approach aimed at the reconstruction of techniques, and more particularly in the case of this study, in the process of making bronze with lost-wax and the decoration process in connection with polychromy. Experimental archaeology consists of three essential and complementary approaches: observation, reconstruction, and comparison between the results obtained by the experiment and the archaeological objects. It therefore is used to test functional hypotheses. It provides technical information but of course has its limitations due to the lack of cultural context and the lack of experience (Reynolds 1994; Reynolds 1999). All of my tests were carried out with contemporary materials, but nevertheless, I focus as much as possible on simple and natural materials that are similar to those utilized at the time. I also recognize depth and breadth of techniques required for the manufacture and decoration of platelet samples. Despite the guidance of a professional, I do not have his years of experience, and I am thus confronted with technical and knowledge limitations, especially with regards to patinas.
The present article is based on the various steps required for the manufacture and decoration of bronze platelet samples of the collection of colour swatches.
Methods: making bronze platelet samples
From modeling wax to refractory casting mould
The chosen technique is lost-wax casting (Rama 1995), except for Corinthian bronze which is simply cast in a mould and hammered. The lost-wax method was used widely in ancient times to make bronze objects. In his Periegesis, Pausanias mentions that the method of casting bronze statues with moulds was invented in the sixth century bc by two Samians, Rhecus and Theodore (Periêgêsis, VIII, 14, 8; X, 38, 6).
The first activity of the assembly of the collection of swatches is to make a hundred platelets in rosin. Rosin is similar to wax with almost the same modelling properties, it softens at a temperature of 90º to 110º Celsius. Platelets are then assembled in packs of ten, with wax on a central axis to form a cluster. The central axis is a rosin ‘jet-master’ with a metal rod for the maintenance and transport of the future mould before firing. The jets allow casting into the mould. A casting pot is added to the top of the ‘jet-master’. Vents can be assembled to evacuate air and gas during the casting. Platelets are arranged downward and obliquely to facilitate the casting of bronze (See Figure 2). So there are ten clusters, each with ten platelet samples.
The second step relates to the production of the moulds that encase the wax models. The mould enables the bronze to be cast and must withstand both the heat of the oven and the pressure of the molten metal. The moulds in my study were made using the Enrobage Réfractaire Mixte (EEM) technique, which uses a refractory material composed of lime and fireclay. The mould has an initial layer on its surface, and six other layers applied successively with a drying time of six hours, at least, between each coating. The thickness of the mould is dependent upon the temperature of the oven, the size of the object, and the pressure from the molten bronze, acting at the time of casting.
The moulds are then placed in an oven with the casting pot down for dewaxing and firing. The firing takes an hour and a half at 750º Celsius. The temperature should rise gradually. At 550ºthe wax sublimates, leaving an empty space to be occupied thereafter by the bronze. After cooling the moulds, the metal rods are removed and minor repairs are performed on the mould with the same refractory material for sealing cracks due to thermal shock to strengthen them (See Figure 3). This action is carried out shortly before the bronze casting to prevent impurities in the hollow cavities of the mould.
Making alloys
Eleven alloys were made according to the bronze composition of my corpus. The first six are an average of alloys that are found among ancient furniture. The first three correspond to binary alloys with a tin content respectively of 8 %, 10 % and 12 %. The other three alloys, numbers 4-6, are ternary alloys. They resume the composition of the first three with the addition of 2 % lead. The four following alloys have elemental compositions unique to ancient objects: Alloy No.7 has 5 % tin and 1 % lead, inspired by the median part of the fulcrum found in Corinth (Mattusch 2003, 220-221). Alloy No.8 is a copper base alloy with 15 % tin and 4 % lead, as known from a Silenus bust-medallion (Walter 1976, 230-232). Alloy No. 9 comes from a fulcrum frame and has equal amounts of 9 % tin and 9 % lead (Mathis 2005, 269-270). And the alloy No. 10 is a leaded bronze with 8 % tin and 14 % lead from a bedframe (Ventura and Giumlia-Mair 2002, 556). The last alloy No. 11 is a Corinthian bronze with 4 % silver and 1 % gold, known from inlays of the median part of a fulcrum (Mathis 2005, 269-270) (See Table 1).
Number | Alloy | Cu | Sn | Pb | Ag | Au | Total (g) |
1 | CuSn8 | 2760 | 240 | 0 | 0 | 0 | 3000 |
2 | CuSn10 | 2700 | 300 | 0 | 0 | 0 | 3000 |
3 | CuSn12 | 2640 | 360 | 0 | 0 | 0 | 3000 |
4 | CuSn8Pb2 | 2700 | 240 | 60 | 0 | 0 | 3000 |
5 | CuSn10Pb2 | 2640 | 300 | 60 | 0 | 0 | 3000 |
6 | CuSn12Pb2 | 2580 | 360 | 60 | 0 | 0 | 3000 |
7 | CuSn5Pb1 | 2820 | 150 | 30 | 0 | 0 | 3000 |
8 | CuSn15Pb4 | 2430 | 450 | 120 | 0 | 0 | 3000 |
9 | CuSn9Pb9 | 2460 | 270 | 270 | 0 | 0 | 3000 |
10 | CuSn8Pb14 | 2340 | 240 | 420 | 0 | 0 | 3000 |
11 | CuAg4Au1 | 28,5 | 0 | 0 | 1,2 | 0,3 | 30 |
Total (g) | 26098,5 | 2910 | 1020 | 1,2 | 0,3 | 30030 |
Table 1. The elemental composition of copper alloys.
Tin is added to improve the castability of the alloy by lowering the melting point and hardens bronze. A bronze with 10 % tin can be easily polished and chiselled, and gives a beautiful patina, while a bronze at 12 % tin is more difficult for working after casting but it is possible (platelet sample 1.3). The addition of lead also improves the castability by lowering the melting point and making the alloy ductile. Greater ductility is beneficial to the work of chasing. Some experimental alloys had an addition of lead, generally less than 5 % except for two specific alloys (See Table 1). It is not usually necessary to exceed 5 % of lead, otherwise it embrittles the alloys by the liquation phenomenon (Rama 1995, 279-280).
Making alloys requires accurate weighing of each metal (copper, tin, lead), cast in a cluster that will result in about three kilos of bronze, with ten platelet samples per alloy.
Casting
A first casting of each alloy is performed to manufacture an ingot (See Figure 4). It is used to refine the alloys to avoid segregation of metals. The metal loading order in the crucible is crucial for the final result. The copper must be introduced first into the hot crucible because it is the metal with the highest melting point, followed by tin, and finally lead. When the ingot has cooled, it is removed from the ingot-mould and numbered (See Figure 5).
Turning now to the main casting, the moulds are warmed in an oven at about 500º Celsius. A hot mould allows for better casting of the molten alloys, because otherwise if it comes in contact with a cold mould the molten alloy would not fill it homogeneously. At the time of casting, the mould is partially buried in sand to prevent the mould from bursting and leaking metal.
Another furnace with a crucible was prepared at the same time for melting the ingot. The crucible is heated above 1000º Celsius. Before incorporating the ingot, pieces of charcoal and glass are added for a reduction firing. They are used to burn oxygen and create an airtight layer on the surface of the alloy during temperature rise. During the temperature rise, the alloy is stirred with tools, usually made from green wood or iron. For iron tools, this is one reason, I think, besides the possible traces of iron in the ore, why there are these traces in archaeometric analyses of artefacts.
When the alloy is molten, it is skimmed by removing the surface layer of carbon and glass. These correspond partially to the slag that is often found on archaeological sites of metallurgical activity. Without pause, after the scour, one removes the crucible from the furnace, removes any remaining impurities and casts the bronze in the mould. The remainder of the alloy is cast in the ingot-mould, and the mould with platelet samples is numbered and allowed to cool.
Cold working
After cooling, the moulds are unchecked (See Figure 6). This activity consists of separating the bronze piece by destruction of its mould with a mallet and a chisel. Then comes the activity of rough grinding. This is to rid the platelet samples of all excess metal that remains: casting jets, burrs, vents. The series of gestures is done using mainly a saw, thus exerting linear percussion (de Beaune 2000). The platelet samples are finally individually numbered.
The platelets are still rough cast at this point. They will then undergo sandblasting, which is an abrasion polishing technique performed with the use of an abrasive (sand) between the material and the polisher (See Figure 7). If necessary, bronze elements are welded together to form the desired object, such as for a great statue. The bronze is finally worked by chasing to eliminate imperfections and casting defects, such as burrs or blowholes. Generally, the chasing is carried out using non-cutting tools, such as a scraper like those represented in painting on the Attic Red-Figure kylix “Berlin Foundry Cup”.
Corinthian bronze (alloy No. 11), an alloy of copper, silver and gold, is highly ductile thanks to the presence of gold. During casting, the molten alloy is very fluid. I achieved only two small ingots of this metal (See Table 1), and by hammering and cutting I produced four platelet samples of one millimetre thickness.
Results: the colours of bronze
The alloys of bronze range in colour from red to yellow (See Table 2). The percentage of tin in the alloys influences the colour changes. The alloy No. 7, which contains the least tin at 5 %, is the reddest, followed in this order of alloys No. 4, No. 1, No. 5, No. 9, No. 2, No. 6, No. 3 and finally alloy No. 8 with 15 % tin, which is yellow (See Figure 8).
Number | Alloy | Colour | Munsell code |
1 | CuSn8 | Light red | 10R 6/8 |
2 | CuSn10 | Reddish yellow | 7.5YR 8/6 |
3 | CuSn12 | Yellow | 10YR 8/6 |
4 | CuSn8Pb2 | Light red | 10R 6/6 |
5 | CuSn10Pb2 | Reddish yellow | 5YR 7/6 |
6 | CuSn12Pb2 | Yellow | 10YR 7/6 |
7 | CuSn5Pb1 | Light red | 7.5R 6/8 |
8 | CuSn15Pb4 | Yellow | 2.5Y 8/6 |
9 | CuSn9Pb9 | Reddish yellow | 7.5YR 7/6 |
10 | CuSn8Pb14 | Pale yellow | 2.5Y 7/4 |
11 | CuAg4Au1 | Red | 7.5R 5/8 |
Table 2. The colours of copper alloys.
The percentage of lead does not have a great effect on the colour of the alloy. Lead slightly darkens the colour. This, however, is not the case with the leaded bronze (alloy No. 10), whose colour is pale yellow. The largest lead content is lower than copper, so the colour of the alloy No. 10turns yellow in contrast to the alloy No. 4 which is light red.
Corinthian bronze (alloy No. 11) has a red colour without patina (See Figure 4, platelet sample 11.1). However, in antiquity this alloy has been presumably patinated with a sulphur solution to give it a black colour on the surface.
The colours alloys are light because the platelets are bright after polishing. The brightness at the surface of platelet samples is due to an important reflection of light.
Methods: surface treatments of bronze platelet samples
After these manufacturing operations, the object can be subjected to one or several decorative and polychrome aesthetic techniques by using surface treatments: finish polishing, damascening, and patination.
Decoration on the wax model
The first surface treatment can be carried out directly on the surface of the wax model. It permits shaping the wax to give it a material effect. This appears on the surface of bronze, creating plays of light due to differences in light reflection and perception by the eye (Coluzza and Formigli 2013; Formigli 2013c).
The techniques used include engraving, smoothing, or picketing as for platelet sample 6.6. The tools are either percussion launched puncture for picketing, or linear percussion for engraving, or diffuse percussion for smoothing (de Beaune 2000).
It is also possible to deform the plasticity of bronze by hammering (diffuse percussion) and by annealing (heat the alloy in the oven and let cool slowly) because of bronze’s mechanical properties – tensile strength, hardness, and elasticity. Plastic deformation is performed by work hardening, with alloy containing between 2% and5 % of lead being easier to work.
Polishing
To polish is to rub the surface of an object in order to vary or regulate the surface. Polishing is done with fine abrasives so that the bronze surface is lustrous. Pumice is commonly used as an abrasive in antiquity, as well as emery rock from the island of Naxos. The exploitation of emery rock and marble made the ancient city’s fortune. Emery was powdered in grains of different sizes, and it was mixed with oil to polish metals. This activity is represented on the Attic Red-Figure Nolan amphora of the Museum of Fine Arts of Boston: Hephaestus is in the process of polishing the future shield of Achilles. The surface of polished bronze is then waxed to protect it from corrosion and loss of brightness.
Platelets without patina (patina No. 1) were polished with pumice and emery paper. Applied materials create an assortment of stripes more or less fine in the direction of the action of polishing. The more the surface of bronze is polished, the thinner, more proximate stripes will appear.
Much of Greco-Roman bronze furniture was probably finely polished to visually render it brighter.
Damascening
Damascening involves inlaying a metal wire (copper, silver, Corinthian bronze) into the surface of bronze. This technique is known from the Mycenaean period. It creates polychrome decorations.
Damascening nevertheless appears in the bronze furniture that I am studying from the first century bc and in Roman furniture. The decorations are mostly floral, such as acanthus, but also more complex as in the scenes of harvest on the bed of Amiternum (inv. 1074) exhibited at the Capitoline Museums at Centrale Montemartini (Pirzio Biroli Stefanelli 1990, 162-170 and 262; La Rocca 2014, 200 and 212-213;). Inlays are also used to make a figure more realistic and animate. Lips, nipples, and traces of blood appear red copper, and teeth, nails and eyes are silver (Formigli 2013a).
I made a red copper and Corinthian bronze damascened-inlay on the platelet 3.1 (See Figure 8). The actions of damascening consist of the creation of a longitudinal groove with a small bevelled chisel a millimetre thick. This tool removes the metal chips and forms two lips at the ends of the groove. The copper wire is inserted into the groove and retained by hammering. The surface of bronze is finally polished to erase the traces of hammering.
Gilding
Gilding is comprised of applying gold to the surface of bronze, patina or not. Gold is a rare metal, luxurious, very bright, very ductile and non-oxidising. Several techniques were practiced in antiquity for adhering gold to the surface of bronze, such as mercury gilding, or gilding by metal bonding. It consists in dissolving gold in mercury to form an amalgam. The latter is coated on the area to be gilded, then to heat. Under the action of heat, the mercury will evaporate leaving only a thin layer of gold on the surface of the object. There is also adhesive bond gilding, as with gold leaf. In the Greco-Roman era, gold leaf was made by goldbeating and could be as fine as 1- 2 microns thick. It was fixed using a binder to the surface of the substrate, probably of organic nature such as egg whites or oils (Callewaert 2010; Aucouturier and Danque-Ceretti 2012;).
As part of the experiment, I created a gilding with leaf gold on a patinated bronze (See Figure 9). The mixture is an oil-based adhesive. Gold leaf is applied at first by tapping it with a finger – fat fingers allow better manipulation of the gold leaf – and finally with a clean and dry cloth.
The gilding accentuates the shine of the alloy and has a protective effect because it stops the formation of oxidation.
Patination
Types of patina: natural and artificial
Patina is surface coloration of bronze which results from the presence of an adherent layer formed by damage to the metal itself, especially through oxidation of copper (Chaplet 1936; Quentin 2005; Aucouturier 2007; Callewaert 2010; Formigli 2013b). It can occur naturally from exposure to the actions of weather, air, oxygen, atmospheric agents, or soil for a long period of time. Artificially, it may also be obtained quickly by application of hot or cold chemical reagents (acid or basic reagents).
Natural patina is mainly an oxide layer called Verdigris. It has variable coloration, depending on the composition of alloy and the nature of atmosphere. Plutarch tells us that statues of Spartan admirals at Delphi had a bright blue patina (De Pythiae oraculis, 395-396). This colour would be the consequence of air and atmospheric agents specific to Delphi. Bronze statues could be coated with a translucent protective liquid, such as olive oil or bitumen, as mentioned by Pliny the Elder (Naturalis Historia, XXXIV, 9, 15; XXXV, 51, 182).
Archaeological bronzes which have been buried for centuries in the ground or under water in a shipwreck suffer natural oxide or chloride patinas, even if the object was artificially patinated by the ancient metalworker.
Artificial patinas allow the addition of desired colours. They also protect the surface of bronze against corrosion and hide traces of tools used during manufacturing activities. Patination in antiquity is attested to in literary sources which describe patina recipes, such as ‘Zosimos of Panopolis’, and in iconographic sources like the new set of Achilles’ armour painted on the Attic Red-Figure Nolan amphora of the Museum of Fine Arts of Boston. On the shield, the hair of the Gorgoneion is black and his tongue is red. The patina of archaeological material can be certified as artificial when it is located between the groove of the inlay and the inlaid metal (damascening), for example a bedframe from the shipwreck of Mahdia with black patina under the silver (Hellenkemper Salies 1994).
Patina can play with the light. Some fine translucent patinas let in light and reflect upon contact with the surface of the bronze. Other more opaque patinas do not reflect light and make the surface matte.
Patination actions
The creation of artificial patinas is a process of trial and error, because it is often difficult to judge a priori what results we will get. There are numerous parameters in the patina formation process, from the composition of the chemical solution, to the composition of bronze, and the various means of implementation.
Before beginning the application of a patina solution, the surface should be degreased with an alkali agent or an organic solvent to remove all impurities and traces, including fingerprints which prevent good adhesion of the patina.
The products used and combined to produce chemical solutions are of different natures: alkalis (ammonia, urine); acids (nitric acid, wine vinegar, acetic acid); sulphates (alum, mineral sulphur, salt of Barèges); salts (sodium chloride, ammonium chloride); and pigments (sanguine – hematite rock). Some of these reagents may also be diluted with water.
The application methods generally used are hot or cold brushing. In both cases, the reaction is the same except that it is faster when applied to a warm surface. Application is done with a brush and a blowtorch, probably with a torch during antiquity. The heat must be between 80º and 100º Celsius. A “spritz” and smoke occur to indicate a chemical reaction has occurred. One should then rinse the workpiece with water and repeat the operation to cover the platelet entirely until the desired colour is achieved. Generally, the more layers applied, the more one darkens the base colour. It is important to use a different brush for each solution in order not to mix the products which will adulterate the reagents and impact the results. It is also possible to apply a patina by immersing the bronze in a bath of a solution. The reaction in this case occurs at an even slower rate. A final method involves enclosing the bronze in a hermetic container and spreading the solution by evaporation, as I have done for the patina No. 8.
A wax coating is the final step, applied to halt the chemical reaction of the solution and to protect the surface. Polishing with beeswax will set the dullness or brightness of the object.
Result: the colour of patinas
First of all, the applied solutions have still not produced a result. For example, I have applied an aqueous solution of alum but there was no significant chemical reaction.
The ammonia solution of urine and sodium chloride (patina No. 3) was also applied in different ways: a cold brushing for three days which has only slightly darkened the colour of the alloy. A bath for twelve days gave no more results. A hot brushing enhances browning of the patina, especially for platelet sample 4.3. It is possible that the urine used did not have enough ammonia. The ammonia mentioned in the recipes of the Greek alchemists was animal urine, which has a higher ammonia content (Halleux 1981, 32).
Another event during the application of a solution involved sealing it in hermetic container for twenty-four hours (patina No.8). The front of platelets, patinated first with a copper nitrate solution, did not give a beautiful patina, unlike the back (exceptionally numbered with bis) which is coloured a homogeneous dark greenish blue patina (See Figure 10, for example platelet samples 10.8 and 9.8 bis).
Number | Solution | Application | Colour | Munsell Code |
1 | Without patina | - | See Table 1 | - |
2 | Ammonia (NH4OH) + ammonium chloride (NH4Cl) | Cold brushing (3 days) | Light bluish green | 5BG 6/8 |
3 | Urine (ammonium carbonate) + sodium chloride (NaCl) | Cold brushing; bath; hot brushing | Brown | 10YR 5/3 |
4 | Copper nitrate (Cu(NO3)2) | Hot brushing | Very light green | 5G 8/4 |
5 | Sulphur (S) + alum (KAl(SO4)2•12 H2O) + water (H2O) | Hot brushing | Black | N 2/ |
6 | Wine vinegar + sodium chloride (NaCl) | Cold brushing (3 days) | Yellowish brown | 10YR 5/4 |
7 | Salt of Barèges (K2S) + water (H2O) | Cold brushing | Dark reddish brown | 5YR 3/2 |
8 | Copper nitrate (Cu(NO3)2) + ammonia (NH4OH) + ammonium chloride (NH4Cl) | Hot brushing; hermetic container (24 hours) | Dark grayish green spotted blue | 2.5G 2/2 |
9 | Copper acetate (Cu2(OAc)4) | Hot brushing | Very dusky red | 10R 2/2 |
10 | Acetic acid (C2H4O2) + hematite (Fe2O3) | Hot brushing | Red | 10R 5/6 |
11 | Without solution | Heated with a flame | Dark bluish gray | 5B 4/1 |
Table 3. The colours of patinas.
The colours obtained from these experiments cover a wide spectrum: green, blue, red, brown and black (See Table 3). The patinas No. 4, No. 2, and No. 8, are green; the patina No. 10 is red and No. 9 has a dark red colour; the patinas No. 3, No. 6, and No. 7 are brown; and the patina No. 5 is black (See Figure 10).
For Corinthian bronze and its black patina, I tested three types of solutions (See Figure 11): a sulphur and alum solution (platelet sample 11.5) that gives a black colour; a copper acetate solution (platelet sample 11.9) for a dark red colour; and an application without a solution but heated with a flame. The latter test gives a dark bluish gray patina (platelet sample 11.11). The formation of this patina occurs only with the Corinthian bronze, it doesn’t form a patina on binary or ternary bronzes. The formation of a dark oxide layer must be produced with gold and/or silver present in small quantities in the alloy.
These archaeological experiments show us the importance of the use and dosing of corrosive products in chemical solutions for the creation of a specific patina. For example, the black patina (patina No. 5) is created only by a solution of sulphur and alum (See Figure 12).
However, the adherence of a patina to the surface of the platelets was different depending on the type of alloy present. I have noticed that the alloy No. 8 with 15 % tin is not always favourable to the application of a patina. The patinas of No. 2, No. 3, and No. 7 have not held or did not react. Is it because the tin content in the alloy was too high?
The hue of the patina may also be different. Hue is produced by a larger concentration of a chemical solution or a higher heating temperature. Such as the copper nitrate solution, which results in a very light green, but also a light green for two platelets (platelet samples 2.4 and 4.4).
Conclusion
The colour palette of bronze platelet samples, and the various stages of its manufacture, have allowed me to expand the study of the archaeological material beyond strict techno-typological analysis, and to develop a new approach in researching the history of manufacturing technique and colour.
Thanks to all the actions and their gestures made during the experiments, it enabled me to understand and be able to transcribe, step by step, the chaîne opératoire of manufacture and decoration of antique bronzes made by lost-wax casting and decorated by surface treatments, such as inlay, polishing, gilding or patination.
The production of different alloys, corresponding to more or less significant values of tin and/or lead added to the copper base, allows us to understand that the physical and mechanical properties of the bronze, as well as its surface colour, evolve according to its composition.
The initial results clearly show a spectrum of colours for bronze. Colours change depending on the composition of the alloy involved, but also in the creation of a patina. A polychromatic effect can be added by inlaying metals or gilding to accentuate some details. Greco-Roman bronze furniture was enriched with colours and shine.
These results could finally open up perspectives and design new approaches for the restoration work of bronze archaeological objects. In effect, when cleaning or stripping, the collection of colour swatches could help to take better account of the colour hue, value and chroma of the alloy or antique surface treatments and keep them during the last step of corrosion stabilisation and protection of the surface of the object when applied a layer of lacquer or acrylic resin (Paraloid B-72).
Acknowledgements
I would like to thank my thesis director Philippe Jockey for his support in this project, and that of my laboratory and Jacques Rebière. I am very grateful to Laurent Inquimbert and his team for their assistance and availability. The collection of swatches of bronzes would not have been possible without them. I also thank Philippe Walter and Matthias Alfeld for their advice and assistance with archaeometric study. Finally, my thanks go to Sarah Beckmann for her careful proofreading.
This work has been produced within the framework of the Unit of Excellence LabexMed - Social Sciences and Humanities at the heart of multidisciplinary research for the Mediterranean – which holds the following reference 10-LABX-0090.
This work has been carried out thanks to the support of the A*MIDEX project (n°ANR-11-IDEX-0001-02) funded by the «Investissements d’Avenir» French Government program, managed by the French National Research Agency (ANR).
About the Author:
Jonathan Devogelaere
Aix Marseille Univ, CNRS, Minist Culture & Com, CCJ, LabexMed, Aix-en-Provence, France
Bibliography
AUCOUTURIER, M. (2007). Patinage et patines. Dossier techniques de l’ingénieur, l’expertise technique et scientifique de référence, cor1570 pp. 1-16.
AUCOUTURIER, M. & DANQUE-CERETTI, E., (2012). Dorure : décor et sublimation de la matière. Paris: Presses des Mines.
BAUDOIN, C., LIOU, B. & LONG, L. (1994). Une cargaison de bronzes hellénistiques. L'épave Fourmigue C à Golfe-Juan. Archaeonautica, 12 pp. 5-143.
BERTELLI, P., FORMIGLI, E., MARINELLI, F., MORSANI, B. & PACINI, A.(2013). Archeologia sperimentale. In: E. Formigli, eds. Colore e luce nella statuaria antica in bronzo. Rome: "L'Erma" di Bretschneider pp. 91-95.
BOUCHER, S. (1982). Les lits grecs en bronze de Bourgoin-Jallieu (Isère). Gallia, 40(1) pp. 171-193.
CALLEWAERT, M. (2010). Les couleurs des artéfacts en alliage cuivreux : analyse physico-chimique des techniques de coloration utilisées du Chalcolitique au Haut Moyen-Age en Europe et au Proche-Orient. Archéo-Situla, 20 pp. 42-60.
CHAPLET, A. (1936). Les patines du cuivre et de ses alliages. Cuivre et Laiton, 182 pp. 2-18.
COLUZZA, C. & FORMIGLI, E. (2013). Interazione luce-materia nei trattamenti superficiali dei bronzi antichi. In: E. Formigli, eds. Colore e luce nella statuaria antica in bronzo. Rome: "L'Erma" di Bretschneider pp. 61-69.
CRADDOCK P.T. & GIUMLIA-MAIR, A. (1995). The identity of Corinthian Bronze: Rome's Shakudo Alloy. In: S. Mols, eds. Acta of the 12th International Congress on Ancient Bronzes, Nijmegen 1992, Amersfoort: ROB pp. 137-147.
DE BEAUNE, S. (2000). Pour une Archéologie du geste : broyer, moudre, piler, des premiers chasseurs aux premiers agriculteurs. Paris: CNRS Editions.
DESCAMPS-LEQUIME, S. (2006). La polychromie des bronzes grecs et romains. In: A. Rouveret, S. Dubel & V. Naas, eds. Couleurs et matières dans l'Antiquité : textes, techniques et pratiques. Paris: Presses de l’ENS pp. 79-92.
DUVAUCHELLE, A., KRIEG, M., DELBARRE-BÄRTSCHI, S. & BIELMAN SANCHEZ, A. (2013). Les lits en bronze d'Avenches : développement des aspects techniques et épigraphiques. Bulletin de l’Association Pro Aventico, 54 pp. 7-118.
FERRO, D., FORMIGLI, E. & BOVANI, S. (2013). La patina artificiale antica dei grandi bronzi di Ercolano. In: E. Formigli, eds. Colore e luce nella statuaria antica in bronzo. Rome: "L'Erma" di Bretschneider pp. 33-39.
FORMIGLI, E. (2013a). Le tecniche del colore nella statuaria antica in bronzo. In: E. Formigli, eds. Colore e luce nella statuaria antica in bronzo. Rome: "L'Erma" di Bretschneider pp. 1-23.
FORMIGLI, E., (2013b). Le patine ‘naturali’ greche e le patine artificiali romane sui grandi bronzi. In: E. Formigli, ed. Colore e luce nella statuaria antica in bronzo. Rome: "L'Erma" di Bretschneider pp. 49-54.
FORMIGLI, E. (2013c). Il ruolo della luce nella statuaria antica in bronzo. In: E. Formigli, eds. Colore e luce nella statuaria antica in bronzo. Rome: "L'Erma" di Bretschneider pp. 72-76.
GIUMLIA-MAIR, A. (2002). Zosimos The Alchemist – Manuscript 6.29, Cambridge, Metallurgical interpretation. In: A. Giumlia-Mair, eds. I Bronzi Antichi : Produzione e tecnologia. Atti del XV Congresso Internazionale sui Bronzi Antichi. Montagnac: Editions Monique Mergoil pp. 317-323.
GIUMLIA-MAIR, A. & CRADDOCK, P.T., (1993). Corinthium aes - Das schwarze Gold der Alchimisten. Antike Welt - Zeitschrift für Archäologie und Kulturgeschichte, 24 pp. 1-62.
HALLEUX, R., (1981). Les alchimistes grecs - Papyrus de Leyde, papyrus de Stockholm et fragments de recettes. Paris: Les Belles Lettres.
HELLENKEMPER SALIES, G. (ed.) (1994). Das Wrack. Der antike Schiffsfund von Mahdia. Cologne: Rheinland-Verlag GmbH.
HUGHES, R. & ROWE, M. (1991). The colouring, bronzing and patination of metals: a manual for fine metalworkers, sculptors and designers. London: Thames and Hudson.
HUNTER, E. C.D. (2002). Beautiful black bronzes: Zosimos' treatises in Cam. Mm.6.29. In: A. Giumlia-Mair, eds. I Bronzi Antichi : Produzione e tecnologia. Atti del XV Congresso Internazionale sui Bronzi Antichi. Montagnac: Editions Monique Mergoil pp. 655-660.
KALTSAS, N., VLACHOGIANNI, E. & BOUYIA, P. (2012). The Antikythera Shipwreck - the ship, the treasures, the mechanism. Athens: National Archaeological Museum.
LA ROCCA, E. (ed.) (2014). Auguste. Paris: Réunion des musées nationaux - Grand Palais.
MATHIS, F. (2005). Couches d’oxydation et patines intentionnelles des bronzes: Croissance et propriétés des couches d'oxydation et des patines à la surface d'alliages cuivreux d'intérêt archéologique ou artistique (PhD thesis, Université Paris-Sud 11).
MATTUSCH, C.C. (2003). Corinthian Bronze. Famous, but elusive. Corinth, The centenary 1896-1996, XX pp. 219-232.
MERTENS, M. (1995). Les alchimistes grecs – Zosime de Panopolis. Mémoires authentiques. Paris: Les Belles Lettres.
MULLER-DUFEU, M. (2006). Les couleurs du bronze dans les statues grecques, d'après les textes antiques. In: A. Rouveret, S. Dubel & V. Naas, eds. Couleurs et matières dans l'Antiquité : textes, techniques et pratiques. Paris: Presses de l’ENS pp. 93-102.
MUNSELL, A.H. (1975). Munsell Soil Color Charts. Baltimore: Munsell Color Company.
PICCOT-BOUBE, C. (1960). Les lits de bronze de Maurétanie Tingitane. Bulletin d’Archéologie Marocaine, IV pp. 189-286.
PIRZIO BIROLI STEFANELLI, L. (1990). Il bronzo dei Romani : arredo e suppellettile. Rome: "L'Erma" di Bretschneider.
PERNOT, M. (1994). Le bronze, ce n’est pas vert. Bulletin de liaison - Moulages, copies, fac-similés. Actes des IXèmes Journées des Restaurateurs en Archéologie, 11 pp. 149-161.
QUENTIN, E. (2005). Gros plan : Une palette de techniques pour colorer la matière métallique. Fèvres, 13 pp. 9-29.
RAMA, J.-P. (1995). Le bronze d’art et ses techniques. Dourdan: H. Vial.
REYNOLDS J. (1994). Experimental Archaeology: a Perspective for the Future. The Reuvens Lecture, Stichting voor de Nederlandse Archeologie, 5 pp. 1-16.
REYNOLDS J. (1999). The nature of experiment in archaeology. In: Harding A. eds. Experiment and Design: Archaeological Studies in Honour of John Coles. Oxford: Oxbow Books pp. 156-162.
STOCK, S. & GIUMLIA-MAIR, A. (2002). The Roman Triclinium Frames in the Royal Ontario Museum Toronto (Canada). In: A. Giumlia-Mair, eds. I Bronzi Antichi : Produzione e tecnologia. Atti del XV Congresso Internazionale sui Bronzi Antichi. Montagnac: Editions Monique Mergoil pp. 559-562.
VENTURA, P. & GIUMLIA-MAIR, A. (2002). Resti di arredo di età romana dal territorio di Pordenone: cornice in lega a base di rame con agemina. In: A. Giumlia-Mair, eds. I Bronzi Antichi : Produzione e tecnologia. Atti del XV Congresso Internazionale sui Bronzi Antichi. Montagnac: Editions Monique Mergoil pp. 554-558.
VEYNE, P. (2005). L’Empire gréco-romain. Paris: Editions du Seuil p. 11
WALTER, H. (1976). Bronzes figurés antiques de la Haute-Saône. Revue Archéologique de l’Est et du Centre-Est, XXVII(1-2) pp. 197-284.