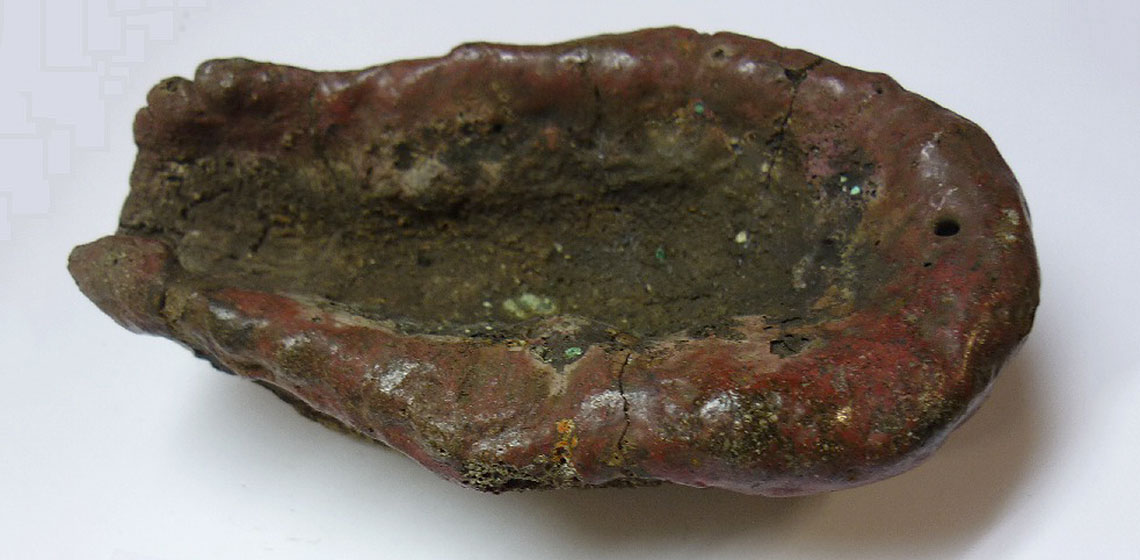
In this study the sustainability of crucibles used during the Scandinavian Bronze Age is tested. Due to the crucible’s high or low sustainability the idea of it being a disposable object may be ratified or discarded. Earlier experiments focusing on the casting process in Scandinavian Bronze Age have concluded that crucibles such as the ones used during Bronze Age were disposable objects due to low sustainability. However, to make a more thorough study one has to replicate not only shape but also temper and clay, something that was not done in these earlier studies. In this study replicas were made and tested to investigate sustainability but also traces of use. The results are that the crucibles have a sustainability of more than 20 castings, in contrary to earlier studies suggesting one to ten castings. Another conclusion is that the traces of use correspond to the ones that are visible in the original Broåsen material.
The project in short
The workshops where bronze objects were produced during the Scandinavian Bronze Age are long gone. A study of what went on in and around the production process is dependent on the archaeological material that we have available through excavations, earlier studies and discussions. An aspect of this information that has not yet been studied thoroughly in Scandinavia is the ceramic melting crucibles used to melt and cast bronze objects from this period. They are one of few categories of artefacts that the Bronze Age workshop consisted of that are still available for study today. This supports the study of crucibles in order to further understand the concept of bronze artefact production in Scandinavia.
The aim of the project was to test whether crucibles in southern Scandinavian archaeology were disposable objects. Earlier experiments have shown us that crucibles made in the same shape as original archaeological material, or even by own design tends, to have a very low sustainability (Nilsson 2008, 21; Kjærulf Andersen 2007). It is often claimed to be around five or fewer times that a crucible can be used before it has to be discarded. However, to make a better estimation of the sustainability not only the shape but also temper and clay must be replicated. Therefore this project was initiated to prove/disprove the above mentioned claims of low sustainability.
Since there are different types of archaeological materials, perhaps representing different kinds of production in southern Scandinavia [for example, at Lejeby (one sherd) and Bokenäs (more than 100 sherds) (Oldeberg 1960, 46f & 50)] the focus was on large-scale production sites. This selection was made on the presumption that if you are looking for the maximal sustainability, a large-scale production site is the place to look. As an example Broåsen was chosen, which is situated in the parish Grimeton, southern Sweden. The material from Broåsen contains potsherds, a glass bead and a socket axe, but also more than 200 sherds of crucibles and almost an equal amount of mould fragments (Svensson 1940,100). Also, three whole crucibles have been found and a furthermore 17 have been refitted. In order to test how many times the crucibles from Broåsen were used before being discarded, a first step would be to investigate how many times they could have been used (maximum). To do so the material and shape of the crucibles/sherds were investigated. Several replicas were then made on the basis of that study. A workshop was also built with the help of the current knowledge available (Johansson 1993; Thrane 1994; Rönne 1996). The crucibles were then used to melt and pore bronze as many times as possible until they were either in need of mending or had to be discarded.
The archaeological material
The crucibles found at Broåsen correspond well with the Bronze Age crucibles in southern Scandinavia in general. They are oval shaped, low and without a lid (See Figures 1 and 2). When studying the crucibles it is clear that they have, in most cases, been exposed to extensive heat from above. This indicates that they have been used in a workshop where the heat is intensified by an added oxygen flow coming from above. The reddish colour that is present inside and on top of the rim (See Figures 1 and 2) derives from copper-oxide coming from the copper-alloy in connection with the melting. The shape of the crucibles found at Broåsen does not vary much. However, the size does to some extent. The twenty refitted and whole crucibles were roughly divided into three approximate sizes: small (8 x 6cm), medium (10 x 6 cm) and large (13 x 8 cm).
Reconstruction: shape, usage and material
By ocular assessment of the temper used when making the crucibles at Broåsen, four different types of temper were observed. Ten sherds that were assumed to represent the difference in temper within the material were then taken for further examination by thin section petrography. Using image analysing software (Nikon NIS Elements) it was possible to determine four types of temper as shown below (See Figure 4 and Table 1).
Grain size concentration * (mm.) | Max/Min grain size (mm.) | Percentage | Organic material | Clay type | Number of sherds | |
Temper1 | 0.125 – 0.5 | 0.063 – 1.0 | 60,00% | course** | 1 | |
Temper2 | 0.355 – 1.4 | 0.063 – 2.2 | 60,00% | course** | 3 | |
Temper3 | 0.5 – 2.0 | 0.063 – 2.2 | 60,00% | course** | 5 | |
Temper4 | 0.5 – 2.0 | 0.063 – 2.2 | 60,00% | x | course** | 1 |
* The interval in grain size were 75% of the volume of the grains are concentrated
** Diamikt course clay
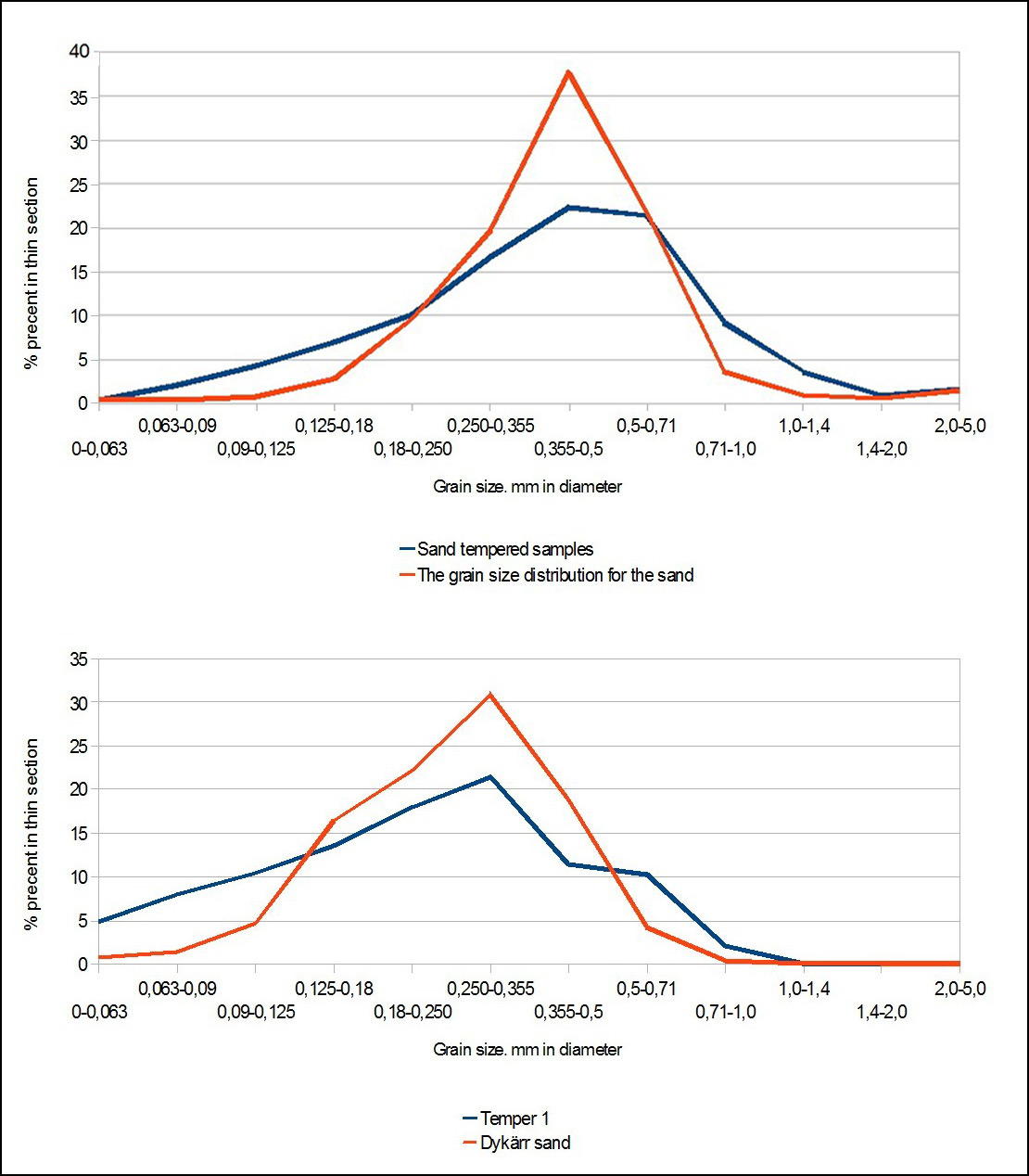
0-0,063 | 0,063-0,09 | 0,09-0,125 | 0,125-0,18 | 0,18-0,250 | 0,250-0,355 | |
Temper1 | 4.8951049 | 7.92540793 | 10.4895105 | 13.5198135 | 17.9487179 | 21.4452214 |
Dykärr sand | 0.72357939 | 1.39405204 | 4.66343601 | 16.4630908 | 22.1986192 | 30.941317 |
0,355-0,5 | 0,5-0,71 | 0,71-1,0 | 1,0-1,4 | 1,4-2,0 | 2,0-5,0 | |
Temper1 | 11.4219114 | 10.2564103 | 2.0979021 | 0 | 0 | 0 |
Dykärr sand | 18.9557886 | 4.22198619 | 0.39498141 | 0.04314923 | 0 | 0 |
Most of the crucibles in the original archaeological material were defined as large after the definitions mentioned earlier in this article. In order to not exceed the project's time frame the large type of crucible was chosen to represent the material from Broåsen.
The clay used to make the original crucibles was coarse clay estimated to correspond to a clay diamicton. Clay from Minnesberg, Skåne was chosen for the reconstructions due to its similarities with the original clay used for the crucibles. The Minnesberg clay is a clay diamicton containing around 17 vol % clay, 55% silt and 28% sand/gravel (See Graph 2).
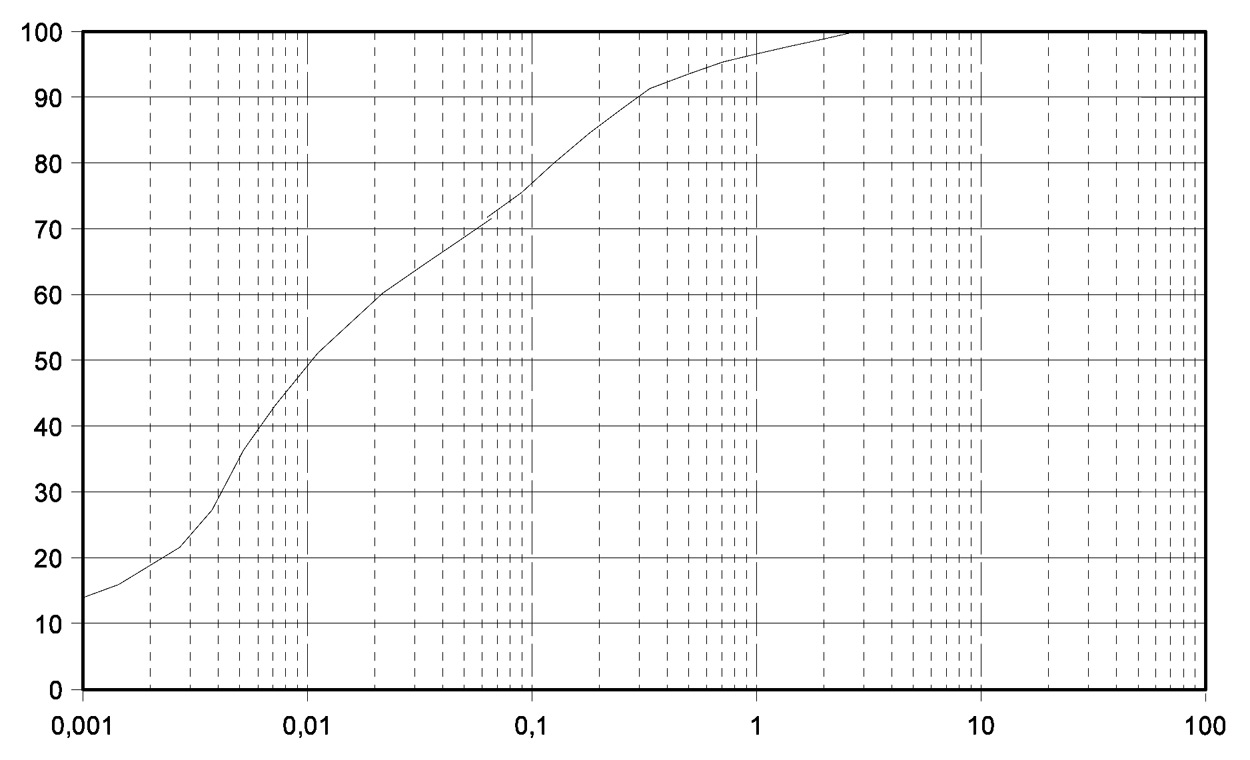
Contents | Grain Size | Percentage |
gravel | 2.0 mm and bigger | 1.17% |
sand | 0.06 – 2.0 mm | 26.35% |
silt | 0.002 – 0.06 mm | 55.27% |
clay | less than 0.002 mm | 17.21% |
Based on these studies and using the material presented above, seven new crucibles were made. Since Temper 3 was present in five of 10 original crucible sherds Temper 3 was used in four of the seven reconstructions. Temper 2 was used in two replicas and Temper 1 was used in one of the replicas. These reconstructed crucibles were labelled 1A, 2A, 2B, 3A, 3B, 3C and 3D according to the type of temper used (See Figure 5).
The experiments
Using earlier studies of Bronze Age workshops (Johansson 1993; Thrane 1994; Rönne 1996) a small hearth was built in order to conduct the experiments in an as accurate way as possible (See Figure 6). A Cu-alloy consisting of 10%Sn and 90%Cu (bronze) was melted in the crucibles. The metal was put inside the crucible that was situated on top of a layer of charcoal directly under the airflow from the tuyére. After that it was covered with charcoal, air was pumped trough the tuyére using bellows and the melting began. When the metal was melted the crucible was taken out of the hearth and the metal was poured out. No mould was used since the casted object not was in focus for this study, instead a cavity in a soapstone was used to dispose the metal. Each crucible was used as many times as possible during one day and then left in the hearth to cool off during the night. The day after, the crucibles were inspected for visible cracks, and if cracks were not present the experiments continued (See Figure 7). When using a crucible it is exposed to enormous changes in temperature. The hearth must hold a temperature of around 1100oC at the lowest in order to melt the copper alloy and to make sure it stays in liquid state during the whole casting process. Outside the hearth the temperature, in this case, is on average around 10 to 15oC. When moving the crucible from the hearth to the mould in order to do the casting it is vital that the crucible does not break due to the enormous temperature fluctuations. Ceramics have a tendency to break when cooling off or heating up too quickly. One of the critical points in the heating / cooling process is 572o C. This is sometimes referred to as the quartz point, where the quartz crystal goes from a-stage to ß-stage and back (Blackburn and Dennen 1988, 74f & 311f) something that results on heavy strains on the ware. During the experiments it was clear that the crucibles endured such ordeals. In spite of this, no visible cracks were detected when inspecting the crucibles at the beginning of the workday. Even though the crucibles were used several times and also by an unskilled craftsman (the author) they did not crack or fall apart into sherds after being used up to ten times as is indicated by earlier studies. On the contrary, all the crucibles (with the exception of crucible 1A which lasted for six castings) were still in one piece when the experiments were concluded. When studied both during the experiment and after it was clear that each crucible had traces of use depending on how many times they were used. The sintering of the ware started from the top/rim and on the inside and slowly spread as the crucible was used repeatedly times. A red layer of copper oxide started to cover the inside of the crucibles and got more intense as they were used. A crucible used for 20 castings showed an even buff red layer of copper oxide mainly on the rim and inside, the ware had sintered mostly on the parts facing the airflow from the tuyére. Due to the traces of use on the replica crucibles, when comparing the replicas with the archaeological material it is clear that the Broåsen crucibles were used for minimum 20 castings.
Conclusions
The first conclusion that can be made from these experiments is that we have to reconsider the statements of earlier studies. In some cases crucibles might have had a low sustainability, but evidently there are also sites that show the contrary. So far there are too few studies focusing on the connection between choice of clay/temper and sustainability in order to get a good overview of the difference between the quality of crucibles. It is highly plausible that the sustainability of crucibles varied between sites and craftspersons depending on factors such as production rate, level of knowledge and available resources (as discussed by among others such as Stilborg 2008). In the literature concerning Scandinavian and European Bronze Age the focus is on who the bronze caster and the people connected to the production of bronze objects were (for example Goldhahn 2007; Kristiansen & Larsson 2005). This is intimately connected to the study of crucibles because there may have been a difference in who made the crucibles at different sites and different types of production. A highly skilled group of craftspersons would probably have both needed and used a sustainable crucible to conduct their work in an effective way. In another scenario, if only one casting was needed, the crucible did not need to have sustainability higher than one time. In conclusion, we now have evidence that crucibles could have had a high level of sustainability, however the sustainability of crucibles from other sites may vary in comparison to the Broåsen material.
Experiments yet to be made
Continuing studies will be conducted on archaeological materials assumed to represent low scale production. The purpose is to investigate whether the high sustainability among the crucibles from Broåsen is also present in that type of material even though it is assumed not to have been necessary.
Acknowledgements
Special thank to Anders Lindahl, Stella Macheridis and Andreas Nilsson for reading and commenting on the text.
Bibliography
BLACKBURN, W. H., and W. H. DENNEN, The principles of mineralogy, Dubuque, WCB/McGraw-Hill, 1988.
EKLÖV PETTERSSON, P., "En hållbar utveckling? -Hållbarheten för bronsålderns keramiska deglar", Institute of archaeology and ancient society, vol. MA, Lund, Lund University, Department of Archaeology and Ancient History, 2011.
GOLDHAHN, J., "Dödens hand -en essä om brons- och hällsmeden", GOTARC Series C, vol. Arkeologiska Skrifter No 65, Göteborg, Göteborgs Universitet, Institutionen för arkeologi och antikens kultur, 2007.
JOHANSSON, T., Forntida Teknik, Västerås, Institut för Forntida Teknik, pp. 176, 1993.
KRISTIANSEN, K., and T. B. LARSSON, The Rise of Bronze Age Society: Travels, Transmissions and Transformations, Cambridge, Cambridge University Press, 2005.
NILSSON, A., "Gjutfel och dålig ornamentik", Institute of archaeology and ancient society, vol. MA, Lund, Lund University, Department of Archaeology and Ancient History, 2008.
OLDEBERG, A., Skälbyfyndet, Stockholm, 1960.
RØNNE, P., "Flydende bronze i digler og forme", Naturens Verden , vol. 41, København, Naturens Verdens Fond, pp. xx-xx, 1996.
STILBORG, O., "A technological study of crucibles from Helgö and Bäckby", Excavations at Helgö, vol. XVII, Stockholm, pp. xx-xx, 2008.
SVENSSON, B., "En gjuteriverkstad från bronsåldern", Göteborgs och Bohusläns Fornminnesförenings Årsskrift, pp. xx-xx, 1940.
THRANE, H., "Bronzens mestre", Skalk, issue 2, Århus, pp. 10-13, 1994.