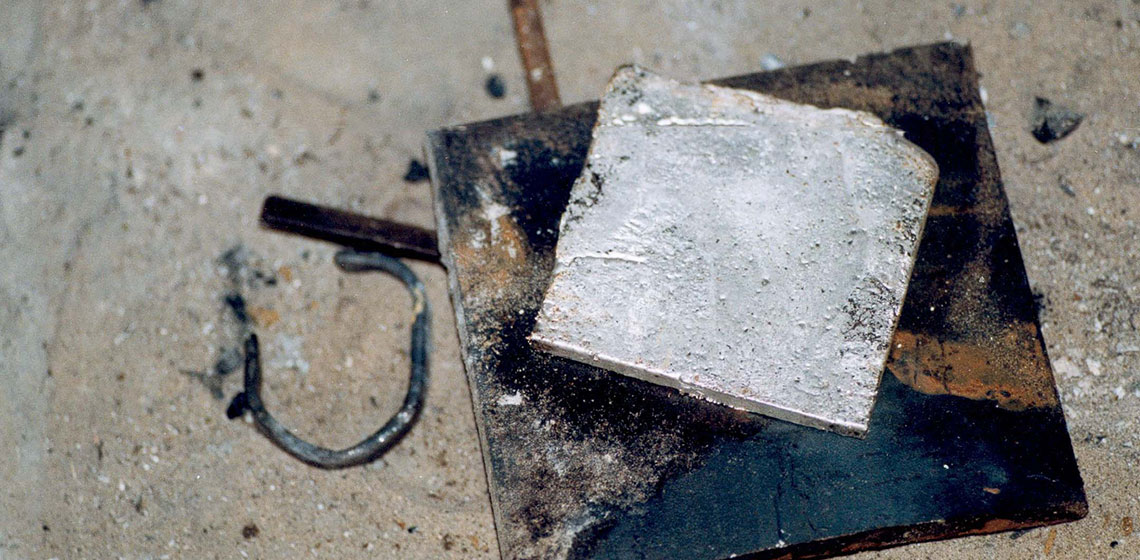
During a short internship in The Hagues Municipal Museum, I noticed some blisters in a seventeenth century V.O.C.-dish. I thought they were gas bubbles which might have been introduced in the material during coagulation. When hammering to sheet the bubbles would take the shape of blisters which would turn visible during annealing. Why, however, were these shapes not visible on many other pieces? Had they not been annealed after completion or was this particular dish just a product of bad workmanship? I cannot imagine the possibility of keeping the metal free from gas bubbles during casting and it is similarly almost inconceivable that none of the pieces coming under my attention during the last few years had been annealed or soldered. Therefore, there might be a way to make the holes disappear as I was taught during my education to be a goldsmith. At that time I was too cautious to believe it. I certainly had, and still have today, no explanation by material science how gasses could be dissolved or transported in a metal structure.
Experiment
When the subject of techniques of reproduction was raised these questions came back to me. Casting a slab of silver and subsequently hammering it might be a way to answer some of these questions. This would involve following the suggestions of certain treatises in combination with scientific research.
In the Library at the Netherlands Institute for Cultural Heritage (ICN) in Amsterdam there are two translations of Theophilus. This clergyman who lived in the 12th century described how silver is cast in a hot circular mould containing liquid wax and subsequently quenched in a solution of salt and lye or lees (depending on the translation by respectively Dodwell or Hawthorne and Smith for the Latin word faecibus) (Dodwell 1961, 76 / Hawthorne & Smith 1979, 99).
In another treatise, written by Biringuccio in 1540, there is mention of hammering silver for making money (Price 1959). He writes that melting in a crucible is very well known to goldsmiths and that crucibles can be made from various materials. They have to meet certain standards however. They must resist fire well, receive the metals well, make a neat casting and not shrink or crack on drying or baking. Copper is cast in hot iron plate-moulds that can be greased with fat. Silver can be heated and blanched in a solution of rock alum1
), powdered tartar2
, salt and water.
Cellini’s treatise of 1568 contains much more detailed information on silver hammering. He writes that it is possible to melt silver in a brick furnace with the aid of bellows. The (unspecified) crucible must be rubbed with olive oil inside and out. The metal is heated up gradually on the furnace until it is red hot. When using the bellows it becomes liquid like water and now a handful of tartar is thrown over it. Then the crucible is removed from the coals, laying a piece of linen which is soaked in oil and folded four or five times over the crucible. The silver is then poured into an iron mould. The mould is made of two iron plates with a few square rods about the size of a little finger between them. This is held together with six to eight iron cramps. It is then painted around the junction with fluid clay to prevent the silver from seeping through. When it is well heated, a little oil is poured in and the mould is put in a ceramic pot filled with ashes or held steady by four bricks. Hereafter the silver is cast (Ashbee 1967).
Afterwards, the silver is cooled down on the iron plates because by doing so ‘it contracts better’. Then, the silver plate has its rough edges trimmed and it is scraped to plane it on both sides when it is red-hot. The edges are slightly rounded off and if the plate happens to be cast in an oblong shape it is beaten into a round shape in the following way: the red-hot plate (not too red) is hammered on a stake ‘with the thin end of the hammer from one angle to the other driving the metal well to the centre’. After the four corners are done ‘it will be marked somewhat the shape of a cross’. Later the process is reversed and one works ‘with the hammer outwards, annealing the plate some four times, till it is of such roundness as your good craftsmanship may seem fit’.
Scraping is, as Cellini writes, not always necessary; ‘it is possible to set off right away to hammer it into shape and give it its rotundity (…) without paring it in any way’ (Ashbee 1967, 84).
After hammering, the centre point is struck and circles are drawn on the sheet while subsequently hammering it under repeated heating. Doing this, the middle should be kept as thick as possible.
Once more circles are drawn and the plate is hammered with a hammer that is ‘one finger thick at the narrow end and one-and-a-half at the broad end; this hammer is battered and rounded off into somewhat the shape of the fleshy part of a finger’. With this one begins ‘beating in the middle of the plate, at the centre point in fact, being careful not to lose the point. The movement of the hammer should be in the form of a spiral, and follow the concentric circles.’ After this treatment the plate seems to resemble a hat and is hammered on ‘various different stakes’ in the shape of a vase. As one goes on, one removes any little imperfections on the surface.
Das Kupferschmiedhandwerk written by Höhne, F. and Rösling in 1839 contains information about hammering metal, but the metal that is beaten is copper and the hammers are mechanically driven. Therefore this treatise is of no great value to this experiment. The treatises of Biringuccio and Cellini hold the most information and are written at more or less the same time. It is also comforting that Theophilus, although adding no information at all, doesn’t contradict these treatises.
These are the reasons to choose the treatises of Biringuccio and Cellini to support my efforts to reproduce a silver sheet by using authentic techniques.
Biringuccio’s treatise is highly appreciated, but it is narratively written and therefore not very detailed. Besides this, he makes it clear that he is not a goldsmith himself (Price 1959, 364) and so one can imagine that he only received his information from someone else, which doesn’t add to his credibility.
Cellini’s writing is known worldwide and is regarded as a highly important work on metalworking in the sixteenth century. However, it has been said that he liked to embellish certain things. Perhaps one should not take the effortless ways and marvellous results that Cellini writes about for granted.
Undoubtedly there have been many people who made silver sheet out of cast plates. However to the best of my knowledge this hasn’t been done by using historical techniques combined with scientific research.
It would be good to cast silver that consists of a historically correct alloy. This can be either done by reducing and refining ores or analysing a historic silver object and adding other metals to the new silver.
Since the crucible is expected to have no effect on the structure of the silver and the treatises do not specify these, a ceramic crucible will be made as Biringuccio describes (Price 1959, 219).
Experimental
The silver will be melted in a crucible which is rubbed with olive oil. A handful of tartar will be put in the crucible and an oil-drenched linen cloth put over it. Next the metal will be poured into an iron mould. The mould, made according to the notes of Cellini, will be painted with clay. The metal shall be cooled on the plate, trimmed, rounded and omitting the planing technique the plate shall be hammered red hot until it is round.
The plate will hereafter be hammered into a hat-like shape according to the treatise by Cellini.
During all these treatments the plate will be annealed when it holds too much strain and subsequently blanched in a solution of rock alum, powdered tartar, salt and water.
There is of course a certain amount of materials and time necessary to undertake an experiment such as this one. The materials will not have to be very expensive (except for the silver perhaps) and are not expected to exceed HFL 250,- The amount of time involved in the experiment including evaluation and report will hopefully not be more than thirty hours.
The silver will show large crystals, dendrites, and some gas bubbles when cast. The silver will then be worked by hammering, the crystals will be flattened, and during annealing they will recrystallise to form small grains. After working it more thoroughly, the crystals will become flat and after a second annealing treatment they will once more produce small grains.
The blisters will probably be formed after flattening the bubbles when working the metal for the first time. Whether they will disappear is the main research question.
It will be fascinating to see how the metallic structure changes under deformation of this kind. There is always the chance that something unexpected or perhaps even amazing will be visible, which raises new questions and will lead to more experiments or deeper investigations.
Practical part
In Wilhelminaoord, there was the possibility to carry out the above discussed experiment. The mould was made in the following manner. Three square iron rods were placed between two thick iron plates with eight iron cramps. To minimise the silver needed for the experiment, the rods were not quite as thick as Cellini would have demanded. The actual diameter was 5 mm. This mould was painted with fluid clay to prevent the silver from seeping through (using a brush of wool bound with grass in a feather socket to stay in the historical context). A tiny crucible was prepared from grey clay, meagred with loam and a handful of pieces of wool according to the instuctions of Biringuccio (Price 1959, 219). This crucible was fired, and after cooling down was rubbed with olive oil. The piece of linen sheet was soaked in the oil as well. A little bit of clay was flattened and this was put on the crucible to keep the charco¬al out and the heat in the crucible. This lid was not treated with oil.
A 17th century silver dish from Venice was taken as a model for the experimental alloy. This had already been analysed and fitted the context of Cellini best. Knowing that in this dish 3% copper, 0.4% lead, 1.4% zinc and some traces of other metals were discovered, 200 gr of silver, 6 grams of copper, 2.8 grams of zinc and 0.8 grams of lead were weighed and the silver was put in the crucible. After melting the silver, the copper and later the other metals were added. The coloured flames produced led to the conclusion that not all of the additions fully formed part of the alloy.
In the haste to pour the liquid metal in the mould, both the tartar and the linen cloth were not used regrettably.
After the silver was cast into the iron mould, the upper part of the approximately 5 cm wide slab was sawn off for future analysis. Casting the silver went well and the result was good; the slab was solid without many defects. The corners were hot-worked using the thin side of a normal hammer. The rest was cold-worked according to Cellini's instructions. The silver slab was probably worked too fiercely in one round, because the material tended to tear at the sides. The only thing to do was to leave this piece as it was for analysing, and to melt more metal and cast another one.
For the next slab, preparations were made as above, accept for making the alloy. For this 198.5 grams of silver, 3 grams of copper, 2 grams of zinc and 0.4 grams of lead were weighed. A large amount of the silver was put in the crucible. Then the copper was placed followed by the lead. Next, the zinc was put in. To cover those metals from the flames, the rest of the silver was put on top of it. This mixture, which almost filled the crucible completely, was fired and when molten, poured in the mould. This time, neither the tartar nor the linen cloth were forgotten. The tartar was strewn on the molten metal and the cloth was put on the crucible when taking it out of the fire.
This produced a square slab of silver of about the same size as the first attempt. The upper part was sawn off, again for analysis, and the remaining object was treated in the same way as the first. This time the plate was worked less heavily. After having worked it, the silver was annealed. Hereafter the slab was worked once more in the same way and annealed again. At this stage the workshop in Wilhelminaoord was over; time was up.
Back in Amsterdam samples of the centre, side and near a tear of the first slab were sawn out. After annealing the slab, samples from the centre, side and corner were taken. The second slab had already been annealed, so samples were only once taken from the centre, side and corner of the slab.
The samples of the casting of the first slab and the piece near a big tear were analysed by X-Ray Fluorescence (XRF). A sample from the second slab after casting and one after annealing were also analysed, along with a good example of blistering.
This blister occurred while making silver sheet during the goldsmith education. This sheet was cast from scrap metal of a commercially bought 92.5% silver alloy sheet. After it was cast, it was hammered and rolled. When annealing after it was rolled the blister became visible.
Results
Sample | Ag% | Cu% | Zn% | Pb% |
Slab 1, cast |
97.4 ±0.23 |
1.5 ±0.02 |
0.5 ±0.01 |
0.2 ±0.02 |
Slab 1, near tear, unannealed |
97.5 ±0.50 |
1.7 ±0.06 |
0.5 ±0.02 |
0.3 ±0.07 |
Slab 2, cast |
97.1 ±0.26 |
1.8 ±0.03 |
0.5 ±0.01 |
0.3 ±0.03 |
Slab 2, annealed |
96.9 ±0.35 |
1.8 ±0.04 |
0.5 ±0.02 |
0.3 ±0.04 |
Blister |
94.0 ±0.66 |
5.1 ±0.12 |
trace amount |
- |
Other metals that were discovered were chromium, mercury, nickel, cobalt, gold, arsenic, cadmium, tin and antimony. However, these metals had always been there as trace elements.
Resuming school meant less time to finish this project. The positive aspect of school would be that there would be room for evaluating the samples taken from the results of the experiment by using a metallurgical microscope. Unfortunately there was too little time to do this evaluation and the results of polishing and etching were not really what had been hoped for. This makes it somewhat difficult to describe the structure exactly.
Due to the above mentioned, only the samples of the first slab have been evaluated because they were more often sampled and it was thought they would therefore provide more information.
Slab 1:
cast: | Typical casting dendrites. Some gas bubbles were visible. The structure there was no different from the rest. |
worked (centre): |
Grain size is smaller on one side. Dark precipitates. |
worked (side): | A lot of precipitates. One line inside the sample looks like a hole that has been closed by deformation. |
worked (near tear): | Looks like crystals have been torn apart. Some precipitates are quite large. |
annealed (centre): | A lot of precipitates. No tearing, holes or coloured lines. |
annealed (side): | A whole lot of tiny precipitates. Some larger and little tears. Some precipitates appear to be in a curled line shape. |
annealed (corner): | Small precipitates divided through the sample. One large precipitate or tear. One closed line. Some precipitates appear to be in network of small lines. |
blister: | There is some precipitation. The grain boundaries are lighter. This appears also at the edge of the blister. |
Conclusions
Though the results are not conclusive, it looks like the gas bubbles disappear when the metal has been worked. The lines which are visible might very well be closed gas bubbles. When annealing, the precipitates that are detected might lower the melting temperature and weld the closed hole together. They also could be the product of a reaction of the metal and the gas inside the former bubble.
It would probably be best if one could monitor the metal very closely when it deforms. The in homogeneity of the metal however makes this difficult to do. After every bit of cold work a small sample would have to be taken. These would preferably come from around the same place in the slab. The side that will be examined by metallurgical microscopy should be as close as possible to the sides of the other samples that will be examined. The other thing is that the gas bubbles do not occur very often, so the samples have to be rather big to have a good chance of seeing one. After having obtained the samples before annealing, it would be best if they were sawn in two pieces and if one piece would be annealed. The side where they had been attached to each other would provide the preferable side to examine both pieces, because they are almost identical. This way, the effect of annealing could be shown best.
To conclude more accurately if the bubbles are closed, the percentage and size of the bubbles should be determined in the sample of the casting. When the size and percentage of the bubbles is the same as the size and percentage of the lines seen in the sample after working the silver, it is more likely that the lines are the closed bubbles. For this method it would be best to cast a large slab and take large samples.
Summary
According to instructions of Cellini and Biringuccio a short historical research has been done on the blistering in silver. Results show inconclusively that gas bubbles can probably be closed by coldworking.
The blisters might occur when the cast silver has not been worked enough. When the slab is annealed, the pressure inside the bubble builds up. If the slab has been made as thin as sheet, the pressure could be enough to deform the material which is weakened by the annealing treatment, creating the blister.
Bibliography
ASHBEE, C. R., The treatises of Benvenuto Cellini on Goldsmithing and Architecture, New York, Dover Publications Inc., 1967.
PRICE, B. C., The Pyrotechnia of Vannoccio Biringuccio, New York, Basic Books, 1959.
HÖHNE, F., and C. W. RÖSLING, Das Kupferschmiedhandwerk mit den nôthigen Vorlehren über die Erzuegung und Behandlung des ROHKUPFERS, so wie aller in dieses Fach einschlagenden Produkte; Weimar, 1839, Aus Neuer Schauplatz de Künste und Handwerk, Hannover, Th. Schäfer, 1839.
van LAER, W., WEG-WYZER voor aankomende Goud en zilversmeden door Willem van Laer, Mr. Zilver-smidt tot Zwoln, Lochem, De Tijdstroom, 1721.
DODWELL, C. R., Theophilus: The various arts, London, Thomas Nelson and Sons Ltd, 1961.
HAWTHORNE, J. G., and C. S. SMITH, The ophilus: On Divers Arts. The Foremost Medieval Treatise on Painting, Glassmaking and Metalwork, , New York, 1979.