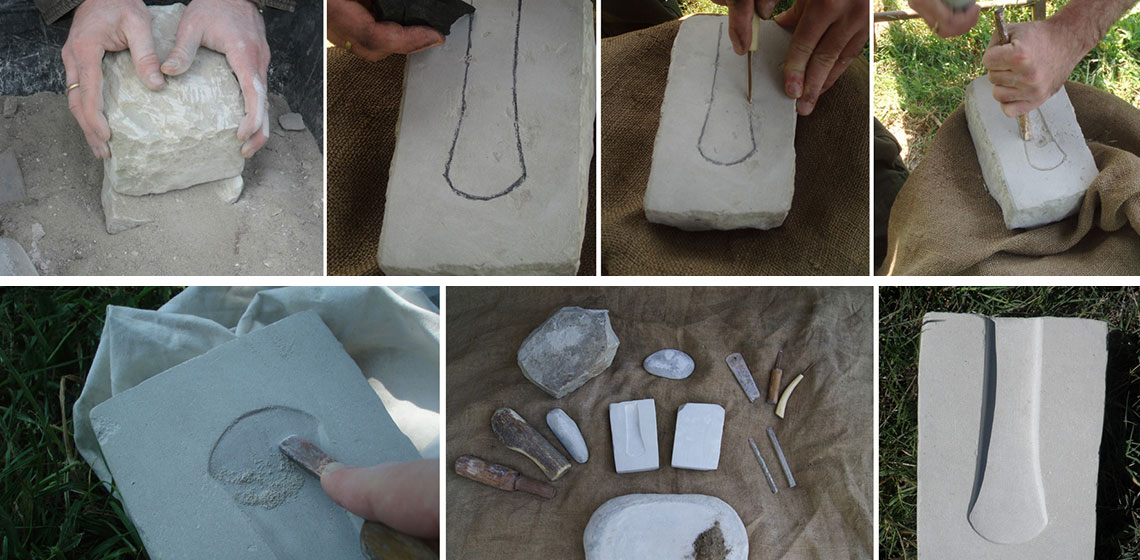
A large number of stone moulds, dating to Middle and Late Bronze Age (approximately 1650-1150 BC) has been found in Terramare sites since the 19th century. They were made to produce a wide range of bronze objects, such as ornaments, weapons and tools. Empirical observations of casting experiments revealed that different types of stone do not give the same response to the heat of molten metal. This was the starting point for research that involved a team of geologists, archaeologists and craftsmen and had two principal aims: to identify the types of stone used by Terramare artisans and the possible supplying areas, and to reproduce one axe mould with the same stone chosen in the past to test its characteristics and verify the level of knowledge and skills required in this kind of production.
Introduction
Although a long list of publications has been dedicated over the last several decades to the questions concerning early metallurgy, the achievements and the potential contributions of experimental archaeology in this area of interest still remain quite underestimated by a consistent part of academia, at least in Italy. At some official occasions the debate between the theoretical knowledge-holders and the technical skill-holders strongly emerges, but very few come back home with a true increased respect and acceptance for the counterpart's work.
This dichotomy comes from the fact that experimental archaeology has been incorporated into the academic studiessporadically and only quite recently. In fact, most of the skilled craftspeople who are able to reproduce ancient objects, structures and processes, work as artisans rather than archaeologists. Sometimes it looks like a ‘class struggle’ between scholars and craftsmen, both forgetting that craftsmanship embodies discursive (knowledge) and non-discursive (skills) abilities; consequently, a synthesis between the two contributions facilitates a better understanding of the archaeological phenomenon of metallurgy.
For example, Maikel Kuijpers in a recent monograph about metallurgy in Bronze Age Netherlands asserts about experimental archaeology:
...this manner of testing a hypothesis raises some doubt, for the hypothesis made by the archaeologists is actually an interpretation, based on a dataset gathered in a subjective way. The information that archaeologists gather from the record, is, after all, dependent upon their knowledge. Hence, if experimental archaeology supports the interpretation this does not have to mean that the interpretation is the right explanation...(Kuijpers 2008, 25).
What Kuijpers argues is partially acceptable (sometimes completely true), but we know cases of systematic collections of data that may present a fragmentary archaeological frame but it is an objective fragmentary frame. The only way to apply the scientific method in order to get the most reliable scientific theory is to test the hypothesis, and when we talk about ancient crafts often an extensive series of experiments is a good instrument (see Coles 1979; Bondioli et al. 1990; Giannichedda and Mannoni 2003; Guidi et al. 2003). As we know that all the inferences done on archaeological contexts are out from the sphere of empirical verification, we could not even exclude that all the theories on prehistory might be false (see Outram 2008). Therefore, experimental archaeology appears as a good instrument to empirically test hypothesis about the development of metalworking technology and the role of artisans in the Bronze Age societies.
To move a step beyond such conservative approaches, we tried to apply a multidisciplinary praxis involving researchers coming from different fields of academic and practical knowledge (archaeology, archaeometallurgy, archaeometry, experimental archaeology, pure craft, et cetera).
The resulting project is called Smiths in Bronze Age Europe and was conceived and directed by the Museo Civico Archeologico Etnologico di Modena within the frame of the OpenArch program. It is funded by the EU with the aim of fostering cooperation and exchange among Archaeological Open Air Museums in Europe. The principal goal of the whole project is to understand the social and economic organization hidden behind the multiform evidences of Bronze Age metallurgy, with a special focus on the Terramare area, namely the Po Plain.
Terramare culture is one of the major features of Middle-Recent Bronze Age Europe (1650-1150 BC circa) both in terms of the significance and abundance of archaeological remains, as well as in the geographical position; they functioned as a joining belt between Central Europe (especially the Danube-Carpathian Basin) and the Mediterranean world (for an exhaustive frame of Terramare culture see Cardarelli 2010, 449-455; Bernabò Brea et al. 1997). Referring to the subject of this article, it is important to point out that Terramareartisans developed a high degree of metal production both in quantitative and qualitative terms. All crafts, not only metalworking, were supported by a flourishing agricultural-based economy. Metal arrived from distant areas via a complex network of traffic, which also guaranteed a supply of exotic goods like amber from the Baltic area and Mycenaean pottery from the Aegean (Cardarelli 2010).
The geographic and chronological framework of this current project is narrow, and we have two aims: to investigate the Terramare Bronze Age technology in relation to stone mould production; and to test the potential of a holistic approach, so often strongly claimed by scholars but not always applied for the reasons here explained (Thornton and Roberts 2009, 182).
Archaeometallurgy represents one of the major fields of conflict between different research methods, techniques and philosophies, and as a result there are a wide range of interpretations about the impact of metallurgy on pre-protohistoric societies.
This derives from two principal facts. First of all, the study of artefacts, metal outcrops in the territory and of employed techniques forces ‘human scientists’ (archaeologists) and ‘pure scientists’ (archaeometallurgists, geologists, chemists or physicists) to cooperate, starting from very different, often antithetic, methodological approaches. Second, the debate is heated because of a simple question of centrality: among all the prehistoric technologies, metalwork seems to play a key role in driving the transformation towards the complex societies of the Bronze Age, based on labour division, specialisation, widespread trade and a more stratified social structure.
Nevertheless this socio-economic process that developed in Bronze Age Europe took place with different features throughout space and time, and the quest for a unique model risks the production of restrictive interpretations. As a general trendin Europe, a certain uniformity in the bronze object typologies is visible in the Early Bronze Age; in the Middle Bronze Age it tends to reduce, being marked by a more articulated typological spectrum (Peroni, 1989; Cardarelli 1992, 394, see also Bietti Sestieri 2010, 74). Even if many authors have claimed that a metallurgical koiné emerged in the Late Bronze Age, starting from quite homogeneous typologies of objects (especially weapons, ornaments and bronze decorated pots; Carancini and Peroni 1997, 595), the framework has now become much less unitarian, especially in consequence of a deeper look at the variability of features, structures and ‘toolkits’, namely the set of tools and techniques involved in the chaîne opératoire (Speciale and Zanini 2010; Bianchi 2010; Bianchi in press).
The typological homogeneity of bronze items in the Late Bronze Age is the most evident output of the circulation of people and models through Europe, intensified along routes supply routes for the raw materials1 , which were already existent in former periods. However, a metallurgical koiné, inferred from the typological analysis of bronze objects, does not necessarily imply that the category of metalworkers operated with the same modes of production and at the same socio-economic level everywhere. Different technologies and networks can considerably influence the quantity and the quality of artefacts produced locally, developing regional adaptations and preferences, as can be seen for example in the techniques of sword/rapier casting, which significantly varies depending on the available raw materials for their moulds production (sandstone, soapstone, clay, et cetera; Pellegrini and Scacchetti, in press).
The heterogeneity of the techniques can be also interpreted as a strong tendency to experimentation and innovation, which for example occurred in the Middle Bronze Age as result of a real 'mass production'2 (Iaia et al., in press), which likely continued at the beginning of Late Bronze Age.
In the following paragraphs we will explore the subject of stone mould production in the Terramare area, trying to analyse skills, knowledge and tools involved in the manufacturing process of a Bronze Age flanged axe.
Materials
A large number of stone moulds haves been found at Terramare sites since the 19th century (for a catalogue see Le Fèvre-Lehöerff 1992). They were made to produce a wide range of bronze objects, such as ornaments, weapons and tools, but the most represented items are axes and daggers. Empirical observations made from casting experiments pointed out that not all the types of stone common in the Terramare area have a good resistance to the heat of molten metal. In collaboration with the Department of Earth Science of the University of Modena and Reggio Emilia, we studied 96 moulds, or fragments of them, from ten terramare areas, such as Modena and Reggio Emiliatoday held in the Archaeological Museum of Modena and in the Civic Museums of Reggio Emilia, in order to understand which types of stone were used by the ancientcraftsmen and to find the possible sources of raw material (Barbieri 2006; Barbieri and Lugli 2012).
Analytical Methods
The analysed moulds are made of fine-grained detrital sedimentary rocks. For the identification of the rock types we took small samples from the original moulds in order to produce thin sections for analysis under an optical microscope (see Figure 1). We identified five different groups of lithotypes: the most represented are calcarenite and biocalcarenite (see Figure 2). Fine-grained carbonate rocks, the most abundant in the investigated area, have the advantage of being easy to work with and resistant to thermal shock.
We identified the main geological formations of origin of these lithotypes (Pantano Formation, Monte Cassio Flysch): they outcrop a few kilometres away from the nearest sites to the low Apennines (see Figure 3). However, the origin of one type of calcarenite, the principle stone used especially in the Modena area, is still unknown. It is possible that this type of stone comes from a small outcrop not detected in our surveys, either exhausted in the past, or that it is not a strictly local stone.
Apparently, a correlation between rock types and categories of objects carved into moulds does exist. Calcarenite was mainly used to produce moulds for daggers, small bars and ornaments (thin and small objects), but never used for axes. Calcareous sandstone was used to produce moulds for big and thick, but also simple, objects, like axes and large bars. The biocalcarenite is the most used lithotype, both for objects of reduced thickness and in some cases of major detail, such as daggers, small bars, rings and razors, and for objects of greater thickness, which are therefore subject to heavier thermal shock, such as axes and large bars (see Figure 4). The selection of these stones could be justified by their availability in nature, by the properties of heat resistance and by the workability characteristics.
Experimental Reproduction
Starting from the archaeological record and the series of petrographic analysis presented above, we decided to reproduce a replica of a Bronze Age mould in order to provide information about skills, knowledge and tools that could be involved in this phase of such manufacturing process.
As a model we chose a fragmentary mould for a simple axe from Montale Rangone, a site that actually represents one of the best known terramara in the Po plain. The stone mould was found in the oldest 19th century excavations, and can be dated at the Middle or Recent Bronze Age (1650-1150 BC). As it comes from non-stratigraphic excavations, a more precise chronology is quite difficult to attribute; moreover the simple, undetailed shape of the axe can not be ascribed to a specific phase. During more recent and modern excavations (1996-2002), a casting pit was discovered in association with fragments of other moulds, crucibles and slags, clear evidences of an operating workshop (Candelato et al. 2002, 266). According to the stratigraphic and chrono-typological series, the context was dated up to the Middle Bronze Age 3 (OxA- 12412: 1450-1380 BC cal 59%; Cardarelli and Labate 2009).Therefore, we can not exclude that the axe mould comes from the same phase, but at the moment it seems more appropriate to maintain a certain prudence on this subject.
The mould is fragmentary but the missing part has been reconstructed on the basis of bronze axes and other axe moulds. Its dimensions are: 11 cm height (the preserved portion), 9.8 cm width, 4.5 cm thickness, while the axe measurements are 9.6 cm preserved height, 4.6 cm maximum width, 1.4 cm maximum depth (see Figure 5).
As the archaeological finds seem to suggest, moulds of this period for simple axes were monovalve; we assume that the matrix was covered with a flat, dimensionally congruent, valve. The two valves were then bound together and the pouring metal came from above (Carancini et al. 2001).
Back to the focus of this work, the material, the stone used is a biocalcarenite of the so-called Pantano Formation. Other finds reveal that this material choice was broadly shared by Bronze Age metalworkers of this area. For example, a similar mould comes from Gorzano, another terramara, located 7 km south from Montale Rangone (see Figure 6). Archaeological evidence of metalworking in Gorzano are quite numerous, including not only finished artefacts but also implements for casting and refining (ceramic crucibles and tuyères, stone moulds, bronze chisels and awls; see Figure 7). Unfortunately the excavations took place in the 19th century and were not systematically led (see Pellacani 2007).
Taking into account the edited geological maps, the most accessible source of biocalcarenite of Pantano Formation was traced out on the hills during an extensive survey campaign. It is located less than 3.5 km in a straight line from Gorzano and 10 km from Montale. Both sites and the stone outcrop stand on the sides of the creek Tiepido.
Although it seems to be obvious, it is nevertheless important to remember that a proper block of stone should be chosen in terms of size, shape and texture, in order to reduce the amount of labour and the time consumed. The biocalcarenite should be both massive and compact, free from chinks or fractures.
Before beginning the experiment, a one-day training practice was undertaken on biocalcarenite samples under the supervision of two expert stone-cutters (scalpellini). This experience revealed some very useful tricks for our main experiment. Observations and different attempts were made on the technique used for sketching out the block of stone and for the first flattening of the surfaces. During the whole manual process, great importance was given to three main factors:
- The force of the impact between the hammer and the chisel;
- The angle between the chisel and the stone surface;
- The chiselling direction.
Points 1 and 2 seem to be inversely proportional. Namely, an increase of the angle between the chisel and the stone surface should be followed by a decrease of the force applied to the strike. Furthermore, concerning point 3, the strikes should be given from the edges towards the centre of the surface. This expedience avoids the risk of cracking of the stone.
Manufacturing Process
We started from with an irregularly shaped block of biocalcarenite of about 16 kg, dimensions 35 × 31 × 24 cm, naturally fallen from the outcrop.
The procedure to obtain the mould can be summarized in eight main steps (see Figure 8):
Step 1 | Sketching out of the block and breaking it into two similar sized pieces. |
Step 2 | Forming two regular parallelepipeds quite uniform in size with a stone hammer (a river pebble) and a bronze chisel (12% tin). This work requires the greatest care because of the risk of fractures. To reduce the risk of fractures to a minimum, the previous remarks from stone-cut experts (especially points 1 and 2) proved to be very efficient. The majority of waste product was produced in this phase. |
Step 3 | Working softly on the two surfaces of the valves, decreasing gradually the irregularity with the stone hammer and bronze chisel. Instead of the chisel, a flanged axe was also tested. Thanks to its wide edge, it worked faster and was less invasive on the stone. Again the expert advice (point 3, direction of chiselling) was very helpful during this phase. |
Step 4 | Scrubbing the two valves one onto each other using coarse dry sand. After a first flattening of the two corresponding surfaces (Step 3), the chisel did not work so precisely as to make the surfaces smooth enough. The friction of the sand completely erased the minute residual imperfections. In the end we smoothed the two valves on each other without sand, because the very fine grains produced by the friction were sufficient to refine the surface. |
Step 5 | Drawing the axe shape onto a valve. A piece of charcoal proved quite useful. |
Step 6 | Engraving the profile of the shape with a bronze awl. As it has to be submitted to strong muscular pressure, it should be handled properly. Good results can also be obtained by using flint points or flakes. |
Step 7 | Carving the inside part of the mould with a bronze chisel and a hammer, preferably a wood or antler hammer (stone can be too hard, while a softer material allows more cautious strikes: effectively, the detachment of the splinters follows the profile of the axe matrix (Step 5). |
Step 8 | Refining the surface of the matrix with a fine handled bronze chisel. |
Operation | Tools | Difficulty | Time | Waste prod. | |
Step 1 | Sketching out of the block and breaking it into two parallelepipeds quite uniform in size | stone hammer + bronze chisel (12% tin) | 2 | 2 hours | 8 kg circa |
Step 2 | Forming two regular valves | stone hammer + bronze chisel (12% tin) | 3 | 4 hours | |
Step 3 | Working softly on the two surfaces of the valves, decreasing gradually the irregularity | stone hammer + bronze chisel (12% tin) or bronze axe (10% tin) | 2 | 2 hours | 4.3 kg circa |
Step 4 | Scrubbing the two valves one onto each other | coarse dry sand | 1 | 6 hours | |
Step 5 | Drawing the axe shape onto a valve | a piece of charcoal | 1 | Few seconds | |
Step 6 | Engraving the profile of the shape | fine bronze awl (8% tin), or flint | 2 | 10 minutes | |
Step 7 | Carving the inside part of the matrix | stone hammer + fine bronze chisel (12% tin) | 2 | 1 hours | |
Step 8 | Refining the surface of the matrix and of the whole mould | fine handled bronze chisel (4%), a piece of biocalcarenite | 2 | 4 hours |
Considering that this represents a first-experience, the entire process required about 20 hours. We can estimate that a time reduction of 30% can be achieved starting from two small, homogeneous sized, blocks of stone and skipping the first two steps. Finally the valves weigh approximately 1.8 kg each.
The first three steps, which can be considered the hardest ones in terms of physical labour, were carried out mainly by Claudio Cavazzuti, but Monia Barbieri, who had no particular training, managed to work successfully on the stone as well. However, after some hours of labour the right wrist (hammer side) got stressed. The rest of the process was mostly led by Monia Barbieri. This second part is the ‘fine work’, requiring much longer time but surely less physical power.
Afterwards, the mould was used for some casting experiments. The first one failed: most of the molten bronze flew out through a very small fissure, due to a faulty matching of the two valves (see Figure 9). That seemed the result of an unsuccessful step 4 and, for this reason, the operation was repeated. The second experiment gave a good result (see Figure 10). The flat axe was then ready for the hammering and polishing to fully replicate a typical Bronze Age flanged axe.
Concluding Remarks
This experience documents that, at least in terms of skills, this kind of production can be carried out by non-specialised artisans as well, for the following reasons:
- The entire process includes a series of relatively simple operations. Muscular energy is not a discriminating factor (each step might be reproduced also by non-adult male individuals, even if it does not mean that it was in the past; see also Sørensen 1996; Kuijpers 2012, 2);
- Biocalcarenite is very easy to work, even without long apprenticeship or training. Its softness allows small ‘tolerable errors’ during the forming of the valve;
- The shape of this type of axe is large and simple in design,and can be obtained with a monovalve mould, which ignores problems of symmetry;
- The implements involved in the whole process are few and common, and might be non-specific for this kind of activity (see also Speciale and Zanini 2010, 59).
This research suggests that biocalcarenite is a very efficient material and, like soapstone, is widely used in many parts of Europe (see for example Gambari et al. 2007; Peche-Quilichini et al. 2012; Nilsson in press). It is easy to work and, at the same time, resistant to high temperatures and to multiple re-use. Other biocalcarenite moulds we produced over the last few years have been employed in hundreds of experiments without fracturing.
Nevertheless, although not covered in this investigation, other kinds of stone are less frequently documented for the production of casting moulds. They probably need a lot more work and specific tools for carving and shape refining. This could be the case for a multiple mould from Casinalbo (MO), for the production of razors and spear-heads, made from an ophiolitic rock (see Figure 11).
We also have to take account of the degree of complexity of the object itself. The flanged axe, typical of Terramare culture does not require big blocks of stone or specific tools to shape the mould, which was mainly monovalve. The lack of minute and/or complicated details in the shape of the axe helps preserve the mould from the effects of thermal. The same observation can be made about daggers or sickles, as well. As we asserted above (see Figure 4), the large majority of axe and dagger moulds from Terramare are made out of sandstone (biocalcarenite, calcareous sandstone, calcarenite, quartz sandstone), which can facilitate mass production, thanks to the endurance of the valves.
We may suggest that there is a deliberate connection between the type of bronze object and the nature of material used for its moulds, and may be related to technological choices.
Other studies led by the same research team have raised doubts about the hypothesis that Bronze Age swords or other big and/or detailed objects could be cast in stone moulds due to the extreme rarity of such archaeological finds (Pellegrini, Scacchetti, in press). It appears to be very likely that casting technologies varied depending on the physical properties of the object (shape, size) and its use, as well. But we cannot exclude that material technological innovations might, for example, drive a typological (aesthetic or even functional) change in a particular category of object.
The low skill-degree required for the production of biocalcarenite moulds for axes, however, is not sufficient proof that it commonly took place at a household level and/or led by non-specialised artisans. We have to consider that our basic level technical experience in stone working is balanced by a deeper scientific (and empiric) knowledge in lithology, petrography, material physics, topography and geological resources.
However this experiment may help to better distinguish the specific skills and knowledge involved in a craft side-activity, where they are often ambiguously treated in the archaeological theory.
Since Childe’s essays, it has often been assumed that primary and secondary metallurgy in Bronze Age Europe were specialised manufactures, for they need deep empirical knowledge, prolonged apprenticeship and experience, manual skills and time (Clarke 1968, 238-239).
Vere Gordon Childe in his introduction to The Bronze Age assumed that:
The masters of these mysteries, the first smiths, were perhaps the first independent craftsmen […]. The art of the smith was so complicated that prolonged apprenticeship was required. His labour was so long and exacting that it could not be performed just in odd moments of leisure; it was essentially a full time job. And the smith's products were so important to the community that those engaged directly in food production must provide for his primary needs in addition to their own. Among primitive peoples today the smith always does enjoy just such a privileged position as might be expected (Childe 1930, 4-5).
It is, indeed, quite likely that miners and smiths constituted distinct crafts or even castes, membership of which implied initiation but conferred some degree of immunity from the bondage of tribal custom. (Childe 1930, 10; see also 1944).
Even if Childe wrote his essay nearly one century ago (referring these words mainly to Early Bronze Age metalworkers), many of these generalizations have become common sense. In popular scientific literature, prehistoric smiths are usually depicted as mythical figures (according to Homer or Celtic Myth Cycles), standing at the very top of the working class, representing a “detribalized” caste, playing ritual or even religious functions, and ‘flirting’ with the emerging warrior elites, who provide a demand for bronze goods, like weapons and ornaments. We have also to remember that Homer writes in the ninth-eighth century BC (at least three century after our period of investigation), and Nordic mythology comes from much more recent times. Can we backdate this view to the all Bronze Age metalworkers?
Other views have been widely expressed. Recently Tobias Kienlin (2012, 21) discussed this elite-related generalization, arguing that the spread of metallurgy may have taken place along kinship lines.
As Cathy Lynne Costin (2008, 149) also argues, “Ethnographic studies of small scale societies suggest that many artisans produce craft goods for others while remaining basically self-sufficient in terms of primary subsistence needs”. After a wide list of ethnographic examples, ranging from Africa to Southeast Asia, Rowlands concludes that each society shows a different attitude towards the smith, and no particular status can be automatically assigned to him (Rowlands 1971, 217).
Returning to the archaeological issues, unfortunately not many Middle-Recent Bronze Age metalworking sites are known in Northern Italy. Our framework about features and topographic relationships between craft and settlement areas still remains quite poor (Cardarelli and Labate 2004;Cierny et al. 2001; Cavazzuti et al. in press; Bianchi 2010).
What seems to emerge, step by step, from the preliminary results of the Smiths in Bronze Age Europe” project, is that metalworking in the Terramare culture appears as a multi-layered activity, consisting of different levels of production, involving several skills and different fields of knowledge (Iaia et al. in press). If we accept that it was a multi-layered craftsmanship, every unique model of ‘metallurgist’ in Bronze Age Europe represents an oversimplification, as other authors have already noticed (Rowlands, 1971; Costin, 2008; Kujipers, 2008); in dealing with the complexity of the phenomenon through space and time, we have started to explore new perspectives and test new hypothesis.
The variability of the necessary technical degree depends basically on the category of objects produced (Fontijn 2002; Kujipers 2008, 2012), but the supply of the raw materials themselves (proper clays, stones, sands, woods) employed in the whole process seems to play in this sense a primary role, because it influences casting techniques and final results.
A recent experiment carried out in the Open Air Museum Terramara di Montale also showed that non-expert, non-trained, non-archaeologist people can cast a good axe and a good dagger, once they are given essential technical advice about the process. The post-casting phases, in the case of axes and daggers, are not so complicated but need time, especially for hammering the flat axe to create the flanged type. Finally, time is an important variable to consider in the definition of different levels of production, objective measurements are quite difficult to obtain in such experiments, as they depend on personal attitudes and abilities.
We do not really know if it may be possible to ascribe the production of these kinds of moulds and axes to a domestic or household level, in the sense of low intensity production or non-specialised, non-full-time labour. We need much more archaeological evidences to get a deeper look inside the question and a reliable interpretation, using the categories, frames and generalizations to which we normally refer in the scientific debate. Yet, many scholars often mention the skillof the ‘metalworker’ (Earle, 2004, 161; Kristiansen and Larsson, 2005, 51–61) to argue for the specialised and ritualised nature of metalworking.
What we can surely now assert is that for Terramare flanged axe production special manual skills or a long apprenticeship is not required. As a counterpart, however, the metalworker (a real specialised artisan or not) requires the (pre-) scientific knowledge to recognise the best raw material and its location in the surrounding areas. To emphasize the preeminent role of knowledge we can recall Childe: “To recognize the continuity underlying such transformations, to appreciate their practical significance and to devise means for their control demanded a power of inference and synthesis unusual in barbarians. The discoverers [of metallurgy] must implicitly make the distinction between substance and its appearances and so may justly claim a place among the founders of science” (Childe, 1930, 4).
Beside knowledge, the metalworker, his (kinship, role or rank -based) corporate group or the community in which he operates, needs access to the raw material (outcrop). This probably means that he/it has to play a role in the political scenario, and for us as researchers implies a much harder effort is needed to reproduce a good picture of early metalworking, because it forces us to combine traditional methods with chrono-typological classifications, pure sciences, spatial analysis, experimental archaeology, and so on in the study ofold and new evidences.
- 1While copper is quite abundant, for the widespread presence of sulphide ores, tin deposits are extremely rare in Italy (small deposits are documented in Sardinia and Tuscany; Giardino, 2010, pp.134-136).
- 2 To have a general idea of the potential amount of daily production in a Bronze Age workshop, some expert artisans experimented that three persons may produce up to 30 sickles in 6 hours (Binggeli et alii, 1997, p. 569). Looking inside the Terramare moulds collections, we can also find sandstone moulds for serial production (see for example Le Fèvre- Lehöerff,1992, pp.227).
Bibliography
BARBIERI, M., 2006. Le forme di fusione del Museo Civico Archeologico Etnologico di Modena: classificazione tipologica e caratterizzazione dei litotipi, Tesi di Laurea in Scienze dei Beni Culturali, Università di Modena e Reggio Emilia.
BARBIERI, M. and LUGLI, S., 2012. Forme di fusione dalle terramare del territorio modenese e reggiano: caratterizzazione dei litotipi e individuazione delle provenienze, in Atti del VII Convegno Nazionale di Archeometria, Modena.
BERNABÒ BREA, M., CARDARELLI, A. and CREMASCHI, M., 1997. Le Terramare. La più antica civiltà padana, Milano: Electa.
BIANCHI, P.A.E., 2010. La produzione metallurgica a Beneceto Forno del Gallo (PR). Organizzazione spaziale e produttiva all'inizio del Bronzo Recente.Padusa XLVI, pp.9-36.
BIANCHI, P.A.E., (in press). Metallurgia e spazi produttivi nel Bronzo Recente in Emilia, in Atti della XLV Riunione Scientifica IIPP, 26-30 ottobre 2010.
BIETTI SESTIERI, A.M., 2010. L'Italia nell'età del bronzo e del ferro: dalle palafitte a Romolo (2200-700 a.C.), Roma: Carocci.
BINGGELI, M., BINGGELI, M., BOSCHETTI, A. and MÜLLER, F., 1997, Una dimostrazione di archeologia sperimentale: la fusione di oggetti in bronzo. In: M. Bernabò Brea, A. Cardarelli and M. Cremaschi, ed.1997. Le Terramare. La più antica civiltà padana, Milano: Electa. pp.567-569.
BONDIOLI, L., LEONARDI, G., LEVI, S.T., MICHELI, M., PRACCHIA, S., VANZETTI, A., VIDALE, M., 1990. Archeologie di oggetti e archeologie di processi: stati della questione. Preistoria Alpina, 24 (1988), pp.203-215,
CANDELATO, F., CARDARELLI, A., CATTANI, M., LABATE, D. and PELLACANI, G., 2002. Il sistema informativo della terramara di Montale (Castelnuovo Rangone – Modena). In: C. Peretto, ed. 2002. Analisi informatizzata e trattamento dati delle strutture di abitato in età preistorica in Italia. Firenze: Istituto Italiano di Preistoria e Protostoria. pp.257-260)
CARANCINI, G.L. and PERONI, R., 1997. La koiné metallurgica. In: M. Bernabò Brea, A. Cardarelli and M. Cremaschi, ed. 1997. Le Terramare. La più antica civiltà padana. Milano: Electa, pp.595-601.
CARANCINI, G.L., CARDARELLI, A., BELGRADO E. and GUATELLI R., 2001. Esempi di metallurgia dell’età del bronzo. Convegno di Archeologia Sperimentale. Comano Terme - Fiavè, 13-15 settembre 2001.
CARDARELLI, A., 1992. Le età dei metalli nell'Italia settentrionale. In: A. Guidi, M. Piperno, ed. 1992. Italia Preistorica. Roma: Laterza. pp.366-419.
CARDARELLI, A. and LABATE, D., 2009, Lo scavo 1996-2001. In: A. Cardarelli, ed. 2009. Guida al Parco Archeologico e Museo all’Aperto Terramara di Montale. 2nd ed., Carpi: Nuovagrafica. pp.33-51.
CARDARELLI, A., 2010.The collapse of the terramare culture and growth of new economic
and social system during the Late Bronze Age in Italy. Scienze dell’Antichità, 15. pp.449-520.
CAVAZZUTI, C., PELLEGRINI, L., SCACCHETTI F. and ZANNINI, P., (in press), Tracce di fosse di fusione dalle Terramare: ci siamo persi qualcosa? In: Atti della XLV Riunione Scientifica dell'Istituto Italiano di Preistoria e Protostoria, Modena, 26-31 ottobre 2010.
CHILDE,V.G., 1930. The Bronze Age. Cambridge: University Press.
CHILDE,V. G., 1944. Archaeological Ages as Technological Stages. Journal of the Royal Anthro- pological Institute of Great Britain and Ireland, 74, pp.7-24.
CHILDE, V. G.,1958. The Prehistory of European Society. London.
CIERNY, J., DEGASPERI, N., FRONTINI, P. and PRANGE, M., 2001. Le attività metallurgiche. In: P. Frontini, ed. 2001. Castellaro del Vhò. Campagnedi scavo 1996-1999, Como: New press. pp.57-78.
CLARKE, D.L., 1968. Analytical Archaeology. London: Methuen.
COLES, J., 1979. Experimental archaeoogy, London: Academic Press.
COSTIN, C.L., 2008. Thinking about Production: Phenomenological Classification and Lexical Semantics. In: Z.X. Hruby, R.K. Flad, ed. 2008. Rethinking Craft and Specialization in Complex Societies: Archaeological Analyses of the Social Meaning of Production. pp. 143-162.
EARLE, T., 2004. Culture Matters: Why Symbolic Objects Change. In: E. DeMarrais, C. Gosden, C. Renfrew, ed. 2004. Rethinking materiality. The engagement of mind with the material world, Cambridge Research 2004, pp.153–167.
FONTIJN, D.R., 2002. Sacrificial landscapes. Cultural biographies of persons, objects and “natural” places in the Bronze Age of Southern Netherlands, c. 2300-600 BC. Leiden (Analecta Praehistorica Leidensia 33/34).
GAMBARI, F.M., RUBAT BOREL, F., COMPAGNONI, R., 2007. Le forme di fusione e l’utilizzazione preromana della “pietra ollare” nella protostoria dell’Italia nord-occidentale. In: La pierre en milieu alpin, de la Préhistoire au Moyen Age. Bullettin d’Études Préhistoriques et Archéologiques Alpines, 18, pp.131-151.
GIANNICHEDDA, E., MANNONI, T., 2003. Archeologia sperimentale e archeologia delle produzioni. In: P. Bellintani, L. Moser, ed. 2003. Archeologie sperimentali. Metodologie ed esperienze fra verifica, riproduzione comunicazione e simulazione, Trento, pp.33-39.
GIARDINO, C., 2010. I metalli del mondo antico: introduzione all’archeometallurgia. Roma, Bari: Laterza.
GUIDI, A., BELLINTANI, P., CHELIDONIO, G., LONGO, L., 2003. Archeologia sperimentale nell'archeologia italiana. In: P. Bellintani, L. Moser, ed. 2003. Archeologie sperimentali. Metodologie ed esperienze fra verifica, riproduzione comunicazione e simulazione, Trento, pp.49-77.
IAIA, C., (in press). Experimental apporaches to tools and technical skills of the bronze age smiths in the Terramare area (Northern Italy). In: Proceedings of the International Conference “Craft and People, Agents of Skilled Labour in the Archaeological Record”. London, British Museum, 1-2 November 2012.
KIENLIN, T.L., 2012. Beyond Elites: An Introduction. In: T.L. Kienlin, A. Zimmermann, ed. 2012, Beyond Elites. Alternatives to Hierarchical Systems in Modelling Social Formations. International Conference at the Ruhr-Universität Bochum, Germany, October 22-24, 2009.
KRISTIANSEN, K. and LARSSON, B., 2005. The rise of Bronze Age society. Travels, Transmissions and Transformations. Cambridge: Cambridge University Press.
KUIJPERS, M. H. G., 2008. Metalworking in the Netherlands (c. 2000-800 a.C.). A research into the preservation of metallurgy related artefacts and the social position of the smith. Leiden.
KUIJPERS, M. H. G., 2012. Towards a Deeper Understanding of Metlworking Tecnhology, in T.L. Kienlin, A. Zimmermann, ed. 2012. Beyond Elites. Alternatives to Hierarchical Systems in Modelling Social Formations. International Conference at the Ruhr-Universität Bochum, Germany, October 22-24, 2009.
LE FÈVRE - LEHÖERFF, A., 1992. Les moules de l’age du bronze dans la plaine orientale du Po: vestiges de mise en forme des alliages base cuivre. Padusa XXVIII, pp.132-242.
NILSSON, A., in press. Casting bronze in stone. Soapstone moulds in Southern Scandinavia during the Late Bronze Age. Origin – Use – Distribution. In:Proceedings of the International Conference “Craft and People, Agents of Skilled Labour in the Archaeological Record”. London, British Museum, 1-2 November 2012.
OTTAWAY, B.S. and ROBERTS, B.W., 2008. The Emergence of Metallurgy, in A. Jones, ed. 2008. Prehistoric Europe: Theory and Practice. Oxford: Wiley-Blackwell. pp.193-225.
OUTRAM, A.K., 2008. Introduction to experimental archaeology, World Archaeology, 40 (1), pp.1-6.
PECHE-QUILICHINI, K., GRAZIANI, J., ANTOLINI, G.F., GARDELLA M.-A. and MILLETTI, M., 2012. Les Moules de fondeur protohistoriques de Corse: état de la recherche et découvertes recentes. In: Chronologie de la Préhistoire Récente dans le sud de la France. Acquis 1992-2012/Actualité de la Recherche. Aiaccio 18-20 octobre 2012.
PELLACANI, G., 2007, “Monografia ed iconografia”. Una rivisitazione degli scavi di Gorzano attraverso gli scritti di Francesco Coppi e dei suoi contemporanei. In: Grandi, belle e rarissime specie. La vita e le ricerche di Francesco Coppi. Modena: TEM. pp.97-153.
PELLEGRINI, L. and SCACCHETTI, F.,(in press). Observations on Italian Bronze Age sword production: archaeological record and experimental arcaheology. Proceedings from the 7th UK Experimental Archaeology Conference, Cardiff, 11-12 January 2013.
ROWLANDS, M.J., 1971. The archaeological interpretation of prehistoric metalworking. World Archaeology, 3(2), pp. 210-224.
SØRENSEN, M. L. S., 1996. Women as/and metalworking. In B. Devonshire, B. Wood, ed. 1996. Women in industry and technology from prehistory to the present day. Current Research and the Museum Experience. Proceedings from the 1994 WHAM Conference, London.
SPECIALE, C. and ZANINI, A., 2010. Gli scalpelli nella Protostoria italiana. Definizione e proposte per una tipologia. Padusa, XLVI, pp.37-80.
THORNTON, C.P. and ROBERTS, B.W., 2009. Introduction: the Beginning of Metallurgy in a Global Perspective. Journal of World Prehistory, 22, pp.181-184.