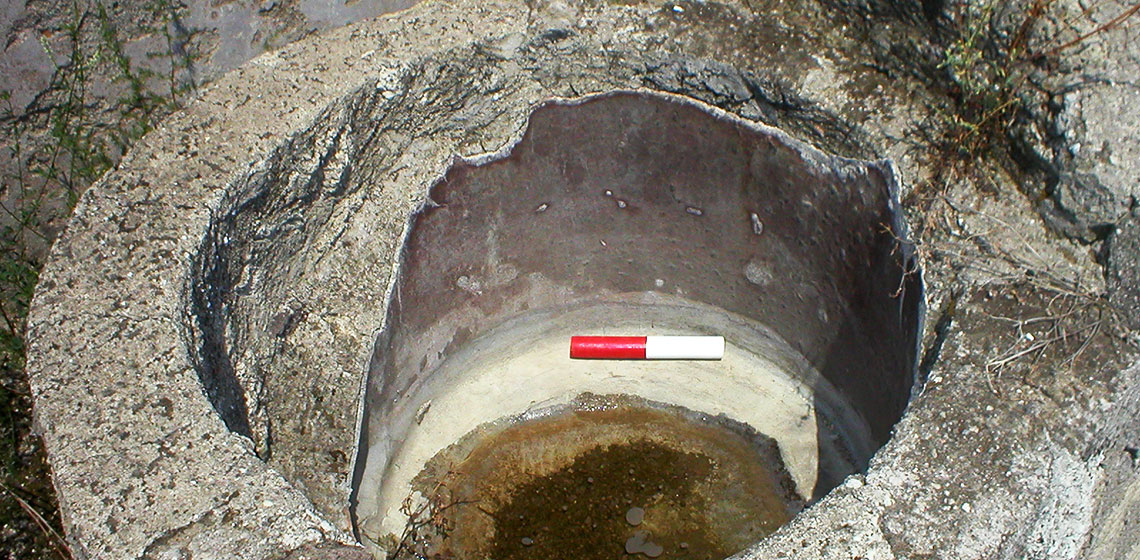
Dyeing, especially in bright, intense colours, has been one of the methods used to embellish textiles and add to their value. A considerable dyeing industry can be shown to have existed in Pompeii. The city of Pompeii was destroyed in a volcanic eruption in AD 79, but its remains were preserved in situ (after Allison 1992). This includes six dyeing workshops (Moeller 1976). The six workshops, together contained between them, forty apparatus consisting of a kettle in a brick or rubble and mortar surround to house a fire for heating the kettle (A survey was undertaken in 1994; Robinson and Janaway, unpublished). The kettles were supported by a ring of material which their bottom edge rested on; thereby leaving most of the kettle bottom unsupported. The dyeing apparatus were extensively researched by Hopkins (2007, 2008) to gain a better understanding of the scale of industry.
During this research, a new survey of the workshops and dyeing apparatus was undertaken. This included a recording of all the workshops and the individual apparatus, as well as their context. The surviving kettles, whose size varied between 90 and 900 litres, were cylindrical with flat bases and they were all made of lead. The use of lead provoked fundamental questions about the process of dyeing in Pompeii. Experiments undertaken at Textilforum 2012 explored the use of different metals in the dyeing process and explained why lead had been chosen by the dyers.
Preliminary research
For Hopkins' work on the Pompeii dyeing industry, a replica dyeing apparatus was constructed. This was based on apparatus five in property VII ii 11 (See Figure 1), with a capacity of 130 litres.
The use of lead in the original kettles, however, could not be reproduced in Hopkins' experimental replica due to health and safety considerations. A thermal and physical match had to be substituted. Stainless steel was such a close comparison that this was used instead for Hopkin's replica apparatus. Other than its thermal conductivity properties, though, the kettle material remained largely unconsidered.
The replica apparatus was used to evaluate the possible output of the Pompeii dyeing industry.
Questions regarding the dyeing process and the kettle material
The findings regarding the possible output of the Pompeii dyeing industry, based on experimental dyeing runs with the replica apparatus, were presented at the first European Textile Forum (Textilforum) in 2009. At this conference, it was found that although the science and archaeology were valid, the dyeing was not in keeping with a modern understanding of historic dyeing. The understanding of the dyeing process used for the study, including experiment design and setup, had been gained from reputable academic sources, but had been restricted to those available in Britain at the time of study. This problem had been touched on by Hopkins (2007) who noted that Monaghan’s thesis on Greek dyeing (Monaghan 2001) stated that no written recipes survived, yet Hopkins cited the early modern German source Lagercrantz (1913) who translated the Greek recipe to modern German. This unfortunate omission is part of the wider problem of missing sources when undertaking archaeological research.
Two questions were considered especially interesting during this conference: whether the textile material was dyed in the fleece, in the yarn or in the cloth; and why lead was chosen as the kettle material for all the surviving vats.
Hopkins, after extensive study of the available literature (for example Wild 1970, Frayn 1984, Ryder 1990), had used the dyeing of fleece as the basis for calculating the output of the dyeing industry. It is theoretically possible to dye fleece (unspun fibre), yarn, or cloth, though every material poses its own challenges to the dyer.
It is commonly assumed that examples showing no white core inside the fibres would have to be dyed in the fleece, before combing, spinning and weaving the cloth (after Wild 1970, after Ryder 1990). However, this can result in a large amount of waste in raw material since fleece is very sensitive to movement in hot liquid, especially in alkaline liquid, factors that are essential to the dyeing of mordanted colours such as yellow, green and red. Moving the textile material is essential for an even outcome of the dyeing in a hot dye bath. Blue, achieved with either indigo or woad, is not dyed hot and the material is not moved much during the dyeing process. Therefore, to dye a fleece blue without significant loss of material is possible. Similarly, a cold mordanting and dyeing process suitable for dyeing fleece may be feasible for different colours; however, this is not plausible in the case of the Pompeii workshops - these contained heating apparatus. Although it is possible to dye cold by simply not heating the apparatus, all the apparatus found were heatable, suggesting limited need for cool apparatus. Furthermore, keeping them cool would have been problematic due to conduction and ambient temperature. For mordanting colours, dyeing a fleece would mean dyeing fibres that would be sorted out as waste during fibre preparation for spinning. As frequent movement of the material to be dyed is necessary for an evenly dyed result, and fibres felt together easily when agitated in a hot alkaline solution, this might reduce considerably the output of spinnable fibre after dyeing.
The results of any dyeing process will vary a lot, depending on the mordant, plants used for dyeing, the raw material, the thickness of the yarn or the cloth, the twist of the yarn and even the quality of the wool itself. This is the case even if the same technique, apparatus and plants have been used, because all those factors influence the receptivity of the fibres. Above all even the quality of water, the presence or absence of chalk/calcium, will influence the colour, most visibly when using weld or madder. The intensity of the dye depends on all those factors and defines the quality of the dyed material, fleece, spun yarn or cloth. It is, in any case, possible to have yarn or fabric completely dyed through, even though it was dyed not in the fleece, but as yarn or in the cloth. While a white core or white spots in yarn or fabric can be seen as proof that something was dyed in the yarn or in the cloth, it is not possible to assume that anything not showing a white core was dyed in the fleece, as complete dye penetration is possible when dyeing yarn or cloth.
The last remaining important factor for the dyeing process is the kettle itself. The apparatus in Pompeii vary in size, the largest one at 900 litres being almost a modern industrial size. The form and height of the kettles, which are cylinders of varying height and diameter, suggest the dyeing of spun yarn - from the dyers' point of view - since spun yarn can be dyed hanging on racks in the pot. This would explain quite well the form of most of these kettles. This method would of course enlarge the output of the industry enormously in comparison to the theory of dyed fleece.
The original study calculated that Pompeii could have produced 48,972 - 53,106 dyed fleeces annually. This appears a large figure, but if the population of Pompeii were approx. 12,000 people (Storey 1997), that would mean 4.1 - 4.4 fleece per person, 8.2 - 8.8 kg, which is the equivalent to a large (laundrette) washing machine load (Hopkins 2007, 2008). Although not every textile item was dyed and there was a trend for plain clothing with patterns (Bender Jørgensen and Mannering 2001; Pritchard and Verhecken-Lammens 2001; Cardon 2001), soft furnishings tended to be dyed wholly in one colour. Ultimately, when the quantity required to make a single pair of curtains is considered and it is remembered that the quantity per person would also have to stretch to commercial, government and religious premises, 8.8kg per person appears to be very small. Even with an output three times as large as the original estimate (Hopkins 2013a, Hopkins 2013b), the dyeing industry would still have been relatively small, certainly not large enough to be a centre of manufacture for export throughout the empire as originally stated by Moeller (1976). However, there is still much wiggle room in these estimates. For instance, if a workshop possesses two kettles, each with approx. 90 l capacity, one of the kettles can be used for mordanting while the other, in parallel, can be used to dye pre-mordanted yarn. In a kettle of this size, according to the practical experience Sabine Ringenberg gained from more than ten years of dyeing, at least three kg of yarn can be processed in one batch, possibly more if the yarn is hung on racks. With an estimated time of about two hours per batch for restocking the pot with dyestuff and re-heating, this could result in an output of at least 12 kg of dyed wool yarn per workday.
Apart from a lively discussion on the possible output of a dyeing workshop and the question of whether yarn or fleece were dyed in the apparatus (reassessed findings in Hopkins 2013a, b, c), the kettle material of the original kettles roused much interest, finally resulting in an archaeological experiment on the influence of metal vessels when dyeing.
During the survey it had been noted that all of the surviving dyeing vessels had been constructed from lead, confirmed in a test undertaken in 2005 (Monteix and Pernot, unpublished). This was noted as an archaeological curiosity, as it was known that the Romans were aware of lead’s toxic nature (Vitruvius VIII), but no further importance was attached to the finding. During the reconstruction, other than its thermal conductivity properties, the kettle material had been largely unconsidered.
Lead is a weak, malleable metal, properties that lend themselves to the physical manipulation necessary to construct a water delivery network, but it had been chosen for use in construction of a mostly unsupported kettle designed to be in direct contact with the flames heating it. Even though the heat was drawn away by the water contained within it, limiting the maximum temperature of the lead to about 100°C, the sheer weight of the water and the fabric meant the kettle may have been unstable. Two findings shed light on this quandary.
Calculations showed that regardless of the size of each kettle, their design meant each was exposed to the same amount of pressure on its bottom by the water it contained, so there was no difference in stability between the larger and smaller kettles. The other finding was that when the photos of the dyeing apparatus were re-examined, concentric circles were noticed in the bases of the dyeing apparatus. This means that they had been subject to ‘creep’, a continous deformation during use resulting in a sunken, concave bottom instead of the original flat bottom. So the lead kettles had in fact been structurally unstable, but not in a way that would have heavily influenced their use in the workshop. The circles can be seen in apparatus five in property VII xiv 17 (See Figure 2). When a computer simulation was constructed to test the outcome of heating the kettles during dyeing, it was discovered that although they did develop deformations in their bottom part, they did not actually break. This result could be seen in reality in apparatus six in property VII xiv 17 (See Figure 3).
This instability during use raised the question of why lead had been used instead of copper or iron, which had been available and would have been much more resilient materials. The most obvious answer is that lead may have presented a chemical property beneficial to the dyeing process, which outweighed the problems of physical instability. As it happens, copper and iron are both known to be mordants that have significant influence on the colour outcome.
Experiment preparation
Since lead kettles are not commonly used in plant-dyeing any more, due to the toxicity of lead, no comparison samples for textiles dyed in lead kettles or knowledge about this metal's influence were available. To shed some light on the possible influence of the kettles in Pompeii, an experiment to test their influence on the dyeing result for several different metals was designed and undertaken.
There are such limited textile finds from Pompeii that information and finds of textile processing during the Roman era have to be gleaned from other sites. Contemporary to Pompeii, but at opposite ends of the Roman world, are textile finds from Masada in Israel (Koren 1994, Sheffer and Granger-Taylor 1994) and Hadrian’s Wall in England (Taylor 1983). Analysis of both of these showed that madder (rubia tinctoria) was the most commonly identifiable surviving dye, alum was the most commonly used mordant (usually used in conjunction with the madder) and the most commonly used textile was wool. Because of this, the study chose to mimic the dyeing of wool with madder and an alum mordant to understand the industrial process and output of Pompeii.
Other sources suggest the use of other dyes, even if for restricted use: Pliny’s Natural History stated that although yellow dye was available, it was used specifically for bridal gowns (Pliny, Nat Hist, XXI). This means that although restricted in use by social convention, the dyes were actually used. To continue the earlier study’s experiments with consistency and to replicate another dye used in the Roman world, dyeing with madder to result in a red colour sample and dyeing with birch to result in a yellow colour sample were used in the Textilforum experiment. Both of these are also sensitive to different mordants, and the authors hoped to see considerable influences of the kettle material with these dyes.
There are, basically, two types of dye: mordant and vat dye. When using a vat dye, the material to be dyed is submerged in the dye and it naturally adheres to the fibres. When using a mordant dye, the material to be dyed must first be treated with a solution containing a water-soluble metal salt, the mordant, which then binds to the fibre material. Following this, the textile can then be submerged in the dye-bath and the dye will bind to the mordant and therefore the material. The same dye can result in different colours due to the use of a different mordant. This is called nuancing. Copper and iron are known to make the resultant colour darker or ‘sadden’ it, that is make it ‘murky’. Lead is not known to be used as a mordant, however (cf. mordants listed in Schweppe, Ploss).
But this raises a further question: As the mordant is dissolved in the water in which the material is submerged, then metal salts are already bound to the material during dyeing. Therefore, it should not be theoretically possible that the metal the dyeing kettle is constructed from should heavily influence the dyeing outcome.
The Experimental dyeing process
The experiment to investigate this question was undertaken at Textilforum 2012. It was the inaugural event hosted by the newly opened Labor für Experimentelle Archäologie (LEA) in Mayen, a satellite of the Römisch-Germanisches Zentralmuseum in Mainz. As the LEA has a fully equipped laboratory, accommodation and conference premises, we were able to run the experiment which required mordanting and dyeing procedures over the course of several days.
The aim of the experiment was to see the difference in outcome of dyeing in different kettles. Two experiments were undertaken: dyeing with madder and dyeing with birch leaf. These were undertaken separately in succession. All heating took place in a water bath for consistency. Tap water was used for dyeing as it was of a known content. Distilled water was used for cleaning measuring equipment.
Identical skeins of wool were premordanted with alum in an inert glass vessel. The alum weight was 25% of the wool weight. Each vessel contained a piece of metal 100mm2 to represent the dyeing apparatus consisting of different materials: copper, iron, lead and lead with a superficial oxide layer (See Figure 4); one skein of wool was mordanted and dyed without metal addition to serve as a reference. The wool was boiled in the containers for an hour then left to stand overnight.
Following premordanting, the metal was cleaned and the skeins were then dyed in inert glass vessels, each containing the same representative metal sample. Only half of the quantity of madder usually used was added, as a subtler dye allows changes in colour to be seen easier by the human eye. The mordanted wool was immersed in the vessels, heated up and boiled for one hour, then left to cool for one hour. The pH and temperature were recorded at several points during the experiment. Differences between the pH of the test vessels were noticeable (See Tables 1 and 2).
|
MADDER |
MADDER |
MADDER |
MADDER |
MADDER |
|
reference
|
lead oxidised
|
lead
|
copper
|
iron
|
wool weight dry before mordanting
|
11.3 g
|
11.1 g
|
11.1 g
|
10.3 g
|
10.3 g
|
alum added
|
2.8 g
|
2.8 g
|
2.8 g
|
2.6 g
|
2.6 g
|
pH with alum added
|
4.18pH 19.7°C
|
4.16pH 19.5°C
|
4.18pH 19.5°C
|
4.18pH 19.5°C
|
4.18pH 19.6°C
|
pH before heating, wool and metal plates added
|
4.21 pH 20.2°C
|
4.18 pH 19.7°C
|
4.18 pH 19.7°C
|
4.19 pH 19.9°C
|
4.19 pH 20.0°C
|
pH while heating
|
|
|
|
|
|
pH after boiling*
|
3.35 pH 84.7°C
|
3.37 pH 80.0°C
|
3.34 pH 78.7°C
|
3.36 pH 81.4°C
|
3.67 pH 77.8°C
|
pH after cooling
|
4.04 pH 23.2°C
|
4.05 pH 23.0°C
|
4.05 pH 23.0°C
|
4.06 pH 23.0°C
|
4.20 pH 22.9°C
|
madder/birch leaf weight
|
5.7 g
|
5.6 g
|
5.6 g
|
5.2 g
|
5.2 g
|
pH of dye liquid before adding metal
|
7.24 pH 21.3°C
|
7.19 pH 21.3°C
|
7.14 pH 21.2°C
|
7.06 pH 21.5°C
|
7.17 pH 21.4°C
|
pH of dye liquid after adding metal
|
7.23 pH 21.6°C
|
7.18 pH 21.2°C
|
7.12 pH 21.3°C
|
7.12 pH 21.3°C
|
7.17 pH 21.3°C
|
pH of dye liquid while heating
|
6.45 pH 63.0°C
|
6.35 pH 65.8°C
|
6.35 pH 66.5°C
|
6.45 pH 67.7°C
|
6.40 pH 69.0°C
|
pH of dye liquid after boiling
|
6.40 pH 80.9°C
|
6.32 pH 80.7°C
|
6.33 pH 82.7°C
|
6.44 pH 80.6°C
|
6.55 pH 78.2°C
|
pH of dye liquid after one hour of cooling
|
6.71 pH 51.3°C
|
6.58 pH 50.4°C
|
6.55 pH 51.3°C
|
6.66 pH 50.6°C
|
6.78 pH 49.3°C
|
|
BIRCH |
BIRCH |
BIRCH |
BIRCH |
BIRCH |
|
reference
|
lead oxidised
|
lead
|
copper
|
iron
|
wool weight dry before mordanting
|
11.0 g
|
10.8 g
|
10.8 g
|
10.7 g
|
10.5 g
|
alum added
|
2.8 g
|
2.7 g
|
2.7 g
|
2.7 g
|
2.6 g
|
pH with alum added
|
4.27 pH 19.4°C
|
4.23 pH 19.6°C
|
4.27 pH 19.5°C
|
4.25 pH 19.3°C
|
4.28 pH 19.4°C
|
pH before heating, wool and metal plates added
|
4.25 pH 20.0°C
|
4.25 pH 20.0°C
|
4.26 pH 19.8°C
|
4.25 pH 19.6°C
|
4.25 pH 19.7°C
|
pH while heating
|
3.56 pH 19.4°C
|
3.55 pH 19.6°C
|
3.54 pH 53.5°C
|
3.53 pH 54.2°C
|
3.54 pH 54.7°C
|
pH after boiling*
|
3.30 pH 82.6°C
|
3.37 pH 82.6°C
|
3.35 pH 80.0°C
|
3.34 pH 80.3°C
|
3.61 pH 79.6°C
|
pH after cooling
|
4.20 pH 21.4°C
|
4.20 pH 21.3°C
|
4.20 pH 21.3°C
|
4.18 pH 21.4°C
|
4.30 pH 21.3°C
|
madder/birch leaf weight
|
22.0 g
|
21.6 g
|
21.6 g
|
21.4 g
|
21.0 g
|
pH of dye liquid before adding metal
|
7.00 pH 21.4°C
|
7.11 pH 21.5°C
|
6.85 pH 21.7°C
|
6.79 pH 22.3°C
|
7.10 pH 22.1°C
|
pH of dye liquid after adding metal
|
7.01 pH 20.7°C
|
7.07 pH 20.7°C
|
6.99 pH 20.7°C
|
6.97 pH 20.9°C
|
7.08 pH 21.0°C
|
pH of dye liquid while heating
|
5.98 pH 67.7°C
|
5.90 pH 69.2°C
|
5.83 pH 70.7°C
|
5.82 pH 71.4°C
|
5.89 pH 72.1°C
|
pH of dye liquid after boiling
|
5.45 pH 78.2°C
|
5.47 pH 77.2°C
|
5.35 pH 74.8°C
|
5.36 pH 77.5°C
|
5.69 pH 75.2°C
|
pH of dye liquid after one hour of cooling
|
5.53 pH 48.3°C
|
5.55 pH 46.5°C
|
5.41 pH 46.1°C
|
5.41 pH 46.1°C
|
5.72 pH 46.3°C
|
After cooling naturally, the wool was removed from the dye liquor and rinsed. The dyeing with birch leaf followed the same methodology. Fresh birch leaf of 200% wool weight was used. The birch leaf was first boiled in water to get a dye liquor; for this the birch leaf was cut into pieces, then put into jars with water that were agitated and heated on hotplates until boiling, then boiled for one hour before straining off the leaves. Samples of the mordant and dye liquors were preserved to allow future chemical testing.
All of the equipment that the dye liquor and wool came into contact with was inert, so it can be stated that the distinctive change in colour was caused by the metal plates added to the dyeing vessels. It was predicted that the copper and iron would have a ‘saddening effect’ but it was a surprise to see the brightness of the colour reached with lead, especially oxidised lead (See Figure 5).
Experiment results
While the importance of different mordants to the outcome of dyeing has long been recognised, the experiment showed that the dyeing kettle itself played a much greater role than had previously been thought. The Roman dyers were evidently aware of this and chose lead, which produced the desired and chemically predictable results such as a true yellow. Lead is therefore the ‘neutral vessel’ available to the Roman dyer. This explains the preference for lead kettles in the dyeing apparatus in Pompeii.
The different colours show that the metals were affecting the dye liquor, but as yet the quantity of metal that had dissolved into the water is unknown; first tests on the samples taken were unfortunately unsuccessful in determining this quantity.
Discussion
Before these experiments the importance of the choice of metal had not been fully appreciated. This shows the importance of allowing for a broader understanding of factors before making conclusions about an artefact - the choice of lead appears reckless from a modern structural or safety viewpoint, but for a dyer it is logical as it performs best. If wider factors are not allowed for, false beliefs develop based on flawed logic which eventually go unquestioned. At the start of the original study there was even disbelief that the kettles were made of lead as it appeared so unreasonable.
The original study investigated the structural stability of lead as it was believed that the lead was unstable enough to affect the workshops’ efficiency (Hopkins 2007, Hopkins 2008). Warping or breakage could cause ‘downtime’ that would halt production and necessitate repair, maintenance or replacement of vessels. The dyeing workshops would either have to possess or buy in someone skilled in lead working. Each of these factors would increase the costs the workshop would face. Lead was used, therefore the effect on dyeing was recognised and so desirable that disadvantages were tolerated, or a way had been found to predict and lessen then.
Where the dyers procured their lead is a wider question that could have larger economic implications. Lead was a by-product of silver smelting. This should have meant that it was relatively cheap. Despite some understanding that lead may affect dye colour, it had been supposed that cost was a strong reason for lead to have been chosen for dyeing kettles (Hopkins 2007, Hopkins 2008). It is now possible that lead could have been at a premium as it would be in demand by the dyers. Transport costs could have added to the price of lead. Dyers may have had to regularly replace vessels, through structural failure or tainting by dye, the rate of which is unknown. This means that the original surmise that lead was cheap may be incorrect, another factor that may have affected the dyeing workshops’ costs.
Some dyeing workshops in Pompeii contained vessels that did not appear to have been metal-lined. They were either ceramic, such as the dolium in I viii 19, or built from rubble and apparently lined with opus signinum, such as the tanks in VII xiv 17. It is possible that these could have contained water or been used in the dyeing process, augmenting the vessels available with others that were not metallic. Apparatus involved in dye processing and dyeing may be ceramic or not metallic, such as those excavated at Sabratha, Libya.
The vibrant colours attained during the experiment show that the palette available to the Roman dyers was far more varied from fewer elements than had been first thought. Each of the metals caused a difference in colour to the control and to each other, ranging from bright, clear hues to ‘saddened’ darker shades. This shows the possibilities for variations in colour and demonstrates the subtlety required in the dyers' art to produce the colours required.
Further questions
Regarding the dyeing process in different material vessels, however, further questions can be explored: is it the metal kettle wall that directly affects the colour, or does the metal merely procure the change in pH that, in turn, affects the colour? Does this influence on the colour happen during mordanting, during dyeing, or equally during both parts of the process? Does the kettle wall also have an influence on the stability of the colour, such as its lightfastness?
The authors hope that these questions and others can be approached in the near future.
Summary
The city of Pompeii was preserved in a volcanic eruption in AD79. Its manufacturing apparatus survived in situ. The dyeing industry in Pompeii was the subject of an intensive study. To understand the dyeing process, a survey and reconstruction of apparatus was undertaken. This raised fundamental questions about the dyers’ choice of materials, which in turn led to the experiment described here.
A survey of the 40 original apparatus showed that the kettles were made from lead. Lead was cheap and available, but is weak with a low melting point. Consequently, the kettles had been subject to creep (accumulated deformation with use). A computer simulation showed the kettles did not break but had been physically unstable. The question remained: iron and copper had been available, so why had lead been used?
Following review by a professional historic dyer, an experiment was undertaken to investigate the effects of using an iron, copper or lead kettle on the dyed material, to determine if the different kettle materials may have significantly influenced the dyeing outcome. Two Roman dyes were used and both gave results with definite colour differences depending on kettle material.
Acknowledgements
Thank you to Labor für Experimentelle Archäologie (LEA) in Mayen for hosting Textilforum 2012, for inviting Textilforum to be its inaugural event and for providing such comprehensive facilities to make this event a success!
Bibliography
ALLISON, P. 1992. The Distribution of Pompeiian House Contents and its significance. Volumes I and II. University of Sydney, Australia.
BENDER JORGENSON, L. and MANNERING, U. 2001. MonsClaudianus: Investigating Roman textiles in the desert. The Roman Textile Industry and its Influence A Birthday Tribute to John Peter Wild. Ed: Walton Rogers, P. Bender Jorgensen, L. Rast-Eicher, A. Oxbow books, Oxford. Pp1-11.
CARDON, D. 2001 'On the road to Berenike: a piece of tunic in damask weave from Didymoi' The Roman Textile Industry and its Influence A Birthday Tribute to John PETER Wild. Ed: Walton Rogers, P. Bender Jorgensen, L. Rast-Eicher, A. Oxbow books, Oxford. pp. 12-20).
FRAYN, J. 1984. Sheep-Rearing and the Wool Trade. Francis Cairns. Liverpool
HOPKINS, H. J. 2007. An investigation of the parameters that would influence the scale of the dyeing industry in Pompeii An application of experimental archaeology and computer simulation techniques to investigate the scale of manufacture of the dyeing industry and the factors that influences output. PhD thesis, University of Bradford.
HOPKINS, H. J. 2008. Using experimental archaeology to answer the unanswerable: A case study using Roman dyeing. In: Experiencing Archaeology by experiment. Proceedings from the Second Conference of Experimental Archaeology. Eds: Cunningham, P. Heeb, J. Paardekooper, R. Oxbow Books, Oxford. Pp 103-118.
HOPKINS, H. J. 2013a. Reconstructing the dyeing industry of Pompeii through experimental archaeology: the challenges and rewards of a new approach. In: Ancient Textiles, Modern Science. Proceedings of the first and second European Textilforum. Ed: Hopkins, H. J. Oxbow books, Oxford.
HOPKINS, H. J. 2013b. Reconstructing the dyeing industry of Pompeii: the importance of understanding the dyers’ craft within a multidisciplinary approach. In: NESAT XI The North European Symposium for Archaeological Textiles XI. Eds: Banck-Burgess and Nübold C. Baden Wüthemberg.
HOPKINS, H. J. 2013c. The importance to archaeology of undertaking and presenting experimental research: a case study using dyeing in Pompeii. In: Archaeological and Anthropological Sciences. October 2013. Springer Berlin Heidelberg. Proceedings of the 6th Experimental Archaeology Conference, York, 2012.
JANAWAY, R. C. and Robinson, D. J. 1994. Unpublished. Lecturer and postgraduate in Archaeology, University of Bradford.
JONGMAN, W. 1988. The Economy and Society of Pompeii. J.C.Gieblen. Amsterdam.
KOREN, Z. 1994. Analysis of the Masada Textile Dyes. In: MasadaIV The Yigael Yadin Excavations 1963-1965 Final Reports. Eds: A. Sheffer and H. Granger-Taylor. Israel Exploration Society The Hebrew University of Jerusalem. pp257-264.
LAGERCRANTZ, O. 1913. Papyrus Graecus Holmiensis Recepte für Silbur, Steine und Purpur.
LAURENCE, R. 1994. Roman Pompeii Space and Society, Routledge, London.
MOELLER, W. 1976. The wool trade of ancient Pompeii. E.J.Bril:Leiden.
MONAGHAN, M.D. 2001.Coats of Many Colours: Dyeing and Dyeworks in Classical and Hellenistic Greece. PhD Thesis. School of Archaeology and Ancient History, University of Leicester.
MONTEIX, N. and Pernot, M. 2005.Pers. Comm from the forthcoming: Some features of the lead craftsmanship in Pompeii and Herculaneum. Poster presented at conference 2005. Summary of work to date undertaken at Centre Jean Bérard, Naples and Centre Camille Jullian, Aix de Provence.
Pliny the Elder. Natural History, with an English translation by H. Rackham and others. Thirty seven books in ten volumes. Loeb Classical Library. Heinemann 1958-1962.
PLOSS, E.E. 1977. Ein Buch von alten Farben. 4th edition. Heinz Moos Verlag, München
PRITCHARD, F. and VERHECKEN-LAMMENS, C. 2001. Two wide-sleeved linen tunics from Roman Egypt. The Roman Textile Industry and its Influence A Birthday Tribute to John Peter Wild. Ed: Walton Rogers, P. Bender Jorgensen, L. Rast-Eicher, A. Oxbow books, Oxford. Pp21-29
RYDER, M. L. 1990. The Natural Pigmentation of Animal Textile Fibres. Textile History 21 (2), 135-48.
SCHWEPPE, H. 1993. Handbuch der Naturfarbstoffe. Vorkommen - Verwendung - Nachweis. Nikol Verlagsgesellschaft, Hamburg
SHEFFER and GRANGER-TAYLOR, H. 1994. MasadaIV The Yigael Yadin Excavations 1963-1965 Final Reports.Israel Exploration Society The Hebrew University of Jerusalem.
STOREY, G. 1997. The Population of Ancient Rome. Antiquity. 71:966-978.
TAYLOR, G.W. 1983. Detection and Identification of Dyes on Pre-Hadrianic Textiles from Vindolanda. Textile History, 14 (2), pp115-124.
VITRUVIUS. Ten Books on Architecture. Translated by Morris Hicky Morgan. 1960. Dover Publications Ltd, New York.
WILD, J.P. 1970. Textile Manufacture in the Northern Roman Provinces, Cambridge University Press.