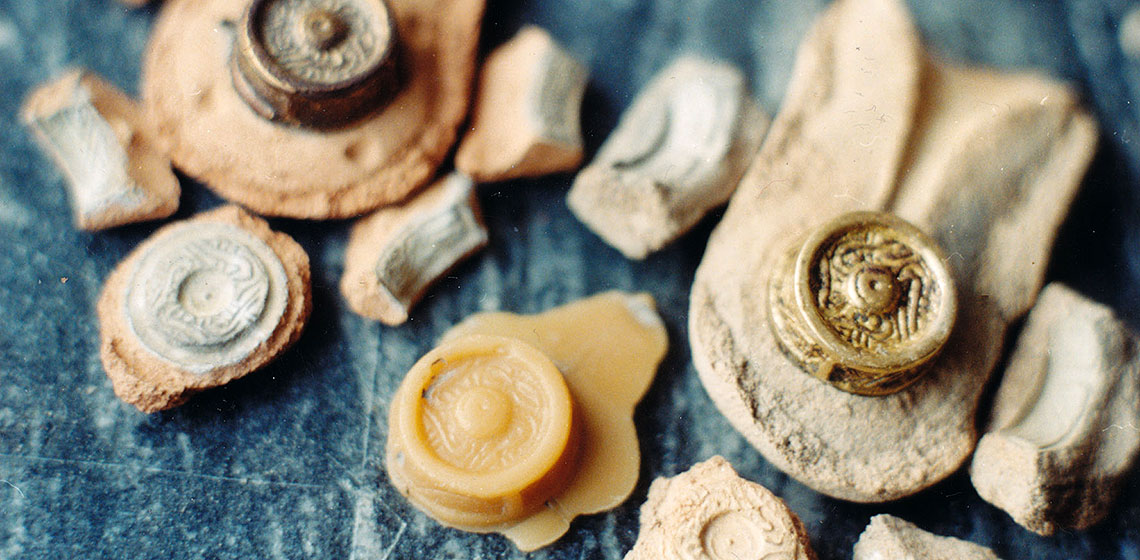
Since the 1940s we have had a discussion in Scandinavia concerning ancient mould-making methods. The question of different methods in the production of ceramic moulds has taken a large part in these discussions; by lost wax or by direct matrix-methods. This study gives a brief background to the subject and presents the results of a small series of experiments, related to questions concerning the methods used at the Migration/Merovinginan Period workshops at Helgö, Sweden. The study claims that lost wax-methods could have been used at Helgö to a larger extent than claimed earlier. This conclusion however does not exclude possible use of direct matrix-methods.
The Scandinavian discussions concerning ancient mould-making methods started in the 1940s under circumstances with very sparse availability of archaeological workshop-material, thus limiting the possibilities for research and reconstruction. This situation has changed dramatically during the past years, because of several large workshop excavations; like Ribe in Denmark and Helgö and Birka in Sweden. The fifth, sixth and seventh century workshops at Helgö in particular, excavated from the 1950s until the 70s, revealed large materials which pushed forth our knowledge dramatically.
Methods for mould-production
The emphasis in the debate for almost half a century has been on questions concerning mould making, reproduction and mass-production. Concerning ceramic moulds, we can see two directions in the discourse: either the moulds would have been made by pressing an original object into the mould material (a direct matrix-method); or they could have been made by the lost wax-method (à cire perdue).
The question of lost wax is difficult to deal with. The literature does not seem to record any findings of wax from workshop-related contexts except for one single case; a Viking goldsmiths' grave from Mysen in south east Norway. A man was found buried accompanied by crucibles, moulds and a piece of wax (Skjølsvold 1951). An archaeological problem with use of wax in casting, is that most of the wax used would have burnt away when firing the moulds. It disappears rather than being preserved in the soil, except for possibly in a few lucky cases.
Earlier, the Swedish archaeometallurgist Andreas Oldeberg presumed that à cire perdue had been frequently used, not as the one and only method, but as one of a few methods used (Oldeberg 1942,243ff; 1966,80ff). The discussion was troubled by the fact that the original ceramic moulds show obvious signs of being divided in two, which would not have been necessary when using this method. Two piece-moulds is certainly not a characteristic feature of contemporary lost wax casting. These facts pushed the research to some extent in a direction disregarding the method of lost wax-casting (Oldeberg 1963,4f; Zachrisson 1960). It created a situation where, in many cases, over-complicated hypothetical production-methods were suggested, probably hitting far apart from the actual production method which was the target of investigation.
Danish experimental research has seized on the assumption that lost wax-casting was frequently used in Scandinavia in the Bronze Age, through the Iron Age and into the Middle Ages. The Norwegian goldsmith´s grave has been accepted as proof for wax being important in the craft. Experiments and comparisions to original objects have supported this hypothesis.
Oldeberg did, at an early stage of the discussions, suggest a reproduction method by pressing a metal original into wet clay, whereupon the cavity made could be filled with wax (Oldeberg 1942,259f). This 'wax-copy method' was later experimentally developed by Danish archaeologist K. R. Hedegaard, who has shown it´s efficiency. According to Hedegaard, it is possible to make 60 wax models of a simple single-faced object in half an hour (Hedegaard 1992,77).
Bjarne Lønborg, Denmark, presented an idea to explain the division of ceramic moulds into two parts. Instead of regarding this as evidence against lost wax-technology, it could be seen as a way of making air vents. The thin space between the parts of the mould could have been created by isolating the halves with grease during the production of the moulds, in order to obtain a narrow space for the escape of emerging gases when pouring in the molten metal (Lønborg 1986,80f).
Wax and reproduction
The essential difference in quality between a ceramic mould made by lost wax and one made by a direct matrix-method, is that the wax will prevent the imprint in the cavity from being exposed to air during the drying of the mould. This creates conditions for casting with a brilliant accuracy to the original: ’what you see is what you get’. With a direct matrix-method this will never will be possible to attain; you can get fairly close to it, but not all the way. A metallic model must be taken out of the mould before the tempered clay mix is completely dry and will thus leave the imprint unprotected from the air. Because of this, the inner surface will shrink and crack in different ways. This will affect the imprint, which will look a bit grainy and these grains will be transferred to the cast object.
Another advantage of the lost wax-method is the possibility of fast and efficient mass-reproduction of objects by the earlier mentioned wax copy-method. A thin oil-film on the metal original makes it easy to remove it from the wet untempered clay, after which wax can be poured into the cavity. The original object can then immediately be used for making the next wax copy. When making an imprint of an original directly into the heavily tempered and unstable mould-material (heavily tempered clay), the original must be left in it until this is leather-dry and stable. This way, the original would be in use for some time, so the next mould cannot be made instantly.
Using the wax copy-method it is even possible to copy objects with slight overcuts in their patterns, as the wet clay can be bent out a little before removing the original object. A craftsman making wax copies for lost wax-moulds, provided by one single metal original, can create several waxes by the time a matrix mould-maker could have created one single mould with his original. This effeciency is an important quality in mass-producing jewellery. Another very important advantage is the possibility of retouching the objects already in the soft wax, instead of doing this afterwards in the cast metal object, which is quite a hard work.
Lønborg suggests that ceramic moulds could have been made in two pieces in order to create air vents. However, there are more reasons for dividing the mould into two parts. When casting thin and fragile jewellery, ordinary one-piece moulds are hazardous. When breaking the mould you could easily break the object as well, as the opening requires a slightly brutal approach. When opening a two piece-mould, connected just by a thin clay coating, the mould can be opened a lot more carefully. These moulds often even crack spontanousely along the zones of the joints after casting, as a result of tension between the cooling metal and the ceramic material.
Cire perdue-characteristics on cast objects and moulds
Since wax used in the lost wax-process generally vanishes away by fumes, we have to look for characteristics caused by the method in the cast objects. The only Scandinavian object I know so far that is obviously a lost wax-cast piece, is a silver ear-spoon from grave 507 at Birka (See Figure 2). It is a small, gilt piece with niello-inlayings. The backgrounds of the figures on the handle have rapidly been modelled with an approximately 1.5mm wide chisel, which has left very charachteristic marks of cutting through wax.
Another direction for our studies would be by studying the cavities of moulds from excavated workshops. Examples of differences in imprint between the two methods, from reconstructed moulds, are shown in Figures 3 & 4. Figure 4 shows a slightly more grainy surface than in Figure 3.
The clasp button moulds of Helgö, Sweden - an example
At the workshops at Helgö near Stockholm, 526 fragments of moulds for copper alloy clasp buttons were found, dating to the Migration Period. They were analysed by Kristina Lamm in the excavation report (Lamm 1972).
Apart from analyzing the styles of the buttons cast at Helgö, Lamm also studied the casting technologies. A method suggested in earlier discussions was the idea of casting in multi piece-moulds made by direct matrix-methods (Zachrisson 1960 & 1968). The interpretation of the Helgö materials did to a large extent lean on this idea, especially since the clasp button-moulds seemed to be broken in a characteristic pattern. Despite the ordinary cracking zone of the two piece-moulds, these moulds were broken by the sides of the buttons and around the upper side as well.
As many of the buttons were made with four decarative fields on the sides, delimited by frames or ridges, Lamm interpreted this ornamental style by technical explanations. These ridges could mark the places where mould-parts were joined, as such ridges are the places on a cast piece where flashes of metal occur running between mould parts could most easily be chiseled or filed away without destroying the ornaments (Lamm 1976,19).
The clasp button-moulds would, according to Lamm, have been divided into six or rather seven parts (Lamm 1980,107f), as shown in Figure 5. The parts would have been modelled around the original object and taken apart in order to remove the original, whereupon they were put together and connected by an outer layer of mould material. This is a direct matrix-method. Concerning lost wax-casting, Lamm says the use of this method cannot be proven with any certainty in this material (Lamm 1973,3).
Experimental series on cracking-patterns
Looking at the findings from Helgö, the mould-fragments do not necessarily seem to support Lamm´s multi piece-mould reconstruction.
The round upper parts are easily recognized (See Figure 6; left & middle) and the lower parts of the moulds as well, but the evidence for the side parts having been divided into four separate pieces seem fairly weak an undistinct. The side parts seem to have been broken in random patterns and the cracks are uneven, as if they have broken randomly. The side-fragment shown at the right in Figure 6 is broken straight across an ornamental field, and not as would be expected by the ridge between the fields.
Could patterns of cracking, like the ones seen on the Helgö moulds, occur on two-piece lost wax-moulds as well? In order to find this out a series of 15 clasp button-moulds were made by lost wax, cast in brass and opened, whereupon the breaking patterns of each individual mould was registered. The wax models for the moulds were made by Hedegaards wax copy-method, with a brass 'clasp button-dummy' as an original.
The moulds cracked at the weakest points, caused by the shape of the objects that were cast. The cracks happened at the division of the moulds (between lower and upper parts) and further where the upper sides of the buttons and the corners between the sides joined.
Images of the cracks from the 15 moulds have been put together in Figure 7 (left). A pattern is suggested as well (See Figure 7, right), where Lamm´s suggested reconstuction slightly can be recognized. There is a vague tendency of the side parts cracking on each side of the mould, but the general impression is that they have broken apart fairly randomly.
To this experiment two time-studies have been added: one on making a mould with a single metal original, using the multi piece-method (See Table 1); and the other one on making a two-part lost wax-mould, using the wax copy-method (See Table 2). As the buttons are hollow at the back, the wax copying required two clay moulds, which were joined immediately after pouring the wax. In an environment providing better conditions of heat and ventilation, it could perhaps be possible to reduce the periods of drying by 50 %. The making of the multi piece-mould would then need approximately 3 hours. Making the lost wax-mould would need 1 hour and 12 min. By taking advantage of the long 'passive' moments of solving clay and drying mould parts, it would be possible to make at least 7 lost wax moulds in 3 hours. When making the multi piece-mould, the original model will have to stay in the mould for at least 3 hours, before it can be removed and used again.
Conclusion and a short discussion
Do these experiments prove Lamm was wrong? Not necessarily, but it could show that Lamm´s interpretation may be leaning too much on weak support. Fragments like the ones shown in her reconstruction could just as well emerge from lost wax-casting.
There is another fact though, that may support hypotheses of direct matrix-methods. On the lower parts of the Helgö moulds, depressions are often found that are easily interpreted as key holes. They are never as regularly placed as in Lamm´s reconstruction (See Figure 5), but are undisputably there (See Figure 8). The only reason for the use of keys and key-holes is for fitting the parts together after the mould is opened in order to take something out - which then would be an original model. These marks could also have been made by the craftsmen checking the dryness of the lower mould-parts with a wooden stick, a suggestion that seems unlikely though not impossible.
Then again, there are several upper part-fragments showing possible features of the distinct imprint of lost wax-casting in the Helgö-material. This could mean that different methods were at use at Helgö. What does this tell us?
The possibility of having the two different methods in use could imply differently skilled craftsmen. The direct matrix-method is actually a more primitive method, though in some ways more complex, than making moulds with lost wax. There must be a reason why a difficult and inefficient method would be preferred, when a faster and easier method that actually provides better results was fully available - and it had probably been available by living traditions and practice since thousands of years. Maybe the different methods used reflect preferences of individual craftsmen.
We could also see economical or other differences in the availability of wax. It would not be too far-fetched to suggest that bees wax was a precious raw-material, perhaps usually only seasonally available. Periodical or occasional absence of wax could have forced the craftsmen to bring other methods into use, despite the loss in quality this could mean to their work.
Finally, the thought of fast mass-production could very easily force us to make analogies with present day demands, which are not at all adaptable to Iron Age/Early Medieval circumstances. There may actually rarely have been any need for working at a speed of 60 wax copies in half an hour as Hedegaard has shown would be fully possible, not even in a great workshop with the dignity of Helgö.
Tables
Moment |
Time required, minutes |
Under part |
14 |
Slight drying |
28 |
Side part I |
9 |
Slight drying |
30 |
Side parts II & III |
10 |
Slight drying |
38 |
Side part IV |
10 |
Slight drying |
30 |
Upper parts |
11 |
Slight drying |
75 |
Opening, removing model |
8 |
Joining parts |
5 |
Sealing with clay-coating |
8 |
Total time required |
276 minutes; 4 h 36 min |
Moment |
Time required, minutes |
Wax copy-mould, upper part |
2 |
Wax copy-mould, under part |
4 |
Pouring wax, fitting parts together |
1 |
Solving clay in water |
20 |
Removal of clay from wax copy |
3 |
Under part of lost wax-mould |
7 |
Slight drying |
30 |
Upper part of lost wax-mould |
6 |
Slight drying |
25 |
Sealing with clay-coating |
2 |
Total time required |
100 minutes; 1 h 40 min |
Bibliography
HEDEGAARD, K R., "Bronzestøberhåndværket i yngre germanertid og tidlig vikingetid i Skandinavien - teknologi og organisation", Lag, vol. 1992/3, Højbjerg, pp. xx-xx, 1992.
LAMM, K., "Clasp buttons", Excavations at Helgö IV, vol. Workshop Part 1, Stockholm, KVHAA, pp. xx-xx, 1973.
LAMM, K., "The Manufacture of Jewellery during the Migration Period at Helgö in Sweden", Bulletin of the Historical Metallurgy Group, vol. 7, issue 2, pp. xx-xx, 1973.
LAMM, K., "Early Medieval Metalworking on Helgö in Central Sweden", Aspects of early metallurgy: papers, vol. 17, London, The British Museum, Historical Metallurgy Society, 1980.
LAMM, K., and A. LUNDSTRÖM, "East Scandinavian Style 1: an answer to Birgit Arrhenius", Medieval Archaeology, vol. 20, London, Society for Medieval Archaeology, pp. xx-xx, 1976.
LØNBORG, B., "Bronzestøbning i dansk jernalder", Kuml - Årsborg for Jysk Arkæologisk Selskab, vol. 1988-89, Århus, Jysk Arkæologisk Selskab, pp. 77-94, 1989.
OLDEBERG, A., Metallteknik under förhistorisk tid. Part I and II, Lund, 1942.
OLDEBERG, A., "Till frågan om de ovala spännbucklornas tillverkningssätt", Fornvännen, Stockholm, KVHAA, pp. xx-xx, 1963.
OLDEBERG, A., Metallteknik under vikingatid och medeltid, Stockholm, 1966.
SKJØLSVOLD, A., "Et eiendommeligt smedsgravfunn fra Mysen", Universitetets Oldsakssamlings Årbok, vol. 1949-50, Oslo, pp. xx-xx, 1951.
ZACHRISON, I., "De ovala spännbucklornas tillverkningssätt", TOR, vol. 6, Uppsala, pp. xx-xx, 1960.
ZACHRISON, I., "Bronsgjutning i flerdelad form", Fornvännen, Stockholm, KVHAA, pp. xx-xx, 1968.