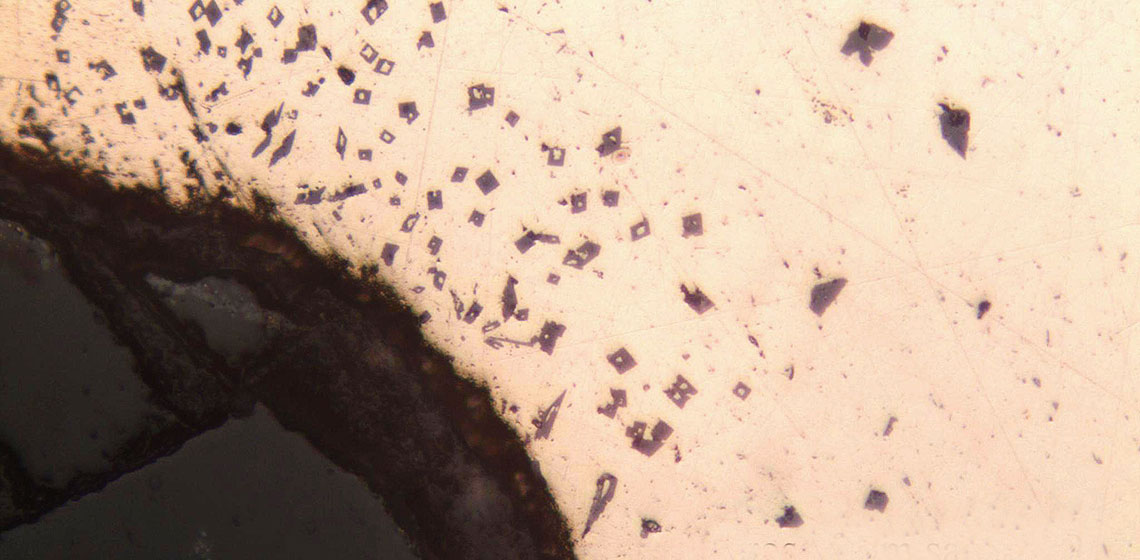
It is accepted knowledge that when re-melting alloys, some of the metal with a lower melting temperature is lost through oxidation, and more metal must be added in order to maintain the desired alloy proportions. In order to understand the changes in alloy content when recycling using Bronze Age technology, experiments were undertaken by the author and others, using a charcoal furnace. These experiments included recycling bronze to quantify loss of tin, and experimentation in co-melting metals. The results were then compared to modern metallurgical practices using electric and gas furnaces. The initial results were presented at the Historical Metallurgy Society’s Research in Progress Conference in November of 2009. However, this paper includes further experiments that build on that work. The conclusions indicate that knowledge of earlier practices was lost with the advance of technology, and that broad assumptions cannot be made about earlier technological practice based on work done with modern equipment.
Introduction
The use of modern facilities makes it possible to do controlled experiments, although the conditions do not always duplicate conditions as they would have been in antiquity. While experiments in the field admittedly relinquish some control, they can yield results that can be quantified in the lab. It was in this spirit that a series of experiments was designed to question how recycling non-ferrous alloys using Bronze Age technology affected the proportions of metal in tin/bronze alloys.
Previous studies undertaken in the Archaeology Department at the University of Sheffield by Mary Wilde had shown that when a 10% tin bronze was repeatedly re-melted in an electric muffle furnace, the tin content dropped from 10% to 1% (Wilde, 2007, p. 49). Microstructural examination of the recycled samples showed that as tin content was reduced, there was a corresponding increase in the copper-copper oxide eutectic and evidence of crystals of tin oxide found in the dross that formed on the surface of the alloy. These results were assumed to be the result of the oxidising atmosphere within the electric furnace. This kind of reduction of tin in copper/tin bronze is also seen in modern foundries where tin is added when the alloy is recycled in order to maintain a consistent alloy. In some foundries a commercially prepared phosphorous deoxidizer is added to help keep tin from oxidising. However it is also standard practice to estimate the amount of tin needed, melt a sample of the alloy, analyse it, and adjust the alloy before the final pouring(Cottrell, 1975, p. 88; Untracht 1985, p. 349; Sohn and Sridhar 2005, p. 11). This raises questions as to how Bronze Age metalsmiths would know how much tin would be needed to maintain the desired ratio of metals in an alloy, and how this loss would compare to modern compositional changes when using a charcoal furnace. As a result, this could provide a basis for estimating the amount of tin needed for alloying in pre-industrial metal production.
Recycling bronze in charcoal furnaces
The first recycling experiment began with approximately 120g of 7% tin bronze. This was melted in a small bowl furnace with an internal diameter of approximately 25cm and 16cm deep. The furnace was fuelled using hardwood charcoal, and air was introduced by hand-operated bellows. New crucibles were used for each experiment.
For the first experiment, the crucible containing the metal was placed in the furnace and surrounded by charcoal. Once the bronze was molten it was poured into an ingot mould and allowed to cool. A sample was taken and the remaining metal was re-melted for a total of eight recycling episodes.
The samples were taken to the metals and glass lab of the University of Sheffield where they were analysed using a Niton portable XRF analyser. It was found that over the course of eight melt cycles there was no detectable loss of tin (See Table 1. Note that the initial reading in each table shows the metal before recycling). Polished samples of the metal were then mounted and examined. The microstructural analysis found no evidence for tin oxide crystals or the presence of a copper-copper oxide eutectic. Well-developed dendrites were visible in all the samples under magnification, with the only variations being the size of the dendrites, which is indicative of the different cooling times of the individual pours (See Figure 1). These results are in contrast to modern foundry practice using electric or gas furnaces where oxidation occurs in concentrations on the surface of the alloy (Cottrell, 1975; Sohn and Sridhar, 2005).
It was considered that the atmosphere in the furnace could have been reduced because the charcoal was heaped over the crucible, and may have affected the results. For the second recycling experiment a 12% tin bronze was melted with the crucible positioned on top of the charcoal and the bellows positioned to blow air directly at the charcoal, thus allowing as much oxygen as possible to reach the metal. Again the metal was melted, sampled, and re-melted for a total of eight recycling episodes. The results were nearly identical to the first experiment with no evidence of tin loss (See Table 2). The dip in the percentage of tin in the second sample accounted for when analysis demonstrated the homogeneity of the final sample, which shows a difference of as much as 1.16% variation within the sample (See Table 3).
The preliminary conclusion was that there might have been minimal tin loss in a small number of recycling events, and that changes in the alloy might have occurred if recycling took place on a much larger scale. For the third recycling experiment, it was decided to hold three separate batches of bronze in a molten state for prolonged periods of time. A bar of 10% bronze was cut into three sections and placed in separate crucibles. These were then held in a molten state, the first for one-half hour, the second for one hour, and the third piece for one and a half hours. This was done in order to simulate the melting times for several castings. It was estimated that the average time that it took to pour the bronze and return the remainder to the furnace was fifteen seconds, and if the metal would be held in a molten state for one hour, the result could represent over two hundred recycling events. Despite these extended dwell-times at high temperatures in an open hearth, appreciable tin loss could still not be detected (See Table 4). It should be noted that in all of the experiments no dross formed on the surface of the metal and there was no slag remaining in the crucible.
Problems with the data were recognised because the metals used in the first experiments were performed using scrap metal that was available in the archaeology department. While they were analysed with a pXRF before and after the experiments, it was felt that a better analysis could be done with alloys purposely mixed for the experiments. However, circumstances and the availability of the Sheffield departmental XRF made this unfeasible, and the project was delayed until 2013, when the opportunity arose to work with Drs Francesca Fulminante and Mukund Unavane of Cambridge University.
The first set of recycling experiments was replicated using a charcoal furnace and bellows, this time using a 90% copper and 10% tin alloy that was purposely mixed for the experiment. A Bruker portable XRF was used for the analyses at the Cambridge University archaeological laboratories, operated by Dr Unavane. The results were substantially the same as in the earlier experiments and no tin was lost during recycling. In addition, the small amount of lead that was part of the alloy was also stable through the recycling episodes (See Table 5).
Control experiments using an electric furnace
A final experiment using an electric furnace was set up to duplicate the previous experiments. In the experiments performed by Mary Wilde, samples of bronze were melted in an electric furnace at 1175°C for increasingly extended periods of time. In her samples, Wilde found that the loss of tin corresponded to an increased percentage of oxygen, resulting in the presence of tin and copper oxides (Wilde, 2007, p. 38).
For the final experiment, samples of 10% tin bronze were melted and held for one half hour, one hour, and two hours at 1150°F. A final melt was done in which the metal was melted at 1200°C for three hours. Unlike the samples created in the charcoal furnace, the samples melted in the electric furnace formed dross on the surface, in addition to a small amount of slag that remained in the crucible.
The samples from this experiment were again analysed using the NITON pXRF, and polished samples were mounted for visual examination. It was seen that the percentages of tin were much reduced. At the end of the first melt, the amount of tin had lowered to an average of 4%. The sample from the final melt lost another 1% of tin (See Table 6). However, because pXRF technology does not distinguish between different forms of metal (e.g. metal and metal oxides) the actual percentages of tin were estimated to be lower, since these could be concentrations tin oxide rather than the primary metal. It was observed that there was a higher concentration of tin on the portion of the sample that was originally the surface of the metal. In the visual examination of the polished sample it was seen that tin oxide crystals were found in small clusters and in a band on one side of the sample (See Figure 2). This agreed with the pXRF reading showing the spatial variation of tin concentration. The dross and slag were also examined and it was found that the slag was rich in both copper and tin oxides. In the dross sample, distinct separation bands of tin oxide can be seen without magnification and appear as fine cracks and borders on the polished surface, while the individual crystals of tin oxide that form the separation bands can be seen in detail under magnification (See Figure 3).
Furthering the experiment: Co-melting alloy components
The previous set of experiments was designed to determine how much tin would be lost during successive recycling events using replicated Bronze Age technology. The results raised further questions regarding alloying practices and further experiments were designed based on these results.
Because there was no tin lost due to the reduced atmosphere, it could be questioned if this would not affect the alloying process. In modern metallurgy, the metal with the highest melting point is put into the crucible. Once that metal is molten, other metals with lower melting temperatures, are added to the crucible (Untracht, 1985; Sohn and Sridhar, 2005).
If no tin is lost when bronze is recycled using a charcoal furnace, then it could also be possible that tin would not be lost if tin and copper were placed in the same crucible and melted together. In the experiment in which the alloy was purposefully mixed (See Table 5), the copper and tin were placed in the crucible and melted at the same time. As can be seen from the data in Table 5, there was no loss of tin, as would be expected using a modern electric or gas furnace.
Conclusion
The results of the above series of experiments highlight the pitfalls of trying to simulate ancient practices with modern equipment. Current logic would dictate that when two metals are combined in an alloy, some portion of the metal with the lower melting temperature would be lost when alloying and recycling. Most modern furnaces are highly oxidizing, but despite conditions of using an open pit furnace with the crucible exposed to as much air as much as possible, the conditions in the furnace still created an atmosphere so reduced that the tin could not oxidize.
The results differed greatly with those gained from using electric furnaces, where modern practice requires the addition of fresh tin for each recycling event. Further it was found that tin and copper could be co-alloyed without the loss of tin, which is also in variance with modern practices. Such results have implications for the estimates of the total use of tin in Bronze Age metallurgy, since extra tin would not have to be added to maintain the alloy when recycling.
It was demonstrated that even an open hearth with the air blast directed at the crucible is insufficiently oxidising to promote tin loss, and that tin bronze is a stable alloy when recycled under these conditions. Using a charcoal furnace had distinct advantages for work done on the scale sufficient for Bronze Age workshops. However, as new technology utilizing gas and electricity developed, the knowledge handed down by Bronze Age metalsmiths concerning recycling practices was altered and eventually lost.
Bibliography
COTTRELL, A., 1975. An Introduction to Metallurgy. 2nd ed. London: Edward Arnold.
SOHN, H. Y. and SRIDHAR, S., 2005. Descriptions of high-temperature metallurgical Processes. In: S. Seetharaman, ed. 2005. Fundamentals of Metallurgy. Boca Raton: CRC Press.
UNTRACHT, O., 1985. Metal Techniques for Craftsmen: A Basic Manual on the Methods of Forming and Decorating Metals. London: Robert Hale.
WILDE, M., 2007. ‘The Effects of Recycling Bronze and Some Implications for Bronze Age Europe’. Masters Thesis. University of Sheffield.